Author: Applied Flow Technology
Phil Sneeringer, Tier 1 Reliability Engineer at Flowserve Corporation, used AFT Fathom to perform a reliability study of a raw brine injection system consisting of five vertical pumps and five horizontal pumps. The system was used to displace product in an underground cavern storage facility at an undisclosed North American chemical plant.
Prior to the study, many of the pumps were competing against each other hydraulically. There had been 41 repairs on the system within five years costing more than $1.23 million, and the mean-time-between-failures were 14.63 months.
HOW A RUSSIAN HYDRAULICS HANDBOOK GAINED THE RESPECT OF THE AMERICAN NUCLEAR INDUSTRY
“There had been 41 repairs on the system within five years costing more than $1.23 million… AFT Fathom showed us the best way to run these pumps to maintain flow and pressure [and]…to increase reliability of the system,” explains Sneeringer. “Plant Operations needed adequate flow and pressure from this system to displace product in the caverns and clarifier wells at an acceptable rate to satisfy production goals.”
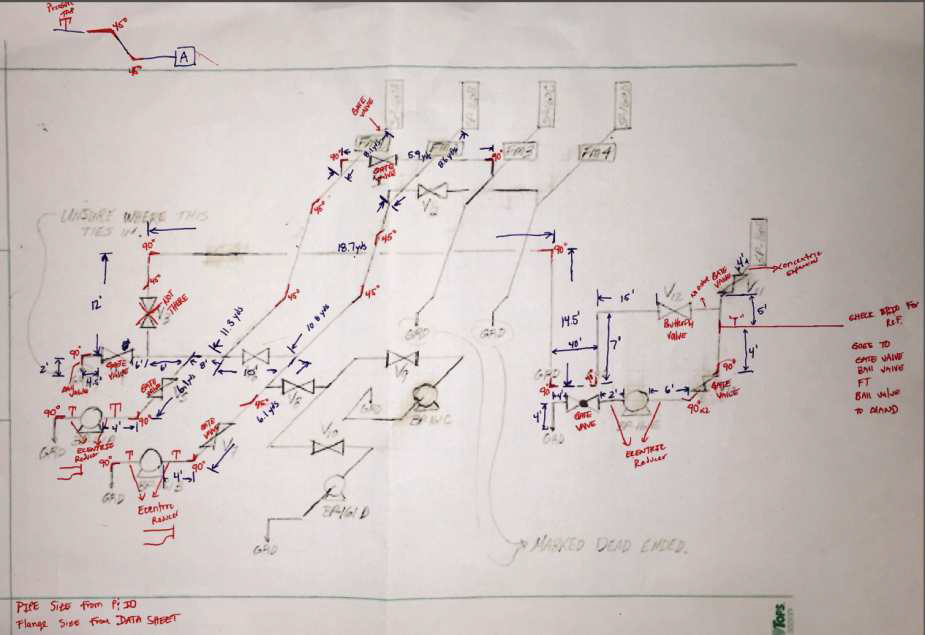
Figure 1 – The initial AFT Fathom model was created by using a field sketch of the system and P&ID drawings.
The first step of the reliability study involved creating a field sketch of the system as well as piping and instrumentation diagram drawings (see Figure 1 above). Sneeringer and the Tier 1 Reliability Team then collected actual field test data using wireless sensors and the customer’s in-line sensors that tied to their distributed control system. An AFT Fathom model was built (below), and the data was used to tune the model.
Multiple scenarios were then run (see Figure 2 below) to test different combinations of pumps and pressures at the delivery point in order to improve the pump flow rates from 35-50% of BEP to 75% (see Figure 3 below).
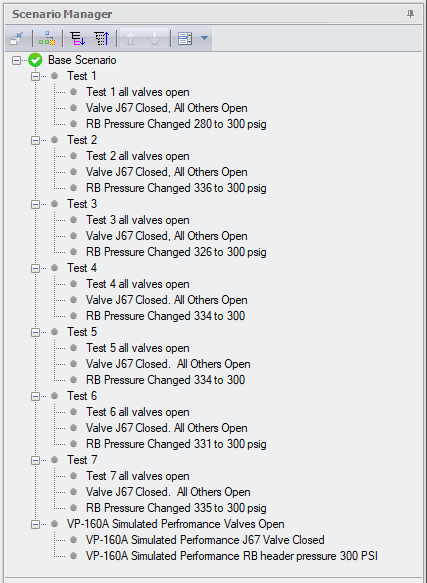
Figure 2 – Scenario Manager in
AFT Fathom used to test
different combinations of
pumps and pressures
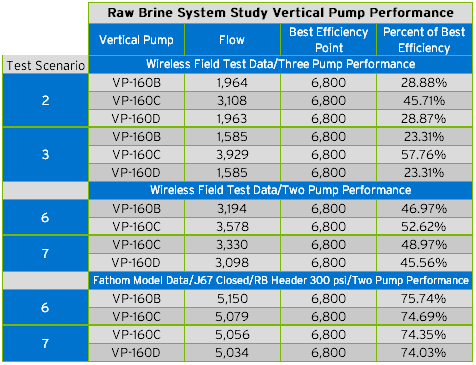
Figure 3 – Recommended operations improve
efficiency from 35-50% of BEP to 75%
(bottom two scenarios)
Through these simulations, Sneeringer was also able to determine a better flow path to deliver the same amount of product by closing a cross-over valve that had been left open.
“AFT Fathom showed us the best way to run these pumps to maintain flow and pressure,” Sneeringer said. “It allowed us to determine the best run combinations to increase reliability of the system (and)… to make recommendations on hydraulic re-rates to increase production in the future.”
Flowserve’s global team consists of more than 18,000 employees in 55 countries who put together the total solution—from project planning to life cycle maintenance programs to some of the most proven technology on the planet. Flowserve has more than two centuries of history—and this deep experience enables them to be a go-to resource for solving the toughest challenges across all industries.
Comments