To prevent the internal corrosion of process vessels and other equipment that operate above ambient temperature, the oil and gas industry has long been at the forefront of adopting the use of high-temperature coatings. There are many great reasons why.
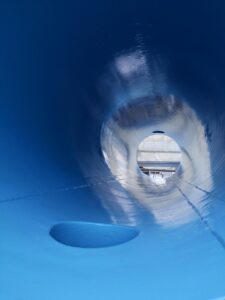
ARC HTS – High Temp Coating System
ARC HTS for immersed aqueous solution conditions up to 150°C (302°F)
Highly Corrosive Conditions
The most obvious reason for this industry’s advancement in the coatings arena is the corrosive conditions prevalent through so many stages of oil and gas production. Severe corrosion can affect equipment from upstream production facilities to downstream refineries. These corrosion mechanisms are primarily aqueous-based, including high levels of chlorides and other corrosive species such as hydrogen sulphide and carbon dioxide. These conditions cause high rates of corrosion to many metals and alloys. Organic polymer-based protective coatings can provide very good long-term resistance in many applications.
Oil and gas companies are highly knowledgeable when it comes to corrosion prevention and have generated a lot of experience over decades. As a result, they typically know which technologies work in certain conditions and which do not. But new market changes are producing challenges for both oil and gas companies and coatings manufacturers.
New Challenges and Ever Higher Temperatures
As oil and gas reserves diminish, the industry is being forced to explore and extract from ever deeper fields and producing fluids with much higher levels of corrosives than in the past. In turn, this has led to an increase in the processing temperatures and pressures required to produce fuels that meet with acceptable specifications.
To keep pace, the protective coatings industry has been required to develop new and improved organic polymer coatings that can handle the higher operating temperatures and corrosive conditions. Chesterton/ARC offers a range of high-temperature coatings that address a multitude of exposures.
The oil and gas industry also operates a lot of older process equipment designed and fabricated from materials suitable for conditions that no longer exist. This equipment either must be replaced at considerable expense or upgraded by either applying protective polymer coatings or cladding with a more corrosion-resistant metal or alloy.
Testing and Acceptance of New High Temperature Coating Technologies
One of the challenges faced by protective coatings manufacturers is to convince the major oil and gas producers that new higher temperature resistant coatings can withstand these more aggressive operating conditions. For oil and gas companies, the stakes are clearly high. Failure of a coating in a process environment that could result in shutting down a production platform can cost the operator millions of Euros/Dollars in lost production. Safety is another key criterion especially in the selection of any material that is used either offshore or at a refinery. All new materials and technologies must be thoroughly tested and proven before corrosion engineers will allow their use.
Most large multi-national oil and gas companies maintain their own lists of qualified and specified coatings that have met the requirements of laboratory testing and/or experience in the field. Often, the laboratory testing must be done by independent third-party laboratories following standardized test methods. However, many operators have their own unique testing requirements that must be conducted for a coating to become listed in their specifications. Therefore, multiple independent laboratory tests must be conducted to meet the requirements of all the global oil and gas companies. This adds to the expense of developing new materials and increases the development time to bring new tested coatings to the market.
While there can be valid reasons why oil and gas companies require some differences in the product testing that must be completed by coating manufacturers, achieving a more common consensus on testing might allow coating manufacturers to develop new technologies faster and to investment in more R&D.
New Coating Advances and How They Work
There are two main polymer types that are primarily used for internal coating of vessels and equipment subject to aqueous corrosion at elevated temperatures and pressures:
- Epoxy polymers
- Vinyl ester polymers
While these types of polymers have been in use as protective coatings for decades, recent advances in these technologies have allowed manufacturers to produce coatings that are able to withstand much higher immersion temperatures under severe corrosive conditions.
These advances have been made possible by developing polymers that have much higher glass transition temperatures (Tg) than older traditional epoxy or vinyl ester polymers. While older technologies were able to achieve Tg’s in the 50° to 60°C range, these new high temperature polymers (such as used in ARC S5 high temperature coating – the most recent development from the A.W. Chesterton Company) have a Tg of up to 210°C, allowing for continuous immersion at temperatures up to 180°C.
Protective coatings based on vinyl ester polymers have also seen advances in recent years in terms of ultimate Tg capabilities. However, the use of vinyl ester-based coatings has been declining in the oil and gas industry due to the more hazardous nature of these coatings during application.
High-temperature coatings are typically used on equipment handling aqueous process fluids, where aqueous corrosion is a concern. Application areas include separator vessels, heat exchangers and coolers, coalescer vessels, knock out drums, pipes and pipe spools, pumps, valves, and a diverse range of other equipment.
Partnerships Will Bring New Technologies to Market Faster
Looking into the future, it is certain that the oil and gas industry will face new challenges that will require new solutions, especially when it comes to corrosion protection in high temperature environments. Protective coatings manufacturers such as the A.W. Chesterton Company are ready to meet these challenges and look forward to building partnerships with the oil and gas industry to bring new technologies to the market faster, and to allow for easier adoption and acceptance.
Nick Wilson joined A.W. Chesterton in March 1989. Nick is responsible for application engineering in the ARC Technical Service Department for the EMEA region. His responsibilities include providing support for the application of Chesterton’s range of ARC materials, including specification of chemical, abrasion and high temperature resistant coating technologies. He provides technical and application engineering support and training to Chesterton’s Sales and Distribution personnel and Customers.
Comments