Used throughout the water, petrochemical and power generation sectors to move large volumes of water, vertical suspended pumps are essential assets. By optimizing performance and efficiency in these important pumps, both operating and maintenance costs can be significantly reduced.
Jason Simcoe, Regional Sales Manager for Sulzer, looks at how various aspects of vertical pump performance can be improved.
Water is a vital resource that is used in industry for cooling processes and other non-API (American Petroleum Institute) applications. At the same time, the need to move water between two points for drainage or flood control, often sees vertical pumps being used because of the reliability of their design.
Matching performance
The vertical suspended pump can be overlooked when it comes to routine maintenance. The reliability of their design means that they rarely suffer from situations that attract attention. However, over time there is an expected gradual decline in efficiency as various components wear, which can be exacerbated if proper maintenance is not carried out.
Maintaining hydraulic alignment to the application is very important to the reliability and performance of the pump. Operating within a tolerance band either side of the best efficiency point (BEP) for the pump increases the resistance to failure. Moving away from this region can lead to increased vibration, reduced bearing life, reduced mechanical seal life, increased random failures and a reduction in overall pump life.
For example, the operator of a power station was running three vertical cooling water pumps, originally designed as duty, standby and backup. Due to a lack of routine maintenance, the performance of the pumps changed to a point where all three were required to keep up with cooling demand. Sulzer was contracted to retrofit one of the pumps and after it was reinstalled, it was able to handle normal cooling demand on its own, leaving the other two on standby.
Changing requirements
A common situation that is encountered is one where a pump has been in service for many years but during that time the application profile has changed. For example, the flow rate has been reduced, often by using a control valve downstream of the pump. This means that the pump could be operating at less than 50% of its design flow rate, which increases operating costs and affects the service life of the control valve. To compound the situation, any loss in pump performance will go unnoticed; the operator will likely open the control valve slightly to compensate.
The solution is to adjust the hydraulic profile of the pump so that it is better matched to the revised application. This allows the control valve to be used for its intended purpose, rather than as a restrictor, and the pump is able to work close to its BEP. However, making a single change, such as trimming an impeller may achieve one desired outcome but at the same time it could present other challenges, so it needs to be carefully analyzed.
When considering such changes in design, it is important to consult with a pump original equipment manufacturer (OEM) such as Sulzer, or similar expert that can apply computational fluid dynamics (CFD) analysis if necessary. This will highlight any other changes that may be necessary to ensure efficient and reliable operation. For example, reducing flow through a bypass valve may also reduce the efficiency of the pump, which is not a desired outcome; the design alteration needs to consider all aspects of pump operation for the project to be considered as a success.
Ensuring minimum flow
Another common issue that is encountered centers around the system for maintaining minimum flow rates at the pump inlet. Recycle valves are used to ensure the minimum continuous stable flow (MCSF) is achieved to protect the pump from low flow damage, but all the water that flows through these valves amounts to wasted energy. To compound this issue, these systems are often set up incorrectly and over time this relatively small issue can have significant consequences, such as cavitation damage to the impellers.
Operators may replace a recycle valve but not have the knowledge or understanding to ensure it is correctly installed and set up. From that point, the pump that is supposed to be protected, can suffer accelerated wear.
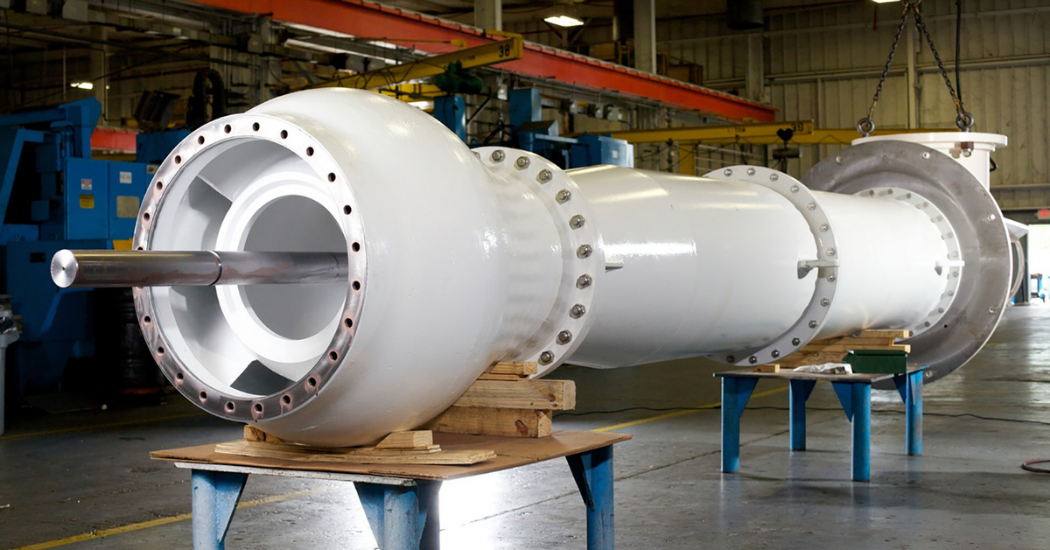
Re-engineered parts offer improvements in performance and reliability
New parts
Clearly, after many years in service, pump components will wear and eventually need to be replaced. At this point it is important to understand the difference between replicated and re-engineered parts as well as how the advances in materials, design analysis and manufacturing processes have enabled new parts to deliver increased performance and reliability.
Merely replicating an existing part can lead to reduced efficiency, early bearing and seal failures, as well as increased vibration. These issues can arise because a lack of design engineering means as-new dimensions are not achieved, the surface finish is below standard and clearances are sub-optimal.
By using the original part as a starting point and applying current engineering standards to enhance the design, it is possible to create a new part that has the best hydraulic profile for the application. Minor alterations can also enable improved bearing and seal designs to be incorporated as part of the project, extending service life and reducing maintenance costs.
Bearings
Vertical suspended pumps by their design rely on good bearing design for continued performance. As such, the options in terms of materials and lubrication systems should be fully understood to ensure the most appropriate system is installed. By matching the bearing design to the application, the service life of a pump can be extended and maintenance costs kept to a minimum.
In many cases, the wear in the bearing system determines the maintenance program for the pump, so the choices that are made at this point can have significant consequences for the future. Taking advantage of composite materials can help to protect against dry running, as well as offering improved anti galling properties and corrosion resistance.
Each application has an optimal bearing design including the lubrication technology that is employed. Some situations are better suited to bearing tube enclosures, while others perform better using product lubricated bearings. It is important to understand the benefits of each system and to work with a pump design expert that can provide advice on the most appropriate system.
Sealing systems
When dealing with bearings, it is essential that the sealing system is also considered. While packing has been the predominant design in the past, it still very much has its place in modern sealing systems. Correctly maintained, it complements the bearings providing additional support and helping to dampen vibration.
At the same time, mechanical seals also have their place, depending on the application, and innovations, such as Sulzer’s Liqui-Seal™, can offer significant benefits, especially for water cooling pumps.
Conclusions
Having completed a maintenance project, correct reinstallation of the pump is vital for continued reliability. Proper alignment of a vertical pump is one of the most important aspects of any maintenance procedure. This applies to the soleplate as well as the intermediate bearings. Assembly and installation procedures must be completed with the utmost diligence, otherwise the slightest deviation will be compounded along the length of the pump and could result in a significantly shortened service life.
Operators of these pumps should take advantage of the knowledge and expertise available from OEMs such as Sulzer, which has a worldwide network of engineering centers and field service personnel. By working together, these pumps can be updated with modern materials where necessary and optimized for their current applications.
Comments