Sulzer’s processing technologies enable effective small-scale bioplastic manufacturing
The demand for sustainable bioplastics is booming, offering unique opportunities to manufacturers entering this market. Small-scale facilities are ideal for new players in the industry as they represent low capital investments with quick returns. When a business in China wanted to develop one of the first fully integrated sugar-to-PLA (polylactic acid) plants in the country, Sulzer delivered a customized project. This allowed the manufacturer to swiftly begin producing 30’000 tonnes of recyclable, compostable and biodegradable polylactic acid (PLA) bioplastic annually.
Sustainable bioplastics can help to realize a circular economy that eliminates waste and reduces the continual use of limited resources. One of the most common and promising bio-based products is PLA, which can be obtained from sugar-rich crops, such as corn and cassava. More precisely, these are used to produce lactic acid and raw lactide, which are then purified and polymerized to obtain high-quality plastics.
By using renewable, biological feedstocks, PLA avoids depleting finite natural resources. The material is also fully recyclable, creating closed loops in which raw materials retain their value as far as possible. Furthermore, its compostability and biodegradability prevent the accumulation of waste in the environment, addressing plastic pollution issues.
Thanks to these characteristics, the demand for innovative sustainable bioplastics, such as PLA, has skyrocketed in recent years with the global market size expected to register a double-digit compound annual growth rate (CAGR) of 16% from 2020 to 2027. The expansion of this sector is also shaping manufacturing activities in China, the world’s leading producer of plastic, which is responsible for 31% of the global production of plastic materials.
Businesses interested in manufacturing PLA bioplastics and entering this growing market can benefit from a product with applications in a wide range of industries. To quickly enter this sector, while minimizing any capital risk, small-scale facilities and infrastructures are ideal. Moreover, these can be built closer to where raw materials are sourced, supporting the creation of localized manufacturing and supply centers.
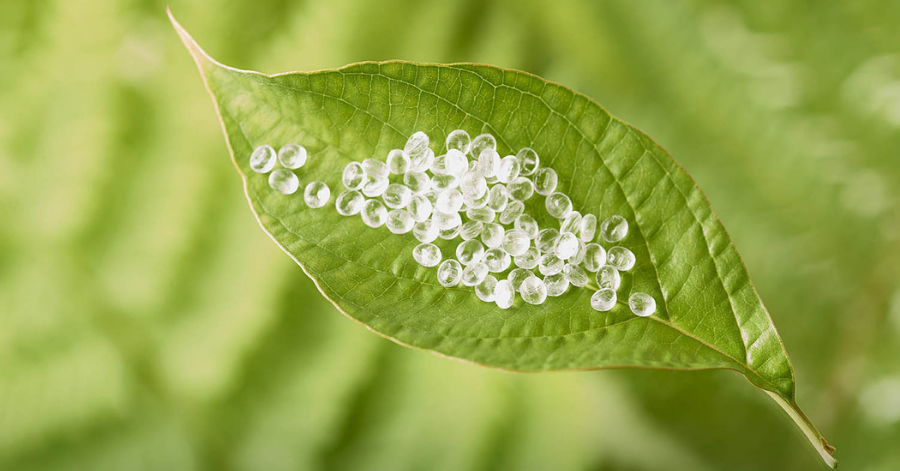
PLA can be obtained from sugar-rich crops, such as corn and cassava.
When good things come in small…plants!
These are some of the reasons why a company interested in building one of the first fully-integrated sugar-to-PLA plants in China took this approach. To quickly create an infrastructure with an annual PLA capacity of 30’000 tonnes, the company selected Sulzer as its partner. With over 25 years of experience in lactic acid and PLA-related processes, Sulzer was responsible for the design, basic engineering packages, supply, commissioning and start-up.
The customer appreciated Sulzer’s ability to provide a comprehensive solution for the purification of crude lactide, polymerization into high-quality PLA and downstream processing. In addition to the creation of a commercial small-scale plant, the producer was interested in setting up a flexible and scalable system that could provide high-quality materials at a competitive price for a wide range of downstream applications, including food packaging and textiles.
Optimizing capital investments
To address these requirements, Sulzer proposed both stick-build or skid-mounted, modular, fully-integrated design. This comprised distillation and crystallization units, static mixer reactors (SMRs) for polymerization as well as degassing (devolatilization) and pelletizing technologies. More precisely, the combination of distillation and crystallization methods allowed the manufacturer to achieve high purity levels while preserving the chemical, physical and mechanical properties of lactide as well as optimizing energy usage.
The use of Sulzer’s SMRs, created a highly homogeneous melt to obtain high-quality, consistent polymer products while cutting the volume of waste and off-spec materials. Moreover, as they do not have any moving parts, the SMRs consume less energy and require less maintenance than alternative solutions, considerably reducing operational expenses.
The system design also supported the mixing of additives in the melt for pre-compounding PLA prior to the pelletization stage. This further lowered energy utilization and reduced the risk of thermal degradation while limiting the number of processing units on the line, minimizing capital and operational expenses.
Sulzer collaborated with MAAG Group, which provided its specialist, state-of-the-art vacorex® x6 class extraction gear pump technology for the polymerization and devolatilization stages. In the degassing units, the melt pumps were used to create the necessary pressure to process the melt through the downstream equipment up to the underwater pelletizer.
In addition to fulfilling the key system requirements, MAAG Group’s technology helped Sulzer and therefore the customer to further reduce energy consumption and carbon dioxide emissions. As a result, the plant could leverage an extremely sustainable setup to produce PLA bioplastic.
The power of a leading technology partner
In less than two years, Sulzer’s specialized teams were able to complete the entire project from design to the start-up of the crude lactide to PLA and downstream line. One of the main advantages of the partnership with Sulzer reported by the Chinese company was the ability of the process technology specialist to act as a full-service provider and take care of the entire project, allowing the manufacturer to focus on other areas of its business. This streamlined the development of a highly effective fully integrated PLA plant and enabled the company to quickly enter the bioplastic market.
While the current setup allows the PLA manufacturer to produce 30’000 tonnes of bioplastic per year, the modular system that was developed by Sulzer can be easily scaled-up, supporting future expansion projects. As a result, the bioplastic manufacturer can adapt to future market demands and grow its business effectively as well as sustainably.
About Sulzer
Sulzer is a global leader in fluid engineering. We specialize in pumping, agitation, mixing, separation and application technologies for fluids of all types. Our customers benefit from our commitment to innovation, performance and quality and from our responsive network of 180 world-class manufacturing facilities and service centers across the globe. Sulzer has been headquartered in Winterthur, Switzerland, since 1834. In 2020, our 15’000 employees delivered revenues of CHF 3.3 billion. Our shares are traded on the SIX Swiss Exchange (SIX: SUN).
The Chemtech division is the global market leader in innovative mass transfer, static mixing and polymer solutions for petrochemicals, refining and LNG. Chemtech is also leading the way in ecological solutions such as biopolymers as well as textile and plastic recycling, contributing to a circular economy. Our product offering ranges from technology licensing to process components all the way to complete separation process plants. Customer support ranges from engineering and field services to tray and packing installation, tower maintenance, welding, and plant turnaround projects – ensuring minimal downtime.
Read more about PLA bioplastics!
Comments