Sulzer overhauls main pumps in water station pumping to ensure decades of reliability
Large transportation pumps are the first step in moving water between station pumping and the end user’s tap. Maintaining their reliability and efficiency is key to minimizing costs and ensuring a constant water supply. For the San Rafael Pumping Station, a major overhaul of its four main pumps, each weighing around 22 tons (20 tonnes), has delivered a cost-effective extension to the reliability of the plant.
Fresh water is one of the most important parts of daily life, one that is often taken for granted. Utilities that deliver the water to homes and businesses need to operate a preventative maintenance regime to ensure the reliability of all the equipment involved, especially the pumps.
Planning ahead
Bogotá is the capital of the Republic of Colombia and is the most populated city in the country, with almost eight million inhabitants. The Bogotá Aqueduct (EAAB-ESP.) supplies drinking water to a total population of almost 11 million inhabitants of Bogotá and 11 municipalities bordering Bogotá. The Chingaza System of the EAAB-ESP. is the main drinking water supply system in Bogotá and Colombia since it supplies drinking water to almost 80% of the population of Bogotá and several neighboring municipalities (almost seven million inhabitants).
The Francisco Wiesner Treatment Plant and the San Rafael Pumping Station are fundamental components of the EAAB-ESP. Chingaza System. The San Rafael Pumping Station is a fundamental component of the adduction of the Chingaza System. Originally installed in 1994, four pumps at the San Rafael Pumping Station had been identified for a staged maintenance program to be completed over 12 months.
As the original equipment manufacturer (OEM), Sulzer was selected for the contract to overhaul the SM 1000-1050-44 pumps. Each one delivers 14’400 m3/hr (63’400 US g/min) at 14 bar (200 psi) and is powered by a 3200 kW (4´291 HP) motor.
The preventive maintenance contract was planned in such a way that the performance of the San Rafael Pumping Station would be unaffected. Before any pumps were removed, each one was assessed using vibration and temperature monitoring equipment to establish a performance baseline. Sulzer’s field service team then organized the operation to disconnect, lift and transport each pump to the local service center.
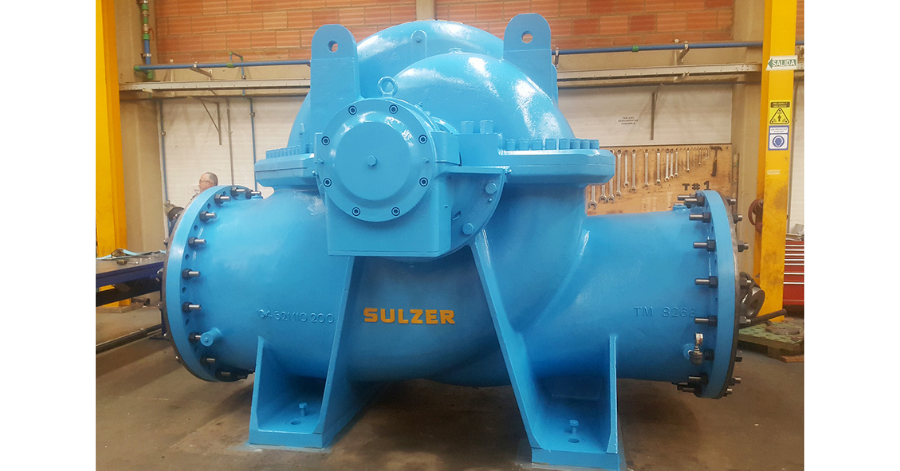
The Bogotá Aqueduct (EAAB-ESP.) supplies drinking water to a total population of almost 11 million inhabitants of Bogotá and 11 municipalities bordering Bogotá.
Complete refurbishment
Having verified the pump-motor alignment, No.4 pump was the first to be removed from its location five floors 40 m (130 ft) below ground level. Once relocated to the Bogota Service Center, it was inspected to reveal all the repairs that would be required, including machining and component replacement.
After complete dismantling of the pumps, the casing and impeller were shot-blasted before the inner surfaces were coated with a ceramic epoxy resin to improve durability and efficiency. The impeller was also coated before it was dynamically balanced and reassembled.
The exterior of the pump casing was repainted to improve corrosion resistance and prolong service life. Each pump received a complete overhaul, including the replacement of bearings, couplings and stuffing box glands. Once complete, the pump was reinstalled, laser realigned and tested by the field service team.
Additional spare parts
Having completed the repairs to No.4, the same procedure was applied in turn to pumps 2, 3 and 1. Each overhaul took approximately four weeks and by working on the pumps individually, the operational performance of the San Rafael Pumping Station was unaffected.
As well as the pump refurbishments, Sulzer also provided a selection of recommended parts to support the pumps in the future. This included a complete pump rotor with an impeller that had been coated with ceramic epoxy resin and the shaft which had an anticorrosion coating to support long-term storage. The parts were delivered with storage instructions to ensure they are still in optimum condition when they are required.
During the installation process, Sulzer provided the operators with recommendations for both temperature and vibration monitoring as well as an understanding of how this information can improve reliability. This included advice on alarm and trip settings.
Ricardo Gamboa Bernal, Chingaza System Electromechanical Maintenance Manager, comments: “The whole project has been delivered with precision and efficiency, without affecting the performance of the pumping station. As a result, the refurbished pumping station will be able to continue its vital role for at least another 20 years.”
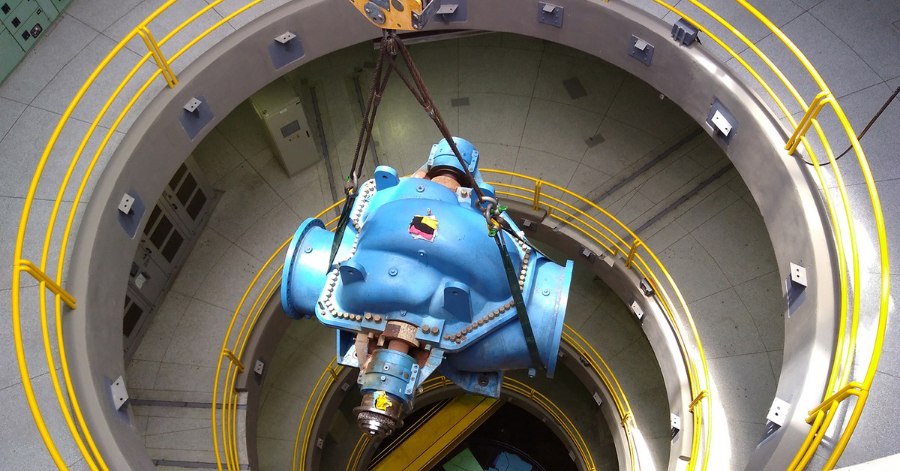
Removing No.4 pump for maintenance
Improved efficiency
While the pumps were being recommissioned, it was also discovered that they were operating well below the best efficiency point (BEP) and Sulzer provided advice on how to improve performance and reduce vibration levels.
Throughout the project, a monthly management report was supplied to the customer, who was also invited to inspect the repairs at the service center as part of Sulzer’s open workshop policy. The whole project was completed in the time frame required by the customer.
After more than 20 years in service the pumps had performed well, and the refurbishment program has enabled them to offer at least another 20 years of reliable and efficient service.
About Sulzer
Sulzer is a global leader in fluid engineering. We specialize in pumping, agitation, mixing, separation and application technologies for fluids of all types. Our customers benefit from our commitment to innovation, performance and quality and from our responsive network of 180 world-class production facilities and service centers across the globe. Sulzer has been headquartered in Winterthur, Switzerland, since 1834. In 2019, our 16’500 employees delivered revenues of CHF 3.7 billion. Our shares are traded on the SIX Swiss Exchange (SIX: SUN).
Throughout the Americas, Sulzer provides cutting-edge parts as well as maintenance and repair solutions for pumps, turbines, compressors, motors and generators. We service our own original equipment as well as third-party rotating equipment operated by our customers. Our technology-based solutions maximize reliability and lifecycle cost-effectiveness.
For more information on Sulzer, visit www.sulzer.com
Comments