Prior to selecting compression packing materials, understand their compatibility with the application.
As one of the oldest and most common sealing devices, compression packing is made from different packing fibers. It prevents product leakage and extend the lives of pumps, valves and other rotating equipment. Constructed of relatively soft materials, packing compresses within the stuffing box between the rotating member and the body of the pump or valve to form a seal.
By tightening the gland against the outboard ring, pressure transmits to the packing set, which expands the rings radially, creating the seal. The different packing braid designs include: multi-lok, square braid, braid over core, braid over braid, and twisted.
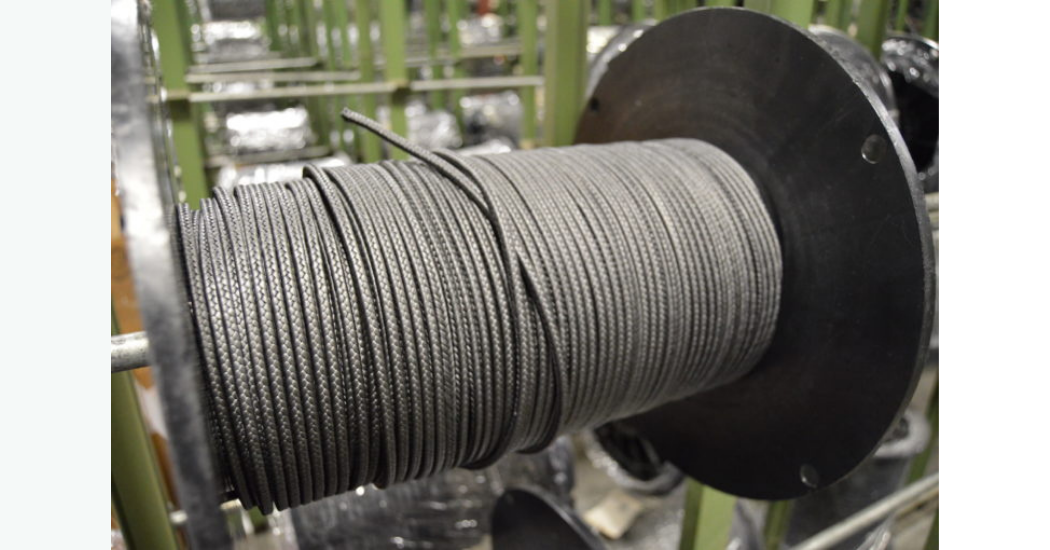
Compression packing spool
Three major criteria needed to select a packing include:
- Shaft speed (for pumps)
- Fluid temperature
- pH of the pumped fluid
Before selecting compression packing, specifiers must research the different types of fiber materials. This article details eight different types of packing fibers. Each should be chosen according to their compatibility with the application. The eight types are:
- Flax
- Acrylic
- Novoloid
- Aramid
- Filament polytetrafluoroethylene (PTFE)
- Expanded PTFE
- Carbon
- Graphite (including flexible graphite tapes)
Flax
Flax packing fibers form packing for brine, cold water, and cold oils. This economical solution serves the shipping industry in stern tubes and some power generation applications in hydroelectric turbines. Flax fiber handles shaft speeds of 1,885 feet per minute (fpm), temperatures to 220°F, and a 5 to 9 pH range.
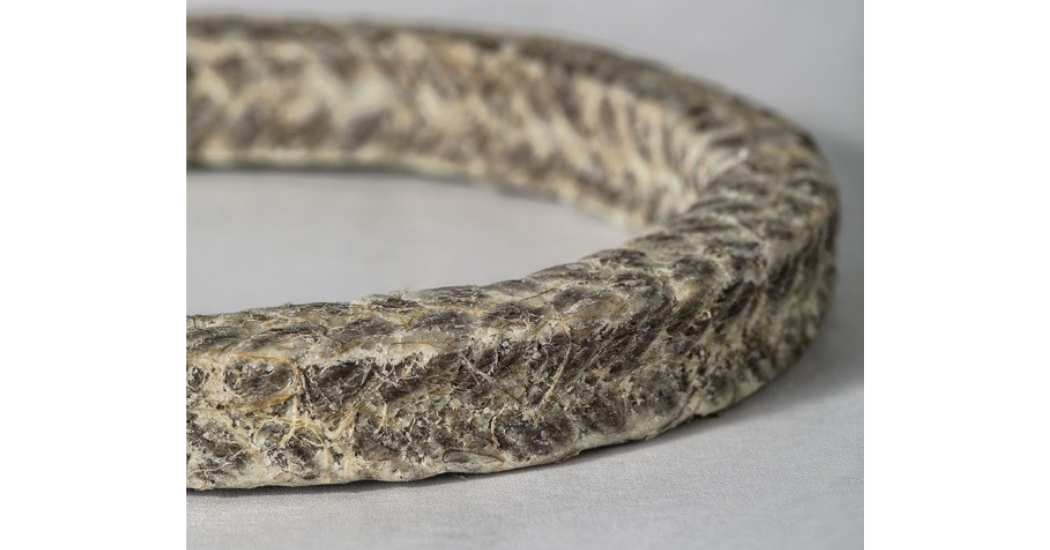
Flax packing is used in brine, cold water, and cold oil applications.
Acrylic
Acrylic fiber creates a good, general-service packing. It is commonly referred to as Teflon or graphite by many end users. This material is used for constructing packing used to seal:
- Mild acids/alkalines
- Brine
- Oil
In addition, optional PTFE coatings protect the fibers from chemical attack and ensure good break-in characteristics. Some acrylic fiber may be braided throughout with PTFE. Saturating and sealing the fibers with the PTFE particles protects them from chemical action. A surface coating of PTFE may be applied after braiding. In addition, a special high-temperature lubricant helps ensure good break-in characteristics.
Acrylic
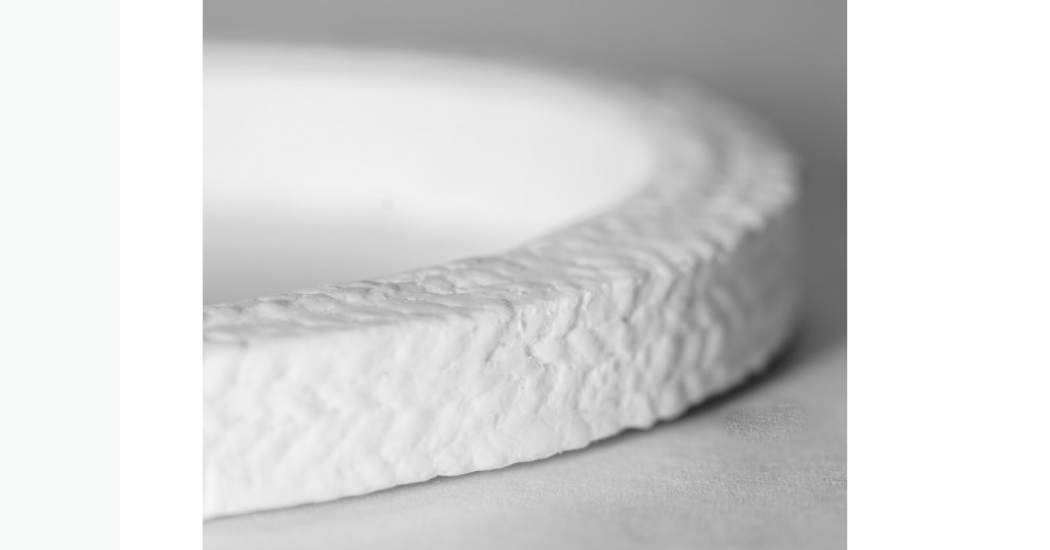
Saturating and sealing the fibers with PTFE particles protect them from chemical action.
This low-cost packing seals rotary and reciprocating pumps and agitators in the chemical and oil and gas industries. It withstands shaft speeds to 1,885 fpm, temperatures to 500°F, and a pH range of 4 to 10.
Novoloid
Novoloid packing fibers are some of the most popular. An excellent, all-around material, it has good thermal conductivity characteristics and withstands higher shaft speeds. Some novoloid packing may have a special lubrication process applied that transforms each individual fiber into a reservoir of lubrication for longer packing life.
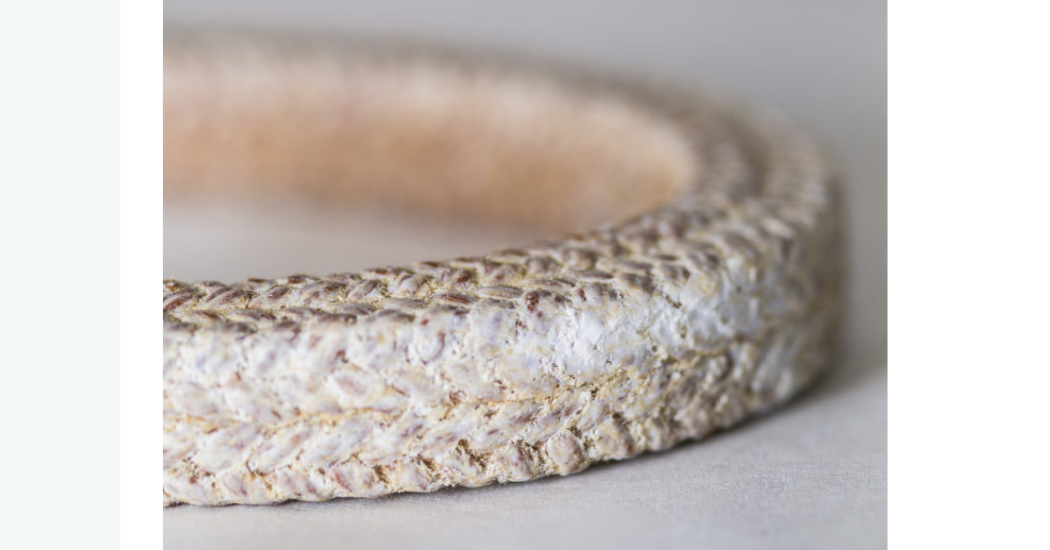
A special lubrication process is applied to some novoloid packing fibers. It transforms each individual fiber into a reservoir of lubrication for longer packing life.
Because novoloid contains no silicon, sulfur, or wax, it is an excellent alternative to graphite packing. Primarily, it seals applications in the chemical and pulp and paper industries in which graphite cannot be used. This high-performance alternative contains fluids and slurries in rotating and reciprocating pumps, washer journals, liquor pumps, refiners, and digesters.
Also, it works well for many general service applications including:
- Steam
- Water
- Acid
- Chemical and solvent applications
- Multiuse in chemical plants and pulp and paper mills
Novoloid fibers handle shaft speeds to 1,800 fpm, temperatures to 500°F, and a pH range of 1 to 13 (except in concentrated, hot sulfuric or nitric acid).
Aramid Packing Fibers
Aramid performs well in extremely abrasive environments. These fiber strands can be individually treated with a PTFE coating and a light, inert oil to improve resistance to:
- Caustics
- Mild acids
- Chemicals
- Air
- Oil
- Gases
- Solvents
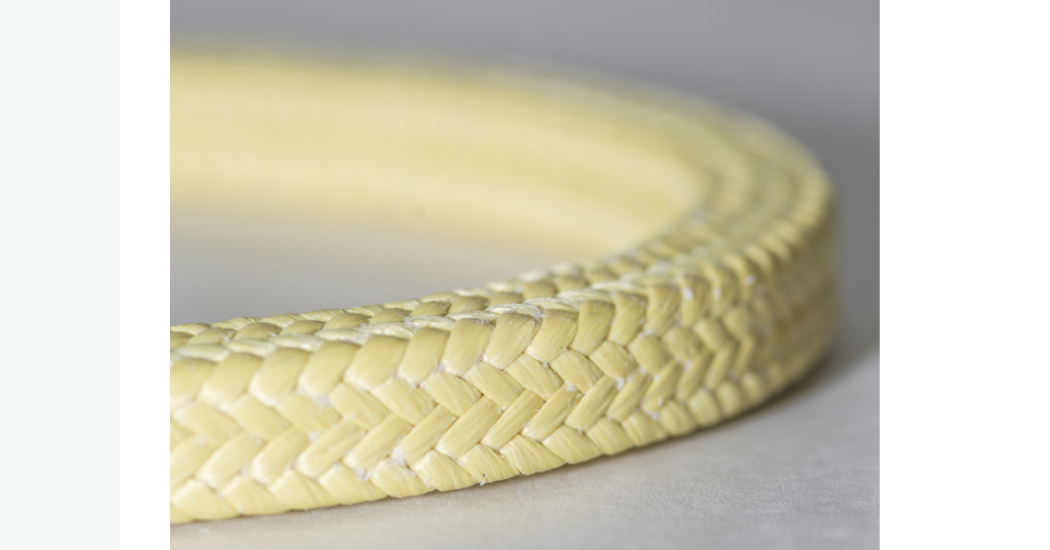
This aramid packing is low-cost and effective in rotary and reciprocating pumps and agitators.
In abrasive services, it also serves as a bull or anti-extrusion ring—a ring of packing used at one or both ends of a packing set. It tolerates shaft speeds to 1,800 fpm, temperatures to 500°F, and a pH range of 3 to 11.
Filament PTFE
PTFE fibers have a high resistance to chemicals with low levels of friction and adhesion. PTFE fibers perform excellently in corrosive services. However, they have poor thermal conductivity without graphite lubricants.
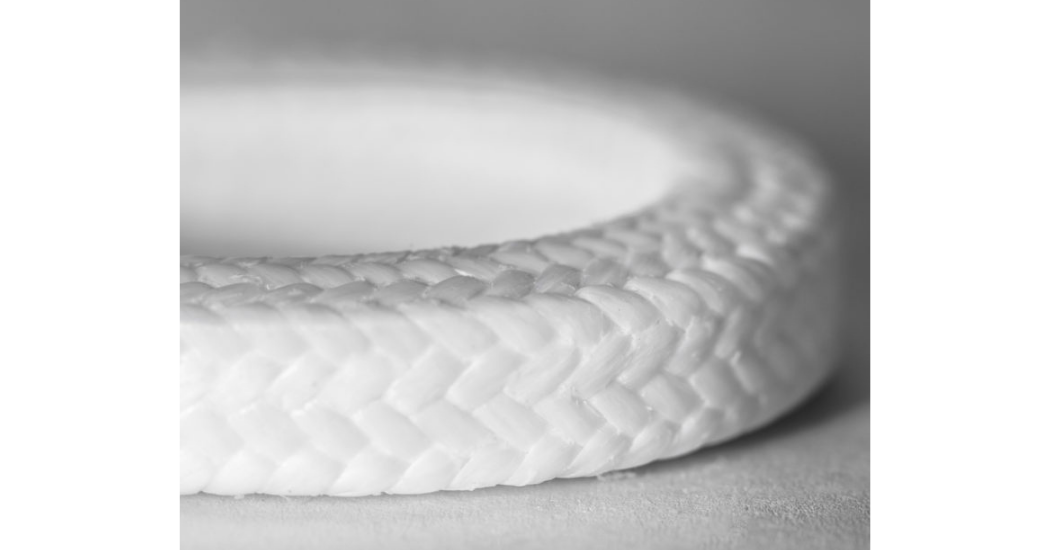
Some PTFE filament packing is pre-lubricated to provide a softer, more flexible packing with improved peripheral speed characteristics and exothermic properties.
Sometimes, PTFE filament packing is prelubricated to provide a softer, more flexible packing with improved peripheral speed characteristics and exothermic properties. It can be used for any equipment in which braided packing is commonly used.
PTFE fibers operate successfully in chemical processing, pumps, and other rotating equipment. They handle shaft speeds to 1,200 fpm (no graphite) and 4,900 fpm (with graphite). They withstand temperatures to 500°F, and a pH range of 0 to 14.
Expanded PTFE Fibers
This family of PTFE is constructed from an expanded PTFE that encapsulates graphite or a proprietary lubricant. The expansion process produces a microstructure that has a higher strength than PTFE filament fibers.
PTFE fiber seals:
- Mixers
- Pumps
- Agitators
- Reactors
- Blenders
It performs well in color-sensitive environments, such as the food and beverage industry, and may comply with FDA and USDA requirements under Title 21 Food and Drugs, 178.2570, Lubricants with Incidental Food Contact, 177.1550, Perfluorocarbon Resins.
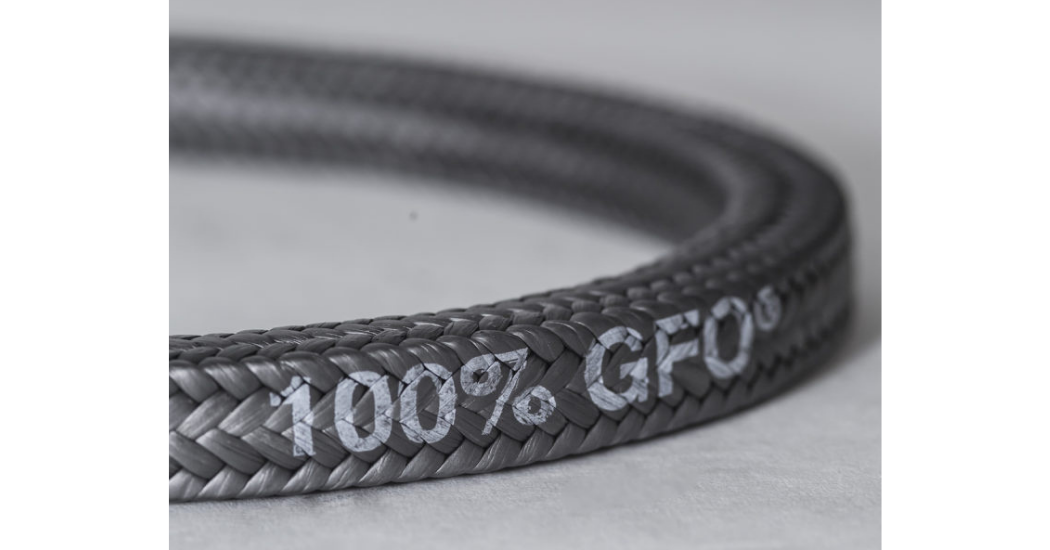
Particles of high-quality graphite are encapsulated by PTFE.
Expanded PTFE fiber, treated with special lubricants that contain no sulfur, silicone, or wax, handles shaft speed ranges from 1,200 fpm (no graphite) and unlimited (with graphite). In addition, it withstands temperatures to 550°F, and a pH range of 0 to 14.
Carbon and Graphite Packing Fibers
These proven industry performers excel because of its manufacturing method: the heat treatment process of a synthetic fiber. These fibers experience multiple heat treatments to achieve the desired carbon or graphite content.
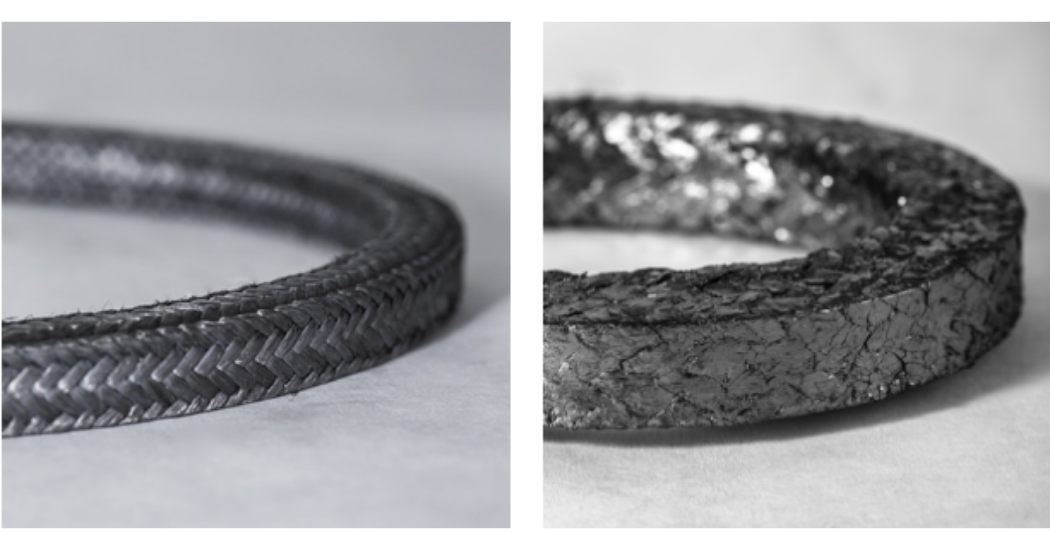
Carbon and graphite fibers are used in high-pressure, high-temperature, and high-shaft-speed applications.
Carbon and graphite packing can also be treated with PTFE to help prevent color contamination and carbon migration.
This fiber performs well in high-pressure, high-temperature and high-shaft-speed applications. It handles shaft speeds to 4,000 fpm, temperatures to 650°F, and a pH range of 0 to 14.
Flexible Graphite Tape
Flexible graphite tape is manufactured by exfoliating, expanding and then compressing the graphite flakes into a specific density. It has excellent thermal properties. Also, when mixed with reinforcing fibers, it becomes a yarn. It is used in high-pressure, high-temperature and high-shaft-speed applications.
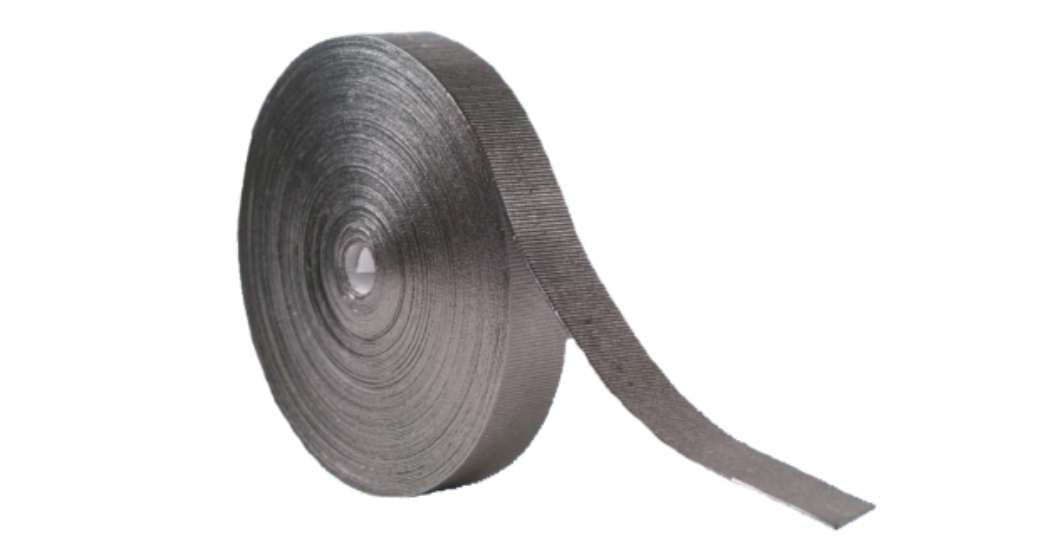
Flexible graphite has excellent thermal properties.
This tape handles shaft speeds greater than 4,000 fpm, temperatures of 850°F in oxidizing services, and a pH range of 0 to 14.
Pure Graphite Packing Fibers
For even higher temperatures, some braided packing is made of pure graphite fibers. A fine, submicron powder of inorganic graphite saturates these fibers. This packing is rated for high-temperature applications and is used in the following equipment when minimum leakage is required under severe service conditions:
- Valves (end rings only with flexible graphite center rings)
- High-speed shafts
- Agitator shafts
- Reciprocating rods
- Plunger rods
In addition, sealing technology experts recommended it for strong caustics, acids, chemical and high-pressure steam. This style works best in high-temperature and high-shaft-speed applications including those in the nuclear industry and those that require temperatures up to 850°F.
The Beginning of Success
To summarize, correctly specifying braided packing requires knowledge of the fiber’s chemical and thermal properties. Choose from a family of packing that will cover all the processes in the plant while providing peace-of-mind performance.
However, this is Step 1 toward success. Proper installation and maintenance are the other two components of successful operations. Correct technique should be followed when replacing packing as well.
Comments