Contributor: Sulzer
Retaining skills and expertise for the next generation
Every business needs to have a skills training program to one degree or another. For those involved in more complex industries, such as oil and gas or petrochemical engineering, gathering new skills as well as the experience of the older generation and passing it onto those committed to learning a new trade is an essential business practice.
Jennifer Gaines, Mechanical Design Engineer of Sulzer, looks at what her employer aims to achieve and how this can help other companies.
Employee training should be a continuous process; from the initial point of starting with a company, learning new skills is an essential part of personal development. As an employee gains more expertise, so the role changes as they become the mentor to the next generation and the cycle continues.
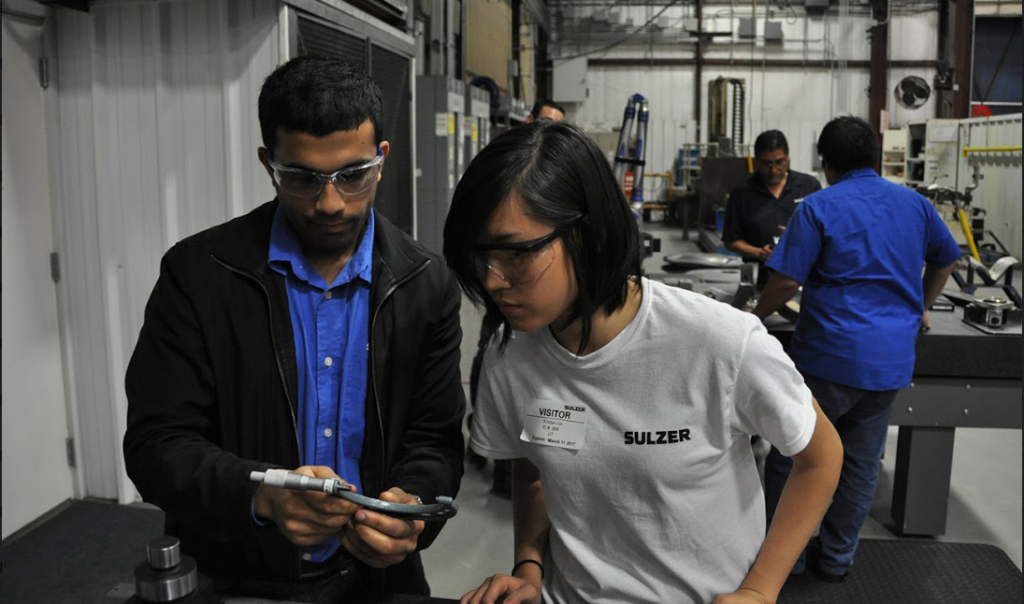
Interns have the opportunity to learn basic engineering techniques as well as increase their practical understanding of turbomachinery
Employee investment
Investing in a comprehensive training program is very important to maintaining a high standard of personnel competence that will benefit customers as well individual members of staff. Starting with the internal training, all employees should be encouraged to expand their knowledge and those that show a keen interest will make the most of the investment being made in them.
For young, potential new employees, many companies will offer an internship program, which takes undergraduates that are learning basics in theoretical engineering and places them in roles that will test and enhance their skills in project management, engineering analysis, and leadership. The selection process for prospective interns starts with careers fairs at accredited universities where students have applied for the program.
Of the hopeful candidates, a handful are selected for the initial interview and, in the case of Sulzer, a chosen few are then invited for a tour of the service center followed by interviews with shop managers and superintendents as well as engineering staff. The final selection is made based on their performance during the interviews and their score from a performance matrix.
Those aspiring engineers who are accepted into the internship program will be able to learn about the capabilities of different departments and the responsibilities of being a production engineer. During this time, through working on different projects, interns will also learn about the many and varied industrial sectors that require precision engineering solutions.
All interns should be supported throughout the departments they are working in as well as being assigned a mentor, who will guide them through the intensive learning process. As they gain an understanding of the various roles within a company, it will become more apparent which area of engineering is most appealing as a future career.
Improving professional standards
It is important that throughout their employment, new engineers are offered both internal and external training in specialized engineering topics that can help both the employee and the company improve the breadth of their expertise. Along with additional support, this will go some way to the employees completing professional licenses and qualifications specific to their chosen industry, such as oil and gas.
Of course, there is no substitute for ‘hands-on’ training and this should be applied in as many different disciplines as possible. Within a large service center there will be a large selection of specialist activities, depending on the main business of the company.
From the more basic machining principles to applying thermal barrier coatings to gas turbine blades, the potential to learn can be enormous. While some may choose to specialize in a particular area, others may wish to maintain a broader outlook and gain a more general understanding of several areas of engineering.
However, starting to work as an intern it is often the first time the candidate has been in full-time employment and as such there are many other skills that will need to be learned at the same time. Health and safety is one of the most important, but other skills such as communication, ethics and quality management should also be addressed with interns as well as other new employees.
Scaling the corporate ladder
Gaining a full appreciation of a company’s capabilities and how they are delivered to customers is an important part of working within an organization. By moving between various departments within a company an employee learns not only about the variety of services offered but also which department is most appealing from a professional point of view.
As an employee’s experience increases, their demands on the training resources will change to keep pace with their career development. Some prefer to specialize in a specific section of engineering or industrial sector, while others aspire to move into management. In either case, continuous training will remain an essential element of the profession.
Capturing expertise
An employee’s value to the company increases as they gain more experience, not only for the expertise they can deliver to customers, but the knowledge they possess can be shared with less experienced employees. Capturing knowledge and experience within an organization is essential to delivering a high quality and effective service, even when the most qualified personnel succumb to retirement.
Recording details of procedures and engineering analysis in a database ensures accurate customer records as well as retaining essential information that can be used to improve company procedures. In addition, procedures and manuals for performing various engineering tasks will also be used to train up-coming employees.
However, the most valuable projects, in terms of new information, are those that pose a unique challenge or require an innovative solution. Gathering this data and creating a forum in which it can be passed on to others working in a similar field is very important in improving the efficiency of future projects.
Encouraging achievements
Many professional qualifications, such as offshore safety and emergency training, require records of personal development through seminars, practical experience and recognized training courses. As employees add to their knowledge through various training activities, both formal and informal, maintaining an accurate record of these achievements is a vital part of career development.
Employees are encouraged to attend technical conferences and committee meetings, where new topics can be explored, to widen their overall knowledge and increase their value to the company. Those with more experience can also take on the role of an in-house trainer, passing on their knowledge to others in a similar position.
Not all training has to remove an employee from the day-to-day job, so productivity can remain unaffected. When time away is required, training is rarely wasted and is almost certainly of simultaneous benefit to both the company and the employee. Ultimately, this will all pay off with the customer seeing a more efficient and effective service.
Improving customer knowledge
While internal training is very important to retaining and expanding professional expertise, many companies can also help their customers to improve the skills of their own personnel. This training can be tailored to suit the needs of individual customers, allowing them to make cost-effective investments in their staff.
As one of the leading repairers of turbomachinery, Sulzer also offers a wide range of training courses aimed at customers who are involved in the daily operation and maintenance of turbomachinery equipment produced by any manufacturer. The aim of these courses is to enhance the competencies of the trainees, enabling them to improve productivity and reduce downtime.
Depending on the roles of the trainees, courses can look at theoretical principles along with the design and operational characteristics of turbomachinery equipment. This can lead to a better understanding of how to specify a machine correctly, which in turn will ensure the equipment is operating efficiently and reliably.
Some customers may benefit from improved knowledge in safe operation or effective maintenance procedures. Training on the most suitable predictive maintenance techniques can provide simple techniques for reducing downtime and maximizing productivity. In every case those participating in the course should be able to improve their understanding and add value to their company’s operations.
When providing training to customers, it is essential that they receive the most appropriate courses for their needs. In doing so they can expand the knowledge of their staff and create a better relationship with the training provider.
Sharing the wealth
The ability to gather knowledge is just the first step in a company’s journey. Retaining that knowledge and making sure that it doesn’t migrate with the natural wastage of employees is the next step. Having the ability to share the expertise for the benefit of both internal staff and customers is the ultimate goal.
While in principle this appears easy, the ability to learn and conserve new information and skills is rarely matched with the ability to disseminate expertise in such a way that makes it easy to take on board. Therefore, in many cases it will be necessary to give those with the knowledge the necessary tools to collate their skills and pass them on to a trainer who can formulate the most effective way to communicate it to both employees and customers, as necessary.
Ultimately, training of any individual requires a willingness on both sides. An eager employee who is given opportunities to learn will make the most of any investment. At the same time, a company that believes in supporting its staff in improving their knowledge will benefit from a more skilled workforce and a more productive working environment.
Comments