David Lozano and Roger Bosch, hydraulic engineers from AQUATEC (engineering consultancy company of SUEZ Group) were tasked with performing a hydraulic analysis of a pumping station in Barcelona’s water network, which is managed and owned by Aigües de Barcelona. The aim of the study was to determine the real impact of two different check valves on surge pressure and compare field data with model data obtained by using AFT Impulse.
Aigües de Barcelona is one of the main water operators in Spain, supplying drinking water to Barcelona and its metropolitan area for over 150 years. The huge network serves 3.2 million people in 23 municipalities. The performed analysis took place at the Tibidabo Pumping Station, which supplies water to the highest
neighborhood of Barcelona known as Vallvidrera.
Tibidabo Pumping Station (Figure 1 above) transfers water from 300 m (984 ft) above sea level, to 437 m (1,434 ft) above sea level. The pumping station is equipped with two pump sets with 78 l/s (1,240 gpm) capacity at 160 m (525 ft) of head.
Aigües de Barcelona was aware of how check valves impact surge pressure. They decided to install two different check valves to compare the pressures reached during the operation of the pumps: a conventional swing check valve from Ritag and a
non-slam nozzle check valve from Erhard.
The first part of the survey consisted of recording the surge pressure caused by stopping the pump sets installed: one with the swing check and the other one
with the nozzle check.
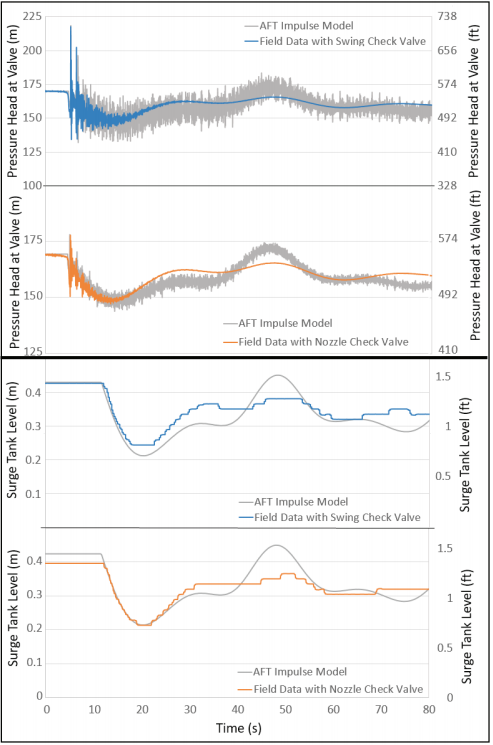
Figure 2: Measured vs. predicted pressure after pump trip for swing valve (top) and nozzle valve (second from the top). Bottom two reflect the liquid level of the surge tank
Field measurements (Figure 2 above) show the swing check valve raised pressure up to 48 m (157 ft) above operational gauge pressure (170 m/558 ft) while the nozzle check valve only raised it 8 m (26 ft). The maximum pressure variation (Pmax – Pmin) recorded with the swing check was 83 m (272 ft) while with the nozzle check it was just 31 m (102 ft).
After the transient events were measured, the pumping system’s GIS data was imported and used to speed the construction of a model within AFT Impulse.
The correlation between the field data and AFT Impulse model for the nozzle check valve is almost perfect for both maximum and minimum pressure (Figure 2, second from the top).
The correlation for the swing check valve and maximum pressure is accurate, but the minimum pressure predicted is significantly lower than measured (Figure 2, top). This could be explained by the significant vibration that was observed during the transient event that could partially dissipate the pressure energy.
Note that the designed anchor of the swing check pump set needed to be reinforced as a result of the stress caused by the initial surge pressures.
Finally, the surge vessel liquid level also shows an excellent correlation between AFT Impulse model and measured field data (Figure 2, bottom).
Comments