How can you make the best choice when selecting a sealing technology for a pump or mixer that handles slurry? Due to the widely varying nature of slurries and equipment, there is no one right solution. A.W Chesterton recommends using a multi-faceted “Best Available Technique” approach to get the maximum return on your overall investment.
Slurry Sealing: Higher Stakes
Slurry is the mixture of an insoluble substance consisting of solids suspended in a liquid matter that is generally, but not always, water. Slurries will vary depending on the properties of the solids. They can be abrasive and corrosive, and create a variation in the viscosity of the fluid.
Choosing the right sealing technology for a pump or mixer has a significant impact on the lifetime operational cost. When sealing slurries which can take an enormous toll on equipment, there are even more dramatic consequences at stake. Sealing slurries often results in potential clogging, abrasion, and significant energy costs. And in industries such as mining or ore processing, the situation is often compounded by operations in remote locations that have little backup inventory and 24-hour operational expectations.
Steps to Improved Slurry Sealing Returns
Our next series of posts will lead you through the slurry sealing selection process to include:
Justifying the sealing investment: Selecting the proper sealing technology should be viewed as an upfront investment measured against the total Lifecycle-Cycle Cost (LCC) of the equipment
- Best Available Techniques (BAT): Use this approach to determine which sealing upgrades will have the biggest return
- Slurry types: Understand which technology is the best fit for the slurry being handled
- Environmental stewardship: Your company’s concerns here can play a significant factor in the sealing selection.
- Sealing characteristics: Learn which kinds of mechanical seals and packing are best for specific slurries
- Piping plans (environmental controls) for slurries: Discover the ideal approaches for specific applications
Considering the Seal Investment in Context
The initial purchase price of a sealing technology is actually only a fraction of the equipment’s total Life-Cycle-Cost (LCC) and must be analyzed in that context. While the upfront costs for a mechanical seal may seem significant, that expense often pales compared to the cost of operating the pump over its lifetime with an inferior sealing solution.
Life-Cycle-Cost factors include:
- Equipment purchase price
- Operational costs
- Repair & labor
- Downtime costs (i.e., reliability)
- Energy costs (which can be the highest single expense over the life of a pump)
- Water costs
- Pump efficiency
- Environmental cost (fines/contamination)
- Safety /maintenance costs: brought about by excess seal leakage
Having a good understanding of the LCC for each piece of slurry sealing equipment goes a long way in helping to justify up-front investments and making the most long-term, cost-effective decision.
Using the Best Available Techniques (BAT) Approach
This formal approach involves surveying the equipment population, identifying bad actors, defining the goals to be achieved, conducting root cause failure analysis and slurry classification studies, and then using the information collected to implement a sealing technology to meet the defined goals.
Using this approach to seal selection focuses on optimized economics and takes into consideration:
- Logical spending
- Increased reliability
- Lowered operational costs
1. Identify the “Bad Actors” — Equipment with a High Cost of Ownership
The first step in BAT is to identify the small percent of equipment that is under-performing on the sealing front and resulting in unnecessary spending.
To identify the pumps that are most worthy of sealing upgrades, we recommend a formal survey. This can include the entire pump population involved in slurry processes or a specific bank of pumps.
Pump Efficiency Assessment – Improved Slurry Sealing
Keep an ongoing spreadsheet or database that tracks:
- Equipment type/brand
- Current sealing technology/product
- Slurry type (addressed in the next section)
- Piping plan used
- MTBM or MTBF and associated downtime
- Root Failure: Save your failed mechanical seals and packing to determine why it failed. Chesterton and many other seal manufacturers offer failure analysis.
Beyond an immediate survey, you will want to expand this tracking to include:
-
Identify the 20% of equipment causing the bulk of work disruptions.
Leakage concerns
- Maintenance costs
- Yearly water costs
- Yearly energy costs
Out of this process, you will determine which equipment is worth an investment for upgraded slurry sealing. It is not unusual to discover that an estimated 80% of the maintenance costs are associated with less than 20% of the equipment.
2. Identifying Slurry Classifications
As the part of the BAT process, you will want to identify the specific classification of slurry being handled by each piece of equipment. You’ll be using this down the road to match the slurry to the most reliable slurry sealing solution designed for the lowest operation costs.
The particle hardness, size, and sharpness assist in defining slurry properties that can be grouped into three classifications of slurries:
Settling Slurries
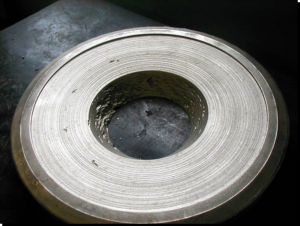
Figure 2- Abrasion Caused by Settling Slurry
Also referred to as Newtonian slurries, this slurry type contains particles which are .003 inches/75 μm or larger and allow the fluid to flow freely. The particles found in settling slurries can be hard and sharp causing the slurry to be highly abrasive (Figure 2). Typically with this type of slurry, the solid particles will settle out of the slurry. One example of settling slurry is minerals in solution (think of a bucket of sand and water at the beach).
How does this impact your sealing choice? Good “flushless” seal performance occurs when solids settle quickly and seal faces remain lubricated. There is sufficient “free” water available.
Non-Settling Slurries
Also known as Non-Newtonian slurries, this slurry type allow particles to remain in suspension. If more than 50% of the particles are smaller than .003 inches/75 μm, then the viscosity of the slurry will change as it flows. Non-settling slurries can be less abrasive. However, they have less free fluid (Figure 3) to lubricate seal faces. Corn starch in solution is an example of non-settling slurry.
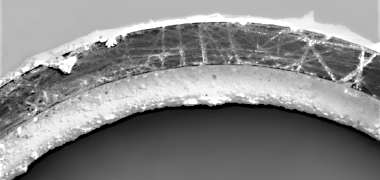
Figure 3 – Damage Caused from Non-Settling Slurry
How does this impact your sealing choice? Harder to seal “flushless” when slurries absorb carrier liquid and don’t settle quickly particles can migrate across the seal face.
Dewatering Slurries
This slurry type contains particles that are less dense than the fluid and are often found to be fibrous and abrasive. The particles have a tendency to adhere to surfaces around the seal and can absorb fluid starving the seal faces of lubrication. When this occurs the seal faces will increase temperature causing heat checking (Figure 4). An example of dewatering slurries is fine paper/pulp stock.
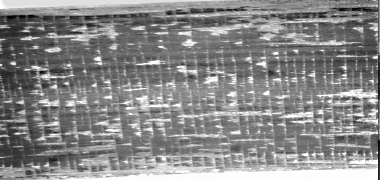
Figure 4 – Heat Checking Caused from De-Watering Slurry
How does this impact your sealing choice? Difficult to seal “flushless” when solids do not settle or can stick to a wall. Flush volumes often need to be increased to saturate and wash away fibrous media. Care should be taken not to add cost to the process.
3. Identifying Environmental Concerns
The final step in in preparing to select the right slurry sealing technology is examining environmental goals and concerns. This includes your organization’s overall sustainability goals as well state/province mandates for water consumption and effluent discharge.
Because of the nature of slurries, leakage is often more of a concern and this may be a lead factor in guiding your selection decision.
Decisions on this front include:
- What amount of seal leakage is acceptable?
- Is leakage a concern loss of product, which can be very expensive over time?
- Is the goal to reduce heavy-duty flush-less slurry seals?
- Environmental controllers to reduce flush?
These decisions can result in the choice of a lower or higher cost sealing alternative. For example, if there is an acceptable amount of leakage for a specific application, packing will provide a lower cost solution.
Comments