The Challenge: A major oil producer was facing the potential of huge capital investments to meet increased oil production requirements. A series of ISO 13709/API 610 (BB5) multistage barrel pumps in brine injection service needed to deliver 40% more capacity.
The Solution: To avoid major capital expenditures and control ongoing operating costs, Flowserve engineers designed a highly efficient hydraulic cartridge that could be easily retrofitted to the existing pump installations with minimal disruption to operations.
When a major oil producer was faced with potentially significant capital investments to meet increased production requirements, Flowserve was consulted to evaluate and implement a cost-effective approach for increasing injection water flow rates for a number of multistage barrel pumps. Any recommendation had to account for the following project constraints:
- Minimized capital investment
- Minimal production downtime
- No changes to pipework or ancillary equipment, including oil lubrication and vibration monitoring systems
- Compliance with temperature limitations and stringent vibration level restrictions
Cartridge Approach Yields Huge Savings
To meet these challenges, Flowserve designed and manufactured a new hydraulic cartridge suitable for installation into the existing barrel and discharge head. This cartridge also incorporated the same balance drum, mechanical seals, oil lubrication system and bearing housings as the original pump, easing the changeover and minimizing the effect on customer inventory.
Engineered Performance
Flowserve engineers undertook a series of steps to ensure the hydraulic cartridge design was optimized to reduce energy consumption while ensuring reliable operation once in service. These steps included:
- Full hydraulic design and analysis of new impellers and diffusers
- Critical speed and finite element analysis (FEA) of the new shaft
- Casing design analysis to optimize throat and volute areas to increase flow and optimize pump efficiency – a process that allowed the customer to avoid the expense of new drivers in spite of the increased flow requirements
Required Duty Conditions
Fluid: Brine at ambient temperature
Original | Revised | |
Capacity: | 365 m3/h (1606 gpm) | 510 m3/h (2244 gpm) |
Head: | 1790 m (5873 ft) | 1790 m (5873 ft) |
Bottom Line Impact
The Flowserve cartridge solution represented a significant cost savings over original equipment options. In addition, this solution met key customer requirements for minimal process disruption by easily retrofitting to the existing installation. Most importantly, by optimizing pump efficiency, the customer now realizes ongoing energy consumption savings in excess of USD 45 600 per year while having avoided major expenditures for new drivers.
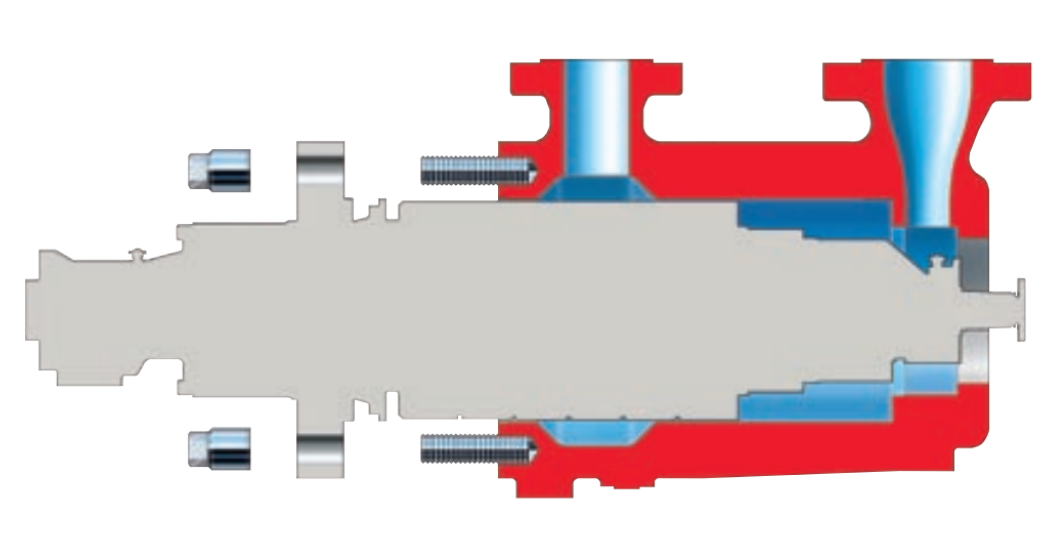
Cartridge construction reduces downtime and minimizes capital investment
Comments