The most common methods of monitoring the condition of pumps and other rotating equipment are vibration and surface temperature measurements. However, surface temperature and vibration measurements of the pump’s motor or bearing housing provide only half of the story.
The Main Causes of Vibration in Pumps
There are many sources of vibration in pumps. The most common causes include bent shafts, unbalances, misalignments, reaction forces, and contact between components. These issues can all be detrimental to the reliability and operation of rotating equipment.
An increase in vibration can result in:
- Excessive shaft movement that eventually harms seals
- Permanent indentations in bearings
- Affected clearances such as in bushings and wear rings
- Looseness
- Damaged components due to fatigue
Correlating Pump Vibration Monitoring with Process Pressure and Temperature
When we look at a pump and the causes for pump failure, we must take a broader look at all its components. It is important to note that pump failures do not always start with changes in vibration and surface temperature. Some pumps’ upset conditions start with changes in pressure — which ultimately translate to vibration. Fluctuations in the fluid characteristics, changes in rotation speed or direction, clogs on discharge or suction, and worn internal wet side components can all cause changes in pump pressure.
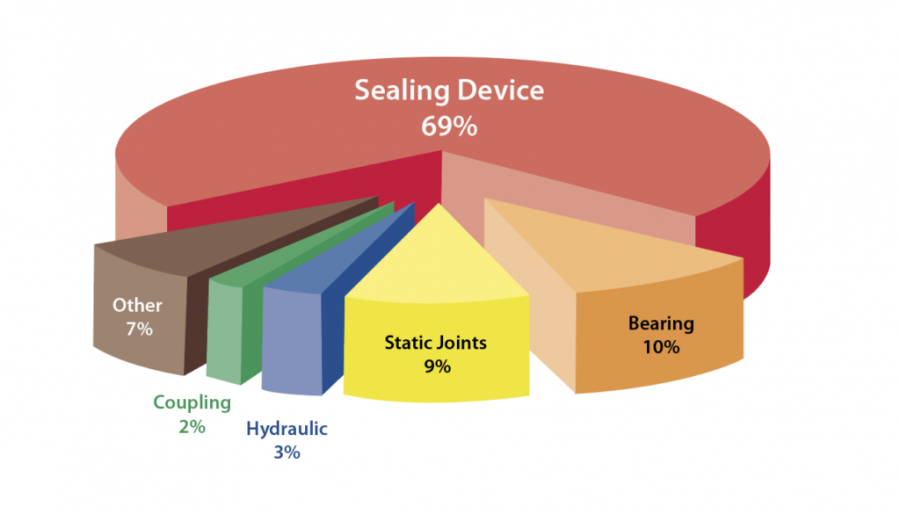
Graph: Pump Failure by Components
Pump Failure Point #1: Seals
The first most common component to fail in pumps is the seal. Seal failures can be caused by multiple factors, many of which are not detected in the early stages.
Some of the most common factors are pressure changes in the suction and discharge sides of the pump which directly disturb the seal chamber (also known as stuffing box) pressure and temperature — ultimately affecting the mechanical seal.
For example: during pump operation, an increase in vibration, followed by an increase in the seal chamber process temperature and drop in pressure is most likely caused by a restriction in the suction side of a pump.
In this scenario, if only bearing vibration and surface temperature are monitored, process changes inside the pump would go unnoticed. With an increase in seal chamber temperature and a drop in pressure, the sealing device (such as a single mechanical seal, or double mechanical seal with a buffer system) could experience dry-running like conditions, thus causing premature seal failure and ultimately pump failure.
For a double mechanical seal running a barrier fluid, monitoring the pressure and temperature of the barrier fluid tank and the process fluid inside the pump helps confirm the proper pressure differential, which is necessary to ensure adequate seal lubrication and operation.
Monitoring process pressure and temperature combined with vibration can provide a clear understanding of the pump’s condition, helping catch upset conditions to prevent failures and increase uptime.
Pump Failure Point #2: Bearings
The second most common components to fail in pumps are the bearings. Typically, bearing failures are caused by corrosion from seal leakage, equipment unbalance, shaft misalignment, damaged impeller, and others. Maintenance of bearings is normally preventive. Bearings are often replaced during seal replacements even when these are still in good condition.
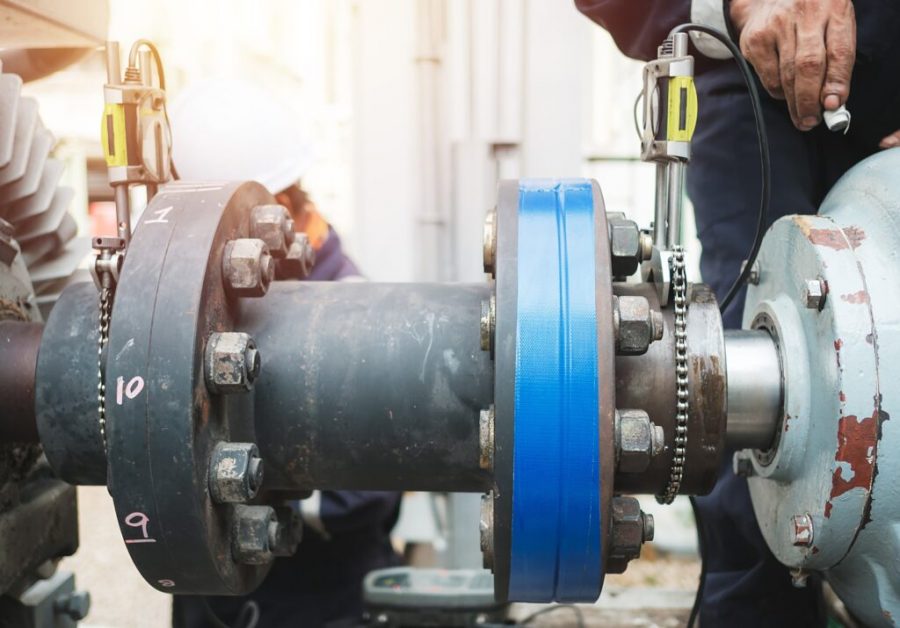
Technician inspector alignment pump and electric motor, Repairing work in factory concept
Complete Monitoring of Pump Conditions
In summary, it takes monitoring pump process pressure, temperature, and vibration to truly provide a full and accurate picture of a pump’s actual condition. The Chesterton Connect™ sensor, mobile application, and Cloud analytics provide 24/7 visibility of an equipment’s condition in all four areas (process pressure, process temperature, vibration, and surface temperature) to allow you to identify issues early and make corrections for overall increased reliability and improved plant performance.
The following are case studies demonstrating how the Chesterton Connect sensor was used to monitor process pressure, temperature, and vibration delivering critical insights for equipment savings.
Case Study #1: Identifying Dry Running Conditions
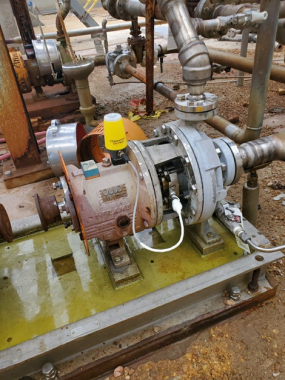
Chesterton Connect on Transfer Pump application
A chemical plant was experiencing an unusually high number of failures of single cartridge mechanical seals on a 65% Nitric Acid Transfer Pump application. The Mean Time Between Repairs (MTBR) was only 1.2 months.
A technician checked the operation of the system as well as the mechanical seal installation and found no noticeable issues in the operation of the pump.
Our Specialist recommended the installation of a Chesterton Connect. Within a few days, they were able to quickly gather enough information to determine that there was a negative pressure in the seal chamber when the pump was in operation. This negative pressure caused the mechanical seal to show classic dry running symptoms. After conducting a system audit, the customer was able to throttle back a valve to ensure proper flow from the pump.
The pump and mechanical seal are now running properly and the projected MTBR has improved to more than 24 months. The potential cost savings for mechanical seals for this one pump is more than $30,000. The savings due to reduced maintenance and operational improvements are estimated to be even greater, but at this time, are still being calculated.
Case Study #2: Vertical Turbine Booster Pump
A two-stage vertical turbine booster pump seal failed within 2-3 days. The seal was changed out, and again it failed within the same 2-3 day period. Clearly, there was a problem, but no one knew why, and it was impossible to ‘see inside’ the seal to determine the root cause of the problem.
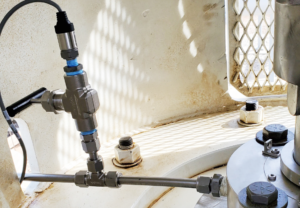
Chesterton Connect installed on Plan 13
Why Pump Vibration Monitoring is not sufficient on its own to avoid pump failure. A Chesterton Connect™ sensor was installed to monitor the process conditions causing premature seal failure. With the Chesterton Connect app, the user was able to chart the process pressure (decreasing) and temperature (increasing) while the pump was operating.
Because of the Chesterton Connect data, critical operating changes were identified and the seal failure problem was fixed.
Learn more about Chesterton Connect on the Chesterton website.
Juan Cid Product Manager at A.W. Chesterton Company
Juan Cid is a Global Product Manager at A.W. Chesterton Company for the packing and gasket product lines. He holds a BS in Mechanical Engineering and has over 5 years of experience designing products for rotating equipment. In his free time, Juan enjoys spending time with his family on outdoor activities such as hiking and traveling.
Read more about equipment reliability from A.W. Chesterton.
As the retired senior Staff Chief Engineer and being involved is new and rebuilt pump systems and a member of the design team of the Three Jumbo Mark II 470 foot foot 16,000 HP vessels. I dealt with many many pumps and their choice and installations. One major point was the types and materials of the couplings and flex joints and to make sure that proper alignments and installations. The wrong choices with only price is the worst way to buy equipment as the old saying of ( Pay me now or pay me later has never been so true.)