Listening to the pain point of a maintenance manager for an agricultural and industrial phosphate producer yields long-lasting results.
One producer of agricultural and industrial phosphate products needed a custom mechanical seal to solve a problem. Every 19 to 28 days pump failures occurred. When the mechanical seal failed, the pumps failed. Working together with a seal manufacturer to redesign a seal, seal life was extended to more than two years.
Mike Sondys, maintenance manager for Nutrien, formerly Potash Corp., had ideas about ways to solve the problem, but he struggled to find a seal manufacturer to listen. One finally did…
The result? Exponential improvement of the life of the mechanical seals and the pumps.
The Problem
Sondys believes it is his job to “dig down” and discover the root causes for equipment failures at his plant. The repeat failures when pumping heavy slurry was a serious problem. When the single internal cartridge seals failed, the pumps failed.
Sometimes, Sondys could wait for a planned outage to replace the pumps. Even then, the process was expensive and time-consuming.
“I’ve been working in research and development on mechanical seals for a heavy slurry environment without water intrusion into the process for a long time,” he said. “The issue we were having was with 30 percent phosphoric acid. The temperature of the acid was close to the temperature of what’s happening around the seal bases.”
In that environment, phosphoric acid plates and causes a crystal formation. Crystal growth around the springs destroyed the seal.
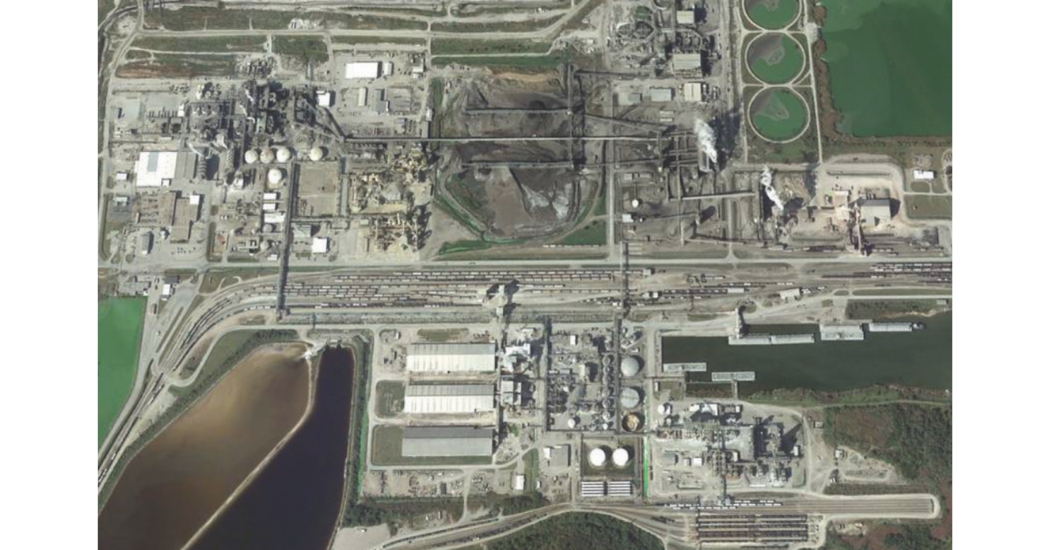
Aerial image of phosphate processing facility
Sondys was convinced he had ideas that would solve the problem, but his vendor could not help. Other vendors he contacted couldn’t either. Pumping this heavy slurry has distinctive challenges.
Mike Sondys of Nutrien was seeing pump failures every two to three weeks on his Goulds 3196 M pumps. He knew the mechanical seal was the source of the problem. He believed there had to be a way to improve the seal for a longer life, but he couldn’t find a manufacturer to listen until he met a regional manager for a seal manufacturer. Then he met the regional manager, and together, they set out to develop a better seal.
Sondys’ operation was pumping almost a solid material, basically clay and water. Sondys had ideas that he thought would help the success of the seal. He made some unusual requests, and the seal manufacturer’s engineering department accommodated them.
The Custom Mechanical Seal Solution
Sondys had technical knowledge that—together with the skills and expertise of the engineering team—proved to be a winning combination for developing a better seal.
Seal Changes
First, they did the following:
- Gave the seal a longer nose
- Lengthened the drive pin and made it more robust
- Moved the springs to the rotating face instead of the stationary one
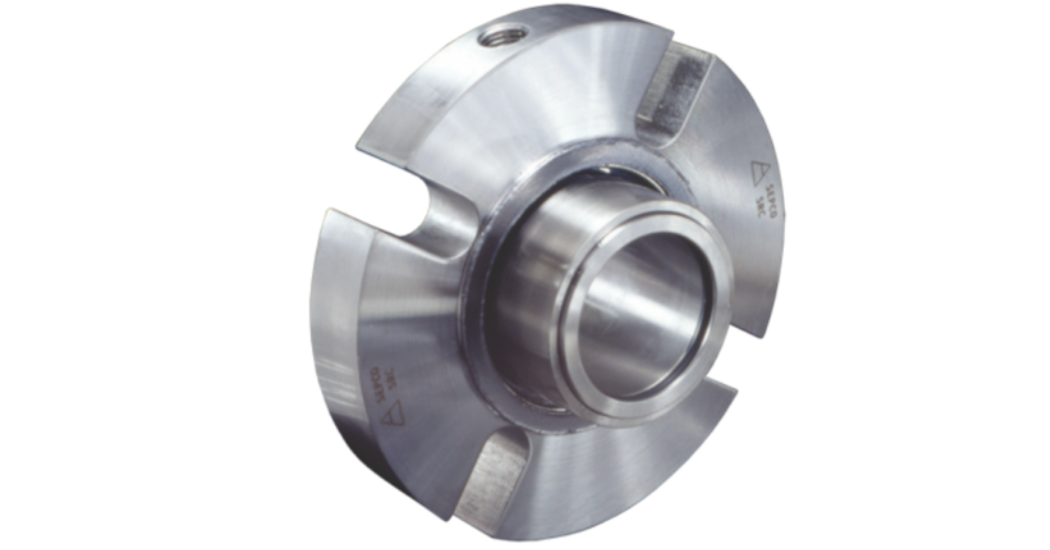
The Hastelloy seal is resilient and unaffected by the different types of acid involved in production.
Sleeve Material
These changes helped, but they still found that the stainless-steel sleeve on the seal showed significant wear. The next alteration was to manufacture the sleeve out of Hastelloy®, a chemically inert metal.
“We needed the seal to be bullet proof but universal,” said Sondys. “We have multiple types of acid in this department, and each has a different chemical corrosion property. Some of those acids make stainless steel porous, so acid would leak past the O-rings, causing the seals to clog and crash. Hastelloy is resilient and unaffected by the different types of acid we have.”
Success
While Sondys had ideas to improve the seal, the manufacturer’s engineers took that vision and make it work. Where his ideas were workable, the team implemented them. When the engineering team could improve on his ideas, it did. Together, a successful seal was developed.
“Previously, we had pumps failing in 19 to 28 days. I thought, if I could get a pump to run for one year, it would be a success. I have one that has been going now for two and a half years,” says Sondys. “I was checking those pumps three times a day during the testing phase. Now, I just let them run.”
By summer 2021, Nutrien has about 80 pumps in operation with this custom seal installed. Other than system upsets, the new design extended the seal’s life up to years verses days. When Nutrien needs new pumps for expansions or replacements, the company requires that the pump manufacturer install the custom SRC mechanical seal.
Beyond the Seal
Sondys cautions that the seal was not the only adjustment they made in this process. He also tweaked the rear cover that the mechanical seal is bolted to.
“The design of that cover has a lot to do with the success of the seal,” he said. “A standard bore box doesn’t provide enough circulation for cooling to keep the crystals from forming. The success rate of the seal depends on its relationship with the stuffing box. You have to use the seal in the right application with the right stuffing box for it to work.”
In addition to the custom seal and adjustments, Sondys plans to have the manufacturing team conduct training later in 2021. COVID-19 brought many challenges for Nutrien Aurora, including new personnel. Because of this, he wants to ensure that the team is correctly trained. The manufacturing team will train new and existing personnel in proper mechanical seal installation, equipment alignment, and other reliability best practices.
Reducing Water Use
The new seal also decreased the water required to cool the stuffing box. Before the redesign, five to 10 gallons of water per minute per pump flushed the stuffing box. This is a problem. As Sondys said, “We’re in the evaporation business. Any water intrusion into the process is costly, because we have to turn around and evaporate the water back out.”
The custom seal allowed him to take the flush water off his process, so he doesn’t have to introduce water into his system anymore. The power consumption alone of evaporating the water from that process was huge. It saves money on water and energy costs.
“The seal has a quench drain port,” added Sondys. “I trickle in water just to rinse out any residual flash gas. There is now zero water intrusion into the process with this design.”
Sondys brought expertise and ideas that were critical to this effort, but a vendor who was willing to listen, improve those ideas, and work with him to achieve success was required.
“I went through multiple variations of different seal designs with multiple vendors over several years. I finally decided what I wanted to do, and the other seal manufacturers said they couldn’t help me. [This manufacturer] did, and it works,” said Sondys.
Work with a manufacturer who does not try to force a solution onto you. You need someone who will work with you on the solution that is right for your application.
Comments