At the height of the COVID pandemic, Sulzer completes a major turbine rotor overhaul in the Philippines.
A team of steam turbine overhaul specialists from Sulzer Indonesia was given special dispensation to travel to the Philippines to overhaul a 53-tonne (128’000 lb) low-pressure rotor for a 345 MW steam turbine. The work, which required a specialist high-capacity lathe and balancing machine to be imported and shipped to the site, was completed ahead of schedule despite all the challenges of operating within national and local COVID-19 restrictions.
Sulzer’s work at the privately-owned power station in the Philippines originally began a year ago, when the owner was planning a blade replacement project on one of the two turbines at the site. That contract was awarded to Sulzer Indonesia after a comprehensive technical assessment by the customer, which sent a quality control inspector to spend a week evaluating processes, capabilities, and standards at the Sulzer site.
With no local facilities able to handle such a large rotor in the Philippines, the owner asked Sulzer to do the work on-site, using transportable equipment that could be shipped from Indonesia. To meet the customer’s tight shutdown schedule, Sulzer air-freighted its transportable 100-tonne (220’000 lb) capacity lathe and balancing machine to the power station. It completed the work to replace a full row of blades, balance, and re-install the rotor in 21 days.
Following the success of that initial project, and with specialized equipment still on site, the customer asked the Sulzer team to assess the condition of a spare rotor, which it kept on standby at the power station. The team was able to confirm the owner’s suspicions that the spare rotor required significant work, including machining of the bearing journals and the replacement of multiple rows of blades.
The lead time for the manufacture of new blades was expected to be several months, so the Sulzer team removed its equipment from the site, returning in the summer to conduct initial work on the rotor.
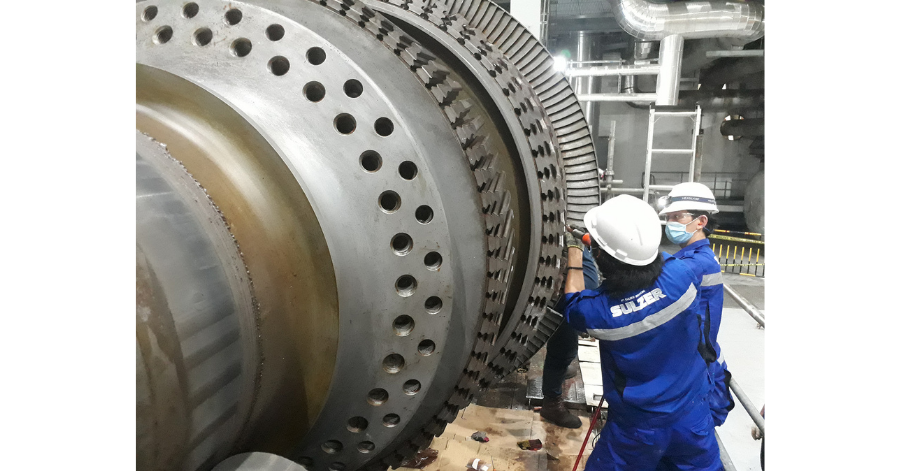
Several sets of blades were removed as part of the repair project
Access challenges
Once the replacement blades had been manufactured and shipped, the full rotor overhaul could be planned, scheduled to coincide with a two-month shutdown at the facility. The work included disassembly, an inspection of blade root connections, replacement of several rows of blades, reassembly, and balancing. Once again, the specialist equipment would be transported to the Philippines to allow the work to be completed on-site.
While both parties were confident in the approach, the feasibility of the project was thrown in doubt when the Philippines imposed a ban on cross-border travel as part of the country’s pandemic response. Gaining permission for Sulzer personnel to enter the Philippines required a special request to the authorities, which was granted subject to strict testing and quarantine protocols.
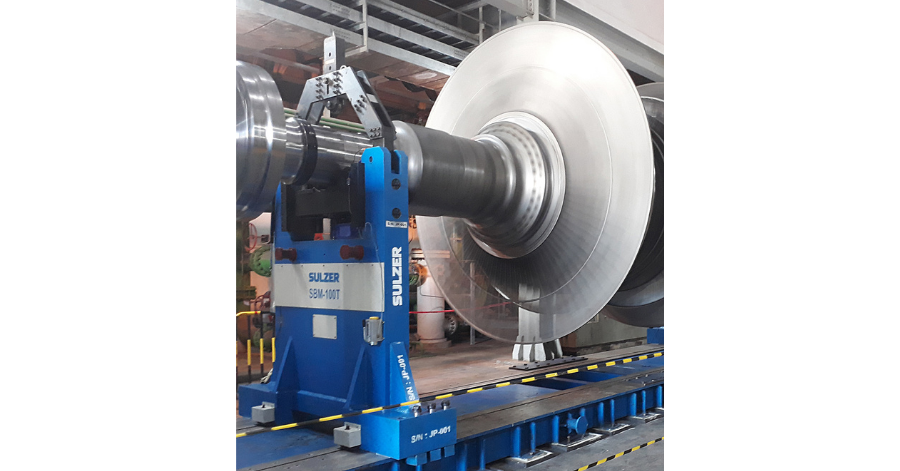
The completed rotor was balanced using Sulzer’s own equipment which had been shipped to the site for the project
With the required paperwork in place, a team of eight Sulzer personnel traveled from Indonesia to the Philippines in late 2020. All team members were subject to Covid PCR testing prior to departure and on arrival, and were asked to spend a week in quarantine before accessing the customer’s site.
The whole team returned negative tests, and so we’re able to begin work as soon as the quarantine was over to assemble the lathe and balancing equipment, which had been sent back to the power station via sea freight. Sulzer overhauled the rotor, completing all the required inspection, blade replacement, and testing work, six days ahead of schedule.
“Steam turbines are high-value capital assets, so shutdowns for maintenance and overhauls are critical events. If work overruns, the financial implications can be significant,” says Hepy Hanipa, Head of Turbo Services South East Asia at Sulzer. “At Sulzer, we are proud of our track record for meeting our customers’ schedule requirements while delivering services of the highest quality. As this project shows, we have been able to do that despite the additional complexities imposed by the pandemic.”
“For this project, we needed the correct equipment on-site at just the right time,” says the Site Maintenance Manager. “Sulzer overcame significant challenges to deliver these projects ahead of schedule.”
About Sulzer:
Sulzer is a global leader in fluid engineering. We specialize in pumping, agitation, mixing, separation, and application technologies for fluids of all types. Our customers benefit from our commitment to innovation, performance, and quality and from our responsive network of 180 world-class production facilities and service centers across the globe. Sulzer has been headquartered in Winterthur, Switzerland, since 1834. In 2020, our 15’000 employees delivered revenues of CHF 3.3 billion. Our shares are traded on the SIX Swiss Exchange (SIX: SUN). www.sulzer.com. The Pumps Equipment division specializes in pumping solutions specifically engineered for the processes of our customers. We provide pumps, agitators, compressors, grinders, and screens developed through intensive research and development in fluid dynamics and advanced materials. We are a market leader in pumping solutions for water, oil and gas, power, chemicals, and most industrial segments.
Comments