Contributor: Edward Paro, Portfolio Manager, Aeration, Water Business Unit, Pumps Equipment – Sulzer Pumps Finland Oy
An innovative compressor design proves that industrial equipment can deliver high performance, low through-life costs and a smaller environmental footprint. Sulzer’s HST turbocompressor shows how a forward-thinking attitude to design, manufacturing and through-life support enables products to meet the goals of the circular economy.
As organizations seek to reduce the environmental impact of their operations, the concept of the circular economy is attracting growing interest in many sectors. At their heart, circular economy principles seek to break the link between the creation of economic value and the wasteful consumption of natural resources.
Products designed according to circular principles aim to use resources for as long as possible, extracting maximum value from them. Once a product reaches the end of its service life, as many parts and materials as possible are recovered and re-processed, leaving the smallest possible waste footprint.
One product that shows how the circular economy can operate in practice is Sulzer’s HST turbocompressor range, an innovative, high-performance machine with a 24-year track record in demanding industrial applications.
HST turbocompressors are commonly used in wastewater treatment facilities, perhaps the original example of efficient resource-reuse. In these applications, the compressors aerate treatment tanks, optimizing the performance of the biological organisms that are used to break down solid contaminants.
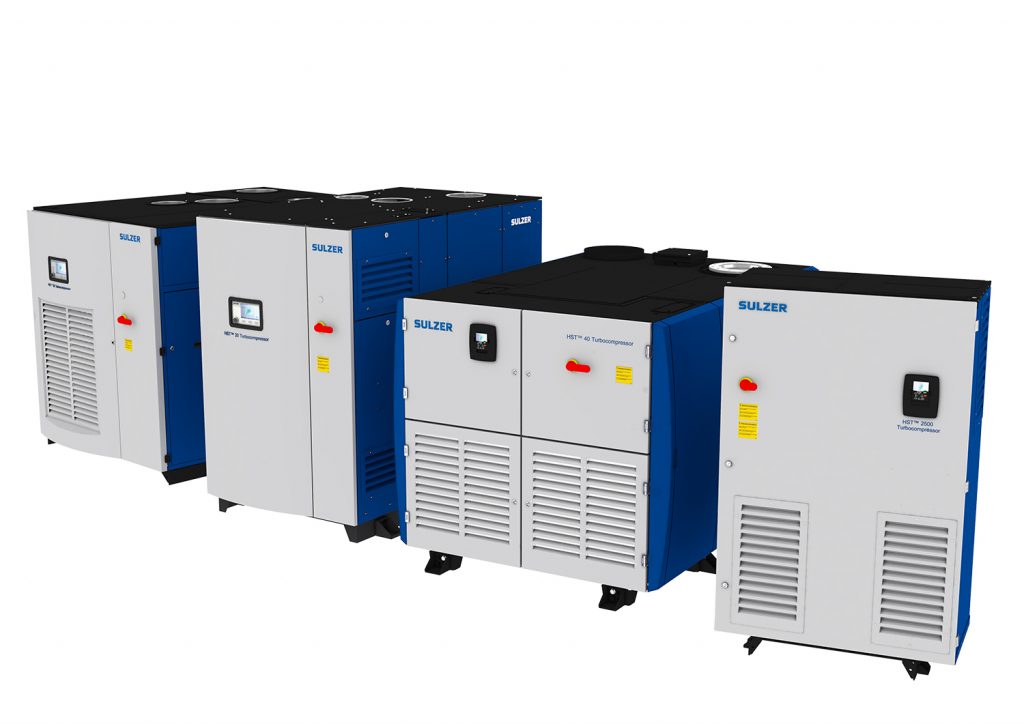
The HST™ turbocompressor product family from Sulzer is a good example of a product designed for the requirement of the circular economy.
Circular product design principles
The environmental efficiency of the HST turbocompressor goes far beyond its end application. It starts with the basic design of the machine. Conventional compressors are extremely complex items of equipment, with elaborate gearboxes and multiple seals, bearings and other parts which generate friction and, ultimately, wear out.
The HST, by contrast, uses a simple design. Its rotor is driven directly by an electric motor, with no intermediate gearing. The rotor itself spins on magnetic bearings, which means there is no metal-to-metal contact of moving parts, minimal friction and almost no mechanical wear.
Its simplicity and lack of wearing parts helps the HST compressor to achieve a very long service life. The design was first introduced in 1996, and many early units are still in continuous operation today.
High efficiency, low maintenance
Furthermore, since the design operates without oil lubrication it needs little regular maintenance and generates no waste lubricants requiring treatment and safe disposal. In fact, the only consumable products in the machine are two filters installed at the air intake and air outlet. Plenty of the original HST units still working today have never required a major overhaul.
High speed turbocompressors, as their name suggests, spin very quickly. The motor in the smallest units rotates at around 50’000 rpm. Even the largest units run at 20’000 rpm. That high operating speed means the motor is around half the size of a motor of equivalent power running a slower, conventional compressor. Furthermore, a smaller motor needs fewer raw materials and less energy to manufacture.
High speed and low friction also translate into high operating efficiency. In tests against conventional alternatives, HST turbocompressors have consistently demonstrated lower energy consumption for the same output. For owners, this means significant operating cost savings over the life of a machine as well as lower carbon emissions.
A circular supply chain
Mechanical wear isn’t the only reason components fail in hardworking machines, and one thing that can limit the life of industrial products is their control electronics. Control systems are very reliable, but the rapid pace of evolution in electronic systems means that they can become obsolete quite quickly. Finding replacement components for a ten- or twenty-year-old machine may be almost impossible.
In the case of the HST, however, the machine’s modular design helps to keep obsolescence at bay. Sulzer service engineers can quickly and easily replace control electronics with the latest generation of high-efficiency variable frequency drives (VFDs).
Older parts removed from machines are returned to Sulzer for inspection. Control systems that are still functional are refurbished and held in stock to provide a source of replacement components for the population of compressors still running with their original control systems. Parts that are beyond repair are dismantled for recycling.
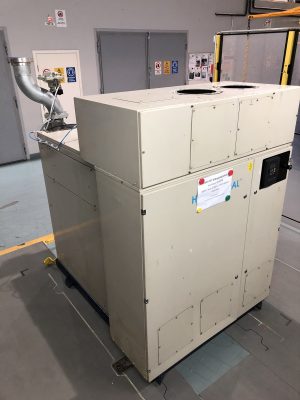
This customer machine originally manufactured in 1999 was refurbished and upgraded with new VFD after 20 years of operation.
Reused or recycled
This circular principle is also applied to complete HST turbocompressors. If a customer wants to replace an existing unit with a newer version, or one of a different output, Sulzer offers a buy-back program for the old machine. Compressors that come back from customer sites are dismantled and, after inspection and refurbishment, their components can also be used as spare parts for other older machines.
If certain parts of a recovered HST are unsuitable for reconditioning and reuse, most are easy to recycle. The main components of the machine: the volute, impeller, rotor and frame are made of aluminum, while the base and enclosure are steel. In addition, the compressor’s manner of operation means that these parts remain clean and uncontaminated in use, increasing their value as a feedstock for recycling.
The circular economy offers significant potential benefits for equipment users, manufacturers and the environment. Realizing those benefits doesn’t need to be difficult, but it does require attention to the full value chain, including equipment design, operation, in-service support and end-of-life. Over almost a quarter of a century, the Sulzer HST turbocompressor range has shown just what is possible when manufacturers and end-users take a long-term perspective on asset performance, efficiency and sustainability.
About Sulzer:
Sulzer is a global leader in fluid engineering. We specialize in pumping, agitation, mixing, separation and application technologies for fluids of all types. Our customers benefit from our commitment to innovation, performance and quality and from our responsive network of 180 world-class production facilities and service centers across the globe. Sulzer has been headquartered in Winterthur, Switzerland, since 1834. In 2019, our 16’500 employees delivered revenues of CHF 3.7 billion. Our shares are traded on the SIX Swiss Exchange (SIX: SUN).
Sulzer Launches First-in-Class COX™ Cordless Dispenser Technology
Comments