Ingenero Technologies Pvt. Ltd.
Thane, India
Platinum Pipe Award Winner: Correlation to Test/Field Data
Does this sound familiar? A client with an aging utilities system operating at the upper limit of its intended design hopes to improve reliability and optimize energy use. They also want to minimize the cost to implement these improvements. If it does, you might be like Ingenero Technologies engineers Swapnil Paingankar and Manish Bohara. This team was tasked with analyzing and recommending improvements to a hot oil network at the edge of its design limit.
Due to flow rate limitations, the client’s hot oil network operated at a marginally higher inlet temperature to meet the required heat duty for the system’s 21 consumers. By addressing the hydraulics of the system, the client could reduce the inlet hot oil temperature, reducing the firing in the hot oil heater to reduce energy use and operating costs. The engineers suggested an AFT Fathom model to identify and rectify design and operating abnormalities. Changes to this calibrated model could then be used to explore improvement alternatives for the system at the lowest cost.
The first step to identify an operating issue is modeling the system as its intended design. The engineers built their model from drawings, capturing fittings and losses using AFT’s provided database and inputting K factor losses for heat exchangers and other flow elements. Other components such as pumps and valve Cv characteristics were integrated into the model from datasheet specifications. Finally control valve setpoints were confirmed using total heat load across the system due to unreliable data. The workspace of their model, color-coding the Hot Oil Supply and Hot Oil Return of the loop, can be found in Figure 1.
The engineers could then compare their first draft model to plant data. The initial model indicated a hot oil pump suction pressure of 3.8 bar (55 psia), more than 45% more than the plant reported 2.6 bar (37 psia). This discrepancy was similarly found in other measured pressures downstream. Increasing the resistance at the pump suction ensured the modeled system and plant data were consistent, as found in Table 1.
This additional resistance led the engineers to consider an unexpected blockage upstream of the pump. The engineers suspected a malfunctioning manual valve at the pump suction, which the client was reluctant to examine. During a shutdown, inspecting the valve revealed the valve stem and gate were no longer connected, leaving the valve in a throttled position. After replacing the valve, plant data was consistent with the original model’s predictions.
Using their calibrated model, the team evaluated diverse scenarios to enhance flow with minimal hardware changes. With resized lines, flow elements, control valves, and the addition of booster pumps, the system could comfortably meet the heat duty at a comparatively lower heater temperature.
AFT Fathom helped Ingenero engineers identify issues plant data alone couldn’t reveal, providing energy savings by eliminating unwanted resistance. A calibrated model allowed engineers to explore alternative proposals to meet the client’s design requirements while minimizing the cost to implement. So, the next time your utilities’ reliability and efficiency evaluation sounds a little too familiar, rest assured AFT Fathom is familiar with helping you solve these problems and more.
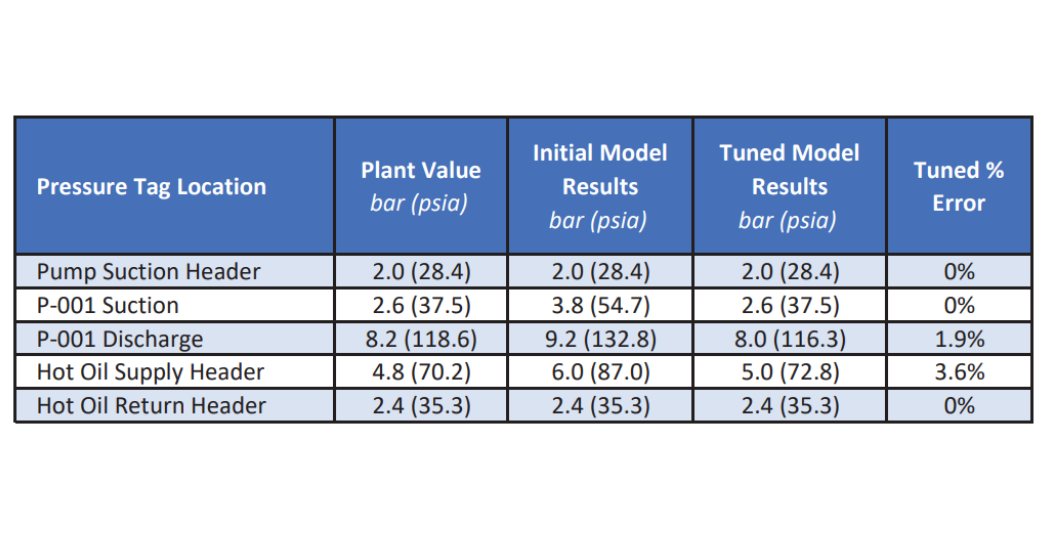
Table 1: Comparison between plant data with faulty pump suction valve, initial model results, and adjusted model results. Ingenero engineers were able to fine-tune their model to both cases to identify the faulty equipment and for use while evaluating improvement scenarios.
Comments