Innovative rotary lobe pump meets the challenge of highly abrasive bonding primer and achieves three times longer service life than competing pumps
One of the products which the German building materials manufacturer Knauf produces is a polymer-based concrete primer, Betokonakt, which ensures that plaster bonds evenly onto smooth walls in construction. The composition of the product, however, creates problems during conveyance: the plaster primer has a mineral solid content of around 60%, which has a destructive effect on the rotary lobe pump feeding the filling station. After competing pumps repeatedly failed in under a month of service, Knauf turned to NETZSCH Pumpen & Systeme GmbH for a solution. NETZSCH installed its industry-leading TORNADO® T2 rotary lobe pump in the Knauf plant in April 2012, and the pump has consistently outperformed previous competing pumps.
Highly abrasive bonding primer leads to frequent pump repair
Knauf is a concrete substrate and adhesive manufacturer located in Iphofen, Germany. One of Knauf’s products is a polymer based concrete primer known as Betokontakt. It is a synthetic dispersion mixed with pure quartz sand and limestone powder, biocides, color pigments and other suspending agents. All told, the product contains approximately 50% mineral solids (30% quartz sand) with particles up to 1mm in size. The quartz sand content leads to greatly increased wear during conveyance as compared to many other products.
In this application, the concrete primer is filled from a storage tank using frequency control and a rotary lobe pump that fills various large barrels. The operating mode is intermittent, and the pump is started up and shut down for each filling process: 5 seconds of stationary time follows 20 seconds of operation. The speed of the pump is raised as the wear increases.
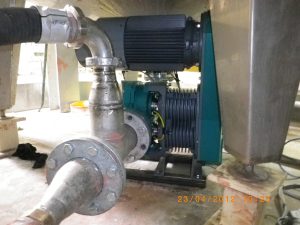
Knauf was using a competing rotary lobe pump for the feeding of the filling machine station from the mixer, with approximately 8,000 tons per year of Betokontakt fed to the filling station to fill 5kg and 20kg containers. The high annual production capacity on the mixing system resulted in a considerable maintenance effort. After approximately every 600 tons conveyed, the rotary lobes and wear plates were so badly affected that the required capacity was no longer achieved. At this point, the wear parts of the initial rotary lobe pump had to be replaced; additionally, every other repair included the replacement of the shaft seals.
“At busy times we were repairing the pump every 3 to 4 weeks,” said Knauf Maintenance Manager Armin Ryba. With an average of 12 repairs per year, Knauf incurred estimated repair costs of over $30,000 per year. The company began to search for an alternative, and consulted with NETZSCH, headquartered in Waldkraiburg in Upper Bavaria, about their TORNADO T2 rotary lobe pumps. After presentation of the benefits and advantages of the pump, Knauf installed a first test pump.
Reversal of materials and innovative drive improve wear resistance
A TORNADO T.Proc was installed in April 2012. Engineered for challenges of this kind, the entire materials concept of conventional rotary lobe pumps was reversed when the TORNADO was redesigned: two lobes made of hardened steel that rotate in a geometrically adapted elastomer insert are used instead of the standard elastomer lobes. This bi-lobe rotor design creates a considerably longer sealing line to the housing, providing more wear padding.
Additionally, a specially developed pulsation reduction system ensures that only the most minimal pulsation or shear forces are generated despite the pump’s straight, bi-lobe rotor design. Elastomer inserts are vulcanized onto the edges of the lobes to create a permanent hard-soft contact between the lobes throughout the 360° rotation cycle, thus avoiding high-wear contact between elastomer parts. The elastomer insert acts as a stator and is subject to considerably less dynamic load and deformation than in the traditional rotary lobe pump design, wherein the elastomer functions as a rotor. Ultimately, the new TORNADO design saves energy, reduces wear, and lengthens overall service life.
Finally, the drive of this new pump design was radically modified from the conventional rotary lobe pump design. The complex timing gear was replaced by a robust synchronized gear with belt drive. In doing so, not only is the danger of transmission damage greatly reduced, but the weight and installation space required are decreased. The drive requires no lubrication, eliminating the chance of oil leaks. Typical repairs or maintenance are simplified because the conveying and gear chambers can easily be opened. The cover and attachment of the components are designed for easy access and every component can be replaced with standard, commercial tools in just minutes.
Positive results at the first service
The first inspection of the TORNADO T2 pump at the Knauf plant immediately demonstrated the value of these features. This inspection took place after approximately 1,200 tons of material had been conveyed, or double the service life of the previous pump. At this time, the cover and elastomer inserts could be easily removed and the conveying elements could be easily accessed and removed in order for the maintenance team to inspect the pump.
In comparison to the conventional rotary lobe pump previously used, there was evidence of significantly less wear, even after 1,200 tons of material had been conveyed. The cover and housing inserts were in nearly the same condition as they were in when first installed; they showed only minor leaching and were still usable. The lobes showed consistent material removal with grooves in the front end; however, the lobe inserts on the edges were hardly worn.
The inspection of the belt drive also impressed the Knauf maintenance team. There was no wear to note, either on the double-toothed belt or on the belt pulley. The belt tension had only reduced slightly and not in any critical way with respect to the condition on delivery, in spite of demanding, non-continuous operation with around 60,000 load changes since commissioning. The pump’s speed had increased, but only to approximately 60% of the maximum.
Three times longer service life with half of maintenance costs
At the time of the first inspection, the new Tornado T2 pump had already delivered double the volume that the previously used, conventional rotary lobe pump was capable of, and had only reached 60% of the maximum speed.
“This pump still has a lot more potential,” said Dirk Schmalz of NETZSCH. “Based on the operating time so far, the T2 can certainly achieve at least three times the service life of the prior pump installation before requiring extensive maintenance and replacement of wear parts.”
After six months’ operation, with 3-4 times the conveyance of the previous pump, the NETZSCH pump was still performing within specifications. “The long service life means that we now only incur around half the previous costs for spare parts, repairs and downtimes,” Ryba commented, adding that Knauf was highly satisfied with the investment in the NETZSCH pump.
Comments