Contributor: Carver Pump
A centrifugal pump works by creating a centrifugal force to move liquid through the pump, increasing the liquid’s pressure as it moves from suction through the discharge end. A multi-stage centrifugal pump contains two or more impellers in the same pump unit. Ring section pumps, which are a type of multistage centrifugal pump, have multiple stages arranged in tandem inside their casings. As the liquid passes through each stage, the pressure of the liquid increases. This is especially useful for certain applications, including boiler feed systems, municipal fire suppression (think high-rise building sprinklers, for example), amine sour natural gas treatment systems, and so many others.
Read 19 Applications where you could use a Ring Section Pump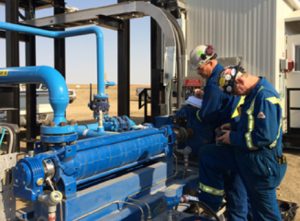
Being able to select the number of stages in a Ring Section Pump can help you meet the design point for your specific application. Adjusting the number of stages in a ring section pump does not affect optimal flow, but allows you to achieve the desired pressure requirements. So for example, let’s say you have a ring section pump with two impellers that produces a flow of 100 gallons per minute at 200 feet of head (pressure). When you add another stage, the rated flow (100 GPM) stays the same, but the pressure increases to 300 feet of head. You could add a fourth stage to get 400 feet of head, a fifth stage to get 500 feet of head, and so on, so forth.
Keep in mind that as the liquid’s pressure increases as it passes through each stage, axial thrust begins to occur as a result of the difference in pressure between the suction eye and the back of the impeller. With a difference in pressure across the impellers, axial thrust tries to push the pump shaft toward the suction eyes. This axial thrust must be offset in order for the pump to operate properly, so the rotor must be designed to be hydraulically balanced to preserve bearing life. Inter-stage diffusers (a ring of fixed vanes) minimize radial loads (force that acts at right angles to the shaft), while carefully controlling fluid flow for a more efficient conversion of velocity head into pressure head.
Instead of adding stages to a pump configuration, some pump manufacturers obtain higher pressure points by using larger impellers or by over-speeding a smaller impeller through a gearbox or variable frequency drive; however, it is important to note that failure in an over-speeding impeller can have catastrophic and costly results. It is better to operate ring section pumps with lower rotational speed instead of high-speed gearbox pumps; this results in lower NPSHr (net positive suction head required), more durability and longer life for the pump.
Before selecting a ring section pump, have a discussion with the manufacturer’s engineers about the operating conditions, NPSHr, temperature of liquid, physical space and piping configuration, seal flush options, and other conditions of service for the accurate selection of your pumps.
About Carver Pump
Since we built our first pumps in 1938, Carver Pump has become recognized as one of the leading centrifugal pump companies, building pumps to the most demanding engineering specifications and military standards in the world. We were one of the first American pump companies to attain ISO 9001 certification – the most recognized standard for quality in the world. This certification is your assurance that our commitment to quality includes not only our hardware, but also superior customer service, leading-edge R&D, and continuous improvement in everything we do. So whether the job is refueling fighter jets on the deck of an aircraft carrier, supplying paint to an auto assembly line, or bringing water to the fountain in a city park, we put our reputation on the line everyday with every pump we build. Learn more at www.carverpump.com.
Lesser known than some, it is a workhorse in the industry.