Contributor: Alex Edwards, Marketing & Communications Manager, Rotating Equipment Services, Sulzer
Lack of maintenance leads to rapid overhaul of generator rotor
Carrying out routine maintenance on a large turbine generator calls for expertise as well as the experience to achieve an efficient and cost-effective project. Resolving bigger issues that are uncovered during the inspection requires considerable engineering capabilities, especially if they are to be repaired quickly – a task that has become a specialty of Sulzer.
We all take electrical power for granted; knowing we have lights, heating or music at the touch of a button. It all relies on power stations meeting the demand as it fluctuates throughout the day, which depends on maintaining reliable generation equipment.
For an Irish power station, the plan was to carry out routine maintenance on a 42 MW generator, which provides 50% of the generating capacity of the site. As such, time is always a crucial factor in these projects, so careful planning is essential to minimize downtime. However, when the initial findings discovered issues beyond routine maintenance, previous experience led to Sulzer being called in to deliver a rapid repair.
The generator was originally built in 1997 and initially spent two years in the Caribbean before being installed in the Irish power station. As part of the move the machine was converted from 60 Hz to 50 Hz output frequency.
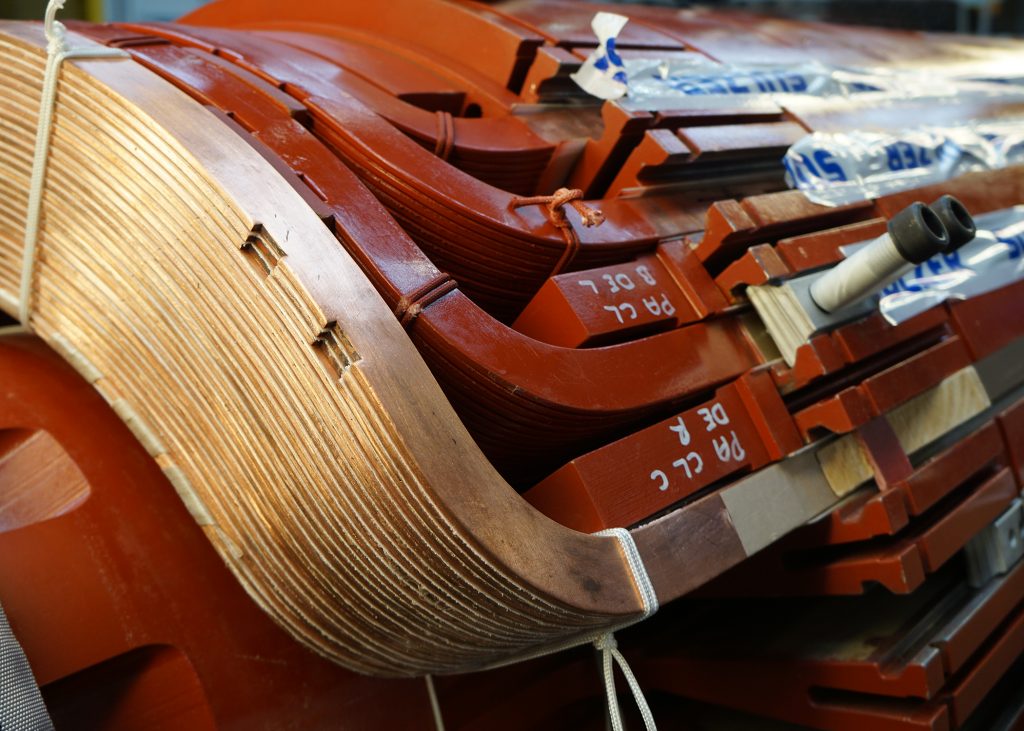
The new rotor windings were installed before being held in place by reverse-engineered aluminum wedges
Coordinated approach
The repair project was coordinated by Sulzer’s Birmingham Service Center, with assistance being provided by facilities in Daventry, Aberdeen and Southampton. The allocation of work across different service centers ensures each designated task is carried out by the service center that specializes in each required discipline. This also allows several tasks to be carried out at the same time, which is necessary to achieve the short turn-around expected by the customer.
Adrian Larmour, International Sales Manager for Sulzer, comments: “We repaired a large compressor motor from the same power station about three years ago and managed to complete the whole project in less than 28 days. The customer was very pleased with the outcome of that project and it definitely influenced the decision to use Sulzer for this generator repair.”
A team of engineers from Aberdeen built the platform, stripped the unit, installed the custom rotor removal gear then unthreaded the rotor which was sent back to the Birmingham Service Center. The stator was cleaned before a full life-assessment investigation was carried out to determine the integrity of the component. The tests carried out included offline partial discharge, tangent-delta, wedge tightness, core lamination imperfection and end-winding resonance.
Unfortunately, the recommended maintenance schedule for the generator had not been followed and this contributed to a number of more serious issues that were discovered during the routine maintenance.
Uncovering hidden issues
In the Birmingham Service Center, the initial visual condition of the generator had already highlighted some detrimental issues. The complete rotor body was covered in rust and the single-length aluminum wedge was corroded and flaking away across the entire length. As-received electrical tests were carried out before the retaining rings were removed.
A cross connection coil was found to have migrated with bare copper only millimeters away from the earthed shaft. A catastrophic failure would have occurred if there had been contact while in service. The overall insulation system on the rotor was also found to be very poor. The retaining rings were corroded and both failed ultraviolet dye penetrant testing. Ultrasonic testing on the single sleeve bearing also highlighted extensive de-bonding of white metal from its parent backing material.
The Sulzer engineers recommended that the rotor be completely refurbished. This was to include a full strip down to the main rotor forging, removing all rust, cleaning all copper coils, machining new retaining rings, machining a set of new rotor wedges, re-metaling the sleeve bearing and rewinding the unit using existing copper. The original work scope was to be turned around in 25 days, with this variation in the order, Sulzer promised that the complete refurbishment and installation would be completed in 50 days.
At the onset, the challenge was to remove the individual slot wedge which was approximately 2.5 m long. The corrosion and bonding of dis-similar metals between the wedge and rotor forging did not allow easy removal. All wedges had to be split in half using a custom-made milling head.
Once the rotor was fully stripped and cleaned, the individual parts were detailed for reverse engineering. Due to the destructive removal of the rotor wedges, the new wedges were detailed off the rotor forging wedge slot.
Aneil Hanafiah, Mechanical Design Manager explains: “The advancement in 3D laser scanning technology has significantly reduced the time it takes from detailing individual parts or assemblies, producing engineering drawings all the way to manufacturing of new components. The original cloud points (virtual model) are kept on our servers and can always be interrogated, eliminating missed dimensions or repeat measurements due to human error.”
Creating exact replica parts, fast
As with any reverse engineered part replacement, it is essential to use the same or superior material while maintaining the same tolerance, as per the original part, to ensure that the rotor performs and meets the original equipment manufacturer’s (OEM’s) design criteria. Material analysis on the wedges matched an old French standard for aluminum alloy which took some considerable time to source the required quantities and lengths. All machining works were carried out and quality controlled in-house in the Birmingham Service Center.
The re-metaling of the bearing was tasked to the Southampton Service Center, which has over 45 years’ experience in re-metaling Babbitt alloy bearings. Bearing clearances for this specific application were calculated, specified by the engineers and supplied to Southampton to include into the quality work pack.
The biggest challenge was to source the specialized high tensile, stainless-steel forgings in the correct size, which are not readily available. Only a handful of forge masters and manufactures have the experience and expertise to produce these items. A typical lead-time for procuring retaining ring forgings and machining is around six months; this could be longer when procured from the OEM.
Using Sulzer’s extensive global network of suppliers, the projects team was able to procure a couple of forgings which met the engineers’ specification from the USA, which arrived within five days. In order to minimize the time required to complete the machining, the task was split between the Birmingham and Avonmouth Service Centers.
Working round the clock, the new retaining rings were finish-machined and inspected within a 15-day period, with the time from point of ordering included. This extraordinary effort went a long way to keeping the overall project schedule below the 50-day target.
Ensuring perfect balance
The complete rotor was rewound with new insulation and the cross-over connection was redesigned to eliminate any future migration. Once completely rebuilt, the rotor was electrically tested and dynamically balanced in Sulzer’s in-house high-speed balance pit.
As this unit was of a single bearing design, a stub-shaft with a journal was designed and manufactured to complete the balancing and over-speed exercise. This substantial stub shaft was fabricated and machined at Daventry to the engineers’ drawings and specifications.
As the unit was practically a brand-new rotor, a 120% overspeed test was carried out for two minutes on this rotor and witnessed by the customer. This specification is in line with international standards for brand new turbo-generator rotors.
With the project almost complete, Sulzer engineers returned to the site to help with reassembly of the generator and to conduct the onsite load testing and recommissioning before the project was successfully concluded.
Adrian Larmour concludes: “In view of the considerable issues that were uncovered during what was a planned, routine maintenance project, the customer was fortunate to have resolved the issues found, prior to any failure occurrence. With the project completed from start to finish in just under 50 days, we have delivered a full turnkey repair solution that provides the customer with the peace of mind that their asset will continue to run reliably for the foreseeable future.
“As a direct result of the speed and quality of service provided by Sulzer, the customer later requested a very similar service for a second generator on the site.” In this way the power station made a significant improvement in the reliability of its generators and also made sure that every household can continue to rely on a steady supply of electricity.
About Sulzer
Sulzer is the leading worldwide, independent service provider for large rotating equipment. With technically advanced and innovative service and maintenance support solutions, Sulzer provides a turnkey service that provides its customers with the peace of mind to focus on their core operations.
Included in this package is a highly efficient and dependable high-voltage coil manufacturing and supply service, delivered from a purpose built facility within the Birmingham Service Centre, UK. It is recognized for producing very high quality coils for high voltage motors and generators; designed, manufactured and shipped by a highly skilled and dedicated team to ensure fast and reliable service.
With an in-house copper rolling mill, Sulzer customers can benefit from round-the-clock manufacturing to ensure that every coil is delivered on schedule. In conjunction with constant quality control and full HV on-site testing facilities, Sulzer can deliver quality, precision and speed, any time, day or night.
Comments