As a manufacturer of gasket material, a common question we are often asked is, “How can you cut this”? It’s a great question that can yield several options based on the knowledge of our experienced gasket engineers to help meet your needs quickly and economically.
When it comes to soft gaskets, there are three main cutting methods with each providing its own pros and cons depending on the gasket requirements. The main considerations for each method are time, quantity, tolerance requirements, material scrap/yield, and the quality of cut.
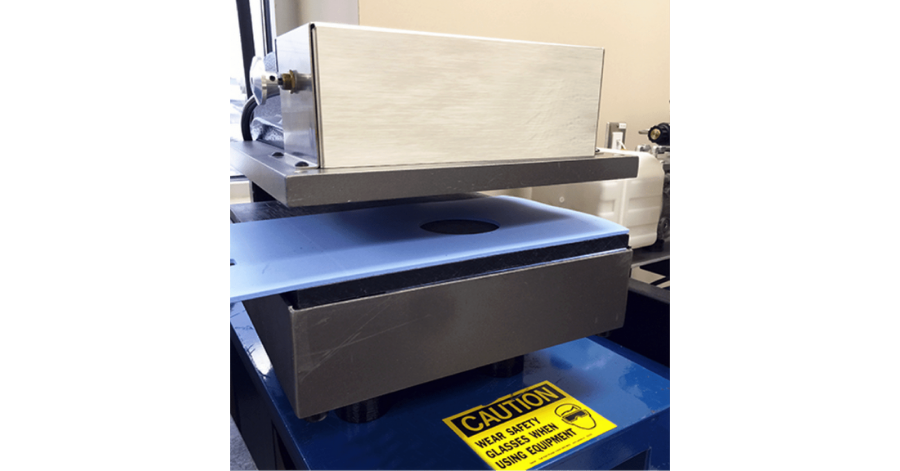
Clicker press
Gasket Cutting Processes
- Manual cutting methods are very common and generally performed in plants for jobs that require custom gaskets to be cut in the field. The material can be cut with a utility knife, scissors or shears, or even by a battery-operated device. The dimensional tolerance of hand-cut gaskets is based on the person cutting the gaskets, however, realistically the tolerance on most hand-cut gaskets would be greater than +/- 3.2mm (1/8”). Additionally, with hand-cut gaskets, there is usually more than one scribe or cut mark, which can potentially lead to jagged edges or nicks in the gasket, thus creating a weak point. Manual cutting is somewhat slow and tedious and tends to result in a higher yield of gasket scrap or waste.
- A Clicker press is another method that is commonly used in higher production runs. A rolled steel die is made up and then the die is placed on the material and pressed into it by a pneumatic press. The tolerance of the gasket is much higher than manually cutting and the material yield is much better. The process is still done manually, however, the yield of material is based on the user/operator. The process is economical for larger gasket quantities because a die still needs to be made for each size and there is some maintenance involved in sharpening and maintaining the dies. Die-cutting is not recommended for larger OD gaskets or custom
sizes that required small quantities. - CNC digital cutters utilize a 3-axis cutting head that have either an oscillating head or drag knife that cuts the material. Gasket dimensions are converted to CAD drawing file(s) and then uploaded into the machine to be cut. The big benefits to using these types of cutters are the speed, high level of accuracy, and material savings due to being able to nest all the gaskets together for the optimal yield. Additionally, for custom size gaskets there is no die or tooling required just a CAD drawing to upload. Literally, the operator can put the material on the table, nest the gaskets desired to cut, hit start, and walk away.
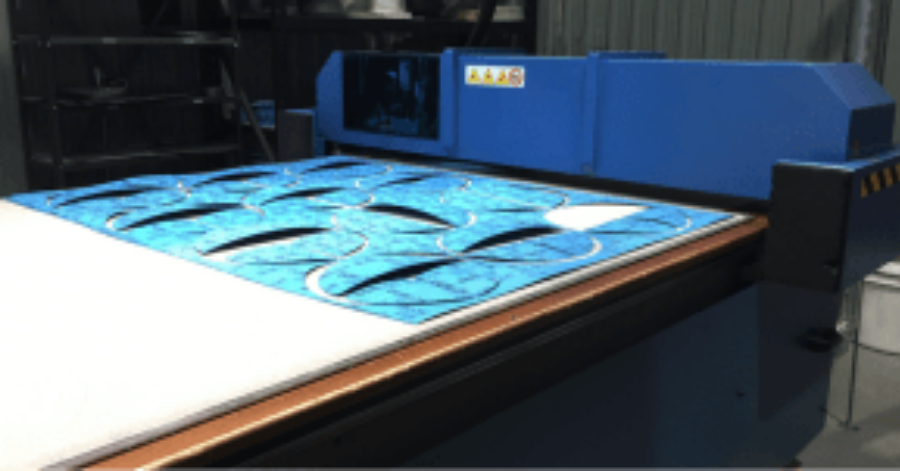
CNC digital cutters
We have many custom fabrication capabilities and we’ve seen success with all of these in different materials on our product line. If you don’t produce your own gasket material, one of the most important things you can do is ask your gasket manufacturer how they would recommend you cut the material. It sure beats wasting time and precious material!
Comments