For thousands of years, miners have extracted precious metals and building materials from the earth. Changes over time have been incremental—but the newest industrial wave is set to make a dramatic difference in efficiency, reliability, and profitability.
With better connectivity, monitoring systems, and processes feeding artificial intelligence through the Industrial Internet of Things (IIOT), the mining world is set to evolve rapidly. That is where Cornell Co-Pilot, a system monitoring device adaptable to pumps, motors, valves, and other process equipment in mining, comes into play.
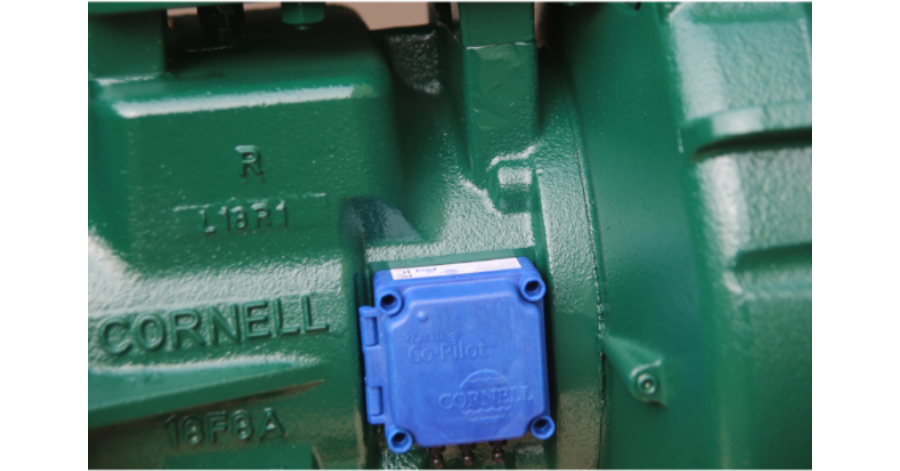
Cornell Co-Pilot’s hardware attaches directly to the pump frame and connects to the cloud to report data at regular intervals (frequency of data reporting dependant on power type. Co-Pilot can run on battery or hard-wired power).
IIOT allows alerts, reports, monitoring, and modeling. Cornell’s Innovative Co-Pilot pump monitoring system confers these advantages to mine operations:
- Remote access: The Co-Pilot gives users the ability to track, monitor, and control their pump remotely without having to travel to remote site installations. Use on any equipment where data from vibration, temp, GPS and/or other sensors can be captured and monitored to improve operating life, increase production time, and drive down costs. Mounted to pump brands other than Cornell, as well as conveyer drives, gearboxes, mixers, compressors, crushers, shaker-screens, centrifuges, engines, etc.,
- Fuel monitoring: Allows users to track and predict their fuel level for each Co-Pilot enabled (remote or portable) pump, which significantly reduces the time it would take for an individual to drive from site to site and continuously check on fuel consumption.
- Wear Rate/Predictive Maintenance: Track changes in machine performance to estimate wear rate, vastly reducing the need to open pumps and check parts. As the system learns running conditions and operations, Co-pilot users can better predict how parts will wear, when to
make adjustments, and then order and replace parts prior to a costly unplanned shutdown. Alerts can be set up and sent to immediately notify of off-spec operating conditions. - Planned Maintenance: Real-time information regarding operating hours, bearing frame temperatures, fuel & fluid levels, and changing machine performance, etc. allow maintenance teams to efficiently plan for upcoming equipment service needs vs. reacting to unexpected problems.
- Reducing downtime: Keeps machinery up and running with increased efficiency and reduced failure rates. Minimizing downtime saves the customer between 75-100k for each pump, based
on estimated lost production and maintenance crew time. - Enhance pipeline integrity: With Co-Pilot’s internal and integrated sensors, monitoring can be distributed all along a pipeline to provide a comprehensive picture of operations to enhance safety, integrity, and performance optimization.
- JIT Ordering: Just-In-Time ordering through Cornell’s e-Commerce platform connected to the Co-Pilot user interface, allows for pre-ordering of the right part at the right time to help maintain lower overhead costs and keep the mine running smoothly.
- GPS Location: Through GPS location tracking, know exactly where a piece of mobile/portable equipment is at all times. Track how often it is moved, when it has been used, under what conditions and do so quickly.
- Greater energy efficiency: Operating the rotating equipment at better points on the pump curve is possible with real-time operational data. A few percentage points of efficiency gained on a piece of equipment running several thousand hours a year can be thousands of dollars in savings.
- Business analytics: Data from connected pumps can be analyzed, overlaid, and integrated to generate mission-critical insights which then can be shared with on-site and off-site teams. Better uses and operating cases can be explored to maximize the utility of your equipment.
- Greater safety: With rotating equipment, sending signals (even shutting down) is possible if operating outside of established parameters, so the equipment can be run more safely for everyone on-site.
- Remote Support: Get remote assistance and diagnostics support directly from a Cornell expert or from one of their trusted partners. You can even perform diagnostics to eliminate unnecessary trips to distant equipment and ensure your time is allocated to the most important tasks.
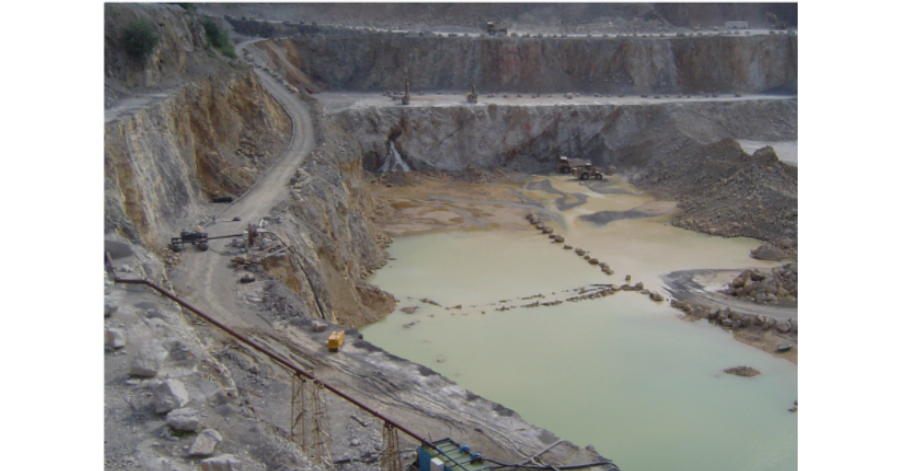
Mining sites like the quarry shown above can benefit from remote monitoring for pumps that are running while the operation is unmanned during dewatering.
Cornell offered a dozen reasons why Co-Pilot could benefit a mine in general. If they look at your specific application, they might be able to define a dozen more for you.
Comments