The northern California City of San Mateo Wastewater Treatment Plant (WWTP) was built in 1930 but modernized several times, most recently in 2009, to handle a capacity of up to 15.7 million gal per day.
A material handing problem surfaced for the City of San Mateo WWTP in March of 2009. Sludge cake transport had become a major problem that required a lasting solution to fit the demands of the operation.
San Mateo turned to Flo-Line Technology, Inc. when their original material handing design no longer met their needs. Flo-Line Technology has had years of experience developing solutions for a variety of complex transport requirements for slurry, filter/centrifuge cake and other industrial applications.
The specifications and distinct issues for this project were carefully examined by the engineers at Flo-Line Technology. San Mateo for example, works very hard to produce sludge cake with the lowest possible water content since the added water weight translates into higher transport costs. In fact, their application yielded cake with a solids content weight in the 18% to 25% range. On the other hand, the drier media is, the harder it is for rotating equipment to convey.
Flo-Line Technology was aware of the merits of progressing cavity pump technology and conferred with Netzsch Pumps North America LLC regarding the specifications and the technology’s effectiveness in dewatered filter cake applications. Thomas Streubel, the Netzsch Pumps North America President, noted examples in various worldwide locations where progressing cavity pumps were used to transfer filter cake with up to 40% solid content with great success.
Flo-Line Technology analyzed the other aspects of the application: the system layout, piping details, typical flow rate requirements and friction analysis. The formal proposal was created and examined with the San Mateo city staff.
The first option
The first option the San Mateo WWTP had tried, however, was a piston pump system typical in concrete pumping. This system included a dual-piston pump powered by a high-pressure hydraulic pump and associated mechanical, hydraulic and electronic controls which appeared to have the appropriate capability.
To fully assess this pumping system, San Mateo staff decided to rent a trial system ($9000 per month) for eight months before committing to a permanent installation. While this pump system was capable of transporting the sludge cake, the pulsing nature of the pump design required 300 to 500 psi discharge pressure to reach the required pump rate of up to 5 tons per hour. Ultimately the system was rejected due to the overall power consumption, the noise generated by this system operation and annual preventative maintenance costs calculations.
Part of the 2009 expansion also had included two new centrifuges employed daily to dewater the treated cake produced by the plant. This required two shafted screw conveyors that extended 60 ft with a 30-degree angle to move the cake from the centrifuges to a storage hopper. Trucks loaded from the storage hoppers transport the dewatered material to established land applications.
These screw conveyors proved to not be dependable from the start. Hanger bearings and conveyor shaft failures necessitated repairs that did not totally remedy the situation.
All of these factors lead the City of San Mateo to try a different approach.
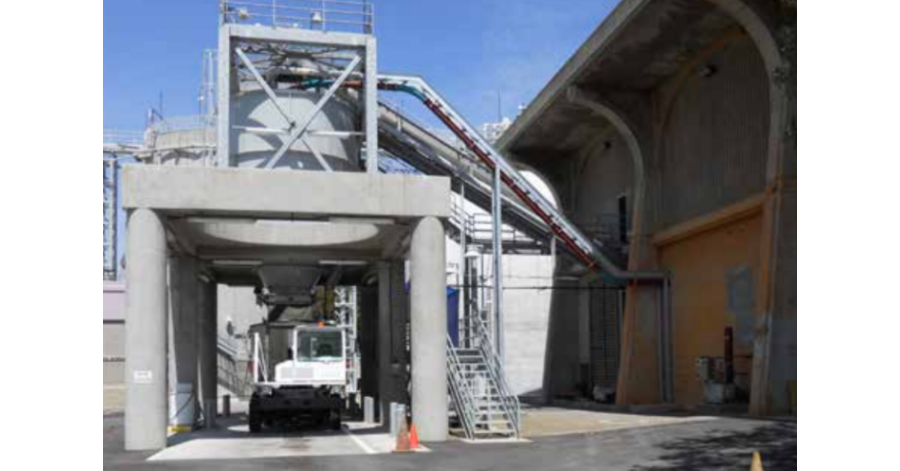
Storage hopper with collection truck.
PC Technology
A progressing cavity pump (PC) transfers media, and in this case, the cake via a rotating helical metal rotor within a compressible rubber stator. There is a tight interference fit between these two components that creates an internal overlap to form cavities which trap and advance the media in a smooth linear fashion based on the speed of rotation. The proposed filter cake pump system required additional considerations related to the viscous character of the cake and so two features were added to the system design.
First, a pump with a force-feed chamber and patented, integral auger screw was specified for easier entry of the product into the rotor and stator from a large inlet hopper. This was to ensure positive feeding.
Next, a Netzsch Friction Loss Reduction (FLR) unit was included in the design. The FLR system can provide pressure and operating cost reductions. Because friction rises on the inner surface of a pipeline when a dried product, like dewatered sludge cake, is moving through the system, the pressure within the system also rises. Friction loss via the introduction of lubricants like water or polymer solutions can mean a drive power reduction and lower schedule piping which can yield a cost-saving.
The FLR system delivers a minimal addition of lubrication media. This is done with the Netzsch Ring Nozzle. It provides a continuous, even 360-degree layer around the entire internal pipe surface delivered by small PC pumps and can be controlled with a variable frequency drive built right into the system’s common control panel. Additionally, the programmable lubrication pump can respond based on the discharge line pressure via a pressure transmitter positioned directly at the end of the pump outlet.
Additionally, the pump was able to transfer the cake the entire distance and incline to the storage hopper within a closed system, eliminating the unreliable conveyer system and minimizing housekeeping, odors and noise.
Over coming time constraints
Equipment installations alone are complex but added were trial equipment removal requirements and time constraints. The city of San Mateo could not extend its short installation window because the cake could not be kept for longer than 14 days without being processed. So after two months, when the new equipment was delivered to the site, a review process including the city, local contractors, and Flo-line Technology was held to determine the most efficient installation process.
Flo-Line Technology President, John Novoselac, offered an in-depth analysis of the tasks to accomplish the system installation in a seven to ten-day window of time. An important discussion about streamlining techniques was included to explore additional ways to save time. At its conclusion, the plant officials for the city of San Mateo were pleased with the example of team effort by all the participants in the installation as everyone went beyond usual contract standards to achieve the common objective for the benefit of the city.
The local contractor removed the existing rental equipment, poured the new concrete base and positioned the new cake pump within their three-day window. Two days were taken by the electrical team to run new conduit and make required control connections. Everyone followed the strategy for the quick-install timetable which allowed Flo-Line Technology ample time to test the system fully without time pressure.
Next steps
This multifaceted system required additional attention for optimal performance so Flo-Line Technology continued on with automation customizations to the controls to achieve smooth and steady interactions within the system. The system evaluation also continued and included plant operator training. The operators were already capable as a result of years of tangential PC thin sludge and polymer applications already employed by the facility.
The cake transfer to the storage hopper resulted in the ideal wear life expectations for the main pump running at a medium speed. The maintenance procedures were well understood and this system did not require specialized training nor any special tools.
The safety features designed into the system, like dry-run protection and high-pressure switches, address all the equipment damage potentials. The centrifuges feed the pump hopper and the pump responds to the incoming media by transferring it to the storage hopper. Particularly dry cake creates a pressure spike due to the higher friction and automatically, the lubrication system adds a small amount of water or polymer to the discharge pipe to reduce the friction which lowers the system pressure. This automatic process requires no operator oversight. New equipment guesswork has been removed and has also removed concerns about equipment damage from learning curves.
Today
The equipment was installed in 2009 and to date, according to Greg Scott, the Flo-Line Sales Engineer, the last stator change was made in 2013. San Mateo had some centrifuge parts drop into the hopper causing some minor damage to the stator about 3 years ago. At that time Flo-Line Technology replaced the rotor and stator for good measure.
According to Greg Scott in May 2016, the current rotor/stator have been operating 24/7 for 3 and a half years since the last change, “An impressive lifetime!”
Plant officials concluded that this project is a model of a collaborative effort among a knowledgeable local equipment supplier, an innovative global equipment manufacturer and plant staff to jointly solve a major operations challenge.
The City of San Mateo WWTP is operating an advanced treatment facility that contributes to an environmentally clean and safe San Francisco Bay.
Comments