Using existing sensors to improve energy efficiency and reliability
When you first designed your pumping system you took great care to pick the right pumps for the job. You picked from choices that would work with the process demands and constraints in the environment, and then optimized them according to manufacturer’s pump curves. This included selecting the Best Efficiency Point and selecting the right HP motor for the job.
But that was a while ago. And process requirements have shifted and there have been improvements to the piping infrastructure and new pumps introduced. All the while energy costs continue to rise and there’s always more scrutiny over how efficiently the pump environment is running.
A path to get more insight into the health and efficiency of your pumps is the power sensor you may already have installed to monitor and protect pumps and their motors.
How does Power Monitoring Work?
Power, measured in HP or Watts is calculated from the electrical connections powering the pump’s motor. By multiplying Voltage X Current X Power Factor (loosely described as the energy required to charge the coils in the motor) we can get an accurate view of the work the motor is doing. This gives us a signal to monitor and control pumps:
- When flow rate is low, Power is low
- When flow rate is high, Power is high
- At light load conditions, caused by cavitation or dry running, measuring the change in
Power is 10X more sensitive than Current (Amps) alone.
Measuring power requires no direct mechanical attachment to the pump or motor, and can be done in an environment free from potential manufacturing hazards such as the Motor Control Cabinet.
Benefits of Power monitoring include real-time feedback on process status, flow and viscosity changes, dry running, cavitation, impeller loss and other error conditions and maintenance issues
Adding in the Pump Curve
Looking at a typical pump curve such as Figure 1 we see that when arriving at a Best Efficiency Point (BEP) a corresponding recommended motor HP can be determined. For this example the BEP would dictate a 30HP motor.
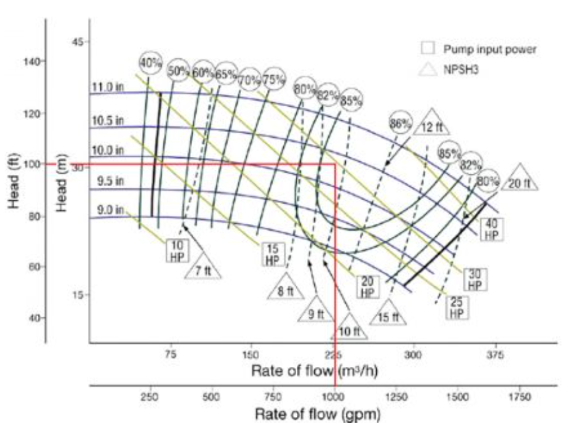
Figure 1: Sample Pump Curve Courtesy: Hydraulic Institute
By using a load control, or motor power sensor, the actual HP requirements of the current process can be captured over time. By comparing the average and peak HP requirements with the installed HP motor and the theoretical pump curve we can draw important insights:
Is the motor potentially oversized (actual HP measured much less than stated HP on the motor)?
Causes for this might include:
- Process changes and improvements that reduce operating Head or Flow
- Addition of new pumps in parallel functions
- Lower throughput requirements based on lower demand from the business
- Overly conservative sizing during the initial installation
- Replacement impeller sizing that places lower demand on the pump’s motor
Or you may find that the process has moved further out (down and to the right) the pump curve indicating the pump motor is potentially undersized. Causes of this under sizing include:
- Increased Flow requirements from the process or business
- Process changes over time that increased Head or Flow
- Aggressive cost savings approach when initially sizing the pump motor
- Wear or maintenance needs
- Spikes from seasonally high demand that were not originally forecasted
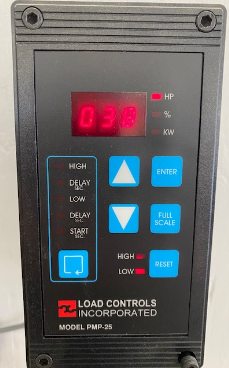
Figure 2 Load Controls PMP-25 Pump Control with HP Display
The Implications
In the case of oversizing there can be significant expense implications. Some industry analysts estimate that up to 75% of installed pumps are oversized, many by as much as 20%. Identifying a 30HP pump motor that is oversized by 20% could save over $25,000 per pump per year. This would yield a payback period for a newer, more correctly sized motor, of just a few months. With industrial pumps accounting for as much as 25% of the world’s energy consumption, the potential for significant impact and savings is large.
Undersizing of pump motors can also be a problem over the long term. Reduced motor life, overheating and excessive wear can cause maintenance headaches. Downtime, whether planned or unplanned can cost valuable productivity and margin loss. Failure of the pump system can also lead to significant cleanup costs and potentially safety risks in the event of a catastrophic event.
By leveraging an existing investment in pump power monitors or load controls, smart pump managers can raise the efficiency, lower operating costs and reduce risk. Analyzing HP data that is readily available from these sensors can unlock significant business benefit and should be part of any forward-thinking pump management program.
About Load Controls, INC.
Since 1983 Load Controls has been providing Power monitoring solutions for Chemical Processing, Pharmaceutical, Food Processing, Paper, Waste Treatment, Machine Tool and other process manufacturing applications. Our sensors and controls are in use by 9 of the 10 world’s largest chemical processing firms, and 9 of the 10 largest Pharmaceutical companies globally. All of our products are manufactured in the USA.
Visit www.loadcontrols.com for more application use cases and product information, or to request a 30-day trial.
Read more about Power monitoring.
Comments