Complete power train dismantled, overhauled and relocated for biomass generator
Sourcing a replacement steam turbine at short notice can be a considerable challenge, but when there is a need for a matching generator and all the auxiliary equipment as well, the task seems almost impossible. Fortunately for a biomass power station in Michigan, USA, an almost identical site had been recently moth-balled and Sulzer was able to refurbish and relocate all the machinery.
Power stations work under a contract to deliver energy to the grid, which is dependent on a consistent supply to ensure the local population and businesses can rely on their electricity. Short, planned outages can be covered by reserve capacity, but losing a power station for an extended period can put exceptional pressure on the network.
Regular equipment checks are important to ensure reliability, especially for essential machinery such as steam turbines. Unfortunately for the site in Michigan, is a 40 MW biomass-fired power plant, several critical components and systems did not function as they should have, resulting in a catastrophic failure of the steam turbine.
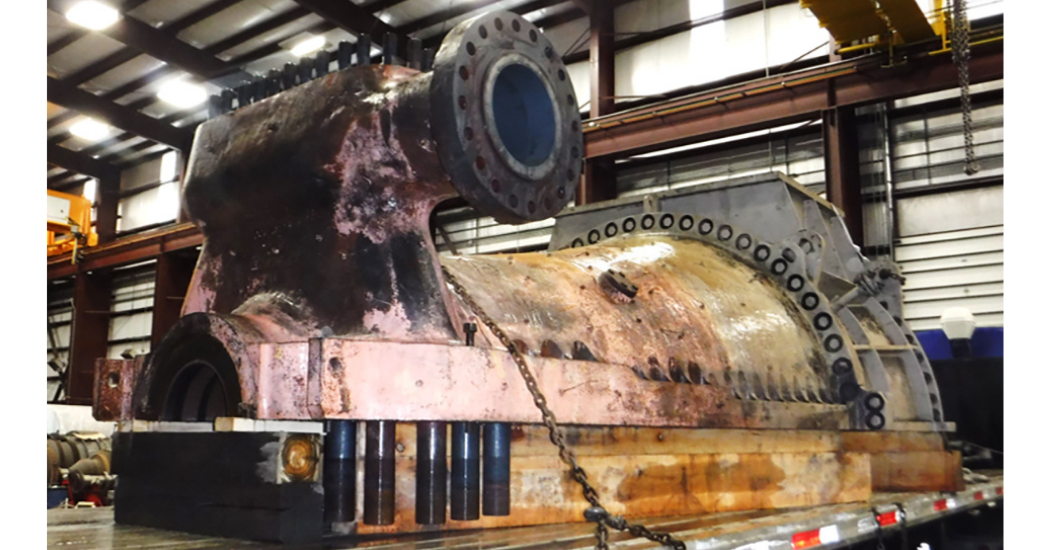
The moth-balled steam turbine casing as it was received
Assessing the situation
The damage was extensive and included the generator as well as several pieces of auxiliary equipment. Without all these assets, there was no way for the company to meet its obligations to supply the grid. The power station needed to be up and running at the earliest opportunity.
However, the time to repair the damage and commission a new steam turbine would be measured in years, so an alternative solution was needed. Fortunately, an almost identical power plant with the same turbine, generator and supporting equipment had been moth-balled six months earlier.
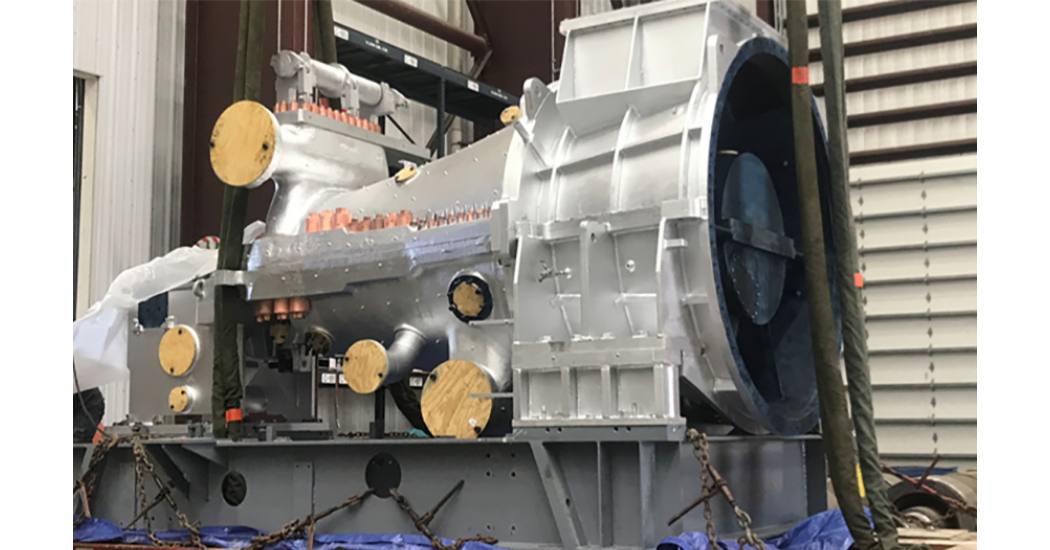
Each half of the steam turbine casing weighed 37’500 lbs (17 tonnes)
Extensive inspections
The moth-balled equipment was in Maine and installed in 1994. The last major inspection of the turbine was 10 years before the site was closed, so any inspection would have to be a complete nut and bolt disassembly. This would include cleaning, non-destructive testing (NDT) and dimensional inspection as well as a full refurbishment of the generator.
Having agreed to purchase all the necessary equipment, the company needed support in moving, installing and commissioning the equipment, and for this, they turned to Sulzer. Instead of a 2-year wait for a new turbine, Sulzer aimed to complete the project in just eight months.
“Considering the turbine had run for 25 years, it was in very good condition; it had clearly been well operated and maintained”, explains Peter Alexander, Project Manager for Sulzer. “However, in this project, we would face some major time pressures since the deadline was as soon as possible.”
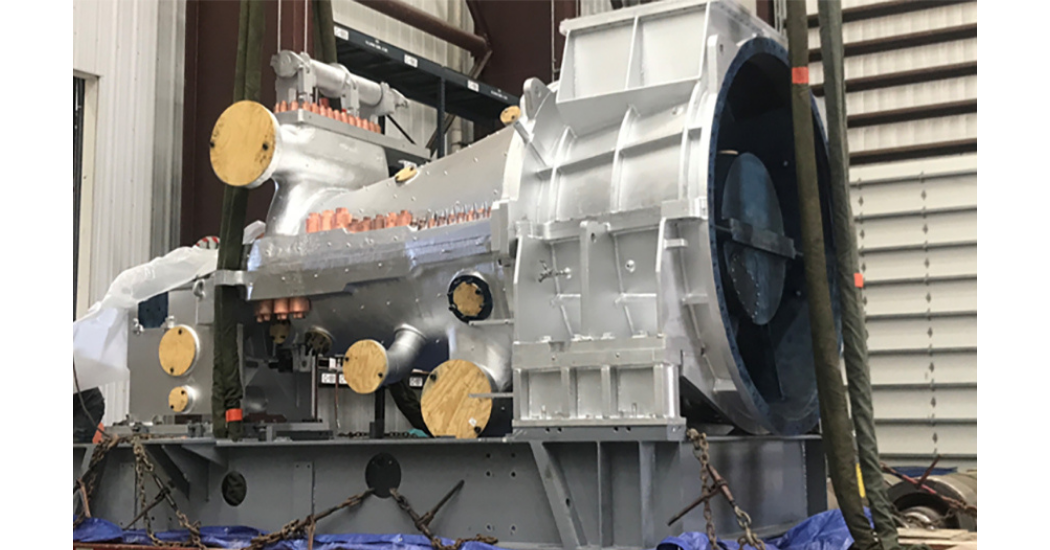
The fully refurbished steam turbine ready to be shipped
Logistics management
The multi-phase project was kicked off in January when Sulzer’s engineers went to the moth-balled site in a remote part of Maine, one of the most northerly points in the USA. Two weeks were spent on site by the field service team removing the equipment from the second story of the plant and transporting it to various locations for detailed inspections and overhaul.
The logistics were complicated by the sheer size of the equipment. The turbine rotor weighs 21’000 lbs (9.5 tonnes) and the casing weighs 75’000 lbs (34 tonnes). At the same time, the generator rotor weighs 35’000 lbs (16 tonnes), and the stator 103’000 lbs (46.7 tonnes). In all, nine truckloads of equipment, including over-sized trailers, were organized by Sulzer.
The generator went to a specialist in New York where the rotor and stator were overhauled. Meanwhile, the steam turbine and its associated components went to Sulzer’s facility in Houston, TX. Having completed all of the inspections and established the work required to return the equipment to full working order, the customer issued the instructions to proceed as quickly as possible.
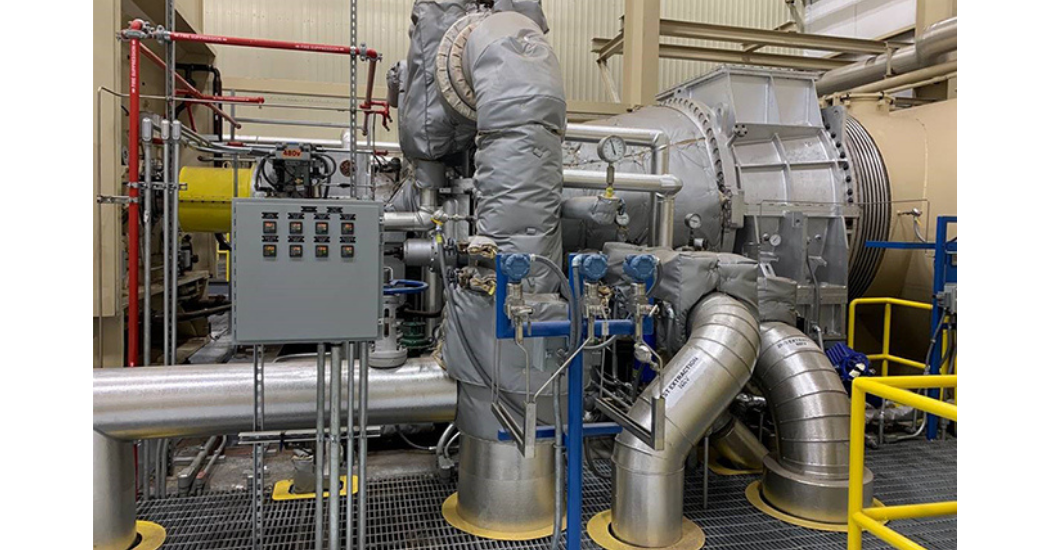
The complete turbine assembly weighed 96’000 lbs (44 tonnes)
Specialist installation
In Houston, the steam turbine had two complete rows of blades replaced, and the white metal bearings were resurfaced along with all the other refurbishments that were required. Once complete, Sulzer reassembled the turbine in Houston under a controlled environment with all the necessary tools and equipment, rather than assembling it on the power station’s site. This was more cost-effective for the customer and minimized the overall timeframe for the project.
The complete steam turbine weighed over 96’000 lbs (44 tonnes), which required special transportation arrangements and would take a week to ship to the biomass site in Michigan. In addition, the size of the components required specialist lifting equipment to be arranged ahead of time for the installation process, meaning that the project timetable had to be maintained.
Peter concludes: “The greatest challenge in this project was the schedule. The scale of the assignment and the amount of work needed to get all the equipment back to peak condition was immense. We coordinated and managed the whole process to ensure the power plant was back up and running as soon as possible.”
Chase Shepherd, Plant Manager at biomass power station, comments: “This has been a huge undertaking but together with Sulzer, we have achieved a remarkable comeback. From initial planning and removal to commissioning and startup support, thanks to their knowledge and expertise, the project has been completed quickly and cost-effectively.”
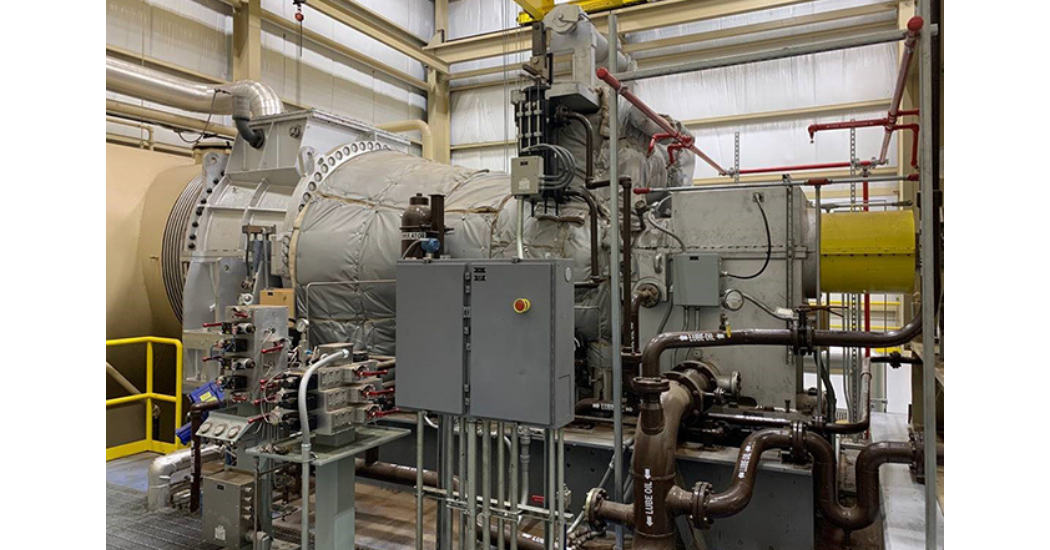
The refurbished steam turbine was installed and commissioned by Sulzer for the biomass power station
About Sulzer
Sulzer is a global leader in fluid engineering. We specialize in pumping, agitation, mixing, separation and application technologies for fluids of all types. Our customers benefit from our commitment to innovation, performance and quality and from our responsive network of 180 world-class production facilities and service centers across the globe. Sulzer has been headquartered in Winterthur, Switzerland, since 1834. In 2020, our 15’000 employees delivered revenues of CHF 3.3 billion. Our shares are traded on the SIX Swiss Exchange (SIX: SUN). www.sulzer.com. The Pumps Equipment division specializes in pumping solutions specifically engineered for the processes of our customers. We provide pumps, agitators, compressors, grinders and screens developed through intensive research and development in fluid dynamics and advanced materials. We are a market leader in pumping solutions for water, oil and gas, power, chemicals and most industrial segments.
Throughout the Americas, Sulzer provides cutting-edge parts as well as maintenance and repair solutions for pumps, turbines, compressors, motors and generators. We service our own original equipment as well as third-party rotating equipment operated by our customers. Our technology-based solutions maximize reliability and lifecycle cost effectiveness.
For more information on Sulzer, visit www.sulzer.com
Comments