Improving motor specification to boost the efficiency of submersible wastewater pumps
Electric motors in industrial applications, including those used in pumping systems, consume 30 to 40 percent of the world’s electricity. For the past two decades, equipment manufacturers, users and regulators have been tackling excessive energy consumption. This has led to the development of higher efficiency standards for motors and the adoption of variable speed drive (VSD) technologies to better match energy use and demand.
For motors designed for running in continuous duty applications (S1 operation), the International Electrotechnical Commission standard IEC-60034-30:2014 defines minimum energy efficiency specifications for four classes of motors: IE1, Standard Efficiency; IE2 High Efficiency, IE3 Premium Efficiency and IE4 Super Premium Efficiency. Each step up the IE efficiency ladder is associated with around a 20 percent reduction in motor losses, which translates directly into significant operating cost-savings.
The 2014 update also includes 8-pole motors and has widened the rated power band to include 0.12 kW up to 1’000 kW motors. US NEMA efficiency standards use an almost identical approach. In Europe, the IE3 standard has been mandatory for new industrial motors rated between 0.75 kW and 375 kW since 2017.
The European Commission estimates that the current efficiency regulations have reduced annual energy consumption by 57 TWh across the continent. The rules will be further extended in 2021 to cover both smaller and larger motors, a change that is expected to double the energy savings figure by 2030.¹
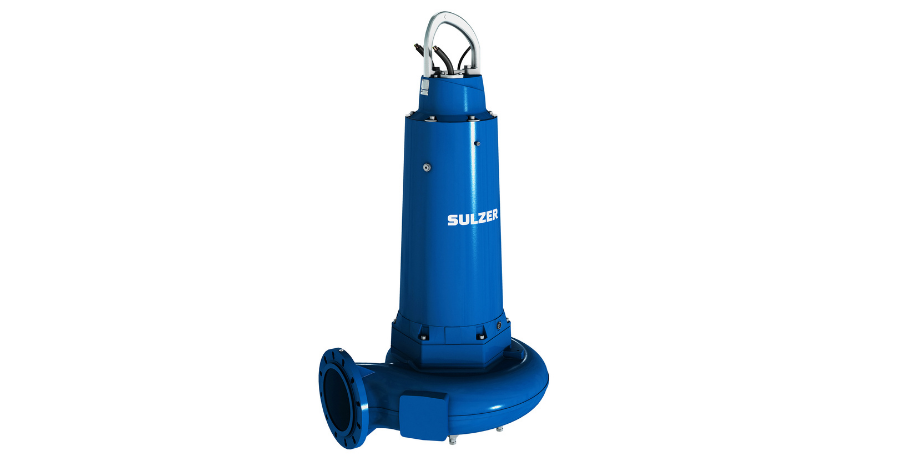
Sulzer’s complete range of submersible wastewater pumps is equipped with IE3 Premium Efficiency motors as standard
Adjusting the focus of efficiency
So far, however, submersible pumps used in water and wastewater applications have been excluded from the efficiency regulations. In the main, that’s because IEC-60034 standards require motors to be tested “bare” without seals, couplings or other system components. For machines with integrated motors and elaborate sealing systems, the calculations are a little more complicated as these losses need to be become part of the hydraulics.
Putting the regulations aside, commercial pressure to improve submersible pump efficiency has also been limited. The savings delivered by efficient motors are directly proportional to the duty-cycle of a motor. The biggest savings accrue from motors that operate continuously throughout the year. As a result, equipment owners have tended to focus their energy-efficiency investments on continuous-duty applications, rather than wastewater pumps which typically run for around 850-2000 hours, or approximately 10-25 percent of the time.
Sulzer believes that the case for premium motor efficiency in submersible wastewater pumps is stronger than either the regulators, or some users, currently recognize. That’s why the company offers IE3 Premium Efficiency motor designs as the first choice in its complete range of submersible wastewater pumps.
Reducing operation and maintenance costs
Looking at the overall life cycle costs (LCC) for a pump over a 15-year period, energy costs represent the largest proportion at around 65%, with operation and maintenance accounting for 15%. The initial cost of the pump itself is only around 10% of the total, highlighting the importance of energy efficiency when it comes to long-term expenditure. The remaining 10% includes installation and decommissioning costs as well as downtime and environmental expenses.
In the case of wastewater pumps, there is an additional factor that needs to be considered. The pump needs to be designed to minimize the number of blockages that are experienced. A study by Water UK found that wipes made up around 93% of the material causing sewer blockages.
Assuming a pump becomes blocked every second month, operational costs to clear the system and expenses for any repairs, consumables and replacement parts, including labor, will represent 15% of the LCC; this can be reduced to less than 5% if the latest design of wastewater impeller is implemented, keeping blockages to a minimum.
Pump operators should therefore focus on two important points. Firstly, selecting new pumps that offer the latest design principles and have been tested for hydraulic performance under real-world conditions. Secondly, they need to focus on overall pump efficiency, which is a combination of motor design and hydraulic efficiency.
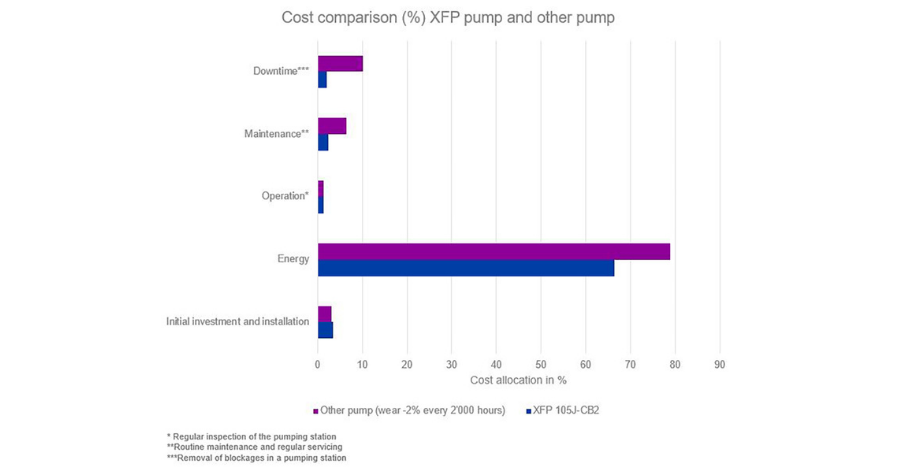
A cost comparison chart between Sulzer’s XFP pump and brand x
The impact of IE3 motors on energy costs
Selecting an IE3 motor and an impeller designed using computational fluid dynamics (CFD), can reduce LCC by EUR 12’000 compared to a low efficiency pump (assuming 15 years of operation of a typical 37 kW pump).
A second, and equally important benefit of higher efficiency, is greater reliability and a longer operating life. Energy is wasted by motors as heat, and in an enclosed submersible pump application, excess heat can dramatically shorten the life of key components such as wiring, bearings and seals. The improved efficiency of an IE3 motor equates to a lower operating temperature, which translates directly to a longer lifetime for all pump components, reducing the need for maintenance interventions.
In addition, motor wiring insulation is specified to give a minimum operating lifetime of 20’000 hours at a given temperature. As a rule of thumb, the lifetime of the insulation doubles for every 10 ºC (18 ºF) drop in operating temperature. The Class H insulation used in Sulzer motors is designed for a maximum winding temperature of 180 ºC (356 ºF). With actual operating temperatures of these high efficiency motors much closer to 105°C (220 ºF), the wiring has an expected lifetime of 320’000 hours. In lab conditions, some Sulzer pumps are reaching a theoretical life of a million hours before the motor windings fail.
For all these reasons, efficient motors are just one part of a holistic approach to pump performance and reliability improvement at Sulzer. Other key components of that approach include the use of advanced CFD to optimize performance and the innovative Contrablock Plus impeller design that resists clogging and allows easy wear compensation. Together, these changes can cut the lifecycle costs of an installation by more than half compared to less sophisticated designs.
About Sulzer:
Sulzer is a global leader in fluid engineering. We specialize in pumping, agitation, mixing, separation and application technologies for fluids of all types. Our customers benefit from our commitment to innovation, performance and quality and from our responsive network of 180 world-class production facilities and service centers across the globe. Sulzer has been headquartered in Winterthur, Switzerland, since 1834. In 2019, our 16’500 employees delivered revenues of CHF 3.7 billion. Our shares are traded on the SIX Swiss Exchange (SIX: SUN).
Comments