Utilities, consulting engineers, and OEMs concerned about protecting low-horsepower pumps against overheating in ‘dry-pit’ (non-submerged pump) applications appreciate new designs that can negate historic problems prone to cause excessive pump maintenance or premature replacement. While all submersible pumps rely primarily on the pumped fluid for cooling, certain designs can better tolerate today’s debris-laden wastewater to keep processes flowing without costly workarounds (Figure 1).
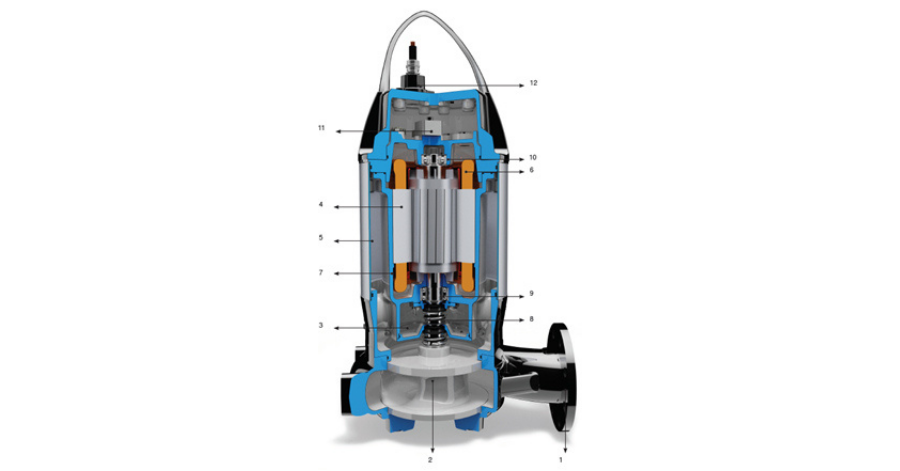
Photo courtesy of HOMA Pump
Figure 1. A pump design with a clog-resistant impeller (2), an ample cooling jacket (5), thermal sensing embedded in the motor windings (6), and options to add shaft-bearing temperature monitoring (10) offers the ability to protect against the most common problems associated with operating non-submersible pumps in hot environments. It has the ability to satisfy applications that are mounted out in the open while delivering performance benefits similar to those of submersible pumps that cool through immersion.
Taking Stock Of Pump Cooling Challenges
Wastewater pumping applications for low-head, low-volume demands in standard wastewater treatment plants, isolated package plants, and even remote pump-station locations pose multiple challenges for low-horsepower pumps:
- Overheating. Air-cooled pumps mounted in aboveground or dry-pit applications, as well as submersible lift-station pumps that run when the surrounding liquid is lower than the motor housing, can experience increased rates of heat-induced maintenance issues or premature failures. Such problems are often exacerbated by continuous-pumping applications, direct sunlight, and extreme seasonal temperatures. Even pumps designed to be cooled by the fluid they are pumping can experience problems if sludge, solids, or other debris fouls the impeller leading edge with buildup of stringy material, or clogs the internal pump passageways.
- Clogging. Any wastewater pumping application can be susceptible to intake or impeller clogging or fouling from flushable wipes, rags, and other debris not screened out of the main flow. While this not only increases run times and amp draw, it also restricts the fluid flow through the pump, increasing the likelihood of pump overheating.
- Maintenance Headaches. Pump impellers and cooling ports clogged by today’s higher solids and stringy material concentrations found in wastewater increase the time and expense needed for routine maintenance, removal and cleaning, or premature motor replacement.
Chronic ragging issues that require pump removal to clear the impellers are costly and time consuming to maintenance personnel. Designs that require additional disassembly to clear the pump internal passageways or that involve resetting or replacing of expensive wear plates (bottom plates) also escalate maintenance costs quickly. Involvement of additional maintenance personnel or even outside repair shops can also delay the maintenance process. This is further exacerbated when pumps are mounted with hard-piped suction and discharge connections that require added maintenance steps.
- Inefficiencies. It is important for engineering, operations, and maintenance personnel to consider pump and impeller designs that provide the best mean time between failures (MTBF). Consideration should be made of how the pump is protected internally from fouling or overheating. Selection based solely on hydraulic efficiency might actually result in a less desirable option. It may require selecting pumps with higher HP, because the published hydraulic efficiency is rated for pumping clear clean water. In the real world of rag-laden wastewater, lower rated pumps may actually provide higher efficiency operation if they are better equipped to deal with debris. Partially plugged pumps can result in extended run times, deliver very low hydraulic efficiency, and most likely incur higher amp draw than their published ratings. When pumping wastewater, ‘sustained’ efficiency over time matters more than the published ‘clean water’ efficiency.
What To Look For In Self-Cooled Pump Designs
While there are multiple design approaches to handling wastewater pump issues, not all techniques provide equally desirable results. It is important to evaluate past performance to pinpoint potential causes of inefficiency or failure. Whatever the initial challenge or changing circumstances in the end use application, look for pump attributes that provide the best performance over the broadest range of conditions.
- Maximum Cooling Resiliency. There are several methods employed to keep motors running within temperature tolerances in today’s submersible pump market. It is important to select one that provides the most consistent cooling performance under the widest range of operating conditions. This will typically minimize unnecessary wear, maintenance requirements, and premature failures as well.
- Integrated Cooling Design. Unlike pumps that depend on external cooling influences such as ambient air, fans, or constant flow of potable water, pumps with integrated cooling designs offer ease of design and installation and are a requirement when pumps are installed in wet wells or potential flood areas. These designs are simple and installation is cost effective. However, not all designs are created equal. Long-term maintenance considerations and overall cost of ownership need to be considered.
- Continuity Of Cooling Operation. The best pump options will minimize overheating risks to reduce cost and maintenance effort, maximize pump life, and minimize the likelihood of premature failures. They will also maintain clog-resistant cooling flow and eliminate the potential for external cooling leaks or human errors that disrupt ancillary cooling flow.
- Cooling Application Flexibility. Not all operating conditions remain the same all the time. Look for pumps that tolerate intermittent operation and variable water levels across clean water, dirty water, and sludge pumping applications, yet function well in dry-pit conditions, submerged or partially submerged operation, and throttled-back variable frequency drive (VFD) performance. This is important because using a VFD for energy-efficient performance raises the heat generated by the motor while reducing the volume of cooling water flow.
- Minimal Clogging Potential. With respect to wastewater flows, choosing hydrodynamically optimized designs enhanced by computational flow dynamics can go a long way toward minimizing clogs that can cause disruptive and costly maintenance issues (Figure 2A). Impellers that optimize flow hydraulics for the passage of large solids and that discourage the accumulation of stringy debris can achieve both (Figure 2B).
With respect to cooling performance, often the simplest solution is best at minimizing maintenance requirements and cost. A cooling jacket that can simulate a completely submerged motor with an ever-replenishing source of clarified pumped product provides the best heat transfer from the motor housing directly to the pumped fluid (Figure 3). Cooling systems that rely on a secondary cooling fluid or oil bath do not transfer the heat directly to the pumped fluid and upset conditions can quickly allow these designs to malfunction. Additionally, increased maintenance costs and expertise are required to maintain some of those more complex systems.
- Simplified, Reduced Maintenance. Reduction of maintenance time and cost is a goal of every wastewater department. The first step for achieving this is selection of equipment that actually delivers these attributes. Simple designs are the easiest to service and typically the least costly. Close-coupled designs are often easily exchanged, especially in wet-well configurations. Different pump designs delivering similar hydraulic performance can vary greatly in long-term maintenance and cost. An in-depth look at available designs should consider more than just initial cost or hydraulic efficiency, as these often play a lesser role in increasing MTBF.
- Pumping And Energy Efficiency. While low-horsepower pumps, especially those running in intermittent applications such as package plants or lift-pump stations, are not the largest energy consumers in wastewater operations, inefficiencies related to impeller fouling and related recirculation in the pump volute can drive up energy costs. The same hydrodynamic principles designed to prevent clogging can also improve performance and energy efficiency (Figure 2), whether operating continuously or intermittently.
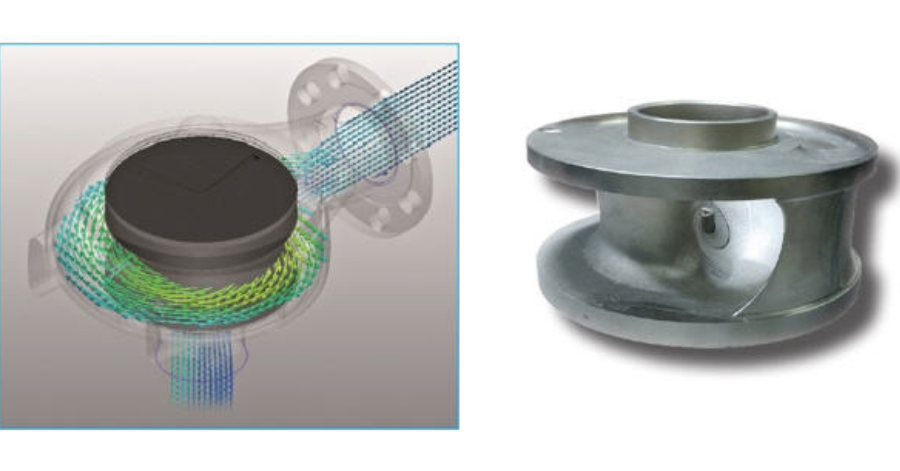
Photos courtesy of HOMA Pump
Figures 2A And 2B. Using computational flow dynamics for efficient pump housing (left) and single-blade impeller (right) designs that minimize ragging or clogging in debris-laden water are two important steps toward improving hydraulics to maximize pump efficiency.
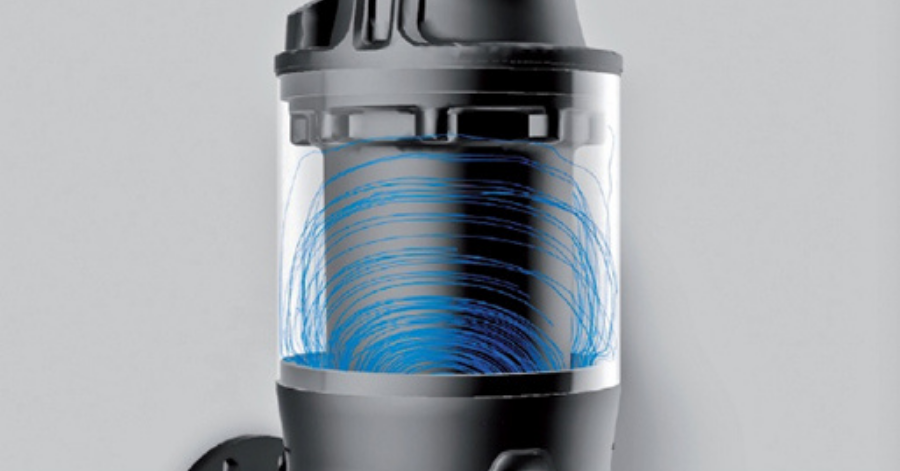
Photo courtesy of HOMA Pump
Figure 3. Using wide open spacing between the pump cooling jacket and the central motor housing instead of small cooling ports minimizes the likelihood of small or stringy debris (e.g., bits of wipes, rags, dental floss, hair, etc.) clogging ports and compromising cooling performance. Because this design features a constant exchange of cooling water and a broad area for good heat exchange, it cools like a submersible pump. It has been shown to lower pump operating temperatures by 15°C as compared to conventional pumps in dry-pit applications.
Added Business Considerations For Versatile Self-Cooled Designs
Self-contained self-cooled pumps can satisfy wet, dry, continuous, or intermittent performance applications that need reliable cooling in a compact footprint — regardless of the level of debris in the water. Look for manufacturers and distributors with a wide range of options to match the right pump curve for the job and with purpose-built pumps that are easily assembled from stock components for quick delivery and ready availability of replacement parts.
Pumps that can operate as totally submersible pumps, as well as being cooled by wastewater flowing through them in aboveground or dry-pit installations, provide added protection for wastewater plants that operate in flood plains. In the event of flooding, that infrastructure investment will not be compromised as a non-submersible pump would be.
Finally, where volume and head requirements are similar, the same self-cooled pumps can satisfy wastewater transfers between tanks, sludge transfers, package plants, and lift stations. This gives utilities the convenience of standardizing on one pump model to be interchangeable across its operations, enabling them to maintain sufficient backup protection with fewer spare pumps or repair parts in inventory.
Originally published on WaterOnline.
Comments