Contributor: Glenn Wieczorek, Managing Director
The pumping industry has faced a growing predicament over the last 25 years. As conservation efforts have lowered overall water consumption, aging pumping systems have been forced to move an increasing amount of solids with less water. The invention of modern, disposable consumer products—such as flushable wipes—has put undue strain on many of these outdated systems, resulting in lift stations that clog and require constant maintenance. To compound the problem even further, demand for cheaper construction methods has led to a new brand of “value engineering,” which often results in pumping systems that are not properly equipped to handle clogs.
A Brief History of Clogs
The cause of these clogging issues dates back almost three decades. In 1992, the U.S. government passed the Energy Policy Act to establish national water efficiency requirements for numerous waste-related plumbing products, resulting in the advent of faucet aerators, photocell-controlled sinks, waterless urinals and low-flush toilets. These advancements are beneficial to the environment, but they took an indirect toll on the pumps responsible for moving wastewater.
A solids-handling pump is rated based on its ability to pass a spherical solid through its volute; for example, a 2-in. solids-handling pump can pass a spherical object with a diameter of 2 in. Before general water use per capita changed in 1992, all pumps were regarded as solids-handling. But the inverse trends of rising solids and lessening water use rendered these pumps ineffective. The flushable wipes that were brought to market under the guise of convenience do not degrade to the same degree as traditional paper products, and increasingly frequent clogs were proof that trouble was brewing.
The pumping industry made several early attempts to combat clogs, the first of which was the grinder pump. These pumps work like garbage disposals found in many kitchen sinks, with spinning, stationary blades that are meant to completely grind solids that pass through them. Grinder pumps proved inefficient, since their flow is limited by diameter and the blades are subject to wear and tear from the constant shredding
of solids.
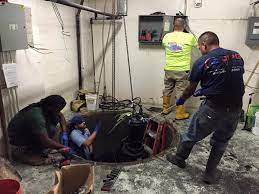
Replacing the pumps at the Intl. Brotherhood of Electrical Workers took 14 hours. Crews pumped out excess wastewater and pressure-washed the lift station to make the replacements.
Cut vs. Grind
The cutter pump is another response to the modern clogging epidemic. First introduced by Tsurumi Pump in 1979, cutter pumps do not completely grind solids that pass through them. Materials are cut just enough to allow for the continued flow of water. The resulting segments are manageably sized and are free to move down the waste stream, where municipalities can deal with them.
Cutter pumps achieve this effect by employing a serrated suction cover in combination with a tungsten carbide-tipped impeller, ensuring that fibrous foreign matter is cut up and transferring sewage without clogging.
Tsurumi originated that design specifically to battle chronic clogs. Other companies in the pumping industry, such as AMES—a Columbia, Md.-based equipment distributor that helps municipal, industrial and commercial customers deal with wastewater and plumbing issues—have taken notice. Together, Tsurumi and AMES are working to mitigate clogging problems across Delaware, Maryland, Northern Virginia, West Virginia and the District of Columbia.
Frank McQuilkin, president of AMES, is familiar with the modern clogging epidemic, and cites flushable wipes as the primary culprit.
“One wipe by itself is not a big deal,” he said. “But in large numbers, they knit themselves together in a phenomenon we call ‘ragging.’ The resulting mass doesn’t break down and becomes a very hard problem to deal with in the waste stream.”
McQuilkin went on to explain why Tsurumi products provide relief from modern pumping problems that are caused by flushing adverse solids.
“Fifteen years ago, there were no baby wipes being flushed down the toilet, and flush valves have been steadily replaced by more efficient, low-flow fixtures,” he said. “The combination of lower flow and higher content of solids is too much for many pumping systems to handle, and Tsurumi offers the most resilient pumps for dealing with these issues.”
Clogging in the Capital
AMES has had the opportunity to assist many of the region’s plumbers with handling clogging issues for their clients. One of the most notable cases involved JPG Plumbing Services, a Washington, D.C.-based plumbing company that was tasked with solving chronic clogging issues at the headquarters of the Intl. Brotherhood of Electrical Workers (IBEW) in July 2015.
John Geiling, president of JPG, said that IBEW’s old pumping system was not designed to handle the challenges of modern, flushable solids.
“The IBEW’s headquarters is a standard base building that was designed using value engineering techniques,” he said. “And frankly, the plumbing installation was not done properly as a result. Not only were the pumps constantly stopping up, but the pit was improperly sealed, and the wrong size of pipes had been used. Up until our crew redesigned the system, we’d been getting a lot of service calls from IBEW. It had progressed to the point where sewage had flooded into the building’s parking lot.”
After pump failure became too regular of an occurrence at IBEW headquarters, the association’s chief engineer requested a complete lift station overhaul. Geiling gave his customer several pump technology options from which to choose.
“I typically give my customers two or three choices when it comes to pumps,” he said. “But the chief engineer at IBEW told me outright that he wanted the best pumps and asked for my opinion on that front. For the clogging issues he was experiencing, I knew that Tsurumi’s C series of cutter pumps was the best option. That’s how we ultimately proceeded.”
Tsurumi’s C series pumps, which range in motor output from 1 to 30 hp, are suitable for handling the abrasive solids found in wastewater. They have a proprietary design, wear plates and impellers are all high chrome for durability, and each impeller has tungsten carbide tips for cutting. The pumps also maintain tolerance during operation, which eliminates the need for readjustments.
“Our crew was able to take the old pumps out and replace them with Tsurumi units in about 14 hours,” Geiling said. “We pumped out the excess wastewater, pressure washed the lift station and surrounding areas, removed the old pumps and installed Tsurumi’s cutter pumps. We have yet to get another service call from the IBEW since the installation, so I’d say it was a success.”
JPG Plumbing chose Tsurumi’s cutter pumps for the installation at the suggestion of AMES. Brandon Wood, aftermarket sales and service manager for the company, was responsible for forming a relationship with JPG’s staff and for showing them proof of Tsurumi’s ability to tackle tough clogs.
“AMES has made a name for itself by working with companies that are likely to face chronic clogging on a daily basis,” he said. “We felt that JPG was one such company, so we hosted a seminar for its contracting team that featured a live demonstration of Tsurumi’s C series pumps at work. When it came time to address the clogging problems at the IBEW building, the folks at JPG had the confidence to choose Tsurumi pumps to get the job done.”
Reality on Reality’s Terms
Clogging issues at IBEW have since ceased, but the fight to end chronic clogging has not. AMES continues to employ cutter pumps to aid in lift station design across the country. According to Wood, an ounce of prevention in preparing for proper solids handling is worth gallons of care.
“When we design pumping applications, we have to take reality on reality’s terms,” he said. “We can’t just design a system based on what we think the demand is going to be, as is the case with many value-engineered buildings. Planning for flow and head rates is a good start, but having experience in the field, we know that we have to prepare for the potential of adverse materials. We have to keep educating people about this problem, and with a manufacturer like Tsurumi on our side, we’re confident that we can make a difference.”
Comments