Sulzer’s specialist expertise improves reliability and efficiency
Legacy pumping installations in nuclear power facilities have been designed and manufactured using proven, trusted technology as well as materials to ensure durability and safety. After several decades in service, these pumps will have received regular maintenance but their efficiency and performance can be improved. These and other opportunities can be addressed by a specialist pump engineering facility that has dedicated its expertise to supporting these assets in the nuclear industry.
Eric Jenkins, Manager Nuclear Sales for Sulzer, looks at the specialist capabilities that are required to meet the demands of the nuclear power industry
Nuclear power plants are almost unique in that they have a pre-determined lifespan and therefore all the assets on site are managed in a way that ensures they can provide continued service until the site is decommissioned. To minimize both operating and servicing costs for equipment such as pumps, plant operators rely on a program of planned maintenance that extends the asset’s reliability and efficiency. Instead of focusing on restoring the equipment to its original state, scheduled maintenance windows can also be seen as an opportunity to improve and optimize pumps.
Dedicated pump design expertise
The original design specifications for every piece of equipment in a nuclear facility were created to ensure optimal reliability and safety, but it is still possible to apply some modern innovations in materials and manufacturing techniques. Sulzer specializes in determining the best improvements that can be achieved within the industry standards to deliver significant savings during the remaining service life of the plant.
Supplying equipment to the nuclear industry requires considerable experience and attention to detail. As a pump original equipment manufacturer (OEM), Sulzer’s expertise in pump design and manufacturing is world-renowned and within the organization one of the specialist service centers that provides support dedicated to this sector is located in Chattanooga, TN.
The variety of projects that can be undertaken by the service center to improve pump performance is extensive and best illustrated by some examples. Every project is handled by highly experienced engineers, managers and designers to ensure that each repair, upgrade or reverse engineering task is delivered fast with particular attention to industry specifications.
Raw water cooling pump energy savings
For one site suffering from excessive vibration in its six raw water cooling pumps, Sulzer specialists proposed an updated design that would resolve the issue and offer an increase in efficiency. The engineering team at the Chattanooga Service Center suggested an adjustment to the impeller and bowl to reduce the pumps’ specific speed while meeting the original specifications.
The modified design saved approximately 100 horsepower (75 kW) per pump under abnormal minimum flow conditions experienced when emergency diesel generators are started to support safe shutdown of the plant. This saving freed up an additional 600 horsepower (450 kW) from the emergency diesel generators, for no additional cost. Sulzer also included some material upgrades and improved the design of the stuffing boxes to eliminate leakage, which had been a standing long-term corrosion issue identified by the maintenance team.
The improved performance considerably reduced maintenance costs, but of greater significance for the customer was the energy saving. As a vital asset during a plant shutdown, the energy requirement for each pump affects the size and quantity of diesel generators required to support the plant during a power outage. To put the energy saving into context, a project to re-rate the generators and provide a similar amount of extra capacity, if feasible, would have cost tens of millions of dollars.
This project shows that for installations experiencing concerns about exceeding the available power from the emergency diesel generators, it is possible to review existing pump curves and adjust the specific speed of a pump without compromising the specifications laid down in the original documentation. Reducing the load on the generators has the potential to save millions of dollars that would otherwise need to be spent on re-rating this equipment.
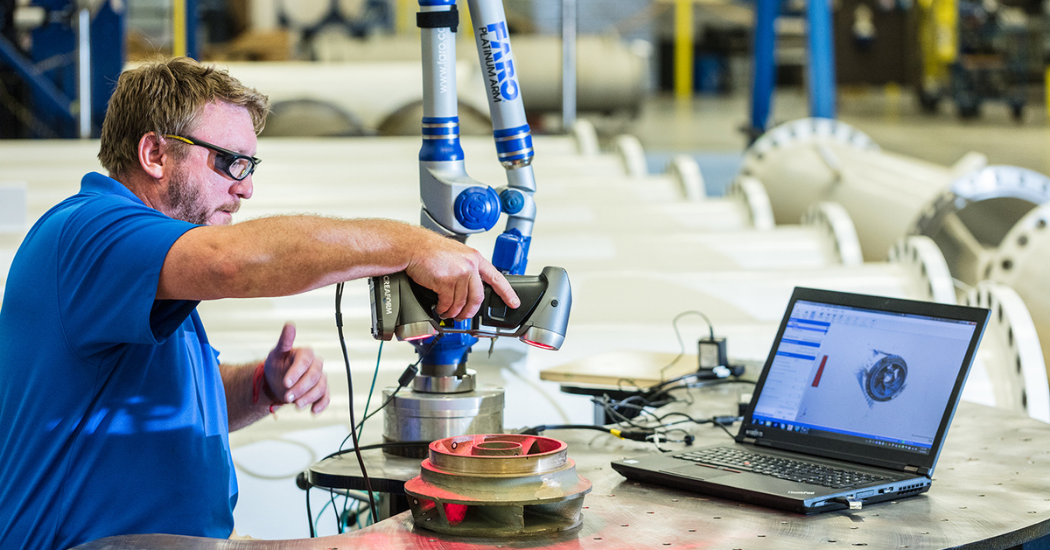
Every project is handled by highly experienced engineers, managers and designers to ensure that each repair, upgrade or reverse engineering task is delivered fast with particular attention to industry specifications.
Reducing maintenance costs in CRD systems
By being innovative, existing control rod drive (CRD) pump trains can be modified to improve the cost of operation. The existing train comprising of a motor, gearbox, pump, and pressurized lube system can in fact be modified, allowing the gearbox and pressurized lube system to be completely eliminated. This also removes the coupling between the motor and the gearbox.
Existing pump powertrains operate at high speed, which requires a gearbox and a pressurized lube system. By replacing the existing pump with one running at 3’600 rpm, both the pressurized lube system and gearbox can be eliminated. By removing these components, the overall maintenance costs are reduced accordingly.
Sulzer’s extensive knowledge and engineering expertise ensures that an upgraded design meets current industry standards. Furthermore, the skid format of the pumping system allows the complete assembly to be fully tested and certified before it is installed. Sulzer’s MSD pump, for example, can deliver the requirements of the CRD role and is a proven platform in many nuclear applications.
Validation and certification
The ability to validate and test equipment is essential for working with nuclear power plants and Sulzer has a dedicated test bed at its Chattanooga Service Center that provides the ability to confirm performance specifications across a range of assets. This minimizes lead times for maintenance projects, enabling the company to reduce customer downtime.
Sulzer can assume responsibility for the design, reverse engineering and certification of pumps and assemblies for most OEMs. State-of-the-art equipment, such as laser scanners to create 3D drawings of complex impeller geometries, enables project duration to be minimized. At the same time, the quality assurance program employed at the service center is certified and audited to meet the requirements of 10CFR50 Appendix B, part 21, and ASME N and NPT Class 1, 2 and 3.
The company’s long working relationship with the industry has seen many sites benefit from its expertise and knowledge. By working closely with operators, Sulzer can deliver considerable improvements in reliability and performance by upgrading existing assets while ensuring that industry standards are met.
About Sulzer
Sulzer is a global leader in fluid engineering. We specialize in pumping, agitation, mixing, separation and application technologies for fluids of all types. Our customers benefit from our commitment to innovation, performance and quality and from our responsive network of 180 world-class production facilities and service centers across the globe. Sulzer has been headquartered in Winterthur, Switzerland, since 1834. In 2020, our 15’000 employees delivered revenues of CHF 3.3 billion. Our shares are traded on the SIX Swiss Exchange (SIX: SUN). www.sulzer.com. The Pumps Equipment division specializes in pumping solutions specifically engineered for the processes of our customers. We provide pumps, agitators, compressors, grinders and screens developed through intensive research and development in fluid dynamics and advanced materials. We are a market leader in pumping solutions for water, oil and gas, power, chemicals and most industrial segments.
Throughout the Americas, Sulzer provides cutting-edge parts as well as maintenance and repair solutions for pumps, turbines, compressors, motors and generators. We service our own original equipment as well as third-party rotating equipment operated by our customers. Our technology-based solutions maximize reliability and lifecycle cost effectiveness.
For more information on Sulzer, visit www.sulzer.com
Comments