Contributor: Jennifer Cardillo, Marketing and Communications Manager Americas, Rotating Equipment Services, Sulzer
New service center in Pasadena, TX, provides increased repair capacity for the Americas
Ongoing investment by Sulzer is widening the services available to customers and reducing the time to deliver repair projects. The opening of the new service center, just outside Houston, Texas, has delivered a large pump repair shop that is equipped with lift capacity to handle the largest of machines along with enhanced repair technologies and equipment to provide fast-paced, turnkey repairs. This will ensure pump repairs, upgrades and retrofits are delivered to the highest standards in accelerated timeframes.
Sulzer’s new Houston Service Center for pump services offers a wide range of services and expertise, especially in the oil and gas sector. The facility is adjacent to the company’s electromechanical services (EMS) center, enabling customers to access a wide range of services from a single location. As a pump original equipment manufacturer (OEM), Sulzer has decades of experience in the design and manufacture of pumps, including large scale, high-energy equipment, that enables the company to repair pumps of any design.
Certified welding facilities offer the ability to weld pressure vessels and carry out non-destructive testing (NDT) to ensure a high-quality repair. The engineers have experience of dealing with a wide range of materials and ensuring that the best possible solution is delivered to the customer. A complementary investment in automated welding provides highest quality welds in reduced timeframes.
Extensive machine tools, both manual and automated, are used in the manufacturing of new parts as well as modifying existing components to improve performance and efficiency. Installation of additional vertical boring mill and lathe machinery supports multiple project execution. With support from the experienced design team utilizing the latest laser scanning technology, reverse engineered parts for legacy equipment can be manufactured on site, even if the original manufacturer no longer supports the pump under repair.
Scott McPherson, Service Center Manager, explains: “We have structured our new repair facility to ensure maximum efficiency in delivering high-quality repairs with minimal downtime. Coupled with our on-site engineering, balancing and hydro-testing capabilities, we offer a comprehensive range of services that can improve reliability and performance of pumping systems.”
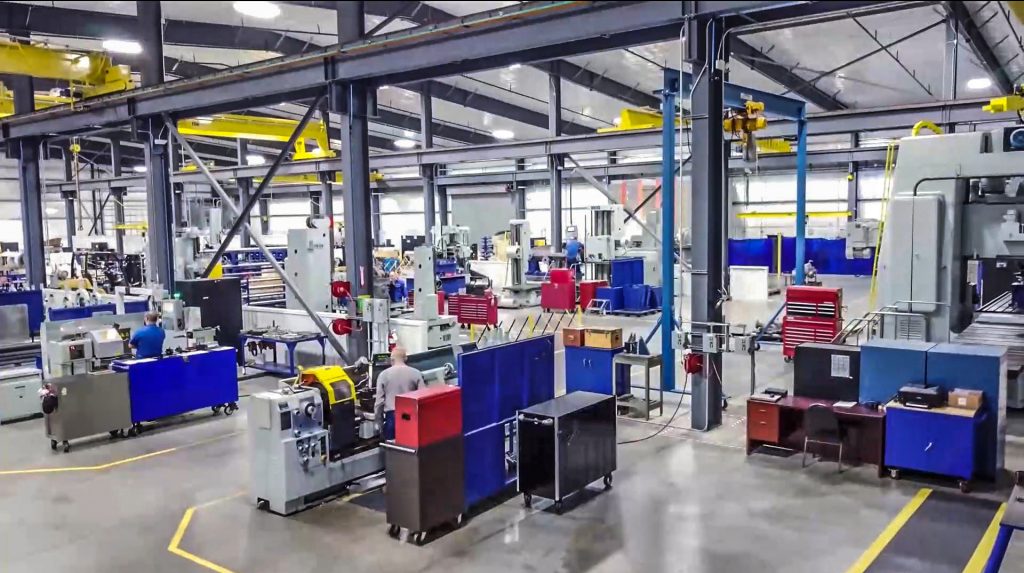
Extensive machine tools are used in the manufacturing of new parts as well as modifying existing components to improve performance and efficiency
Glenn Doerksen, President Pump Services North America, adds: “The new Houston Service Center will strengthen Sulzer’s overall capabilities in pump services and ensure that we continue to deliver cutting-edge solutions for our customers.”
All of these services are available via Sulzer’s global network of facilities. The company’s single point of contact philosophy means that a customer’s local service center is able to manage any repair project and ensures that it is delivered on time by using the extensive resources within the Sulzer network.
About Sulzer:
Sulzer is the leading worldwide, independent service provider for the repair and maintenance of rotating machines including turbomachinery, pumps and electro-mechanical equipment. With a global network of over 180 technically advanced manufacturing and test facilities, Sulzer offers a collaborative advantage that delivers high-quality, cost-effective, customized and turnkey solutions, providing its customers with the peace of mind to focus on their core operations.
Sulzer Rotating Equipment Services, a division of Sulzer, can accommodate all brands of rotating equipment including turbines, compressors, generators, motors and pumps. With an enviable track record, dedicated teams of on-site engineers provide best-in-class solutions to ensure that the most effective service is delivered.
Sulzer is dedicated to providing superior service solutions to a range of industries including power generation, oil and gas, hydrocarbon and chemical processing, water and air separation. Every solution is customized to suit the business needs of each application – whenever or wherever that may be.
With a long history of providing engineering service support, Sulzer is headquartered in Winterthur, Switzerland where it began in 1834. Today, with sales over US$ 3 billion and with approximately 15,500 employees, the Sulzer footprint spans across the globe. The core aim is to deliver a flexible and cost-effective service that optimizes customer operational efficiency and minimizes downtime.
For more information on Sulzer, visit www.sulzer.com
Comments