A sugar cane producer in Hawaii was having issues with previously installed slurry pumps, transporting wastewater through a production plant. The liquid was abrasive, and the customer used rubber-lined slurry pumps to deal with the sugar’s and plant fiber material’s tendency to scour the inside of the pump.
The installed pumps needed frequently maintenance/service shutdowns, and required flush water for the seals. For the application, the specific gravity of the sugar slurry was 1.05%, the TDH was 60’, the operational RPM was 470, and flow was 4,900 GPM.
Cornell Pump suggested our 10SP series because the customer preferred to stay with a slurry pump. The SP comes in metal and rubber-lined, 2”-12” discharge. Cornell suggested the metal liner to better deal with the abrasion. With the specific gravity and percentage of solids in the application, Cornell’s MP or N series pumps in hardened material could have also handled the slurry.
Three 10 SPs were installed in 2014, and a fourth was held on standby. The spare was never used, even though the 10 SP’s ran 24 hours a day, every day. The seals were not replaced, because they never leaked.
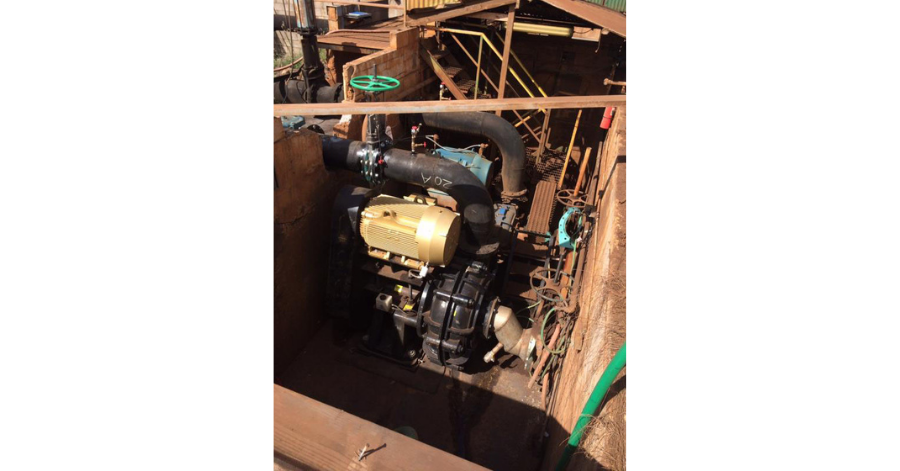
Pumps installed in Hawaii (Piping was changed at the suggestion of Cornell Pump)
The Cornell 10SP pumps delivered an estimated $12,000 a year in saved maintenance. An even bigger cost savings accrued to the plant by not requiring flush water. A typical 10” pump needs about eight gallons a minute of flush water for a mechanical seal. At 0.004 cents a gallons (average US price per gallon of municipally supplied water) that may not seem expensive. Eight gallons a minute run 24 hours a day, is 4.2 million gallons of flush water, at an average cost of $16,800 a pump per year. The three pumps saved over $50,000 a year in flush water costs. The pumps operated for a little over two years, and save the producer over $130,000 in operational costs. The plant ended up shutting down, because of overall world sugar prices.
Pumps provided to the sugar plant:
- Four 10SP Cornell Cycloseal® slurry pumps.
- Frame mounted with 150HP-1200rpm motors.
- Cast iron housings
- Chrome iron liner with chrome impeller
- Chrome iron back plate with Cycloseal®
- 150HP 230/460 volt, 1200 rpm TEFC motor
- Steel overhead motor base with belts, shives, and guard.
- 2 year warranty
Comments