The Challenge: A fossil-fuel generating station providing standby power was experiencing recurring maintenance concerns and thermal inefficiency problems with the seals on its boiler circulation pumps. Mechanical seals along with floating seal rings and breakdown bushings and an external flush water injection system were employed to address steam flashing, pressure reduction and leakage issues. The sealing system performed poorly, leading to high maintenance costs and lower than expected thermal efficiency. Injection water booster pumps required costly semi-annual maintenance. Additionally, seal flush water was provided by a 4000 hp start-up boiler feed pump. This resulted in additional costs associated with multiple pump-motor starts, maintenance and thermal inefficiency problems.
The Solution: After evaluating the boiler feed and circulation pumping system, Flowserve recommended the installation of a state-of-the-art dual cartridge sealing system designed specifically for high-pressure, high-temperature power applications. A flush plan independent of circulating water was also recommended. This system significantly improved equipment availability and plant efficiency, with long-term savings expected of over U.S. $110 million with a payback of less than 0.31 years.
A fossil-fuel generating station in southern California was experiencing significant efficiency and maintenance issues with the sealing systems for its VEM boiler circulation pumps. (VEMs are specialty power pumps based upon the design of the DFSS and DVSS nuclear radially split single-stage pump for primary coolant/reactor recirculation service.) Each of the station’s two units contained three VEMs. Employed as standby with the requirement to come on line within 12 to 24 hours, the station relied upon a 4000 hp start-up boiler feed pump to provide cooling/flushing water to the VEM pumps’ mechanical seals. This necessitated frequent, expensive start-ups and additional costly thermal inefficiencies to maintain the station’s “hot standby” status.
Originally, the VEM pumps were installed with a combination of floating seal rings, breakdown bushings and packing. Eventually, the packing was replaced with a D-type mechanical seal.
Recommendations
After evaluating the boiler circulation pumping system, Flowserve recommended the installation of DHTW high-pressure, dual seal cartridge arrangements and control panels with dual Plan 23/52 heat exchangers to replace the D-seal, floating seal rings and breakdown bushings. This system significantly improved equipment availability and plant efficiency. It specifically improved operational flexibility and “peak” power generation by allowing operators to “bottle the boiler” (i.e., to efficiently keep boiler water at elevated standby temperatures) without the need for seal cooling water injection or auxiliary boiler feed pumps.
Benefits of the boiler circulation pump upgrades that resulted in improved efficiency and equipment availability included:
- Reduced costs due to thermal efficiency improvements, by saving approximately 12-25 gpm leakage in heated feed water per pump plus retention of heated water during hot standby operation.
- Elimination of the entire injection system piping and booster pumps, resulting in significantly reduced maintenance costs over the life of the pumps.
- Reduced effects of severe service duty and provided an installed back-up seal with the staged pressure DHTW dual seal cartridge.
- Required minimal installation costs due to robust cartridge design. Every seal is factory tested prior to delivery.
- Optimized sealing cooling and pressure control for low maintenance and reliable operation with separate Plan 23/52 piping loops.
- Improved operational flexibility by allowing operators to “bottle the boiler” without the need to operate an injection pump or auxiliary boiler feed pump.
- Improved unit ramp-up time because the effect of the relatively cool injection water was eliminated.
- Virtually eliminated safety issues due to water/steam leakage.
The upgrade successfully met customer expectations for reliable, cost-efficient hot standby operation while
eliminating the need for external injection water booster pumps. A total savings of US $110.85 million is projected at a
project cost of US $2.1 million, with a payback period of 0.31 years.
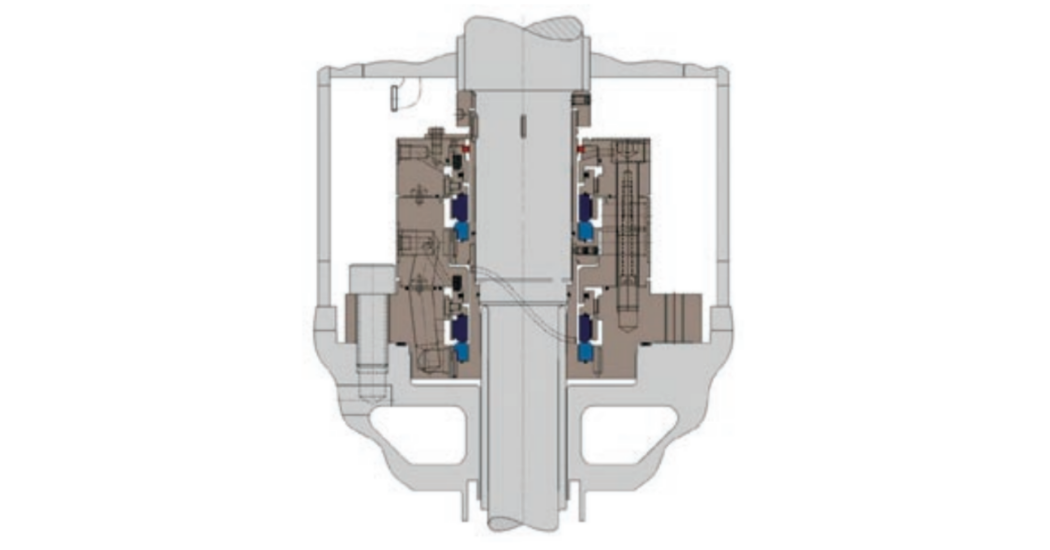
Flowserve DHTW High-Pressure, Dual Seal
Financial Benefits
The projected cost savings presented here are for the three boiler circulation pump upgrades of one of the station’s generating units. Equivalent savings are expected upon upgrade of the second unit.
Per Unit | Cost savings |
Total Life Cycle Cost Savings Over 20 Years |
USD 56.72 million |
Elimination of Water Injection System | USD 1.36 million |
Hot Standby Operation vs. Operation of Units at Night |
USD 52.77 million |
Total Cost Savings | USD 110.85 million |
Expected Return on Investment | 0.31 Years |
Comments