Sulzer increases capacity and efficiency for Babbitt bearing manufacturing
White metal or Babbitt bearings are used in a wide variety of rotating machinery and, just like conventional roller or ball bearings, they need to be replaced when they reach the end of their service life. Replacements can be manufactured by specialists such as Sulzer’s Southampton Service Center, which has recently upgraded its facilities.
For some of the largest industrial machines, roller or ball bearings are not suitable and here white metal bearings play an important role. Without them, generators and turbines would cease to turn, stopping the production of power that is vital to industry and everyday life.
White metal bearings are designed to operate with a film of oil in between the bearing surface and the rotating shaft. The most common failure mode is caused by a lack of lubrication and this will normally be highlighted during regular inspections. Once the issue has been identified, it is important to plan for a maintenance intervention at the earliest opportunity.
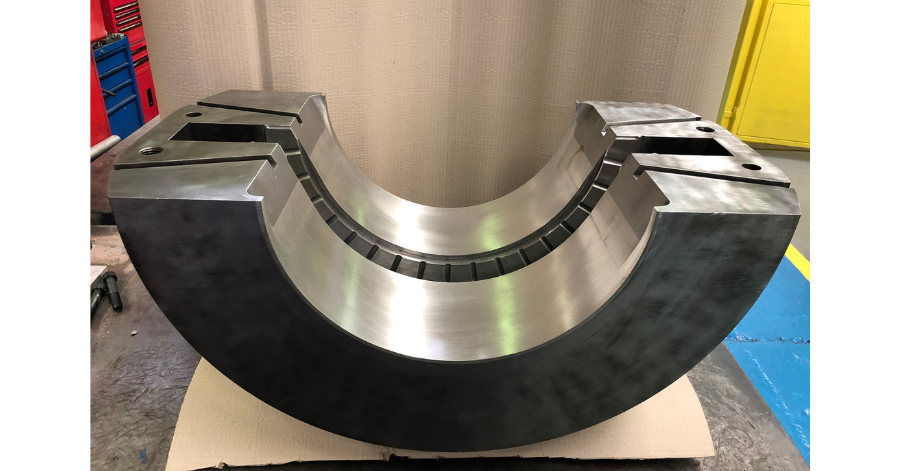
Every Babbitt bearing refurbishment is designed to match the application for improved reliability
Sulzer’s Southampton Service Center is equipped to pour and machine white metal bearings to almost any size. Sulzer has invested in its facilities to increase capacity and ensure the continued manufacturing of high quality bearings. This has included the addition of facilities to manufacture white metal spindles for specialist applications.
Simon Dawkins, General Manager Operations in Southampton for Sulzer explains: “We can adapt our processes and equipment to meet specific customer needs. For example, we created a special piece of equipment that can pour white metal spindles for a customer that needed a unique solution. Our flexibility and precision means that we can deliver comprehensive solutions, including in-situ repairs on marine vessels.”
Once a white metal bearing is delivered for refurbishment, Sulzer can remove the remaining white metal and reuse it to create the new bearings. White metal bearing composition is dictated by the application and Sulzer assesses the exact materials used in the original bearing to ensure that the new component matches it exactly.
Simon concludes: “We have the capability to turn around the majority of projects within seven days. To date, the largest bearing we have created had a 1’450 mm (57 inch) diameter and we embrace challenges in more unusual applications to help our customers keep their equipment operational.”
Sulzer specializes in repairs to rotating equipment such as gearboxes, generators, turbines compressors and pumps. As such, the Southampton Service Center has the capability and expertise to manufacture white metal bearings and this facility can be accessed through any of the service centers in Sulzer’s global network
About Sulzer
Sulzer is a global leader in fluid engineering. We specialize in pumping, agitation, mixing, separation and application technologies for fluids of all types. Our customers benefit from our commitment to innovation, performance and quality and from our responsive network of 180 world-class production facilities and service centers across the globe. Sulzer has been headquartered in Winterthur, Switzerland, since 1834. In 2019, our 16’500 employees delivered revenues of CHF 3.7 billion. Our shares are traded on the SIX Swiss Exchange (SIX: SUN).
For further information click here or e-mail: marketing.resuk@sulzer.com
Comments