Author: Sven Olson
Multiphase flow is a familiar concept and a natural physical state of the flow regime coming off the wellhead in oil and gas production. Multiphase pumping, however, is much less commonly known. It is becoming increasingly used by operators around the world as a tool for more economical and environmental friendly oil and gas transport. The whole idea is to flow and pressure boost the raw well stream before separation, treatment and processing. This leads to a number of production improvements for the operator and to a simpler and more economical way of transporting hydrocarbons over longer distances from the producing field to the process facility.
Multiphase boosting and gathering in general is not needed as long as the energy in the reservoir is able to overcome backpressure created by flow line drag losses, terrain variations and the arrival pressure at the first state separator at the process facility. In the early life of the reservoir, the natural gas cap drives the liquids to the surface where often a choke in the wellhead has to be used to restrict pressure. As the reservoir matures, the pressure drops off, the choke is eliminated and the backpressure starts to reduce the flow at the wellhead. This cycle will happen naturally over the life span of the reservoir. The increasing backpressure can be dealt with by enlarging flow lines and the use of low-pressure separators. Or, as is most common, a different type of artificial lift such as ESPs and gas lift or conventional pump jacks can be added. This approach may help some wells but others on the same gathering system are held back by the backpressure.
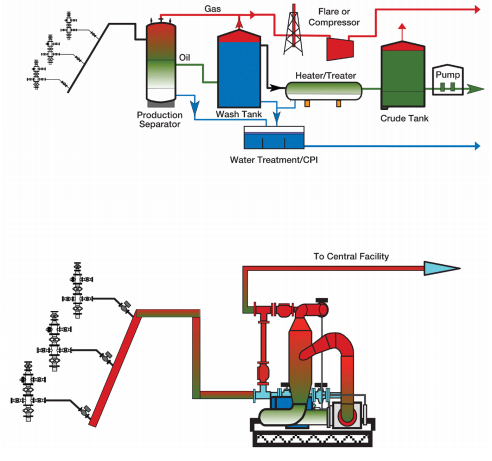
Simplifying facilities by eliminating process equipment
Here is where multiphase pumping comes in as a valuable tool. Multiphase pumping offers the unique solution to gather and boost both gas and liquids in one process with one single piece of machinery. The pressure in the oilfield gathering system can be lowered to a point allowing all producing wells to come online and produce. Also low pressure wells and previously shut-in wells are brought back to production without separation, flaring or venting. Alternatively, a smaller multiphase pump can be tied to the annulus gas outlet of a single well and bring that well to production.
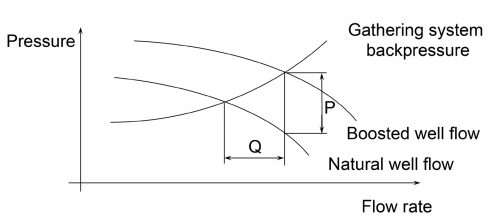
Pressure boosting (P) leads to producton increase (Q).
The development of multiphase pumping is moving forward at a steady pace and new applications of technology have demonstrated their usefulness to operators all over the world. Below are some of the most important motivators to operators to apply the technology, which in turn encourage suppliers to emphasize the development of better system solutions, improved reliability and to extend the range of operation of pumps.
Reduced facilities
Pumping the total production from the field to a central processing facility onshore or as a tieback to a platform or FPSO in a single flow stream of oil, water and gas in one flow line thereby eliminating separation and compression equipment and installations. Compared to conventional equipment much less footprint is required.
Adding production and enhancing total recovery
Lowering the gathering pressure leads to lower bottom-hole pressure, which in turn improves the reservoir to wellbore liquid inflow. The result is increased production, enhanced total recovery, extended field life and delayed well abandonment. The draw down of the gathering system pressure will also assist low-pressure wells to overcome the system backpressure and add to production.
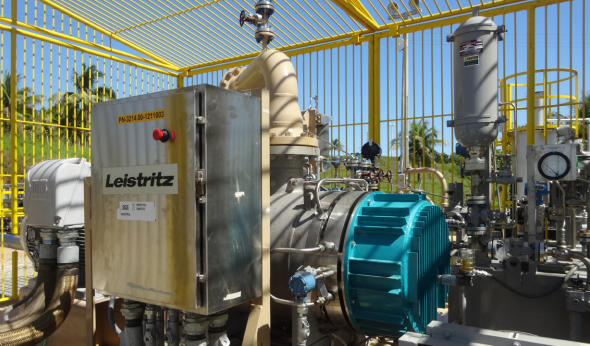
Multiphase pump for gathering and boosting.
Environmental impact
By eliminating flaring or venting of gas during production, blow down operations and well testing, regulatory restrictions on methane emissions can be met. Strict new rules and regulations to limit emissions from hydrocarbon production are now in place in many countries throughout the world.
Hydrate, paraffin and emulsion mitigation
Multiphase pumping, especially when using twin-screw pumps, can contribute to mitigate hydrate blockage by lowering the pressure in flow lines below hydrate formation point. The pump can transport hydrate slurries speeding up recovery of hydrated flow lines avoiding issues with shut in production. This helps to reduce costs for MEG handling. Extra heavy crudes, often appearing as shear sensitive water/oil emulsions and waxy crudes can be pumped without risking blockage. The efficiency of the first stage separator can be improved, as these emulsions are easier to break up.
Eliminating slugging and surging
Multiphase pumps will provide a smooth pumping action with any flow regime without pulsations and vibrations, even in wells with very high gas production. The pumps and header system can be designed for parallel operation at high GVF (gas void fraction) without detriment to the equipment. Due to a liquid management and recirculation system it is possible to mitigate the hazards of slugging and surging in flow lines and risers.
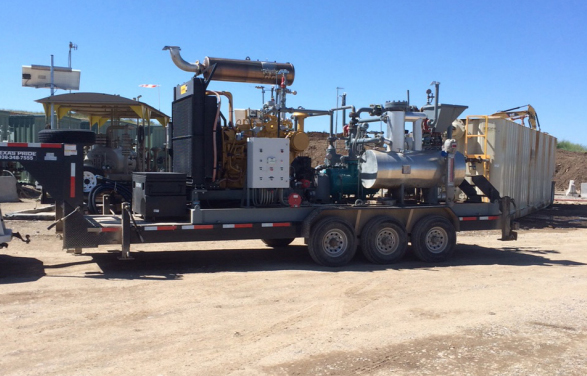
Portable multiphase pump for gas well de-watering.
Subsea boosting
With production coming from ever-greater water depth combined with the desire to extend the tieback distance from a platform or FPSO, multiphase pumping technology has become increasingly important. Deepwater reservoirs sometimes with high viscosity and high gas production can now be produced successfully. A multiphase pump unit located on the sea floor close to the producing subsea well can boost the combined production to the surface, overcoming pressure losses in flow lines and risers. With extended tiebacks the need for costly additional platforms and fixed structures are reduced. The units can be also deployed and retrieved using modern intervention vessels, which save on operating costs.
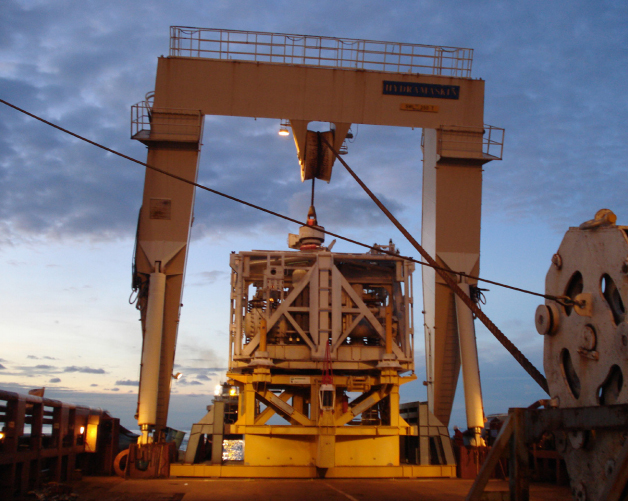
Subsea multiphase pump during deployment.
Multiphase pump designs
This article focuses on multiphase pumps of twin-screw positive displacement type. The second pump type used is known as the helico-axial pump, which follows the principle of the hydrodynamic pump where the hydraulic performance is dependent on flow density and inlet pressure. Of the approximately 500 multiphase pumps currently installed around the world, roughly 50 are the helico-axial type and the balance mainly twin-screw pumps.
Twin-screw multiphase pumps, work with fixed displacement pump chambers, where each chamber, formed when the two meshing screws rotate, delivers a constant volume from inlet to outlet. In order to compress gas, the liquid phase of the multiphase flow becomes very important. The twin-screw pump uses two opposing sets of screw profiles to move inlet flow from opposite ends of the screw sets towards the middle where it discharges to the pump outlet. Using rotational speed of the screws, centrifugal forces will cause the liquid phase to split and separate from the gas phase. As a result, the liquids will concentrate in the perimeter of the screw set and in the annulus between the liner and the screw tips and the gas along the root of the profile.
When the pressure increases from inlet to outlet, the liquid phase will become more defined and a laminar stream of liquid is formed along the screws tips moving in the opposite direction of the main flow stream from high to low pressure.
As the liquid reaches and fills the next upstream pump chamber, it will compress the gas collected in the core of each chamber. Overflow liquid will continue to fill the next upstream chambers and gas is compressed as the liquid continuously fills the chambers. This process continues as long as the screws rotate; the re-combined liquid and compressed gas will reach the outlet of the pump and continue to move downstream. Although the twin-screw multiphase pump is a constant displacement machine, the back flow of liquid makes it a virtual variable displacement pump thereby allowing it to compress gas.
At the same time, the pump also functions as a conventional pump, allowing it to handle 100% liquid phase at any time, which is of course not possible in a conventional compressor.
The presence of liquid is critical to successful gas compression in a multiphase twin-screw pump. The liquid serves to seal the screw profiles and compress the gas, as well as removing the heat from compression. The liquid fraction should be kept at 3-5% (95-97% GVF) of the inlet flow for most twin-screw multiphase pumps. At higher GVF (98-99%) the integrity of the liquid phase is no longer stable and the liquid will foam or be in a turbulent flow regime and the pump will lose its ability to compress gas and remove the compression heat. If not corrected, overheating could take place and the pump will have to be shut down.
Liquid management
The importance of liquids in gas compression is therefore clear, and it is critical to keep the required liquid fraction within the pump at all times. When a reliable and constant liquid phase is not present a system to trap and collect the liquids has to be incorporated in the design. This is often referred to as a liquid management system and has to be sized and designed correctly for the expected flow regime.
Proper liquid management will allow the pump to work over a wide range of GVF % and will also allow the pump to effectively handle liquid slugs typical for multiphase flow. The GVF % in a typical specification is an average number and a best estimate from the well test. A multiphase pump will encounter different types of flow regimes in the field, including slug flow where GVF can change from zero to 100% instantaneously.
Thus, the multiphase pump system can incorporate a collection and re-circulation system with a liquid trap downstream of the pump. A liquid trap can be anything from a simple liquid knock out boot with a cyclonic separator or a high-efficiency two-phase separator with demister pack, liquid level control, etc.
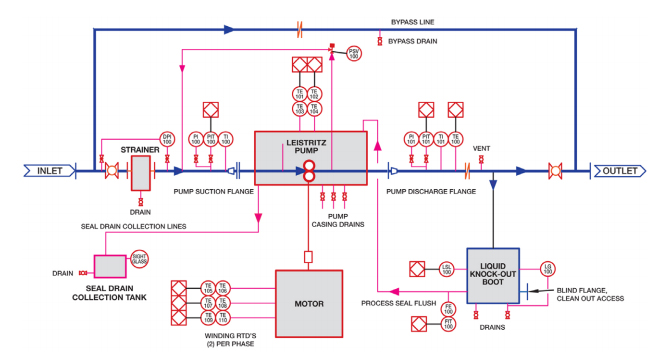
Typical P&ID with liquid recirculation system.
Summary
Looking towards the future, multiphase pumping technology is maturing and the market has seen a substantial increase in reliability and availability. Components such as mechanical seals and bearings, have dramatically improved in reliability as pump and component manufacturers work closely together. Experience gained by operators has been put to good use and has been the source of many component and system improvements.
Diamond-faced mechanical seals, stellit and other hard faced coatings used on rotors and wear parts are good examples of such improvements. Process control with variable speed electric motors or torque converters increase the operating window of the pump and allows it to easily respond to changes in reservoir conditions. Automation and controls with trending and diagnostics are frequently used in addition to conventional instrumentation and monitoring of the pump operations. Standards such as the multiphase pump section of API 676 III Ed. are today assisting operators and EPCs to specify equipment.
The total system approach has gained acceptance as multiphase pumps become a key part of the hydrocarbon production process, resulting in complete turnkey multiphase pumping installations allowing pump operation at even higher gas fractions and pressure boosting levels.
The technology as stood its test of time and is now getting recognition and acceptance from many operators. There is, however, still more distance to go and suppliers will have to continue the relentless pursuit of making multiphase pumping technology even more attractive to future users.
*This article was originally published in Oilfield Technology magazine, April 2017.
We have a planning to make more efficient the pumping system of our crude oil or fluid from some remotes platform to Processing Platform. Please advise us your engineering contact person or agents in Indonesia, Jakarta to be contact for further design and selection of your multi phase pump offshore.
Best Regards,
Edward Sinaga