Implementing The Right Solution To Address Code And Building Requirements
Elevators Have Their Ups And Downs
The first concern for an application rooted in a life/safety issue should be reliability. Pumps, and associated controls to manage all liquids in the elevator shaft and sump, play a vital role simultaneously maintaining safe equipment for passengers and firefighters while being environmentally conscious with hydrocarbons.
Code derived from ASME 17.1 provides guidance to plumbing engineers and elevator inspectors responsible for upholding requirements for elevators. Section 2.2.2.5 (2007) outlines three points that create the backbone for specification with a sump pump and approved alarm system —outlining location, flow requirements and need:
- Plumbing and mechanical systems. Plumbing and mechanical systems shall not be located in an elevator shaft. Exception: Floor drains, sumps and sump pumps shall be permitted at the base of the shaft provided they are indirectly connected to the plumbing system.
- Elevator pit drain or sump pump. All elevator pits for elevators that have Firefighters’ Emergency Operation shall have a drain or sump pump in accordance with ASME A17.1 Section 2.2.2.5. The drain or sump pump discharge shall be into the sanitary or storm drainage system through an indirect waste connection. In elevators provided with Firefighters’ Emergency Operation, a drain or sump pump shall be provided. The sump pump/drain shall have the capacity to remove a minimum of 3,000 gal/h per elevator (50 GPM).
- Oil separators required. At repair garages, car-washing facilities, at factories where oily and flammable liquid wastes are produced and in hydraulic elevator pits, separators shall be installed into which all oil-bearing, grease-bearing or flammable wastes shall be discharged before emptying into the building drainage system or other point of disposal. Exception: An oil separator is not required in hydraulic elevator pits where an approved alarm system is installed and an indirect waste connection in accordance with §P802.1.8.
Application of this code varies by jurisdiction depending on interpretation. And varying interpretations are commonplace. The Stancor Oil Minder® product portfolio was built with the necessary modularity to address a variety of configurations and interpretations.
Oil Minder merges Stancor’s knowledge of both pumps and controls to create a system design specifically for elevators. At the heart of the system is a sensor, protected by intellectual property, that uses conductive sensing to reliably identify oil and water. Information from that sensor then guides the action of the accompanying pump(s) and/or valves to the control panel. Finally, several accessories round out the system to ensure proper operation: a single power supply, two floats and, if specified, a junction box DIRECT WIRED along with an eight-pin connector.
Benefit Of A Modular Product Design
Flexibility, designed into the system, has led to multiple configurations that can be tailored to meet jurisdictional interpretations and application challenges. Ultimately, the function—and resulting configuration—depends upon how the code is interpreted in that location. Some potential interpretations that can impact what is specified include:
- Control panel location: it will, in most cases, be located someplace easily accessible like a janitor’s closet or hallway. Sometimes they are placed in elevator machine rooms, but this is becoming less commonplace with the advent of machine room-less systems. On rare occasions, control panels are permitted to be included in the elevator shaft.
- Use of a junction box: the additional component, which combines four cables into a single 8-pin connector, makes installations incredibly easy and efficient. A few states mandate a direct-wired system that does not include a junction box.
- Disposal of liquid in the pit: Oil Minder® recognizes and manages liquids in an elevator sump. In most installations, the system pumps water to storm or sewer and alarms on oil. Some jurisdictions, however, want all liquids out of the pit. The Stancor Liquidator system—available in both simplex and duplex configurations—pumps both water and oil out of the pit.
The modular approach to the Oil Minder product portfolio provides a canvas to specify a cost-efficient way to satisfy code officials, contractors and building owners.
And the result is a tremendous savings in space and cost compared to oil/water separators. Oil/water separators function on principles of gravity. Sizing is a based on the type of oil, amount of oil and flow rates. Saturated, or full, holding compartments can cause significant problems in how liquid is managed. The complexity of an oil/water separator, compared to Oil Minder, also requires additional maintenance to ensure the system is maintained in proper working order.
The vast majority of Oil Minder systems will pump water and alarm on oil (Liquidator systems can pump both water to storm or sewer and oil to containment). This simplified approach, compared to oil/water separators, meets the intent of the code and does so in a cost-effective, reliable manner. The Oil Minder is fully automatic—meaning it will continue to pump, without human intervention, when the probe is in contact with water (which is conductive). This is true even after oil is detected, as it is an automatic resetting system.
The inherent flexibility of the Oil Minder portfolio allows multiple configurations to meet every application. As an example, a bank of three elevators that uses a common sump (to save space) could use a single Oil Minder® system that can pump 150 GPM (50 GPM x 3 elevators). This is becoming more popular. And it is made easy by an integrated system designed specifically for elevator sumps in terms of: minimal size, operation as defined by code and redundancies to operate reliably in a life/safety application.
Evaluating Total Costs
Code is put in place to ensure proper operation and safety associated with a given application and associated equipment. There could be many ways to satisfy that code. Ultimately, it’s in the best interest of the building operator—as well as the supply chain, including architects, plumbing engineers, contractors and, potentially, plumbing warehouses—to meet code demands in a reliable and cost-efficient manner.
Oil Minder was designed to minimize design and installation costs while maximizing the probability that the equipment will be installed and maintained properly. Installing an elevator sump pump system can be a challenge—as contractors could justify either having a plumber or electrician assemble the components. It requires skills from both trades. And the installation must be done correctly due to the potential life/safety issues for firefighters. It is for this reason that elevator manufacturers have avoided installations to eliminate potential liability.
Stancor’s answer to these challenges is: simplicity. The Oil Minder system makes installation as easy as possible. And, in doing so, minimizes costs associated with labor and ancillary equipment.
Oil Minder requires only one 115V power outlet. The power cord is connected to the control panel, which has two benefits:
- easy access to power where the control panel is placed and
- the avoidance of designing in an outlet in confined space (the elevator sump pit). Competitors that have added a sourced control to a pump they manufacture end up requiring two power sources (one for the control and the other for the pump), which results in unnecessary costs.
There are three downsides to a second power source:
- the initial cost for a second outlet,
- the need to go into confined space for access to that outlet and
- the additional complexity required for installation. The latter point, related to installation complexity, is where Oil Minder shines compared to its competitors. Approximately one hour of time can be saved using a multi-option (senior) system with a junction box vs. any competitor. Additionally, Oil Minder® is a plug-and play system—factory-mounted probes and floats eliminate guesswork on where to mount components critical to proper operation.
Think about what that means to the specification engineer and contractor. For the specification engineer, a simplified approach to installation helps ensure that equipment will work as designed. For a contractor, a system that is easier to install reduces liability and saves an hour of labor that creates multiple benefits:
- saving $50-$100 in installation cost,
- ensuring jobs are completed on time and
- freeing up resources to do other jobs.
The savings associated with Oil Minder also extend to the building operator. At the heart of the Oil Minder system is the conductive sensing technology designed into the probe that differentiates between water and hydrocarbons. Stancor has intellectual property protecting the use of conductive sensing to help ensure the system is maintenance free. The voltage difference between water (5VDC) and oil (15 millivolts DC) greatly reduces metal ion exchange and greatly reduces the risk of foreign material building on the probe service. This “self-cleaning” function helps ensure the probe works properly over the life of the application. This is in stark comparison to competitors that use optical sensing and nullify their warranty if the pump is exposed to a hydrocarbon.
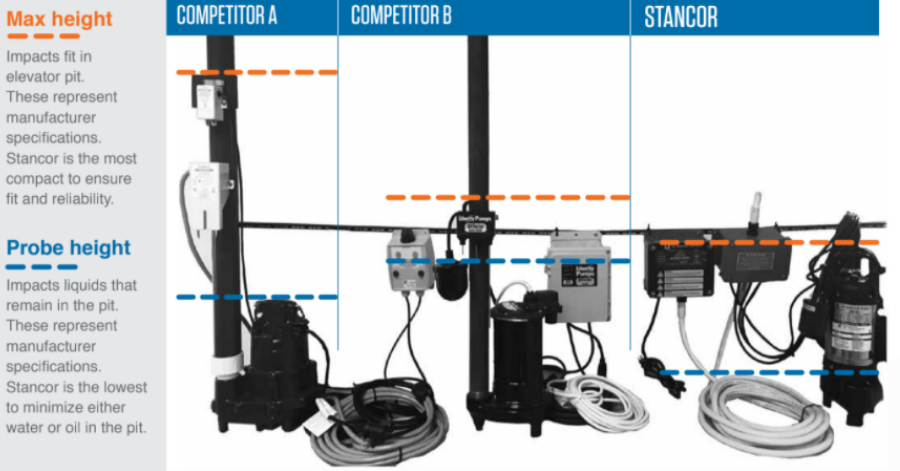
Stancor’s pump and control knowledge forms a complete system—offering a space-efficient, easy-to-install answer to elevator pumps.
The final aspect of streamlined, integrated elevator sump system is the benefits of the compact design. Oil Minder provides the industry’s most space-efficient envelope dimensions within the pit.
Engineers can fit larger systems (including those that serve multiple elevators from a common sump) into a standard 2′ x 2′ x 2′ pit. Installation is easier for contractors given space constraints. And building operators reap multiple benefits:
- space savings from minimized pit size and
- the industry’s lowest probe height minimizes liquid in the sump, which ensures proper operation and limits maintenance costs.
Maximizing Reliability In A Life/Safety Application
Oil Minder® was originally developed for transformers used by Utilities. Given the amount of oil in that application, used to cool the transformer, there are significant environmental risks to a leak. The liability from oil escaping the application is an EPA fine that could be millions of dollars.
Elevators pose a different, and more substantial, risk—personal injury or, in the worst case, a human life. Code is put in place, and enforced, to protect firefighters that might have to use the elevator to quickly reach a fire. So not only is code in place to protect firefighters, it also might help save those impacted or trapped by a fire.
Firefighters that need to gain access to the elevator initiate a sequence of operations to help ensure their safety. The elevator is automatically sent to the first floor. Sensors monitor the temperature on each floor to pinpoint the fire. And sprinklers are on standby to potentially help dose a fire. Oil Minder is operating in the background to ensure water is pumped out the hoist way reliably and maintain elevator functionality in the event of an emergency.
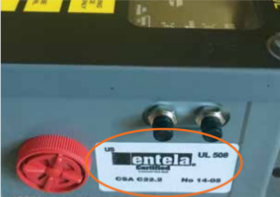
Oil Minder utilaizes a third party to ensure rgid quality standards are met in a life/safety application.
Stancor has taken numerous steps to ensure proper operations should a situation arise that requires firefighter involvement. This heightened sense of responsibility guides more than 25,000 Oil Minder units in the field.
First, all Oil Minder system components are UL approved. The system is built to last the lifetime of the elevator—from the NEMA 4X polycarbonate control panel to IP-protected, self-cleaning probe. Oil Minder was designed to respond to exceed expectations as measured by ease of installation, maintenance commitment and performance reliability. The result is a product that reduces overall costs.
Stancor lives up to this lofty ambition by contracting a third-party firm to inspect the consistency of production processes. The Intertek (formerly Entela) label can be found on 1- and 3- phase SE40, SE50 and SE100 Oil Minder systems.
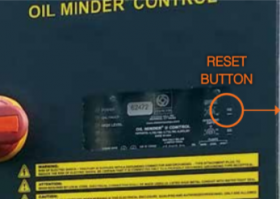
Push-to-test button ensures Oil Minder is properly installed and can be used to excercise the system.
The Oil Minder system features several functions that make it unique in the industry. These features are the result of thinking holistically about the application adding value through a synergistic relationship between the pump and control, as opposed to sourcing a control to pair with a pump like so many of Stancor’s competitors. The push-to-test feature, located on the control panel, allows contractors and operators to ensure the system is in working order with the push of a button. Holding the button for three seconds will trigger a self-diagnostic test that will prompt the pump to run and oil alarm to sound. Contractors and building operators can now have confidence the system is installed correctly or receive a reminder that it remains in working order. And utilizing the push-to-test feature on an annual basis will exercise the system so components are ready should an emergency arise.
Yet another benefit of the Oil Minder® systemic approach is a series of redundancies to alert building operators of a potential problem. Oil Minder features two floats. The high-level alarm offers backup to the lower float, as well as triggering system alarms that indicate the need for immediate attention. The redundant high-level alarm, plus the automatic operation, incorporates watch dog functionality into the Oil Minder system to constantly monitor liquid levels within the elevator.
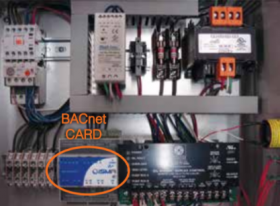
Oil Minder’s integrated BACnet solution features a card in the control panel and can communicate with any protocol.
Finally, for those operators that want to connect the information from Oil Minder to a Building Management System (BMS), and have the IT infrastructure to do so, fully integrated BACnet options are available. BACnet (Building Automation and Controls networks) is an open standard maintained within the HVAC industry. This functionality provides building operators an opportunity to utilize a system that already exists. Stancor makes it easy. The integrated hardware/ software solution can be applied to an Oil Minder system, across any protocol (with MS/TP being the most popular) and offer a menu of commands to properly monitor system performance.
Modularity Drives Customization To The Right Solution
Every building is different. And, therefore, needs can vary greatly. Code provides guidance through regulation to establish requirements. However, integrating building needs, code requirements, local interpretations, budget restrictions and maintenance planning into a singular design can be a challenge.
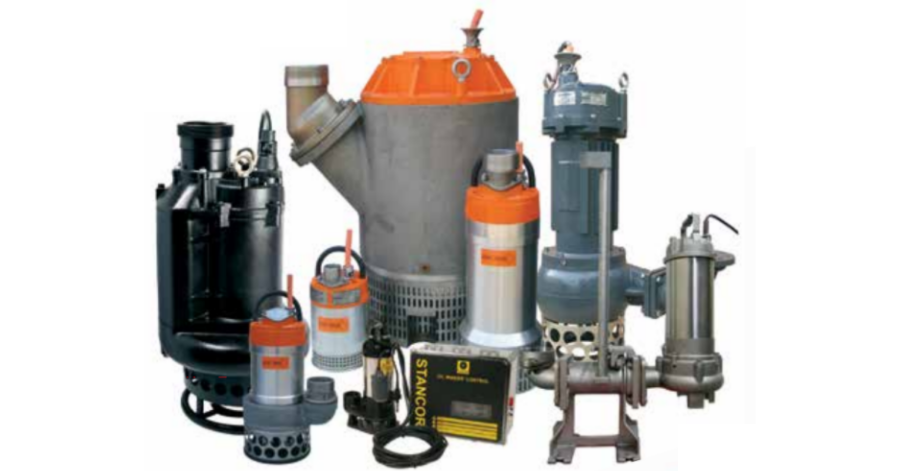
Any one of Stancor’s pumps can be paired with Oil Minder to offer a wide range of potential solutions.
The Oil Minder® product portfolio was created to offer design engineers the flexibility to specify the right solution—every time. Selection begins with Stancor’s comprehensive line of pumps, including stainless, low suction, cutter and grinder options. Oil Minder can be adopted to any Stancor pump.
The control panel can also be customized. In some cases, enhancements account for local jurisdictional interpretations. Oil Minder® Liquidator systems offer an answer when local authorities want all liquids pumped out the sump. Essentially, the Liquidator series offers the market a cost-effective oil/water separator.
Additional control panel modifications include:
- Sensitivity setting: this can be used to capture different hydrocarbons or prevent oil/water mix in sensitive applications. It is rare, however, that a higher setting is specified. This does represent yet another option to make the system flexible and future proof as new oils are developed and introduced in the marketplace.
- Additional or repurposed dry contacts: Stancor’s expertise in controls offers the potential to communicate performance metrics measured by the system. That information can be used to feed a Building Management System (BMS). Additional dry contacts can be added to further enhance the control panel’s functional and, accordingly, improve maintenance programs. Wiring diagrams can be provided, and altered, as the specification is created.
- BACnet functionality: as previously mentioned, Oil Minder can be ordered with BACnet accompanied by a full integration package. A BACnet card is added to the control panel, increasing the enclosure size, to facilitate commands in any number of protocols.
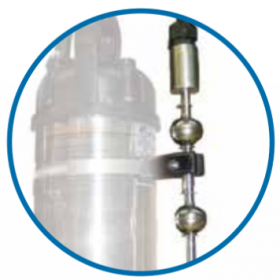
Vertical floats used, in space-constrained applications are an example of features used to meet the needs of every job.
An important aspect of overall system flexibility is variety in the components used to make full functionality possible, even with unexpected application constraints. The default on Oil Minder systems are two tethered floats (including high water for redundancy). Stancor offers an alternative in applications that are space constrained – two versions of vertical (or narrow) floats, featuring stainless steel balls, that eliminate the risk of a float not actuating in small or contaminated areas.
Another feature that can be added is disconnects. Not every jurisdiction will consider the connection between the 8-pin connection and the junction box in a multi-option (senior) system an approved disconnect. NEC-compliant disconnects can be added to the junction box, or even the control panel, to help meet code interpretations and assist applications with high voltage requirements. This is yet another example of how Stancor can customize Oil Minder to meet specific needs.
The Oil Minder system is the culmination of Stancor’s pump and control knowledge. And the company’s ability to use its resources, including 30+ years of engineering to application needs, is maximized through in-house resources. Oil Minder systems are built in our Connecticut facility. This allows Stancor to meet short deadlines. It also qualifies Oil Minder as a Made In America product. Most importantly, it allows Stancor to provide a service as reliable as the 25,000 Oil Minder units operating reliably in the field today.
Comments