Sulzer Chemtech has helped to open new doors in the reuse of ocean-bound plastic waste by providing technical support to Tide Ocean SA and the Eastern Switzerland University of Applied Sciences. Using its expertise in polymer processing, Sulzer Chemtech has developed a method to turn recycled polyethylene terephthalate (PET) into high-quality foams that match the properties of virgin plastics. This development will help #tide to accelerate its work in addressing pollution and increasing the adoption of recycled polymer-based products.
A leader in the field of ocean-bound plastic upcycling, Tide Ocean SA collects and transforms this waste into premium raw materials, the award-winning #tide ocean material®, for new sustainable products. The company is able to process a wide range of polymer waste including PET from plastic bottles, polypropylene (PP) and polyethylene (PE). These are currently turned into pellets, yarn and filament which can be used in a variety of applications such as plastic injection, textiles and 3D printing.
In the search for new processes to upcycle ocean-bound plastic waste, OST – University of Applied Sciences Eastern Switzerland approached Sulzer Chemtech. Leveraging its pilot plant facility equipped with cutting-edge foaming equipment, the company has proven that it is possible to use the recycled granules to produce expanded PET (XPET) foam boards. It also defined the key processing conditions to obtain boards that are indistinguishable from conventional XPET made from virgin plastic. This will enable #tide to offer products that can be used in packaging and construction, helping to improve the sustainability of these industries.
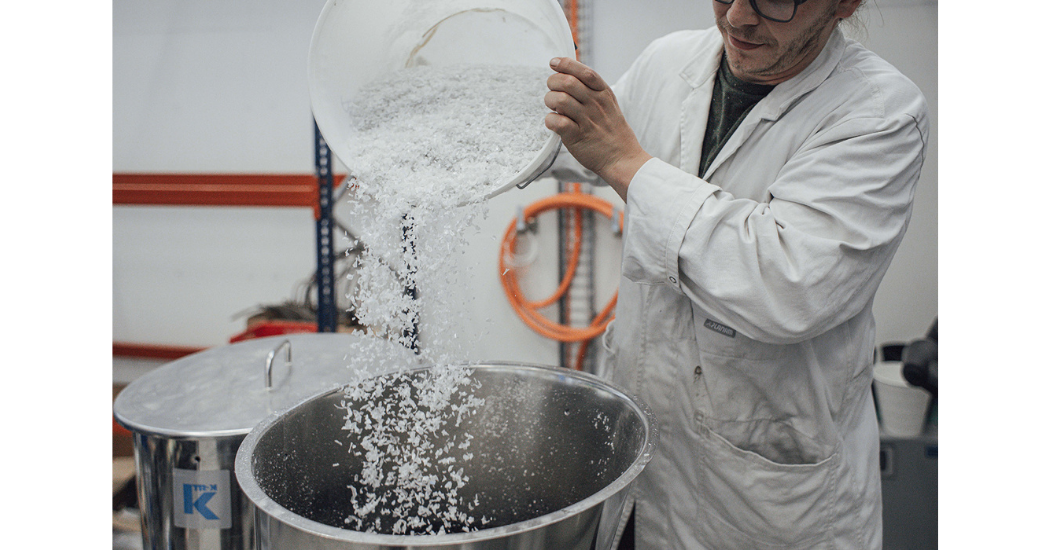
Sulzer Chemtech has helped Tide Ocean SA and the Eastern Switzerland University of Applied Sciences identify new processes to upcycle ocean- bound plastic waste.
Daniel Schwendemann, Professor at the Institute for Material Science and Plastics Processing (IWK) at OST – University of Applied Sciences Eastern Switzerland, comments: “The partnership with Sulzer Chemtech has been key in the development of XPET foam boards made from our recycled feedstock. The company’s specialists helped us determine the suitability of #tide ocean material® as well as the optimum processes to deliver high-quality products. We look forward to collaborating with them in the future.”
Marc Krebs, CCO at Tide Ocean SA, says: “We are always looking for new applications for our recycled plastic pellets. The ability to produce expanded foams opens new doors to a wide range of markets, helping us reduce plastic waste by upcycling it to obtain advanced materials. We are very thankful to Sulzer Chemtech for helping us develop this new processing method for our recycled pellets.”
Daniel Rytz, Global Head Strategy and Business Development at Sulzer Chemtech concludes: “We are delighted with the feedback received from OST and #tide. Our extensive experience in developing expanded foams from recycled plastics helps us conduct feasibility tests quickly and effectively. At the same time, we can leverage our advanced extrusion technology to develop and prove processes. We look forward to supporting more innovative projects to produce sustainable foams in the future.”
About Sulzer
Sulzer is a global leader in fluid engineering. We specialize in pumping, agitation, mixing, separation and application technologies for fluids of all types. Our customers benefit from our commitment to innovation, performance and quality and from our responsive network of 180 world-class manufacturing facilities and service centers across the globe. Sulzer has been headquartered in Winterthur, Switzerland, since 1834. In 2020, our 15’000 employees delivered revenues of CHF 3.3 billion. Our shares are traded on the SIX Swiss Exchange (SIX: SUN).
The Chemtech division is the global market leader in innovative mass transfer, static mixing and polymer solutions for petrochemicals, refining and LNG. Chemtech is also leading the way in ecological solutions such as biopolymers as well as textile and plastic recycling, contributing to a circular economy. Our product offering ranges from technology licensing to process components all the way to complete separation process plants. Customer support ranges from engineering and field services to tray and packing installation, tower maintenance, welding and plant turnaround projects – ensuring minimal downtime.
Comments