The European Sealing Association, Sealing Devices, and the role of PFAS’s. The European Sealing Association (ESA) represents most Sealing Device manufacturers in Europe. The ESA has over 50 members, with a combined turnover of Euros 2.6 billion, and employs some 12,500 people. 50.6% are in manufacturing, 8.8% in R&D, and 25.9% in Sales and Marketing. The ESA works in close cooperation with the Fluid Sealing Association (FSA) which represent the large majority of Sealing Product manufacturers in USA, Canada and Mexico. For a full description of the five main Sealing Device product groups represented by the ESA please refer to Appendix 1.
PFAS are critical to global industry in their use as sealing elements. This document outlines the position of the European Sealing Association (ESA) that seals made from fluoropolymers (fluoroplastics, fluoroelastomers) are irreplaceable in certain industries and that a blanket ban or regulation of PFAS required for the sealing industry will have a profound negative impact on society (health, welfare, and standard of living).
Per- and Polyfluoroalkyl Substances (PFAS) is a broad “Class” of materials under scrutiny for health and environmental concerns. Governments and regions are seeking to regulate the use of PFAS, which could lead to restriction in their use, stringent control measures, or a ban of this entre class of materials. REACH (Registration, Evaluation, Authorisation and Restriction of Chemicals) in the EU are seeking to restrict the use of PFAS and the placing on the market of products containing PFAS in the EU as far as possible.
Controversially REACH scope for proposed PFAS regulation includes both small molecules and polymers. The inclusion of small molecules in scope for PFAS is understandable; small molecules are subject to REACH registration, they each have a unique defined chemical structure, known physical properties, and their health and environmental impact can be assessed. Small molecular weight PFAS include surfactants, plasticisers, and also chemical reagents used in the manufacture of other chemicals including monomers for PFAS polymers.
By comparison, when REACH was developed, requesting registration for polymers was deemed too difficult, because of the complexity of the polymer market, in terms of the size and variability of polymers on the market. In 2015 Bio by Deloitte undertook a review of REACH for the EU regarding how registration of polymers could be included within REACH.1 The review assessed which polymers could be considered Polymer of Low concern and thereby waived from REACH registration, this took into account worldwide research and the position of global governing bodies. For a polymer to be of Low Concern certain criteria had to be met, including;
– High number average molecular weight of the polymer
– Negligible presence of low molecular weight materials including oligomer and residual monomer content
– Resistance of the polymer to degradation
– No functional groups in the polymer that are known to be harmful
Polymeric PFAS, also called fluoropolymers, are used as coatings for non-stick cookware, as water repellent textiles, and in electronic equipment. In the sealing industry fluoropolymers include fluoroplastics such as PTFE which are used in gaskets and in compression packing yarns, and cross-linked fluoroelastomers (rubbers) with application as O-rings and custom geometry seals.
This document outlines the position of the European Sealing Association that fluoropolymer seals which fall within scope of PFAS are irreplaceable in certain industries and that a blanket ban or regulation of these polymeric PFAS will have a profound negative impact on society (health, welfare, and standard of living). Larger molecular weight materials, such as polymers and cross-linked rubbers are non-bioavailable. PFAS polymers are considered to be Polymers of low Concern (PLC). They are critical to global development and pose no concern to public safety, yet the current REACH definition of PFAS groups these polymers together with low molecular weight PFAS of known concern such as PFOA and PFOS. 2 3
The ESA asks that PFAS fluoropolymer (Fluoroplastic & Fluoroelastomer) materials are exempted from the proposed regulation.
It is important to note that because fluoropolymers are manufactured using low molecular monomers and short chain intermediates. PFAS monomer feedstock must continue to be allowed for manufacturing with use controls, if appropriate, put in place.
PFAS
Per- and polyfluoroalkyl substances (PFAS) comprise a “Class” of organic alkyl (carbon based) substances in which the carbon-hydrogen groups on which all (Per-) or many (Poly-) of the hydrogen atoms have been replaced with fluorine. PFAS is the widest definition and class name for all chemicals containing CF2 or CF3 groups. This includes discrete small molecules, monomers, short chain fluorochemicals used as part of a polymerisation process as an example, up to high molecular weight fluoropolymers such as PTFE, FKM and FFKM. This is the class subject to regulation by REACH in the EU.
The strongest covalent bond that carbon (C) makes with any other element is with fluorine (F). 4 The C-F bond is resistant to both chemical and thermal attack. Fluorine atoms are very large by comparison to hydrogen atoms so in addition to the individual C-F bond stability as more hydrogen atoms in an organic alkyl compound are replaced with fluorine the overall stability of that material increases due to the large fluorine atoms shielding other chemistry within the molecule from attack. Furthermore, fluoropolymer materials containing C-F bonds have an exceptionally low coefficient of friction; being slippery. Fluoroplastics repel both water (hydrophobic) and oil (Oleophobic) making them of industrial importance as surfactants, water repellents, and non-stick surfaces.
The strength of the C-F bond means PFAS materials are resistant to degradation by acids, bases, oxidants, reductants, light, nuclear radiation, microbes and metabolic processes. These properties make fluoropolymer a product of choice when excellent chemical resistance, High thermal stability or extended lifetime are required in a sealing application. As a result, they can be “Persistent Substances” in the environment.
The use of fluoropolymer (fluoroplastics and fluoroelastomers) in the Sealing Industry
Industrial seals are used to contain media (powders, gas and liquids) inside hardware (process or storage equipment). Media within non-moving equipment are secured by “Static Seals” such as gaskets, whereas pistons and rotating equipment such as bearings and gearbox use “Dynamic Seals”.
Hazardous, toxic, flammable, corrosive and reactive chemicals are media found in different industries all of which require high performance seals to be used efficiently and safely. Seals are used in aggressive environments where they can be exposed to conditions, such as, wear, abrasion, radiation and extremes of temperature.
Different types of materials; metals, Inorganics such as ceramics and graphite, and polymers (plastics and cross-linked elastomers) are used in industrial seals. In each case the seal material is selected based on the specific application requirements.
Seal materials must:
- Withstand the environmental conditions of the application, including, media, temperature, pressure, speed, and abrasion
- Not damage other equipment (hardware) in which the seal is housed
- Be compliant with the counter surface to maximize sealing efficiency
Prevention of damage to hardware such as flanges, pipes, valves, and containers necessitates that contact seals are comprised of softer materials than the hardware into which they provide the seal. This prevents physical damage to hardware such as scoring or wear. For this reason, graphite, plastics and elastomers are favored. Demanding applications, such as the prevention of fugitive emissions in the petrochemical industry or with toxic media and with high system pressures, require sealing materials with sufficient mechanical strength to withstand the system pressure and that have very low permeability to the media. Fluoropolymers (fluoroplastics and fluoroelastomers) have unique importance for demanding industrial sealing due to their mechanical properties (strength and comparative softness) combined with chemical stability, thermal stability, low permeation, and low surface energy.
Polymers (plastics and elastomers) are manufactured from monomers which react together to form the repeating unit of the polymer. Fluoropolymers are manufactured from low molecular weight PFAS monomers and in some cases using PFAS process agents. It is an important consideration that a class ban on low molecular weight PFAS is in effect also a ban on fluoropolymers (Fluoroplastics & Fluoroelastomers).
The use of low molecular weight PFAS raw materials is limited to the manufacturing locations of the fluoropolymer and fluoroelastomer. It is therefore recommended that PFAS monomers in the polymer supply chain are exempted from any PFAS ban and that different controls are considered which enable their safe and continued use.
Where short chain PFAS and polymeric PFAS (High Mw) are used
Use of fluoroplastics
Fluoroplastics (i.e., PTFE, PFA, …) are the only plastics that combine both the broadest chemical resistance with the highest operating temperature with an acceptable compliance to counter surface and therefore are used when other alternative plastics cannot offer the required chemical & thermal resistance combination for industrial applications. Many references are available in the public domain that highlight this:
Classes of Substances at 20°c, Chemical Compatibility Chart. REF 5
Chemical Resistance of High Performance Polymers. REF 6
REF 7
Use of fluoroelastomers
The well accepted ASTM D2000 chart below represents the elastomer families available on the market and rates them against heat and oil resistance. 8 The green shaded area represents materials with the best chemical resistance and best thermal stability, all of which are fluorinated.
Above 200°C only fluoroelastomers come into consideration for elastomeric sealing applications and at lower temperature, the drive for using fluoroelastomer is mostly linked to the broad chemical resistance.
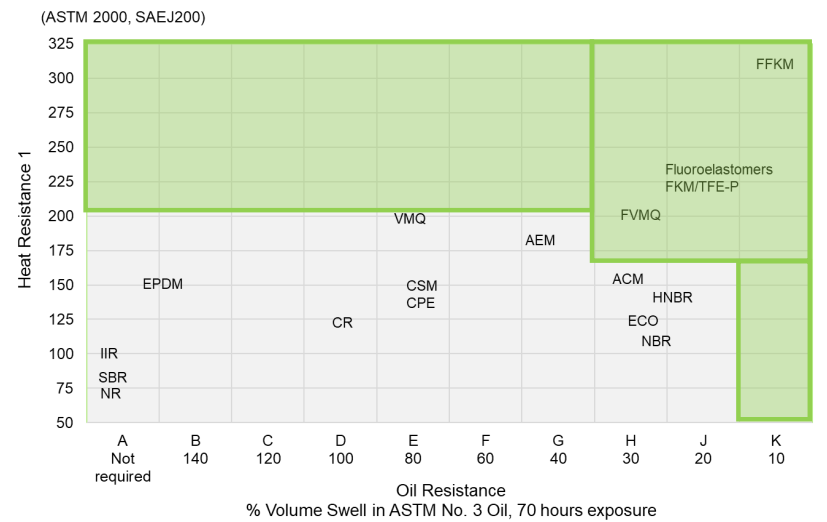
1 Maximum temps at which vulcanizate can be aged for 70 hours with changes in tensile strength ≤ ± 30%, elongation ≤ -50%, and hardness ≤ ± 15 points.
Summary
Linked to the high strength of the Carbon-Fluorine (C-F) bond, fluoropolymers (fluoroplastics and fluoroelastomers) uniquely offer chemical inertness vs aggressive media with thermal stability.
Many applications are enabled in our everyday life thanks to the use of fluoropolymers:
– Reduction of engine emissions both for planes (Increased efficiency allowed by higher operating temperature) and cars (higher thermal resistance allowing engine downsizing)
– Production of more powerful and more energy efficient computer processors which are now part of our everyday life (Smartphone, Datacenters, Artificial Intelligence)
– Reduction in fugitive emissions linked to lower permeation in chemical production
– Reduced worker exposure linked to longer seal lifetime in the application. Every seal changed is a potential exposure for workers to the sealed media
– Sealing of drug production vessels to allow to production of the latest disease treatment thanks to their extremely low to no extractable materials
Banning the use of fluoropolymers articles and the use of low molecular weight PFAS intermediates at the fluoroplastic manufacturing locations would step the science of sealing backward to the 1950s timeframe.
The ESA asks that PFAS fluoropolymer (Fluoroplastic & Fluoroelastomer) materials are exempted from the proposed regulation.
It is important to note that because fluoropolymers are manufactured using low molecular monomers and short chain intermediates. PFAS monomer feedstock must continue to be allowed for manufacturing with use controls, if appropriate, put in place.
Case study: Use of fluoroelastomers Sealing elements in Gas turbine Engines
Key facts:
- 400% increase in passengers over the past 30 years
- Multiple gas turbine suppliers in Europe (Rolls-Royce, Safran, MTU, …)
- 70% fuel consumption reduction over the past 40 years
Planes are a common means of transportation with a 400% increase in passengers over the past 30 years as it has become affordable thanks to the gain in aircraft efficiencies.9 Military planes are also an essential asset for countries defence system.
In both cases, gas turbine engine development has been driven by higher engine efficiencies and higher thrust while reducing emissions.
From the literature it can be found that at constant rpm, maximum thermal efficiency can be obtained by maintaining the highest possible exhaust temperature 10 and this resulted in turbine entry temperature doubling between 1940 and 2010 11. This has helped to minimize emissions (70% reduction in fuel consumption over the past 40 years 12).
In summary, higher engine operating temperature helps increase efficiency and reduce emissions. This has driven temperature in some sealing location well above 200°C which can only be withstood by fluoroelastomers. To ensure sealing at elevated temperature the use of fluoroelastomer or perfluoroelastomers is required to meet the combination of lifetime, fluid compatibility and temperature requirements. 13 Other elastomeric solution would not withstand the thermal / Chemical exposure load.
Case study: Use of fluoroelastomer Sealing elements in the Semiconductor Chip manufacturing process
Key facts:
- Semiconductor market size has grown from 204 billion USD in 2000 to 527 billion USD in 2020 14
- Drive for better energy efficiency to increase device battery lifetime or lower power consumption
- Computing power 2x every 2y with same or lower energy consumption
- 2021 European chip act to regain tech sovereignty
The electronics market needs microprocessors that are faster & more powerful (Moore Law shows a two times increase in transistor density in chips every 2 years 15 and at the same time chips become more energy efficient to reduce the global emissions). To achieve this, semiconductor components require thinner (7nm and below) microchip engraving. 5nm technology developed by TSMC is used for example in the latest A15 processor powering the Iphone 12.
The drive for energy efficiency can be observed by the move for HDD (Hard Disk Drive) to SSD (Solid State Drive) which use microchip as memory. SSD consumes 2 to 3 times less energy than HDD. This translates in less power consumption and less heat generated that would otherwise require air conditioning in data centres.
State of the art chip engraving technology uses processes that combine temperatures above 200°C with fluorine plasma and highly polar chemicals. Engraving at a nanometer scale, 5 nm at present and with demand for thinner engraving, is extremely sensitive to nanometer particulate contaminants.
By announcing a European Chips Act in her State of the European Union address in 2021, President Ursula von der Leyen sent a strong geopolitical and economic signal to enhance European production capacity for semiconductors and European tech sovereignty. 16
The use of fluoroelastomer or perfluoroelastomers is essential to seal the ultra-clean processing chambers used to manufacture chips and to enable thinner chip engraving. No other class of material exists that can meet the requirements of combination of lifetime, fluid compatibility, plasma exposure and temperature. 17 18
Case study: Use of Fluoroplastic Sealing elements in Chemical production and transport
Key facts:
- Fluorinated polymers are used as gaskets in equipment for chemical processing, transport, and storage
- The fluorinated gasket market exceeds €100 Million globally per annum
- Refining of petroleum and chemical, drug and food production all use reactive chemicals, e.g., strong acids, where in many instance fluoroplastics, specifically PTFE are the only choice for sealing
- Stringent control on the number of leachable extracts that can be released into the media from the gasket exit, e.g., in Food and Pharmaceutical applications
Chemicals processing and storage industries produce and use an array of aggressive media (such as strong acids) as feedstocks, intermediates and as final product where chemical compatibility issues dictate the utilisation of certain materials for sealing equipment. Many applications require sealing systems that can work at the extreme of pH; 0 to 14.
PTFE polymers are preferred due to their substantial chemical resistance to media attack, extremely low fugitive emission sealing characteristic as well as favourable mechanical properties such as creep resistance, stress retention properties, low friction characteristics – particularly in valve stem and rotary shaft sealing applications and where other materials and compounds do not perform to the same category of sealing integrity required from the industry and EPA. Virgin PTFE also has excellent permeability resistance and no or low leachables which make it critical for food and pharmaceutical industries.
The options for alternative non-fluoropolymer-based sealing materials in these critical process sectors have proved unsatisfactory and unsafe. The unique properties of PTFE polymers are an essential component in the manufacture of gaskets and sealing components within the chemicals processing sector and offer high integrity sealing of VOC’s and other aggressive chemicals protecting the environment from harmful and unintended emissions or leakage.
Case study: Use of fluoroelastomer Sealing elements in the Marine Propulsion
Key facts:
- The majority of ocean-going ships operate with oil-lubricated stern tubes and use lubricating oils in on-deck and underwater (submerged) machinery.
- In 2010 between 36.9 to 61 million liters of lubricant leaked into global marine waters from stern tube and operational discharge from shipping 19
- Mineral Oil was the preferred lubricant for global shipping, however, Mineral oil is harmful to aquatic and terrestrial ecosystems
- In 2013 the Vessel General Permit (VGP) from the Environmental Protection Agency (EPA) in the US mandated the use of Environmentally Acceptable Lubricants (EALs) in all oil-towater interfaces for vessels 79 feet or longer that enter waters 20
Traditional marine sealing materials (e.g., nitrile) designed for use with mineral oil are incompatible with Environmentally Acceptable Lubricants (EALS). They experience changes in mechanical properties, their volume, hardness and tensile strength can all change, resulting in seal failure.
Three different types of EAL exist on the market: vegetable oils, synthetic esters and polyalkylene glycol lubricants. Each lubricant type breaks down chemically when mixed with water to release different biproducts.
Due to complexity in the supply chain and operational use sealing material must work with all types of EAL and be compatible with the cocktail of different bi-products. FKM Fluoroelastomers are the only seal material found to offer compatibility with all EAL type lubricants.
A ban on the use of FKM Fluoroelastomers would result in global supply chain disruption with frequent ship breakdowns or would require the re-adoption of polluting mineral oil lubricants in combination with non-fluoroelastomers seals.
Seawater lubricated open systems that use seawater as the lubrication medium in place of oil are an alternative for new build vessels, however, a mild steel propeller shaft is required for corrosion protection from the seawater. Upgrading existing vessels is extremely challenging and expensive.
Case study: Use of fluoropolymer Sealing elements in the Oil and Gas industry
Key facts:
- Fluoroelastomer seals are critical for sub-sea Oil and Gas exploration and production
- Sour Oil and Gas fields (containing hydrogen sulfide) with high operating temperatures are dependent on sealing systems manufactured from Fluoroelastomers 21
- Natural Gas is a critical commodity with forecast increase in demand 22
- Liquefied natural gas (LNG) is natural gas that has been cooled to a liquid state (liquefied), at about -260° Fahrenheit, for shipping and storage. The volume of natural gas in its liquid state is about 600 times smaller than its volume in its gaseous state 23 24
- Reports vary that between 20 to 43% of the global gas reserves are Sour 25 26
Exploration and production of Oil and Gas requires the use of seals for well head equipment. Exploration and production is risk averse with extensive regulation of equipment and components, and requiring expensive product and system testing. Fluoroelastomer seals are the only option available for many wellhead applications. Combinations of Sour Oil and Gas with carbon dioxide or water are highly corrosive and which chemically attack other grades of polymer seal. For high temperature applications FKM, and FFKM Fluoroelastomers are specified by the industry as the only available materials suitable for sealing.
Handling of Sour Gas and transport of Liquefied Natural Gas require sealing materials that can withstand the hydrogen disulphide and/or extreme low temperature applications yet retain excellent fugitive emission performance. Fluoroplastics such as PTFE retain sealing compliance at cryogenic temperature because of their extremely low glass transition temperature. PTFE lip seals for cryogenic valves, and PTFE gaskets for cryogenic storage tankers are essential.
References
1 Technical assistance related to the review of REACH with regard to the registration requirements on polymer, De Toni A, et al, European Commission – DG ENV, 2015 Feb 17
2 Risk to human health related to the presence of perfluorooctane sulfonic acid and perfluorooctanoic acid in food European Food Safety Authority, 2018 Dec 13
3 Perfluorooctanoic acid (PFOA) exposures and incident cancers among adults living near a chemical plant Barry et al, Environ Health Perspect., 121(11-12), 2013 Nov-Dec, pp 1313-8
4 Understanding organofluorine chemistry. An introduction to the C–F bond O’Hagan D, Chem. Soc. Reviews, 2, 2008
5 Chemical Compatibility Chart – LDPE, HDPE, PP, Teflon Resistance (calpaclab.com)
6 https://www.findoutaboutplastics.com/2020/05/design-properties-for-engineers.html
7 Design and Manufacturing of Micro-Turbomachinery Components with Application of Heat Resistant Plastics, June 2018
8 Choosing the right elastomer for the right application Stahl W, World Pumps, 2006, 481, 2006 Oct, pp 30-33
9 Air transport, passengers carried | Data (worldbank.org))
10 Aircraft Gas Turbine Engine Performance, aircraftsystemstech.com
11 Future Aero Engine Designs: An Evolving Vision, Advances in Gas Turbine Technology (pp.3-24)
12 Low Emissions Propulsion Engine Combustor Technology Evolution Past, Present and Future Hukam Mongia and Willard Dodds -GE Aircraft Engines, Cincinnati, Ohio, U.S.A. ICAS 2004
13 (Thomas, E., “Fluoroelastomer and Perfluoroelastomer Compatibility With Advanced Gas Turbine Lubricants,” SAE Technical Paper 2003-01-3029, 2003).
14 source statista/WSTS semiconductor market forecast 2021
15 Moore’s law – Wikipedia
16 https://ec.europa.eu/commission/commissioners/2019-2024/breton/blog/how-european-chips-act-will-put-europe-back-techrace_en
17 Contamination Considerations for Perfluoroelastomer Seals used in Deposition Processes IEEE, May 2008
18 Journal of Vacuum Science & Technology A 38, 013002 (2020); https://doi.org/10.1116/1.5124533
19 Environmentally Acceptable Lubricant United States Environmental Protection Agency, Nov 2011, (pp 2)
20 VESSEL GENERAL PERMIT FOR DISCHARGES INCIDENTAL TO THE NORMAL OPERATION OF VESSELS (VGP) Environment Protection Authority, USA, 2013 April 13
21 Elastomers for fluid containment in offshore oil MERL, Research Report 320, Health and Safety Executive, UK, Campion et al, 2005, pp 29
22 Gas 2020. 2021-2025: Rebound and beyond
23 Liquefied natural gas – U.S. Energy Information Administration (EIA)
24 Introduction to Natural Gas A.T. Kearney Energy Transition Institute, 2014 Oct, pp 49
25 Introduction to Natural Gas A.T. Kearney Energy Transition Institute, 2014 Oct, pp 15
26 The Global Sour Gas Problem | Stanford Energy Journal
Comments