Challenging offshore repair demands specialist skills
The business of offshore oil and gas extraction is beset with challenges, not least maintaining productivity and reliability in a harsh working environment whilst ensuring staff safety. So, delivering routine maintenance services requires a concerted team effort, such as that demonstrated by Sulzer when replacing a large motor from an oil production vessel in the North Sea.
Floating production storage and offloading (FPSO) vessels are purpose-built for the offshore oil and gas industry to process hydrocarbons and act as temporary storage facilities. As such, they are complex structures with a great deal of equipment installed in close quarters.
It is, therefore, quite an effort to remove a component as large as a 10.7 MW motor so that it can be taken onshore for planned maintenance. This task alone requires some expert precision, while the refurbishment needs to be completed by a properly qualified service center that is approved to work on components that are Ex rated and operate in potentially explosive atmospheres.
Extending service life
In this case, Sulzer was contracted to complete a motor change-out due to deterioration of the installed equipment, which had been in service for 10 years. The environment on the FPSO is one of the harshest possible – the offshore oil and gas industry. It is therefore essential that every component within the motor is carefully examined and repaired as required.
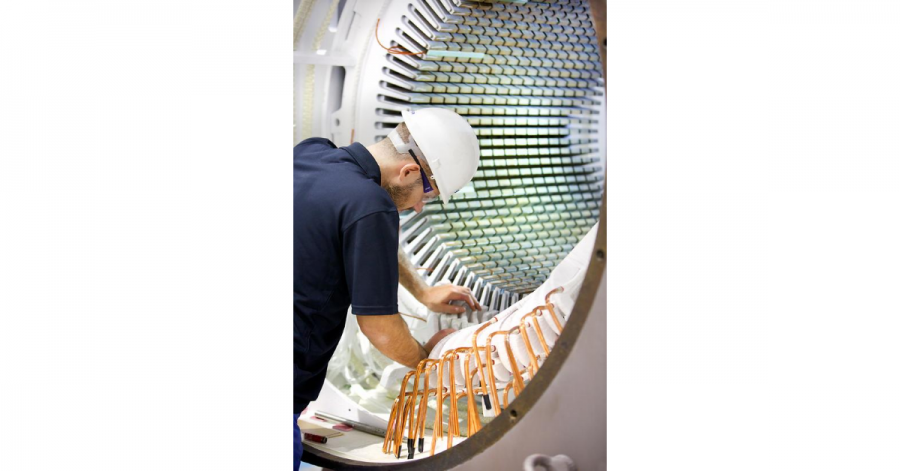
Repairs to the original motor included new stator coils to ensure at least another decade of reliable service
Marc Stuart, Falkirk Service Center Manager explains: “We became involved with this project right from the start, and we suggested a number of repairs to the out-going motor, including new stator coils, that would ensure the motor delivered at least another decade of reliable service. At Falkirk we have all the necessary facilities to complete the whole project in-house, including the latest in high voltage testing equipment.”
The motor, which was originally manufactured by Laurence Scott in 2007, powers a high-pressure export compressor. Sulzer is currently the authorized repairer for ATB Laurence Scott motors and offers its technical expertise and rapid response to all customers, especially those operating in the North Sea Oil & Gas facilities.
Specialist training
A complex lift plan needed to be put in place before the motor was loaded onto a waiting vessel and transported to Sulzer’s service center in Falkirk. A team of Sulzer’s engineers are specially trained for working in offshore environments and assist in disconnecting, removing and packaging the motor ready for transport.
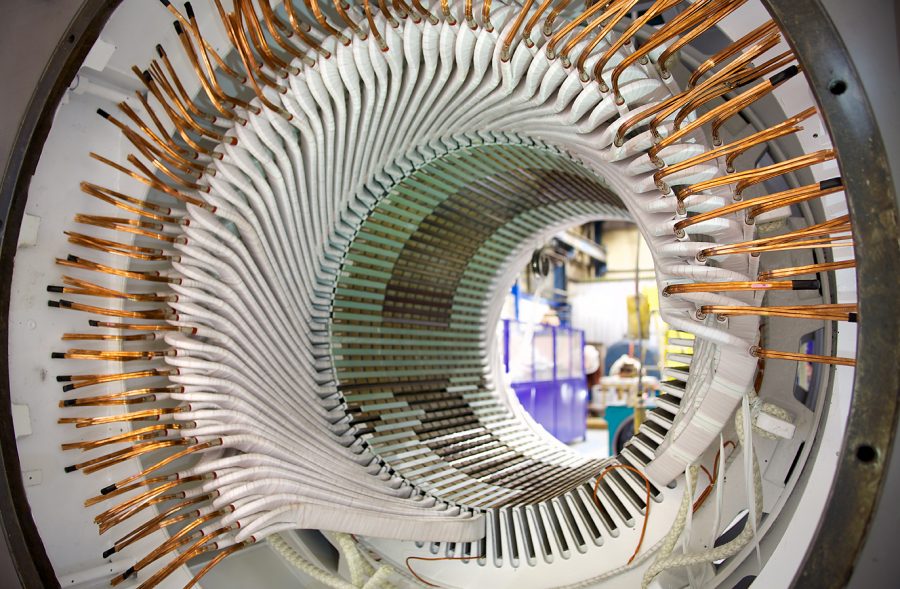
New coils can be delivered with a short lead time by Sulzer’s in-house HV coil manufacturing facility to minimize downtime
Although much of the refurbishment process was routine, special attention was required with all of the electrical connections and their enclosures to ensure continued compliance with Ex regulations. Any equipment that is designed for operation in potentially explosive atmospheres must be repaired and installed by suitably qualified engineers.
The facilities within the Sulzer network, such as the in-house copper mill and high voltage (HV) coil manufacturing center, combined with expertise in the offshore sector, were some of the many reasons that the company was selected. In this case, Sulzer was holding a spare motor in stock, and this would be installed to minimize downtime on the FPSO. Due to the complex crane lift required to transfer the motor onto the vessel, the operation had to be carefully timed to coincide with a calm sea state, which is something of a rarity in the North Sea.
Close cooperation
Marc Stuart continues: “In situations where an unexpected issue requires immediate attention, Sulzer can draw up a rapid response plan that will help a customer diagnose the problem and provide the most appropriate solution. Of course, the offshore industry is particularly averse to downtime of its equipment, so we can work round-the-clock to complete repairs in the shortest time.”
The close technical cooperation between ATB LS and Sulzer ensures that customers receive the highest level of maintenance service with the support of the original equipment manufacturer (OEM). That included a complete set of new stator coils, which were manufactured in Birmingham by Sulzer’s high voltage coil shop, while the mechanical repairs were completed in Falkirk.
Once all of the work was complete, the rebuilt motor was comprehensively tested before a full factory acceptance test (FAT) was carried out by ATB LS. The test ensures that the correct procedures have been carried out and that the rebuilt motor meets OEM standards and can be reinstalled.
Marc Stuart concludes: “Speed and expertise must go hand-in-hand for projects like this to be a success. Working with a team of skilled engineers that has the support of the OEM ensures the repairs will be delivered quickly, and in this sector, time is certainly of the essence.”
About Sulzer
Sulzer is a global leader in fluid engineering. We specialize in pumping, agitation, mixing, separation and application technologies for fluids of all types. Our customers benefit from our commitment to innovation, performance and quality and from our responsive network of 180 world-class production facilities and service centers across the globe. Sulzer has been headquartered in Winterthur, Switzerland, since 1834. In 2019, our 16’500 employees delivered revenues of CHF 3.7 billion. Our shares are traded on the SIX Swiss Exchange (SIX: SUN).
Comments