Contributor: Tom Zuckett, PSG®
E-Series AODD Pumps From Almatec® Are A Go-To Technology For Chemical Manufacturers Who Can Tolerate No Diversion From Established Specifications In Their Production Processes
Introduction
Their names sound like sinister creations that would spring from the evil mind of a mad scientist in a futuristic novel or movie: hexafluorochloride, dexamethasone, germanium and cadmium telluride. In reality, they are among the many chemical ingredients that are indispensable foundational components in the manufacture of such commodities as pharmaceuticals, semiconductors and solar panels.
The main concern for the manufacturers of these so-called “high-purity” chemicals is not trying to pronounce their names or remembering how to spell them, but ensuring that they are produced in a manner that guarantees the highest level of purity. When these chemicals are not manufactured according to strict specifications for purity, nightmarish scenarios can result that are worthy of a science-fiction novel or movie for both the manufacturer and the end user.
With that in mind, this white paper will illustrate how one type of pumping technology – solid-body plastic, air-operated double-diaphragm (AODD) pumps – possesses the design, construction and operational characteristics that are necessary to guarantee the high-purity manufacture of chemicals, while also offering the ultimate level of energy efficiency and reliability.
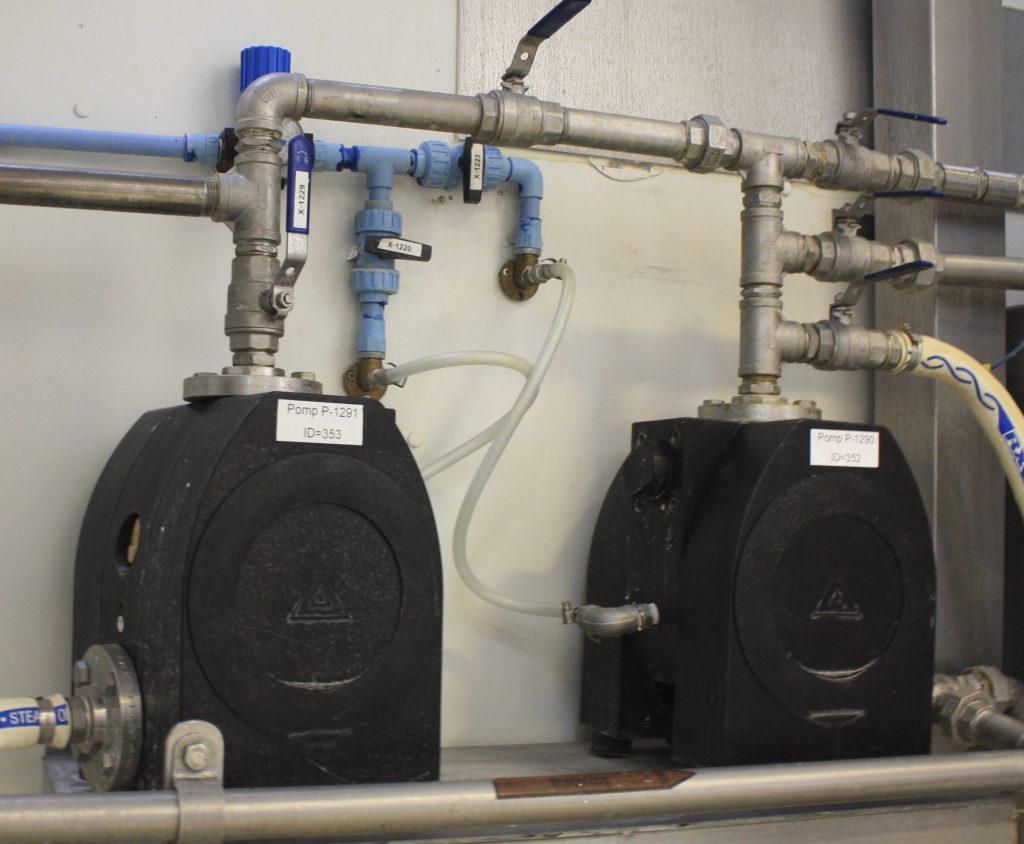
The plastic solid-body construction of Almatec ® E-Series AODD Pumps eliminates the small crevices or cavities that can be found in injection-molded models. It is in these crevices that liquids can accumulate and leak paths can be created.
The Challenge
The universal chemical market consists of thousands of products that are used in hundreds of industries. At the most basic level are the low-grade chemicals that are used in making simple plastics or swimming-pool cleaners and sanitizers. As you move up the chemical food chain, you eventually arrive at the high-purity chemicals. These products are used in precise manufacturing processes where there can be no variance in the makeup of the chemical or slippage in its overall quality.
On top of the need for pristine purity is the fact that these chemicals are very expensive to produce. Therefore, if a batch is deemed not to meet expected quality levels, it can cost hundreds of thousands of dollars in lost revenue for the manufacturer – as well as putting a blemish on the manufacturer’s reputation. Additionally, because of the high stakes that are involved in the production of high-value commodities, their manufacturers will strictly audit the production processes of the chemical companies to make sure that the chemical is produced according to established specs. Anything that can cause the chemical to become out-of-spec would be grounds for the end user to consider finding another supplier.
Another concern for chemical manufacturers is that many of their products can be highly toxic and dangerous to handle. This means that any time high-purity chemicals are handled there is an inherent risk involved. The risk stems from the fact that the release of these chemicals can lead to severe health consequences for humans and animals, as well as damage to the environment.
With all that said, keeping dangerous high-purity chemicals fully contained is often easier said than done. Since many can also be highly corrosive, the pumping equipment used to transfer them is prone to chemical attack if the materials of construction are not compatible with the acid, caustic or solvent. Materials of construction are not the only factor to consider when determining if a pump should be used to handle dangerous chemicals. Another area to focus on is the actual design features of the pump. For example, if the design incorporates mechanical seals or packing, they may be prone to leaking.
Attempts have been made to eliminate the shortcomings of pumps that feature mechanical seals through the implementation of magnetic couplings or double barrier seals. While these methods of containment do outperform mechanical seals, they do possess some disadvantages that reduce their effectiveness. The viscosity range of liquids that are transferred by pumps with magnetic couplings is limited by the amount of transferable torque that can be created. The use of pumps with double seals or barrier liquids can be impractical due to their high cost and the elevated level of maintenance required.
Some common pump styles that have traditionally been used to handle high-purity chemicals include lobe, gear and centrifugal models. While they may be constructed of chemically compatible materials, their design features mechanical seals, the performance of which can be compromised over time, raising the possibility that leaks will occur.
In terms of actual performance, these competitive pump styles also have limits when it comes to the reliable, energy-efficient transfer of high-purity chemicals. Gear pumps, for instance, move liquids through the meshing of gears. Over time as the gears wear, the pump’s volumetric consistency is reduced, resulting in fluctuating flow rates and increased energy usage. The operation of both gear and centrifugal pumps can also create turbulence in the pumped liquid, which can lead to shearing that will damage or alter the liquid’s chemical properties and move it out of spec. Lobe pumps, since they are not true PD pumps, can be subject to product slippage, which will make attaining consistent flow problematic and result in compromised production rates.
In total, pneumatically driven AODD pumps possess many attributes that most electronically driven pumps do not, including portable design, seal-less operation, dry-run and deadhead capabilities, good suction-lift capability, ability to handle a wide product viscosity range, ability to handle small particulates, control without need of a variable frequency drive (VFD), easy grounding, and simple operation, maintenance and repair.
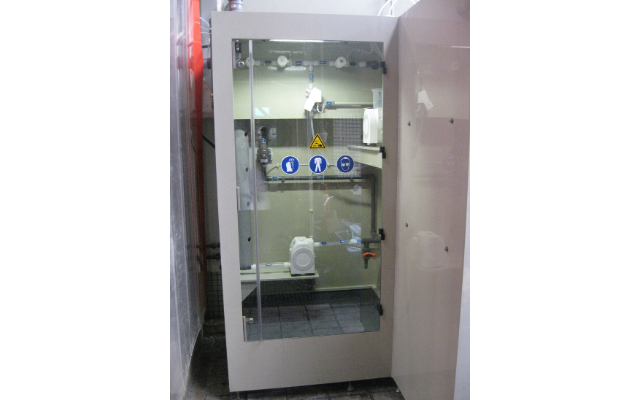
Many high-purity chemicals can cause compatibility concerns when used with certain types of pumps. Almatec ® E-Series AODD Pumps can be constructed of plastic materials that are specifically compatible with the chemicals that are being handled, which eliminates cross-contamination and leak fears.
The Solution
While other PD-pump technologies have shortcomings when handling high-purity chemicals, the AODD pump does not come with such concerns. Specifically, solid-body plastic AODD pumps that are CNC-machined are the preferred choice over their injection-molded cousins. The CNC based design enables tight tolerances, reduced vibration, lower risk of leakage, and greater stability and durability. In general, solid-body AODD pumps are stronger and have a longer life cycle with less required and easier maintenance. Injection-molded plastic pumps, on the other hand, can have small cavities or crevices in the body where liquids can accumulate and potential leak paths can be created. During their operation, injection-molded pumps can also vibrate or bounce more than solid-body models, which can loosen pipework and increase the chances that a leak path will form.
Solid-body plastic AODD pumps can also be constructed of high-quality materials such as polytetrafluoroethylene (PTFE) that are specifically compatible with the chemicals that are being handled, which eliminates corrosion and leak concerns. The overall design and operation of AODD pumps gives them dry-run capability and good controllability, while they are seal-less. Their compressible drive medium permits gentle delivery with attenuated pressure peaks. Startup is simple and the space required is considerably less than in the case of piston-actuated diaphragm pumps or screw pumps.
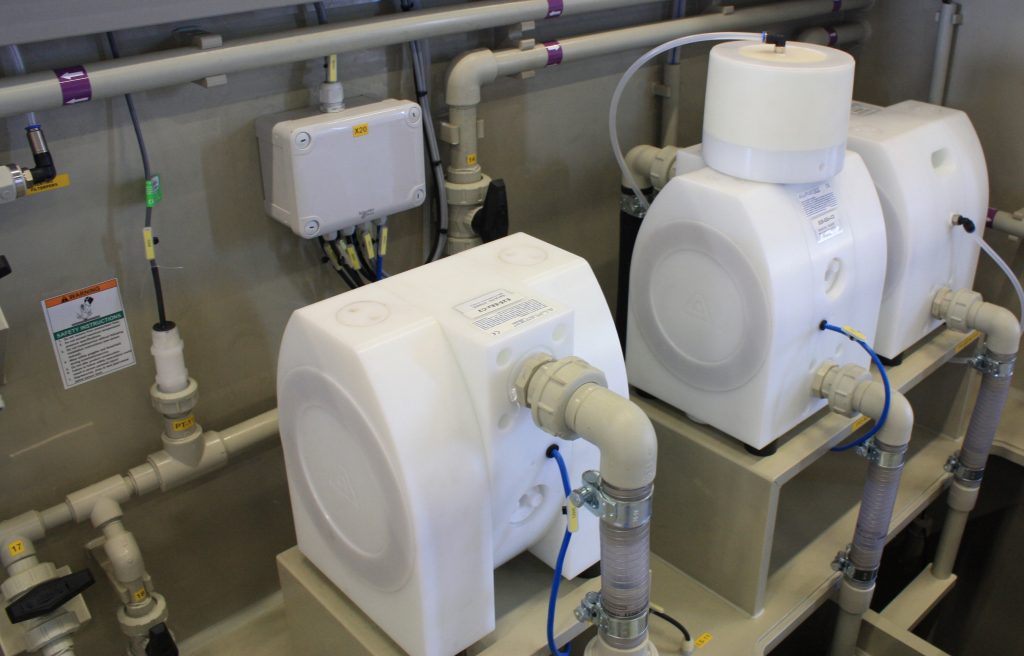
Other positive displacement pump styles like gear and lobe will lose volumetric consistency over time, leading to higher operating costs. By the nature of their operation, Almatec ® E-Series AODD Pumps reliably maintain their flow rates throughout their lifespan, resulting in optimized production cycles and energy usage.
Almatec® Maschinenbau GmbH, Duisburg, Germany, is the actual inventor of plastic solid-body AODD pumps and offers an extensive product range. In the handling and transfer of high-purity chemicals, Almatec, which is a product brand of PSG®, Oakbrook Terrace, IL, USA, a Dover company, recommends its E-Series AODD Pumps. E-Series pumps offer a long list of features and benefits for manufacturers and users of high-purity chemicals:
- Solid-Body Construction: E-Series pumps are CNC-machined from solid blocks of polyethylene (PE) or PTFE. The result is a pump that is not prone to the creation of leak paths while being able to operate in the harshest pumping environments.
- Diaphragm and Containment Ring: The E-Series features a unique stainless-steel containment ring and ring-tightening structure that creates consistent high-torque compression that pulls the components tightly together and compresses the diaphragm in such a way that a leak-free seal is achieved.
- Integrated Diaphragms: The diaphragm’s metal core is integrated into the interior of the closed diaphragm, meaning that diaphragm discs are not required, which eliminates common leak points. The diaphragm’s surface is also smooth and not interrupted by any seals, allowing for consistent product flow.
- PERSWING P® Air Control System: The PERSWING P is a lube-free valve with only two moving parts that allows the E-Series pump to achieve superior flow-rate efficiency and air consumption, which helps lower the overall cost of operation.
- Material Compatibility: The E-Series pump’s housing can be constructed of PE, PTFE, PE conductive or PTFE conductive, which allows it to be used with a wide range of chemical formulations. Additional versatility in regard to material compatibility is realized through the availability of EPDM, PTFE/EPDM and NBR diaphragms; EPDM, PTFE, NBR and stainless-steel ball valves; and PTFE cylinder valves. Depending on the material combination, certificates for USP Class VI, FDA and EC1935 confirmation are available.
- Intrinsic Safety: E-Series pumps that are constructed of PE/PTFE conductive plastics are intrinsically safe and meet the requirements of the ATEX 2014/34/EU directive. This means they can be safely used in explosive atmospheres or when pumping flammable liquids.
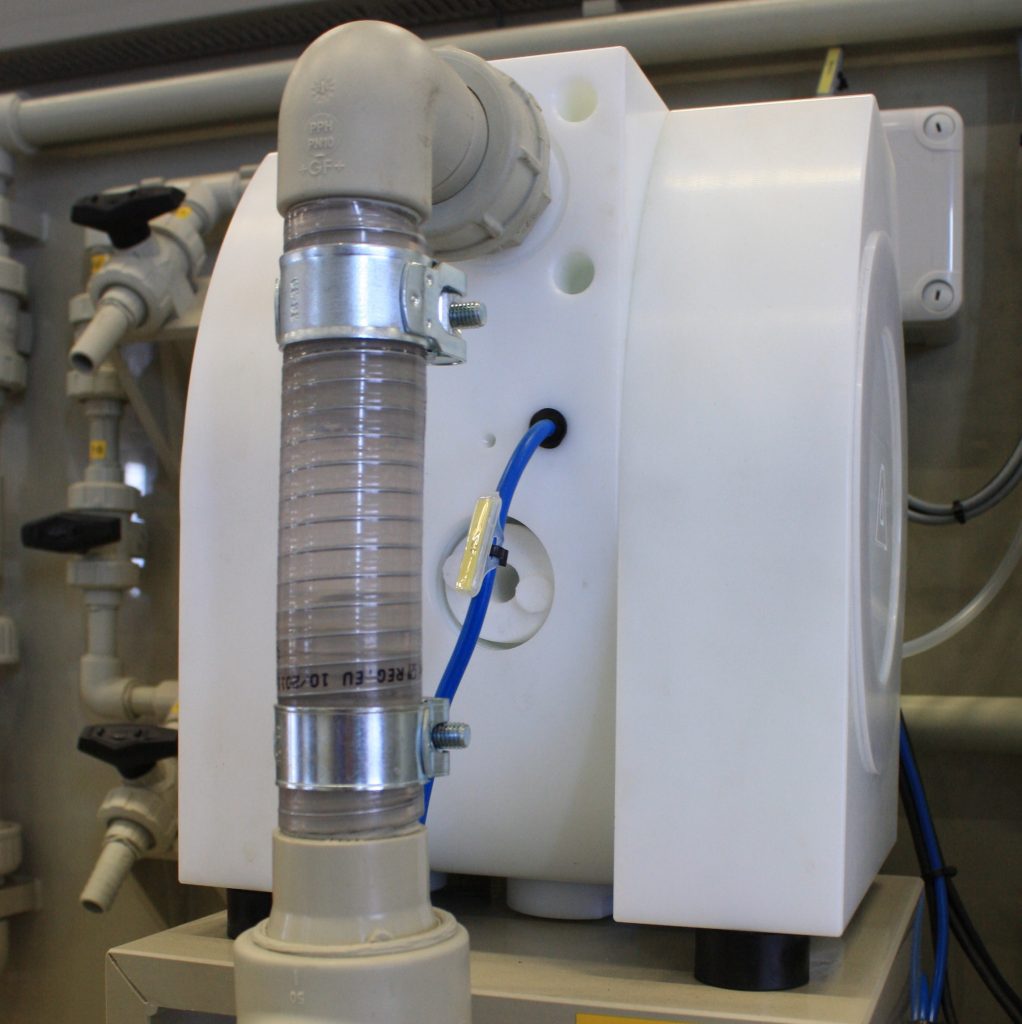
During their operation, injection-molded AODD pumps can vibrate and bounce, which can loosen pipework and increase the chances of a chemical leak. Almatec ® solid-body AODD Pumps are more stable during their operation, which leads to a higher level of product containment.
Knowing that high-purity chemical manufacturing operations are not homogeneous, Almatec has developed a series of optional accessories that can be used with its E-Series pumps, depending on the demands of the application. These options include:
- Barrier-Chamber System: The individual diaphragm is replaced by two diaphragms that are arranged in tandem with a barrier chamber of conductive PE between them and filled with a non-conductive liquid. Any change in the conductivity of the barrier liquid is detected by sensors and signaled to a controller, which triggers an alarm or halts pump operation.
- Pulsation Damper: This accessory is metal- and maintenance-free, self-regulating and meant to be installed on the delivery side of the pump in order to obtain a virtually uniform flow. When operating, it removes pulsation from the liquid flow by equalizing the pressure on both sides of the diaphragm, resulting in pulsation-free flow consistency with no fear of shearing.
- Internal Drain System: Consists of a bypass system in the side housings that can be activated either through hand-operated valves or pneumatically, which allows the pump and piping to be drained without having to be disconnected. This capability also reduces the amount of cleaning agent and solvent that is needed, which also greatly reduces environmental pollution. All of these capabilities make possible the recovery of high-value liquids.
- Stroke Counter: E-Series pumps can be run continuously (24-hour operation), intermittently for hours or minutes, or for a defined number of strokes. To accurately count the strokes, a stroke-counter sensor is installed in the center housing.
Conclusion
Admittedly, there is a science-fiction “out there” feeling to many of today’s high-purity chemicals with fertile, inquisitive minds needed to develop them and find their uses. What is firmly rooted in reality, however, is the need to manufacture and handle them in accordance with a strict set of specifications that cannot be compromised. That’s why guaranteeing their purity and quality is job No. 1 for their manufacturers. Those concerns can be overcome through the use of pumping equipment that has been designed to achieve reliable production of high-purity chemicals. While other pump technologies can claim to do this, only plastic solid-body AODD pumps, specifically the E-Series model from Almatec, can turn those claims into reality.
About the Author:
Tom Zuckett is the PSG® Regional Sales Manager, Americas, Northeast for Almatec® Maschinenbau GmbH, Duisburg, Germany. He can be reached at tom.zuckett@psgdover.com or +1 330-351-5334. Almatec is a premier manufacturer of air-operated double-diaphragm (AODD) pumps. Specializing in machined plastic pumps and stainless-steel pumps for various markets, the brand name Almatec® has become synonymous with quality, reliability and safety. Almatec is a product brand of PSG®, a Dover company, Oakbrook Terrace, IL, USA. PSG is comprised of several leading pump brands, including Abaque™, All-Flo, Almatec®, Blackmer®, Ebsray®, EnviroGear®, Griswold®, Neptune™, Mouvex®, Quattroflow™, RedScrew™, and Wilden®. You can find more information on Almatec and PSG at almatec.de and psgdover.com.
Comments