As energy costs continue to rise and water utilities strive toward carbon neutrality it’s only natural that well run organizations look to optimize their pumping processes. The cost to run a water utility’s pumps can run into the millions of dollars a year, and typically represent 70-80% of a utility’s total electricity bill. Add in blowers, mixers and sludge collectors and it’s clear that improving the energy efficiency of electric motors can be a big win both for the bottom line and the environment.
By adding power sensors to pumps and other electric motor applications, water utilities can not only protect and extend the useful life of their motors and pumps, but they can also unlock important energy usage insights.
How does Motor Power Monitoring Work?
Motor power, measured in HP or Watts, is calculated from the electrical connections powering the motor. This motor may be powering a pump, mixer, clarifier, blower or other industrial process. By multiplying Voltage x Current x Power Factor (loosely described as the energy required to charge the coils in the motor) we can get an accurate view of the work the motor is doing. This gives us a signal to monitor and control motors. For pumping applications:
- When flow rate is low, power is low
- When flow rate is high, power is high
- At light load conditions, caused by pump cavitation or dry running, power can give clear data on error conditions and need to react.
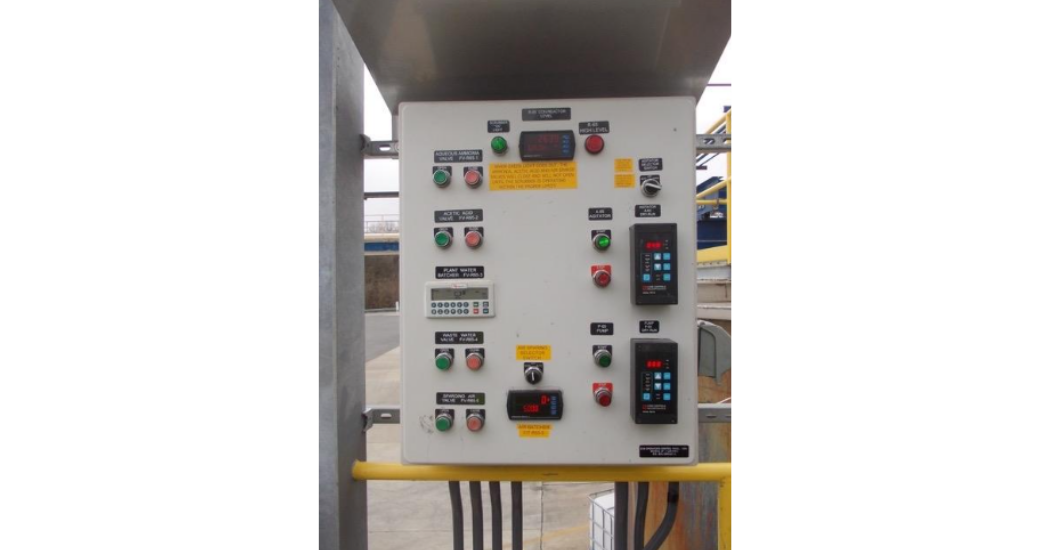
Figure 1: Power Sensors in Action
What are the applications for the Water industry?
Implementing power sensors across the range of motors in a Water delivery and treatment facility can have significant benefits. The following are areas that power sensors can connect to and deliver valuable feedback on motor conditions:
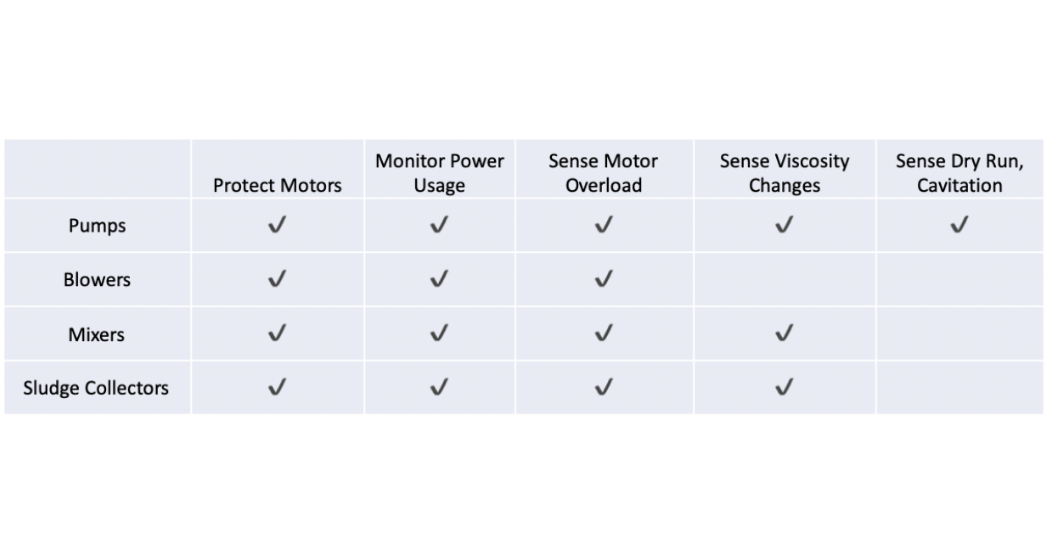
Figure 2: Applications for Power Sensors in Water/Waste Treatment Utilities
Power sensors and Motor Protection
When motor power is sensed and tracked in real time it can provide immediate feedback on abnormal running conditions. High power levels in a pump can indicate jams or clogs. Low power levels can be symptoms of loss of prime, cavitation or dry running. Shutting down the pump motor in these conditions can save the cost of the motor and potentially the pump as well.
A power sensor connected to a sludge collector or mixer can act as an ‘electronic shear pin’, shutting off a motor in high power events such as jams or viscosity changes that threaten to damage the motor or downstream equipment connected to the motor.
Power Sensors and Energy Management
When motor power (measured in HP or kW) is aggregated over time it can easily be converted into kWh. This can be useful for insights into power consumption for the most important assets in the water treatment and delivery process. Power sensors also incorporate ‘power factor’ into their calculations, providing additional data on the true operational costs of motors and the link to monthly energy bills. By understanding energy trends at the device level over time, operators are able to initiate energy saving measures such as:
- Knowing whether pumping operations are becoming more or less energy efficient.
- Being able to tell which pumps or other motors are contributing to the utility’s overall energy spend, and when peaks of demand are occurring.
- Determining when to replace motors with more efficient designs.
- Comparing measured HP to rated HP of the motors can indicate large savings by highlighting oversized pump motors. Replacing oversized motors with appropriately sized motors or Variable Frequency Drives can provide payback in a few months.
- Implementing staggered or off-peak operations. Spacing out the timing of peak demands can lower overall power usage and save significantly on the monthly energy bill.
Conclusion
Power sensors and load controls can deliver important benefits to the Water industry, including:
- an excellent investment to protect all motors that power pumps, mixers and sludge collectors, and blowers
- offering key insights into changing process conditions, particularly viscosity changes in waste treatment operations
- providing long-term and detailed energy usage data that is critical to reducing ongoing costs.
We believe every Water treatment facility should take advantage of power sensors to protect and optimize their installation. Many utilities can leverage rebate programs from their local electric provider, potentially offsetting any investment in power monitoring sensors.
Comments