The plastics industry is the third largest manufacturing sector in the U.S. While packaging is by far the largest market for plastic resins, the building and construction, transportation, furniture, and electrical and electronic components markets are also heavy users. The average person in North America consumes 220 lbs. of plastic annually, primarily in packaging. North American plastic products production rose more than 6 percent in 2014 to meet the growing demand.
Manufacturing plastic resin starts with refining oil to extract hydrocarbons. Various hydrocarbons are chemically processed in large, continuous-flow polymerization plants. The polymer resins are then further processed with the addition of dyes, fire-retardant chemicals and plasticizers. The fully mixed resin material is allowed to cool and then output in the form of pellets, chips or beads. The polymer resin pellets are ultimately used to manufacture countless finished products through a variety of processes, including extrusion, injection molding, blow molding and rotational molding.
PUMP DRIVETRAINS PLAY A CRITICAL ROLE
Large-capacity, motor-driven pumps are utilized at polymer processing plants to move resin material throughout the facility. Durable couplings are required to connect the pump rotors to gearboxes. Serious problems can occur if a pump drivetrain fails anywhere along the process. A pump driveline failure would stop the continuous resin flow, allowing the liquid resin to cool and harden in place. This event would cause significant production downtime for cleanup and repair.
FRESH THINKING YIELDS A NON-TRADITIONAL SOLUTION
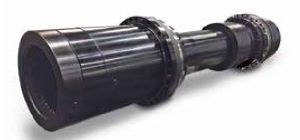
This 10’ long, 23” diameter custom Ameriflex coupling features specific split retaining rings on both the pump and gearbox end hubs, multiple convoluted diaphragm pack flex elements at each end, and a special spacer configuration for added stiffness in this dual output application. An integral indexing/timing device aligns the coupling with the mixing blades of the polymer pump
A major global petrochemical company experienced a coupling failure on a polymer pump in one of its larger resin processing facilities. The coupling problem caused expensive, time-consuming production line shutdowns.
Ameridrives was contacted to help provide a solution. Gear couplings were initially installed for this high-torque, low-speed (50 RPM) application on all the polymer pumps between the pumps and the gearboxes.
However, while plant maintenance crews did their best, keeping all the expensive gear couplings properly lubricated throughout their plants around the world proved to be a tough challenge.
After careful review of the situation, Ameridrives engineers recommended replacing the gear couplings with Ameriflex diaphragm couplings, which can run continuously and require no lubrication or maintenance (unlike gear couplings which require maintenance at 6-month intervals).
Ameriflex couplings are typically used on high- performance, high-speed applications. However, the Ameridrives team collaborated with industry-leading experts to provide custom-designed diaphragm couplings to meet the resin pump requirements.
Many custom Ameriflex couplings were designed and delivered in a variety of sizes and configurations with torque ranges up to 1,100,000 Nm (10,000,000 in.lbs.).
AMERIFLEX MULTIPLE CONVOLUTED DIAPHRAGM DESIGN SETS NEW STANDARDS FOR LIFE AND RELIABILITY
Ameriflex couplings feature an exclusive convoluted diaphragm design. While competitor couplings have a single diaphragm, only Ameriflex utilizes multiple separated diaphragms in a pack to provide enhanced performance. Other features include:
• High torque-to-weight ratio
• Field replaceable flex element sub-assemblies
• Low windage and horsepower loss
• Diaphragms are 15-5 PH stainless steel
• High torque-to-diameter ratio
• Low repeatable unbalance
• Diaphragms are designed for infinite life using Finite Element Analysis verified by strain gage and dynamic testing
• R Series integral filler design maintains diaphragm flex area separation with optimized convolution form
• Diaphragms are shot-peened for improved fatigue strength and stress corrosion resistance
• All Ameriflex couplings are manufactured to API-671 requirements
• Maintenance-free for years of dependable performance
Comments