Isolation gaskets may seem to be a complicated subject when trying to determine what is required and whether you require them at all. When looking at possible isolation gasket application requirements I like to put on my “Sherlock Holmes” hat and asks myself the following 5 W’s – What, Why, Where, When, and Who.
What
Let’s begin with what are isolation gaskets? Isolation gaskets are exactly as they sound, they isolate flanges from the flow of electrostatic charges through the pipeline and or can separate dissimilar metals which can cause galvanic corrosion. For galvanic corrosion to occur you need an anode (metal 1), cathode (metal 2), and an electrolyte or carrier such as water to help allow the transfer between the two metals. The anode will be the sacrificial material and will corrode at a much higher rate than the cathode; in some cases, the cathode material may even stop corroding completely. The further the two metals are apart on the galvanic corrosion chart (Most Noble – Cathodic to Least Noble Anodic), the higher the potential for corrosion (See Figure 1 – Dissimilar Metals).
Durlon® iGuard™ isolation gaskets are commonly sold in kits that are composed of a gasket, a set of insulating sleeves for the bolts, 2 sets of insulating washers, and two additional sets of steel washers. (See Figure 2 – Isolation Gasket Kit Components). The gaskets themselves can be either full face (Type E), ring style (Type F) or RTJ (Type D) and are offered as a carrier ring such as phenolic, neoprene faced phenolic, Silicone Glass G-7 or Epoxy Glass G-10 or G-11 and comes standard with a Viton sealing element but has other sealing element options such as PTFE, nitrile or EPDM. Additionally, the gaskets can also be composed of sheet material such as Durlon® 8400, 8500, or 9000 (1/8” thickness recommended) which have excellent dielectric breakdown properties (371 – 406v/mil). The standard offering for isolating sleeves is mylar, Phenolic for the isolating washers, and zinc-plated steel washers. Additional materials for the isolating sleeves and washers are available upon request.
Why
Galvanic corrosion is a big problem because it can lead to a rapid metal loss in piping systems and tanks. It can cause leaks or even failures which can have catastrophic consequences for plant personnel safety and the environment.
Where
Isolation gaskets are found anywhere that you have flanges that consist of dissimilar metals such as cast iron to carbon steel or even aluminum to stainless steel for instance. The isolation gasket kits create a dielectric break which generates cathodic protection for both above and underground piping where metal components that are in contact which each other in the bolted flange joint assembly. Isolation gaskets are commonly used in the petrochemical industry, oil & gas, and marine/offshore applications that deal with high chlorides such as seawater.
When
Whenever galvanic corrosion or electrical isolation is a concern in the piping system. It should also be noted that there are additional benefits to using isolation gaskets (carrier ring with sealing element) such as: Isolation gaskets seal at very low stress, perfect for low torque requirements. Installations that have frequent assembly and disassembly, such as pressure test stands. These can be reused multiple times due to their resilient double-ogee sealing element (normally it is not recommended to reusing gaskets).
Who
Engineers, plant & maintenance managers, pipefitters, and installers can all use the benefits of Durlon® iGuard™ isolation gaskets for plant piping protection in both new design and existing piping systems.
So, if you are wondering if you need an isolation gasket for your application, there is a good chance you do, but if you are still not sure……give us a call and we can help guide you through the isolation gasket material selection process.
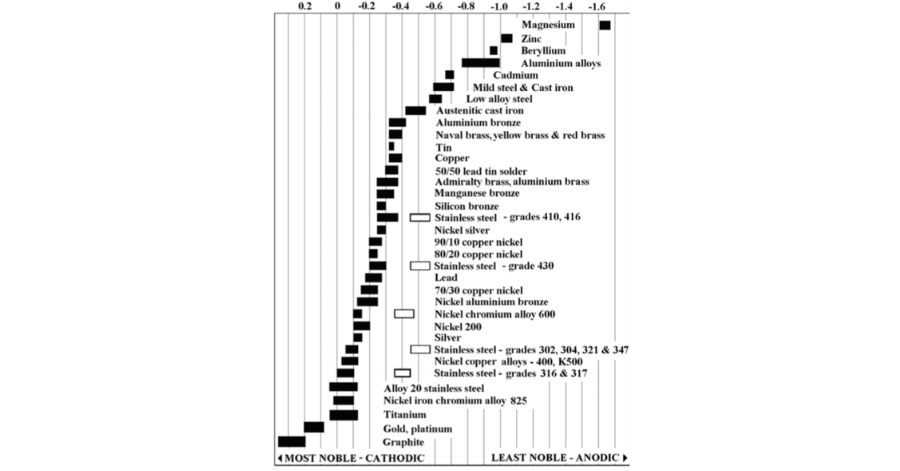
Figure 1
Comments