NEMO® progressing cavity pumps reliably transfer high-solids sludge cake for recycling
Like many municipal wastewater treatment facilities across the country, a wastewater authority in Illinois was looking for a better way to dispose of the large volume of treated sludge it produced on a daily basis. The municipal agency serves over 300,000 residents within its service area, with three advanced sewage treatment plants, over 125 miles of interceptor sewers, and a combined average design capacity of 63.4 million gallons a day.
In 2006, the municipality built an award-winning sludge recycling plant. The plant dries the waste sludge and processes it into glasslike pellets that can be used in various industrial applications, such as paving and roofing, for fertilizer, or as potential low-grade fuel for power-generating plants.
Wastewater authority requires greater efficiency in transporting high-solids sludge cake
At each of the wastewater authority’s three wastewater treatment plants, the solids are thickened and dewatered by belt filter presses. The dewatered sludge is then loaded into trailers and transported to the municipal Sludge Recycling Facility, where it is stored in two silos prior to the drying and pelletizing process. At the bottom of each of these large silos are four pumps that feed the sludge into a dryer.
Given that the sludge in this application is a very heavy cake, with up to 22% solids, the operators of the recycling facility were experiencing maintenance problems with the existing progressing cavity pumps. These pumps were not designed to handle such heavy sludge cake adequately, and so operators were incurring significant expenses from downtime and pump service. Additionally, the customer was frustrated by the frequent, intensive and messy work they had to perform when servicing the pumps.
“One of the main objectives for replacing these pumps was that the plant operators wanted the pumps to last longer before maintenance and they wanted pumps that were easier to service,” a local sales representative for NETZSCH said. “The original silo pumps needed to have the stators replaced too often, and the when they did, it was a major undertaking. NETZSCH was able to specify progressing cavity pumps that not only would experience significantly reduced wear but also were easily serviced.”
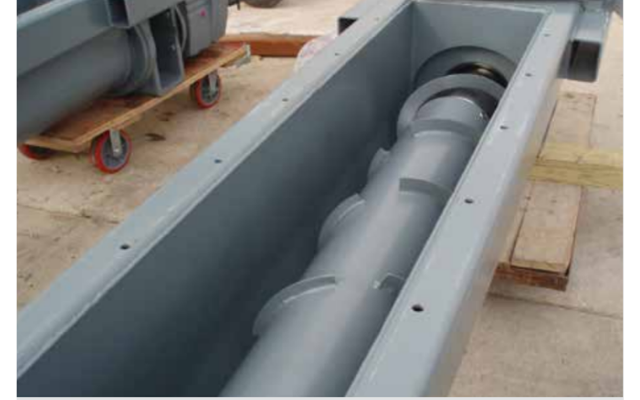
The NETZSCH progressing cavity pump seen here with the segmented, oversized auger with the patented
positioned feed screw auger.
NETZSCH pumps meet customer needs for efficiency, reliability
NETZSCH offered the customer progressing cavity pumps that were designed to transport dewatered municipal sludge with a solids content of 16 to 22% at a rate of 11-16 gpm (2.5 – 3.6 m3/hr) with a discharge pressure of 350 psi (24 bar).

Integrated rotor/stator replacement system with inflatable shut-off (or seal-off) bladder to isolate hopper contents allows for the exchange (or repair) even with a full silo.
NETZSCH engineers custom-designed these progressing cavity pumps with a number of advantages for the customer. A customized hopper let the customer use the existing silo bolt pattern, saving them time and money by eliminating unnecessary modifications to install the NETZSCH pumps. Additionally, the segmented, oversized auger in the NETZSCH pumps, with a patented positioned feed screw auger, prevents bridge-building in the hopper and allows for optimum filling of the rotor stator cavities. The NETZSCH pumps effectively solved the auger-related problems that the customer experienced with previous pumps.
An exclusive rotor release system was also provided to the customer, which eliminates downtime and the mess the customer experienced from having to remove the entire pump from the silo every time a rotor or stator change was made. With this system, a patented shut-off bladder can be inflated that isolates the sludge in the hopper from the rotor and stator. The rotor is connected to the joint with a polygonal profile connector, which allows a quick removal without the need to disassemble the entire hopper, as was the case with the previous pumps.
The NETZSCH pumps have significantly reduced maintenance costs and downtime for the plant operator since they were installed in October 2012. Additionally, the sludge processing plant has reduced the amount of waste it produces from 200 tons a day to just over 30 tons a day.
Comments