Smarter control of wastewater pump networks transforms performance, reliability, and cost-efficiency
Data flows faster than water, providing a stream of optimization opportunities. The latest in control technology allows pumping stations and wastewater treatment facilities to talk to each other, providing a better picture of real-time conditions and enabling smarter, more proactive management of the whole network.
A modern municipal wastewater system will rely upon numerous pumping stations and typically each one in the network contains its own control logic. Wastewater levels are detected by ultrasonic, radar or pressure sensors, backed-up by float switches. To prevent flooding, or damaging and wasteful dry running, the controller in the station switches the pumps on or off, based on the data from those sensors.
This distributed approach is simple and robust, but what is best for one pumping station might not be optimal for the whole network. If multiple upstream stations all switch on at the same time, for example, their combined flows could overwhelm the capacity of the next station downstream. That situation is especially likely to happen if a blockage or mechanical problem temporarily reduces downstream pumping capacity.
Making the link
Today, larger pump networks are addressing this challenge by taking a smarter, more proactive approach to control systems. Sulzer pump controller technology, for example, allows every station to connect with the treatment works using secure, two-way communications. Stations can report real-time local levels, flow rates and operating conditions with the central controller issuing commands to adjust pump control parameters as required.
This interconnected approach gives operators a much more detailed picture of the real time status of the wastewater network. They can spot increasing flows earlier, allowing them to take preemptive action to prepare the treatment site for a spike in demand. They can also reduce the severity of these spikes by instructing pumping stations to delay their activation, taking advantage of the storage capacity within the network.
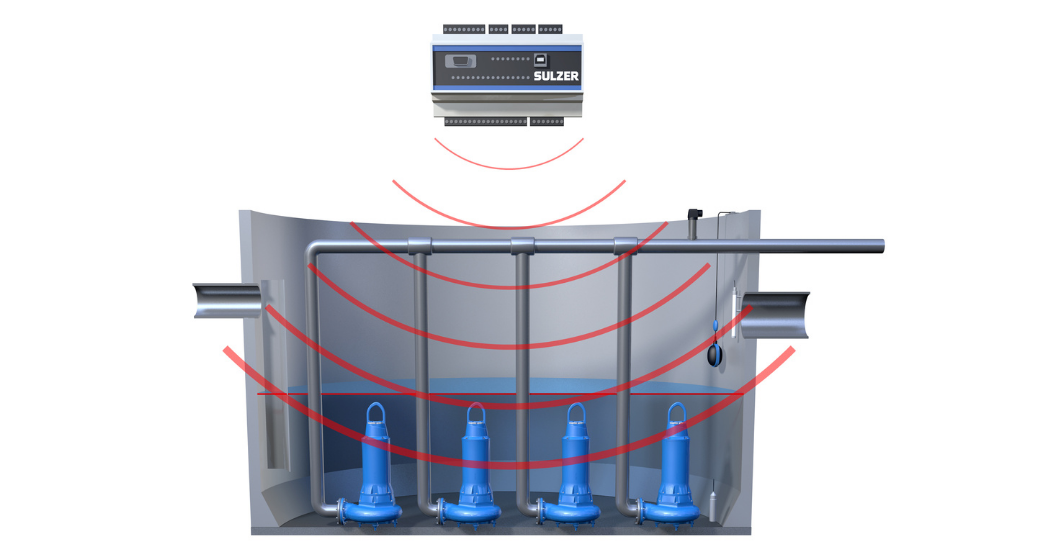
Intelligent pump control enables a network of pumping stations to work more efficiently
From reactive to proactive
Sulzer’s smart control approach even allows operators to take proactive steps to meet demand before it hits the network. Take the example of a large, but intermittently used facility such as a sports stadium. Around the time of a big match, that stadium might impose a significant additional load on the network, while for the rest of the time it produces relatively low flows.
With a smart control system in place, the pumping station closest to the stadium can detect the initial increase in flow that indicates a forthcoming spike in demand. That signal can automatically trigger a series of actions. Stations downstream of the stadium can switch to a lower “start” level, emptying the well and increasing their available storage capacity. Other stations in the network, meanwhile, can be instructed to store more wastewater temporarily, releasing it into the system when the local peak has passed.
The same approach can help operators handle other transient events, such as intense local rainfall, or regular demand peaks when many people use their showers at the beginning or end of the day. In addition, the system enables energy consumption and costs to be optimized. If storage capacity allows, for example, the activation of pumps can be delayed until times of the day when low-cost electricity is available. Alternatively, stations with multiple pumps can cut the number of units in operation to reduce flow rate and energy consumption as demand tapers off after a peak.
Same assets, more value
Best of all, smart control doesn’t require a mass of costly new hardware. Sulzer pump controllers generate their data from the standard sensors already installed in the pumping station. Outflow rates are a function of pump capacity and run time, while inflows can be calculated from the rate of level change reported by the level sensors, multiplied by the well’s cross-sectional area. If a pressure sensor is added to the outgoing mains, this reading can be used to further increase the pump capacity and forward flow calculation accuracy as well helping to determine problems such as partially clogged mains.
For these systems to operate effectively, the station’s sensors do need to provide reliable, consistent data, however. The experience of one major water utility in the UK suggests that radar sensors tend to be less dependent on optimal setup and maintenance than ultrasonic sensors, for example.
Whatever technology is used, built-in features of the Sulzer controllers can monitor sensor performance and alert operators if a sensor becomes faulty or poorly calibrated. This is achieved by comparing the level reported by the sensor to a known reference point, such as the activation of a float switch. The system can also warn of other problems in the station, such as a potential blockage, pipe breakage or pump fault. That allows operators to deploy field maintenance resources quickly and cost-effectively.
Sulzer’s smart pumping station controls can deliver truly significant savings and system performance improvements. At the UK water company mentioned earlier, for example, the introduction of this approach led to a 45% reduction in operating costs and a 75% reduction in potential environmental impact costs. The payback period for the entire new control and monitoring system was only two and half years.
Learn more about Sulzer’s control and monitoring equipment by watching this video!
About Sulzer:
Sulzer is a global leader in fluid engineering. We specialize in pumping, agitation, mixing, separation and application technologies for fluids of all types. Our customers benefit from our commitment to innovation, performance and quality and from our responsive network of 180 world-class production facilities and service centers across the globe. Sulzer has been headquartered in Winterthur, Switzerland, since 1834. In 2020, our 15’000 employees delivered revenues of CHF 3.3 billion. Our shares are traded on the SIX Swiss Exchange (SIX: SUN).www.sulzer.com. The Pumps Equipment division specializes in pumping solutions specifically engineered for the processes of our customers. We provide pumps, agitators, compressors, grinders and screens developed through intensive research and development in fluid dynamics and advanced materials. We are a market leader in pumping solutions for water, oil and gas, power, chemicals and most industrial segments.
Comments