The Domtar Nekoosa pulp and paper mill, founded in 1883 as the Nekoosa Paper Company, has been operating along the banks of the Wisconsin River for more than 130 years. The facility is an integrated mill, producing market pulp and publishing grade paper. Annual paper production capacity is 118,000 tons, and an annual pulp production is 155,000 tons.
The facilities management team continually seeks ways to improve the reliability and performance of key equipment at the mill. In an era of tough competition and closing paper mills, this approach has contributed to the mill’s continued success.
COSTS AND CONCERNS SPUR CHANGE
Side entry agitators are used in the pulp and paper process to continuously mix product, preventing solids from settling to the bottom. Due to high amounts of stress on the shaft, agitators commonly suffer from shaft deflection and misalignment, making them very difficult to effectively seal. When a seal fails, it leads to product leakage and contributes to premature bearing failure, causing an increase in unscheduled downtime, expensive maintenance repairs and costly product loss. Six of these side entry agitators were located at the Domtar Nekoosa mill and had become a maintenance issue from ineffective sealing.
Two of the tanks located outdoors contain white liquor, a hot, corrosive and hazardous by-product of paper pulp production. One agitator was sealed with a double mechanical seal with a conventional glycol seal pot support system. The other agitator was sealed with mechanical packing. White liquor leaking through the seals was not only a maintenance issue but also an environmental concern.
The other four agitators were located on tanks inside the mill. These tanks held abrasive ground Calcium Carbonate and Filler Clay slurries. Because the slurries are abrasive, wear to the shafts and packing was excessive. This led to frequent re-packs, unnecessary maintenance and significant product loss. Flushing the packing with clean water would delay the breakdown, but wasn’t acceptable due to dilution of the product in the tanks.
Annual costs for maintenance and lost product on these six agitators at the mill averaged over $82,000. The maintenance team recognized it was time to investigate new sealing options to improve performance and reduce costs.
In late 2005, the Maintenance Management Team met with Chuck Kimball, President of M.R.O. TECH, Inc., a local, long time Inpro/Seal distributor, to discuss options for upgrading the sealing method used on these agitators. Kimball recognized the side-entry agitators on the large tanks were an ideal application for Inpro/Seal AM (Air Mizer®) Solutions™ shaft seals. The maintenance team was eager to try the new sealing technology.
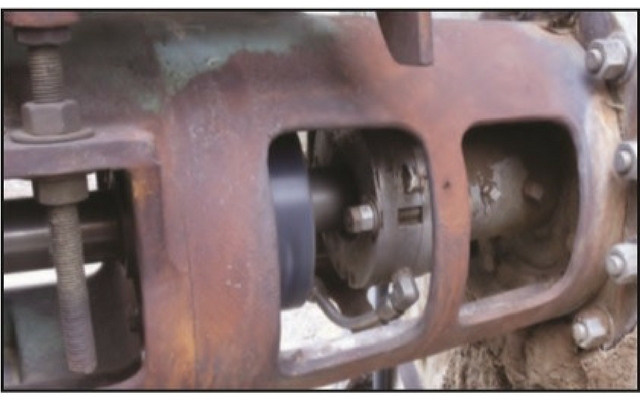
One of two split Inpro/Seal AM Solutions shaft seals installed on white liquor tank agitators
AM SOLUTIONS
Inpro/Seal AM Solutions shaft seals are non-wearing, permanent shaft seals that use a positive purge to create an effective seal, preventing product or harmful emissions from escaping into the atmosphere. They seal by directing small amounts of air, or inert gas, through a precision clearance between the throttle and shaft, pressurizing the clearance. The sealing medium is evenly dispersed around the shaft to prevent dead spots and is directed toward the product and atmosphere evenly to safeguard against both product loss and contamination.
Unlike traditional seals, AM Solutions shaft seals fully articulate to accommodate shaft deflection, run-out and misalignment and do not require periodic adjustments. Their unique non-contacting designs do not wear out or groove the shaft, therefore, providing a permanent sealing solution. All AM Solutions shaft seals are custom engineered to fit the application, and seal powders, liquids, slurries and bulk solids.
Kimball explained to Tom Hintz, Pulp Mill Maintenance Supervisor, the operating principle and technology of AM Solutions shaft seals and the performance up-grade to be expected. The decision was made to proceed.
In December 2005, a split custom engineered stainless steel AM Solutions AM Smooth Bore design was installed on one of the white liquor tank agitators. It proved to be the perfect solution for their leaking agitators. Other installations followed in rapid succession – the second white liquor tank agitator in Aug 2006, and the indoor slurry agitators in 2006, 2007 and 2008.
Hintz said, “The split designs made installation quick and easy. No modifications to the agitators were required, and there is no on-going maintenance with the seals other than maintaining a low pressure air purge.”
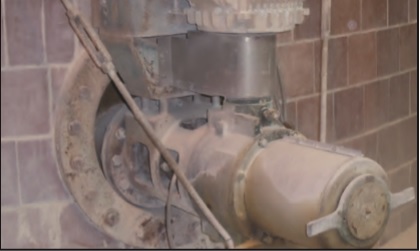
One of four slurry tank agitators installed with Inpro/Seal AM Solutions shaft seals to eliminate product loss and decrease maintenance costs.
By switching to AM Solutions shaft seals, the Nekoosa mill has realized impressive savings. After initial and continuous air costs, the AM Solutions shaft seals are saving the mill:
• $23,000 per year on the two white liquor tank agitators.
• $51,000 per year on the four calcium carbonate and filler clay tank agitators.
Because the cost of the new seals consisted mainly of up-front, one-time expenditures, the team expects the $74,000 savings per year to continue. A significant portion of this saving is the elimination of product loss. “Installing AM Solutions shaft seals on our side entry agitators has proven to be a tremendous success. These seals paid for themselves within the first year of operation and we look forward to continued cost savings for many years to come.”, stated Jim Love, Paper Mill Maintenance Planner.
Comments