The Situation
Historically, in the United States, there has been a broad tendency to specify 4-pole nominal 1750 rpm motors for use on submersible solids handling pumps. 2-pole 3500 nominal rpm motors are not only becoming widely accepted – they are increasingly the preferred solution for lower flow/higher head applications. There are a number of important considerations behind this change.
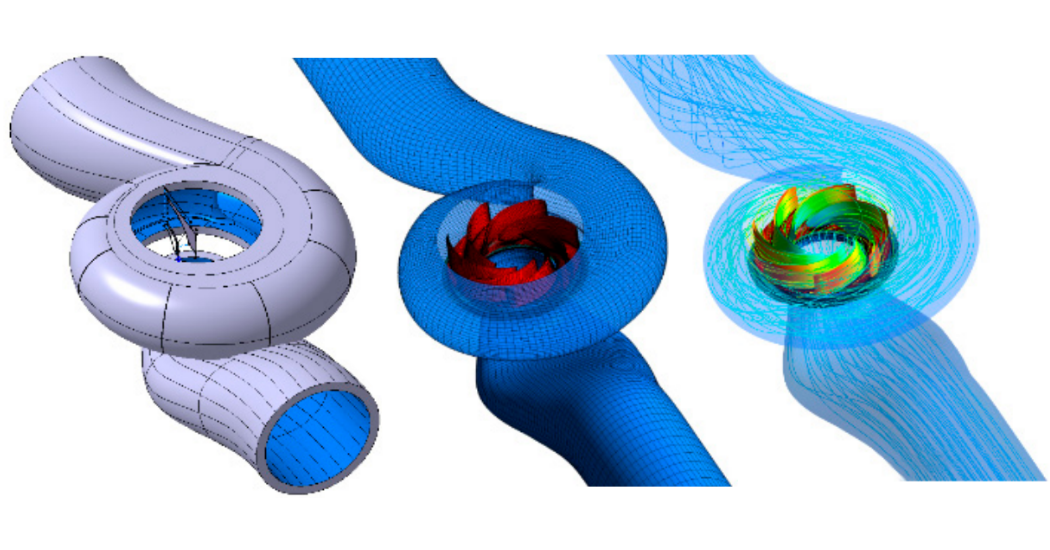
Figure 1: Automated Hydraulic Design
So exactly what has changed?
New technologies have altered how we can view mechanical and hydraulic challenges. Pumps that are to be driven by 2-pole motors have been specifically designed for operation at 3500 rpm in order to achieve the same flow and head characteristics as those designed for operation at 1750 rpm. These new design considerations include:
• Impeller tip speeds
• Selection of appropriate bearings for the application speeds which meet the associated L10 life expectancies
• Appropriate seal face materials
• Optimal diametric running clearances between impeller skirts and the mating machined registers in the interior of the volute
• The use of modern internal volute designs that minimize velocities.
These lower internal velocities eliminate the concern that higher speeds will increase the rate of erosive wear. Today’s machines, using CFD (Computational Fluid Dynamics), are designed with flow patterns, machined tolerances, surface finishes, and many other considerations, for suitable life spans at-2 pole speeds. With CFD we can simulate sand wear as well as analyze forces and vibrations at various flows.
A special consideration that we should make when comparing 2-pole to 4-pole design and life span is impeller vane tip speeds – which will be the same regardless of how fast or slow the motor turns. This is because vane tip speed, which we measure in feet per second at the circumference of the impeller, directly influences the velocity of the pumped media. And in turn, this velocity is directly related to pumping head. In other words, in order to achieve a given head, we need a specific velocity regardless of revolutions per minute. Importantly, the majority of impeller wear occurs at the vane tips. A lower rpm motor needs a bigger diameter impeller to overcome the same head pressure as a higher rpm motor – which will use a smaller diameter impeller. With identical vane tip speed we are able to predict that there will be identical rates of erosive wear.
A smaller high-speed pump with the same impeller vane tip speed as a larger low-speed pump will therefore have a lower initial cost. Additionally, it is more expensive to replace a worn impeller on a slower pump since the part will be larger and will cost more.
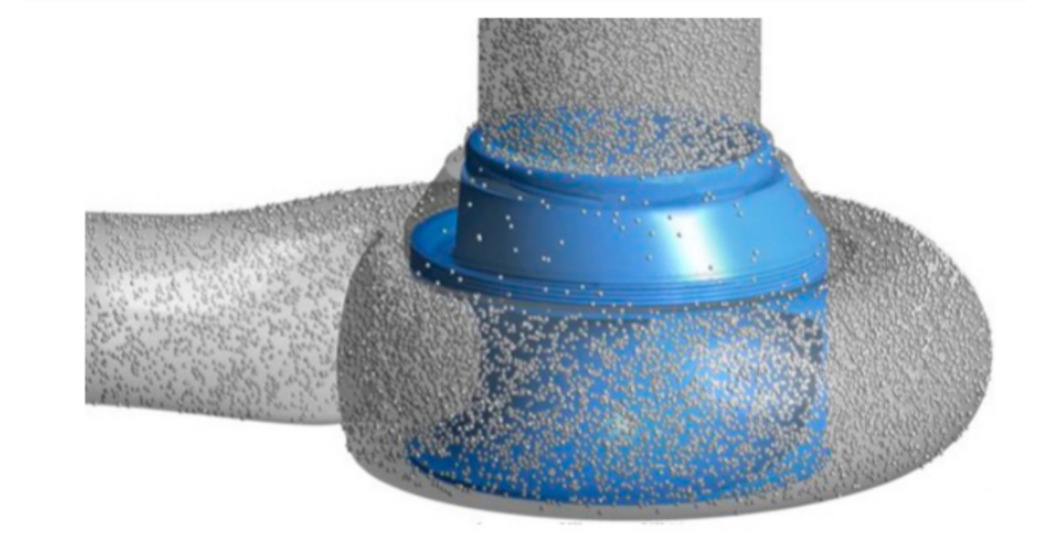
Figure 2: Flow simulations are used to predict sand wear on hydraulic components. This allows the hydraulic designer to optimize the geometry and maximize pump lifetime.
Further, since the increased speed enables the use of smaller pumps, additional benefits include a reduced footprint for use in tight mechanical rooms and lighter weight for safer handling.
Another concern is that with a larger impeller (at lower speed) – balance could become a greater issue. Imbalance will lead to bearing wear, alignment issues, poor performance, decreased efficiency, and reduced pump life.
With the support of CFD we don’t have to rely on instincts and hopes that slower speed motors will protect the pumps. We calculate and demonstrate that the pumps and materials are appropriate for the application and the design criteria.
Many thousands of successful installations over the past ten years attest to the acceptance of this 2 pole solids handling pump design by the specifying engineering community.
Comments