A great deal of the UK hydroelectric capacity was built during the 1950s. These installations have performed extremely well, especially considering the methods of design calculation that were available at the time of construction. Now, with over 50 years of renewable energy production achieved, the time for large scale overhauls and refurbishments is rapidly approaching.
While the design technology and materials have moved on considerably, one thing that remains constant is the remote location of many of these sites and the inherent logistical issues that arise when working on large rotating equipment. The challenges of delivering a refurbished hydro generator were recently highlighted when Sulzer’s Falkirk Service Center was awarded a turnkey project to repair one of two generators at the Lochay Power Station, near Stirling in Scotland.
The Lochay hydro power station scheme, with a total capacity of 47 MW, is part of the Breadalbane Hydro scheme. The two main generators are English Electric 22.5 MW units, which were commissioned in 1958. The remaining 2 MW are produced by a smaller Pelton turbine, which uses the compensation water that is released into the River Lochay when the main sets are not running.
Initial diagnosis
In 2012, one of the generators started to exhibit some noise and vibration issues and SSE, the owners of the installation, called in the specialists from Sulzer’s Falkirk Service Center to dismantle the generator in question and investigate the cause. The stator was originally built in two halves and bolted together on the frame on site, which is an unusual design for a large hydro generator, primarily because of the difficulty in transporting and moving the materials to the remote location during its construction.
The investigation found that a gap existed between the two halves of the core. During the original assembly on site this gap was filled with a strip of insulation material, but over time this had gradually deteriorated and an increased clearance had appeared between the two halves of the core.
When the generator started up from cold it would vibrate until it reached an operating temperature of around 50°C, when the core would expand and lock together and the vibration ceased. More recent energy demand in the area had seen the usual continuous operation of the generators being replaced with more frequent start and stop operation that was exacerbating the situation.
Considering the mature status of these generators, it was testament to their construction that only the bearings had been replaced during the past 60 years. However, the latest development indicated that a complete refurbishment would soon be necessary and so plans were put in place to complete the work in the most cost effective manner.
Logistical challenges
The nature of large scale hydro-electric power generation requires large volumes of water to descend through a significant distance before reaching the turbines. Suitable locations for such facilities are therefore relatively rare and nearly always in a more remote setting, away from major transport links and general infrastructure. As such this can present substantial challenges in terms of logistics and moving large components that need to be repaired.
In the case of the Lochay generator, these issues were compounded by the natural beauty of the surrounding area that attracts large numbers of tourists, especially during the summer months when the majority of the remedial work was being carried out. Fortunately, the Sulzer project management team has considerable experience of organizing and repairing hydro generators and it was able to minimize any disruption to the refurbishment schedule.
Remedial actions
After the initial investigation it was clear that ultimately the generator would need to be rewound, but in the mean time it would require a programme of remedial maintenance in order to keep it operational until the more substantial refurbishment project could be organized. Sulzer worked closely with SSE to develop the maintenance strategy that could be completed during the summer months in preparation for the winter period when local water levels would allow continuous operation of the generators.
Initially, a project was organized to tighten the core and re-wedge it in order to reduce the noise and vibration, which enabled the generator to continue operating through the winter of 2013. Further work was carried out in 2014 to reinforce the end winding consolidation before it was returned to service. For these aspects of the repair program, Sulzer worked closely with SSE, which provided engineers to remove the rotor, after which the Sulzer engineers would complete the remedial work and then allow SSE to rebuild and restart the generator.
In 2015, Sulzer embarked on the turnkey project to dismantle the generator and start the complete rewind process which would see design improvements that in turn would deliver considerable enhancement to its performance. Using the on-site lifting equipment, the 56 tonne rotor was removed to allow access to the stator and its windings which would be removed along with the stator core.
Design Specialists
The whole project was coordinated and run by the local service center in Falkirk but involved the skills and expertise from other key service centers including Birmingham, where the design improvements for the stator and coils were created. The first of these was the creation of a new one-piece core that would replace the original two-piece design.
The new core was constructed using over 30,000 plates to create the new lamination segments. Each segment was manufactured from a standard high grade lamination steel M330-50A-C5. Compared to the steel material used in the original design, the steel specific loss is reduced from 5.75 watts/kg to 3.3 watts/kg.
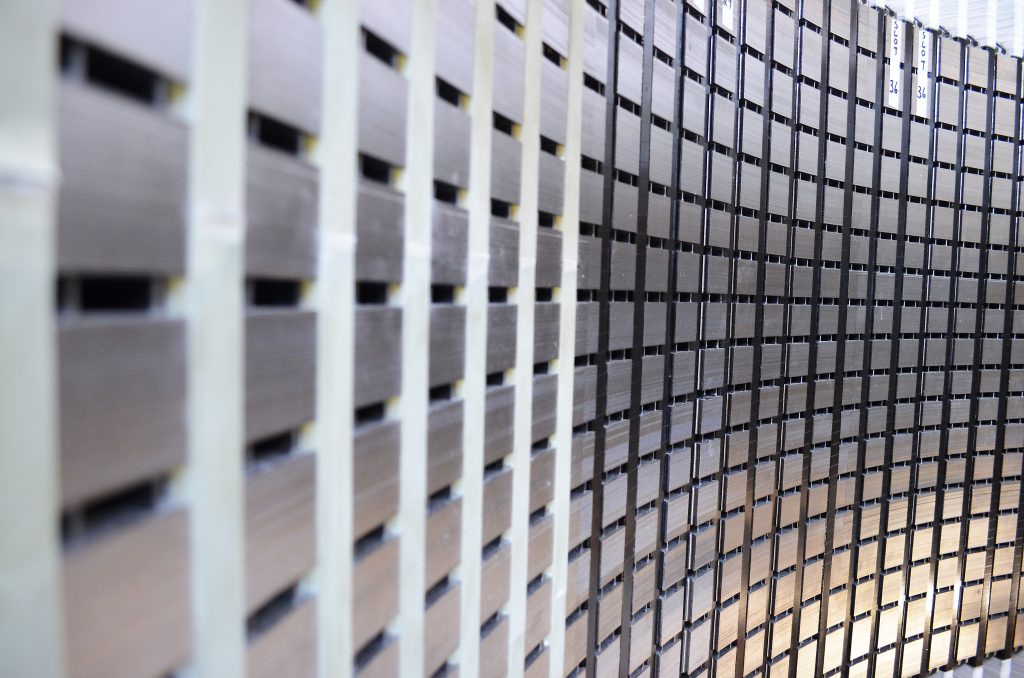
The stator contains 126 slots and the plates are designed in such a way that half of the laminations are split at the slot and the other half are split at the tooth.
The stator contains 126 slots and the plates are designed in such a way that half of the laminations are split at the slot and the other half are split at the tooth, which enables the core to be continuously built up with each layer overlapping the joints in the previous layer. The new segments are arranged with the clearance between them maintained to a minimum to allow for thermal expansion.
Additional design improvements were made including a new vent duct beam and support ring to ensure that the new core pack would be fully supported and pressed. New press fingers were also designed with better clearance to the coil side to prevent partial discharge on the overhang which was an issue that had occurred in the original machine.
Installation
The installation process involved the construction of a ring of plates around the stator frame to allow 22 hydraulic jacks to be used to pressurize each core pack and to remove any air pockets. The cylinders were connected to multi-port manifolds to ensure that the same pressure was applied equally around the core. Although a time consuming process, it was essential that the construction of the new core was of the highest quality to ensure the reliability of the generator when it was returned to service.
During the core assembly, a slot gauge was made to ensure the correct slot alignment; the core internal diameter was measured at eight radial positions and three heights to check the concentricity. The clearance between the core back and dovetail bars was also measured with a filling gauge for each core pack and each dovetail bar to check the consistency and quality of the core build.
In order to properly test the rebuilt core, a large generator was brought to site to provide sufficient power to test the core at a working flux level so that both iron loss level and power factor of the iron can be checked. The core flux test parameters were recorded and the temperatures recorded using a thermal imaging camera, which together determined that the new core was in excellent condition.
Following the assembly of the new core, the engineers used a high precision laser measuring device to create a complete 3D engineering drawing of the stator that was used to help create the new windings and ensure a perfect fit. These dimensions were used by the Birmingham service center to create a precision jig that was used to double-check to shape and dimensions of every new coil that was produced.
Technical expertise
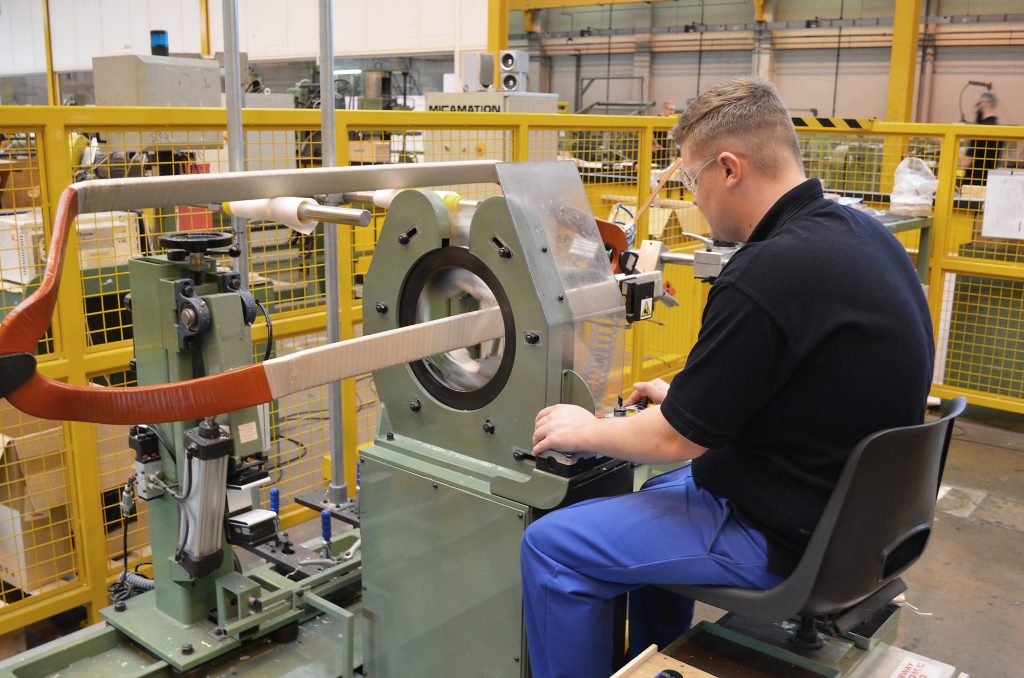
The new coils have been redesigned to account for the considerable improvements in insulation technology since the original was manufactured.
The new coils have been redesigned by the Group technical team at the Birmingham site to account for the considerable improvements in insulation technology that have occurred over the past 60 years. The insulation class has been improved from class B to class F, a modern resin rich insulation system that allows the thickness of insulation to be reduced, which results in an increased copper content in the slot.
The original windings had less copper content and a transposition from coil to coil connection was employed to reduce the eddy current loss. In the new design, the copper content in the slot is increased by 20%, the winding connection is redesigned from three parallel paths to six parallel paths and the number of turns per coil has changed from five to ten. The new design delivers a number of advantages, eliminating the need for the transposition which saves time, reducing the risk of connection errors, easing the winding connection and reducing the voltage per turn. The greatest improvement from the new design is the total copper loss which has been reduced by 10% taking into account eddy current losses.
Rebuilding
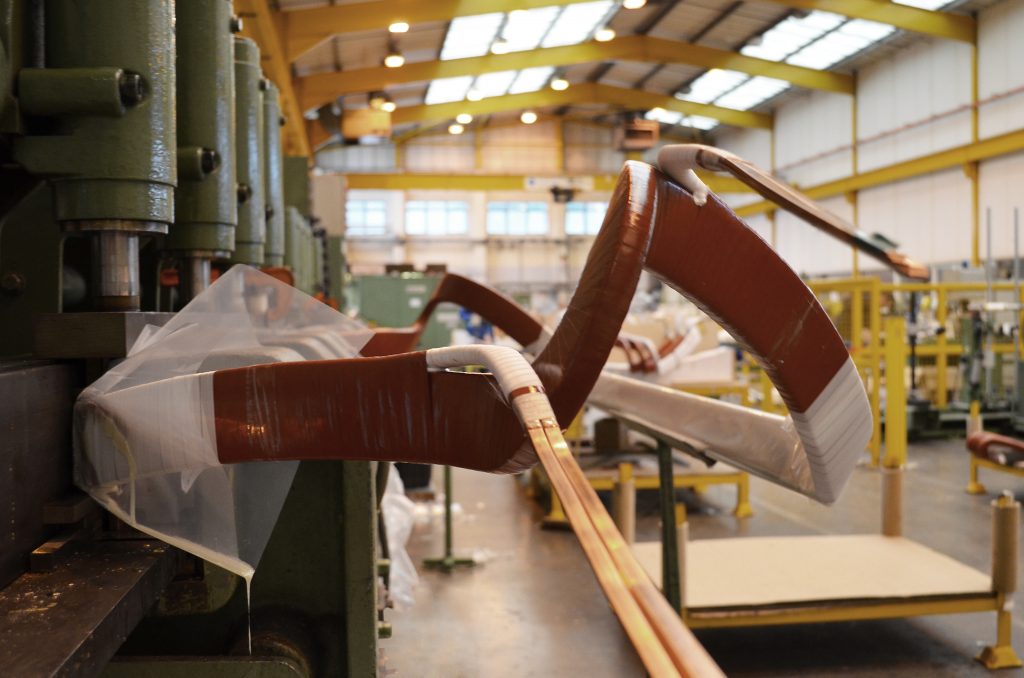
126 new coils were manufactured in Birmingham while the Falkirk Service Center reinsulated the 12 rotor poles using the latest class F insulation.
While the 126 new coils were being manufactured in Birmingham, the Falkirk Service Center reinsulated the 12 rotor poles, again using the latest class F insulation, in order to provide consistent durability throughout the generator. At the same time the Falkirk engineers also rewound the DC exciter train ready to be reinstalled once the stator coils were all in place.
Once the new stator coils started arriving on site the process of rebuilding the stator continued, with all of the coils being carefully positioned and wedged into place before the first round of high voltage tests was completed. After completing the coil connections and another round of HV testing, the generator was turned into an oven by sealing the unit and installing heaters before varnish was applied to the coils and baked in situ.
Finally, the rotor poles were reinstalled and the exciter train reassembled before the rotor was lowered back into place. Final tests were completed before the main covers were replaced and the generator recommissioned and placed back into service.
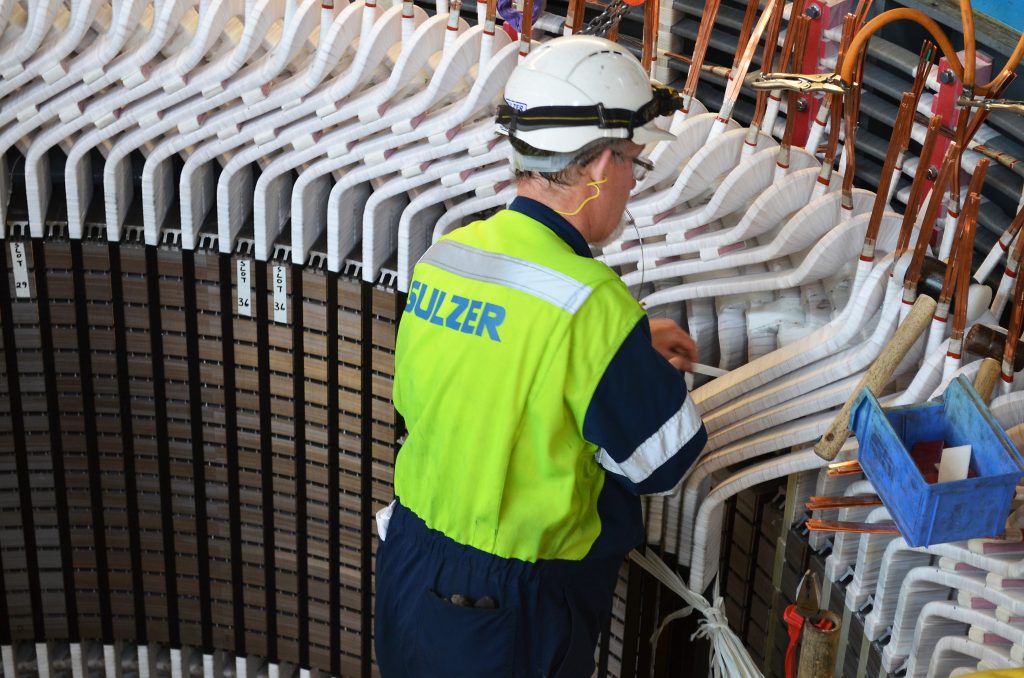
The Sulzer network allowed for experienced engineers from other service centers to be called upon to maintain the 24 hour schedule that was in place for a time.
This project has been managed from start to finish by the Falkirk Service Center, reinforcing Sulzer’s commitment to use one point of contact for the customer to simplify the communication process for the project. Behind the scenes Falkirk is able to call on the technical expertise in Birmingham and also bring in experienced engineers from other service centers to maintain the 24 hour schedule that was in place for a time. It is this cooperation and broad base of skilled engineers that allows Sulzer to deliver turnkey projects on time and within budget.
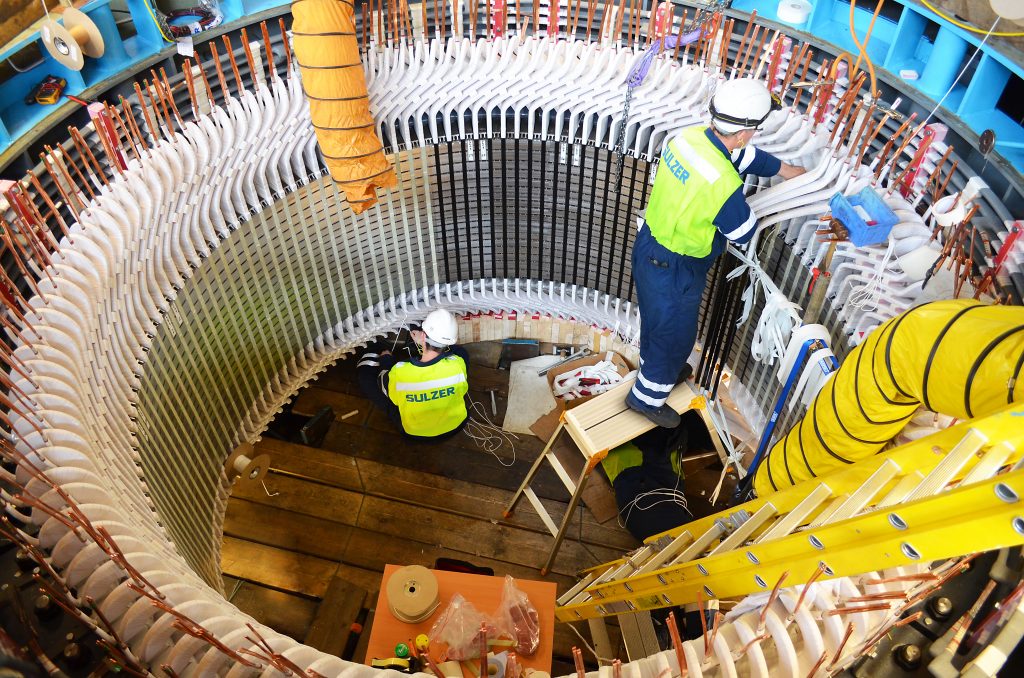
As a result of the improved design and the use of the latest insulation technology, the overall output has increased by 15%, from 22 MW to 25.6 MW.
As a result of the improved design and the use of the latest insulation technology, the overall output has increased by 15%, from 22 MW to 25.6 MW. Furthermore, these improvements and the physical assembly of the stator will rejuvenate and greatly extend the working life of the generator for another 40 years.
Comments