Author: Cal Hayes, General Manager-WaterWorks Division, Proco Products Inc.
Just over 300 miles northwest of Santa Monica, California, where the world’s first marine outfall was installed in 1910, check valves are being re-designed and engineered for outfalls all over the world. Outfalls – which are essentially discharge points of a waste stream into rivers, drains, sewers, or other bodies of water – are located in thousands of places across the planet. Many of these outfalls, sanitary sewer overflows, and combined sewer overflows (CSOs) have steel flap gate valves that are ready to be replaced. When it comes time to replace valves, owners should take the opportunity to not just replace their equipment, but to upgrade it. When we say “upgrade it”, we’re not talking about buying the most expensive check valve on the market – we’re talking about looking at the application and really evaluating the best replacement option available with today’s current engineering designs and manufacturing technologies.
When replacing check valves in outfalls, it will be important to consider the following issues:
- Does the existing installed pipe have close tolerances to the outfall base or to the cement pad that the municipality may have installed many years ago?
- Will the check valve be operating in a location where fire retardant attributes may be required?
- Does the check valve need to be algae and/or barnacle-resistant?
- How will different temperatures affect the operation of the check valve?
- Are your goals to have zero standing water and 100% emptying-capacity?
It is very easy to keep re-ordering the check valves that have been used for decades, but when you consider employing a different check valve design, you tap into the possibility of making your job much easier. For example, let’s say that the outfall invert of the pipe is close to the floor of the manhole or outfall; in this particular case, a brand new flat-bottom valve may not be very easy to install. To avoid costly and/or labor intensive changes to the existing structure, consider using a check valve that has a sloping bottom design.
Sloping bottom check valve designs also require less maintenance. For instance, in cases where waste streams are heavily laden with solids, the sloping bottom design allows for complete drainage – so your maintenance team does not have to go and clear the clogged check valves at the outfall! Instead, your maintenance team can feel confident that the check valve is doing its job, and your team can focus their time and resources on other initiatives.
Having a full port design on a sloping bottom check valve (such as the 711/731ProFlex™ from Proco Products – shown below) is incredibly important for dealing with jet velocities and headloss (the amount of energy which is lost as a result of resistance to flow). When it comes time to replace your check valve, it’s good to know your options. Take a look at the Proco Style 711/731ProFlex™ check valve or see it in person at WEFTEC in Proco’s booth 3118!
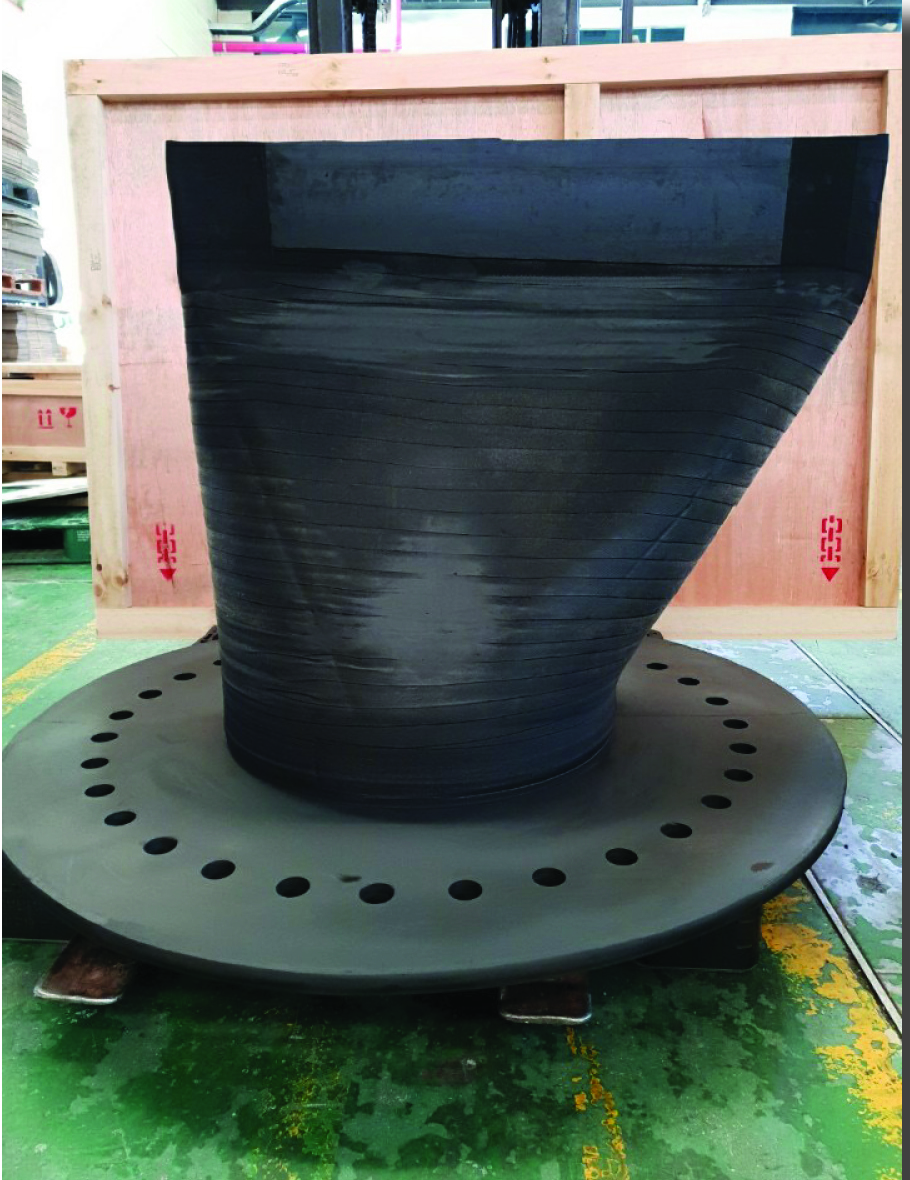
This image above portrays Proco’s ability to design a unique flange drilling to allow for installs in odd headwall drilling.
About Proco Products Inc.
Proco Products, Inc. has been supplying water and wastewater treatment plants with cost-effective, durable rubber check valves for decades. Our experience in these industries over the years has allowed us to develop sturdy, high-quality expansion joints and rubber duckbill check valves to assist in the control of back pressures while resisting corrosion and breakage from harsh conditions. Proco operates worldwide, and maintains one of the largest product inventories in North America. For more information on expansion joints and rubber duckbill check valves from Proco Products, Inc. and to check pricing and availability, contact them today.
Comments