Author: Mark Pyk
To the surprise of probably no one, in its International Energy Outlook 2017 report, the U.S. Energy Information Administration (EIA) predicted world energy consumption would rise 28% between 2015 and 2040, from 573 quadrillion British thermal units (Btu) in 2015 to 736 Btus in 2040. This extrapolation is supported by the EIA’s “Reference case,” which “assumes continual improvement in known technologies based on current trends and relies on the views of leading economic forecasters and demographers related to economic and demographic trends for 16 world regions based on Organization for Economic Co-operation and Development (OECD) status.”
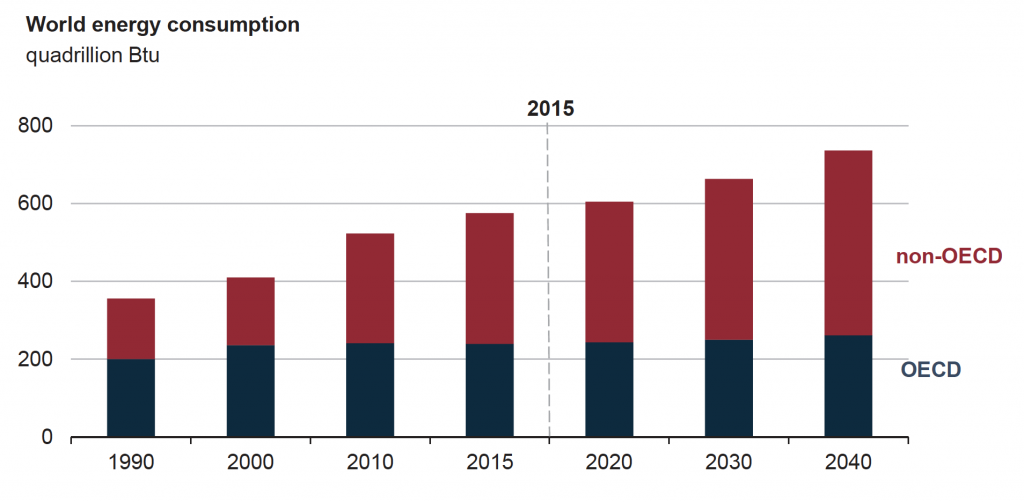
According to the Energy Information Administration’s (EIA) International Energy Outlook 2017, world energy consumption will increase from 575 quadrillion British thermal units (Btu) in 2015 to 736 quadrillion Btu by 2040. This will put pressure on operators in the industrial sector to continue to optimize their energy consumption while still satisfying demanding production rates.
What is the OECD? Founded in 1961, the OECD is an intergovernmental organization that is committed to stimulating economic progress and world trade. There are currently 36 OECD countries: Australia, Austria, Belgium, Canada, Chile, Czech Republic, Denmark, Estonia, Finland, France, Germany, Greece, Hungary, Iceland, Ireland, Israel, Italy, Japan, Korea Republic (South Korea), Latvia, Lithuania, Luxembourg, Mexico, the Netherlands, New Zealand, Norway, Poland, Portugal, Slovakia, Slovenia, Spain, Sweden, Switzerland, Turkey, the United Kingdom and the United States of America.
Related to the rate of growth in world energy consumption, the EIA opined that the global industrial sector – for our purposes, the manufacturing, mining, agriculture and construction industries – will continue to account for the largest share of energy consumption through 2040. At an annual growth rate of 0.7%, global industrial energy use will increase a total of 17.5% from the 240 quadrillion Btus in 2015 to 280 quadrillion Btus by 2040.
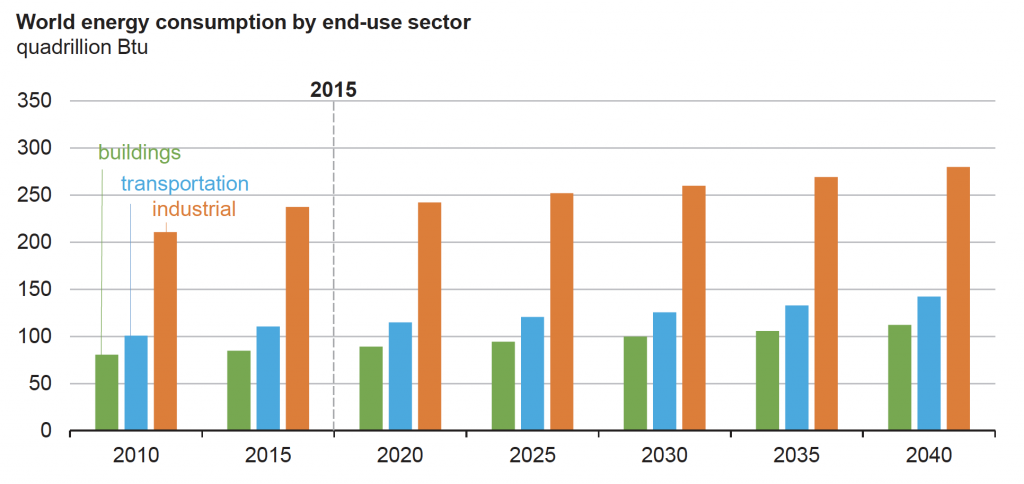
The EIA’s International Energy Outlook 2017 predicts that the industrial sector will continue to account for the largest share of energy consumption through 2040. Therefore, operators will need to continue to identify and deploy the most energy-efficient pumping technologies, with positive displacement sliding vane pumps being the best choice in most instances.
The main reason behind this steady increase in energy consumption should be equally obvious – the world’s population continues to increase with the United Nations’ Department of Economic and Social Affairs saying that the current population of 7.6 billion people will expand to 8.6 billion in 2030 and 9.8 billion by 2050. This consistent population growth is most significant in developing, non-OECD countries, and is being driven by improvements in infrastructure, food production and healthcare that have created a better standard of living for many of those countries’ residents.
That being said, the need for more industrial operations to satisfy the demands of a constantly growing population can collide with edicts that manufacturers reduce their utility and overall operating costs while simultaneously meeting the requirement that they do so in a more environmentally friendly manner. This has forced operators in the industrial sectors to reconsider the types of equipment they have been using in their facilities and operations, with an eye on upgrading to systems that can reliably provide both environmentally safe and cost-effective production.
A Positive Outlook
First, a bit of background: positive displacement (PD) pumps were developed long before centrifugal pumps, with Greek mathematician Archimedes said to have invented the first screw pump around 225 B.C. The operation of PD pumps is signified by the displacement of a known quantity of liquid with each revolution of the pumping elements, which can include vanes, lobes, gears, rotors, screws, etc. The liquid is displaced through the spaces that are created between the PD pump’s specific pumping elements. After the liquid is collected in this space, the movement of the pumping elements transports it to the discharge port. In general, this method of operation allows PD pumps to handle liquids with viscosities up to 1,320,000 centistokes (cSt)/6,000,000 Saybolt Seconds Universal (SSU); capacities up to 1,150 m3/hr (5,000 gallons per minute/gpm); and pressures up to 700 bar (10,000 pounds per square inch/psi).
Today, according to The Hydraulic Institute, pumps account for nearly 27% of total electricity use in the industrial sector. While centrifugal-style pumps remain the most used technology in industrial fluid-handling applications, there is no “one pump fits all” solution. This opens the door for operators to consider the benefits that PD pumps can offer their businesses from an efficiency and energy-savings aspect, even in applications that have traditionally been reliant on centrifugal pumps.
With that in mind, selecting the proper pump for each of the myriad operations in a manufacturing facility can be a daunting task. When making the final choice in pump type, several crucial factors may need to be taken into account: required flow rate, suction and differential pressure, temperature, viscosity, weight, corrosiveness of the liquid being handled, etc. In addition, facility managers too often choose oversized pumps as a fallback when outfitting their systems under the erroneous belief that such equipment will address future capacity needs. These decisions ignore the added energy costs that are inherent in continuously operating oversized pumps.
While the majority of the world’s pumping tasks may currently be performed with centrifugal-style pumps, PD pumps can become a top-of-mind choice when facility operators are apprised of the better functionality that PD pumps can offer their users, including:
- PD pumps are inherently self-priming. All centrifugal pumps must be pre-primed (even those that are touted as “self-priming” are truly “pre-primed” pumps). Industrial facilities can design their process around this centrifugal pump weakness by including pre-fill cycles, minimum tank levels or expensive below-grade installations. On the other hand, industrial facilities can reduce or eliminate these costly and time-consuming system-design considerations by utilizing a PD pump that is inherently self-priming. This capability allows the PD pump to draw a suction vacuum and compress air into the discharge piping, all while dry running. This enables the pump to be used in top-offload suction-lift installations or with long sections of suction pipe.
- PD pumps can line strip. Product recovery is critical for both safety and cost savings. PD pumps left on after a batch cycle can evacuate the suction and discharge piping, preventing any product spillage when the pumps are maintained or when an operator disconnects a hose. This is a critical safety advantage. Further, PD pumps can extract costly products from the bottom of supply tanks (known as the liquid “heel”). The site may purchase an entire tanker, but a portion of that paid-for liquid is left behind by centrifugal pumps, which creates the risk of product cross-contamination, as well as increased tank-cleaning costs. Finally, long pipe runs have substantial liquid volume that is left behind by centrifugal pumps. PD pumps can recover liquid from within the piping system.
- PD pumps are insensitive to the system’s pressure fluctuations. Does your operation feature a batch process, have high backpressure or struggle with operating near a centrifugal pump’s Best Efficiency Point (BEP)? While centrifugal pumps are sensitive to system pressure, PD pumps do not have a BEP and are immune to any system pressure fluctuations.
- PD pumps are viscosity flexible. There is no reduced performance at increasing viscosity (or decreasing viscosity for ultra-thin multi-phase liquids). Centrifugal pumps degrade in performance below 1 cP viscosity and above 1 cP viscosity. PD pumps can operate continuously at 0.2 cP or 200,000 cP viscosities. In fact, you can use many PD-style pumps on a thin solvent and on thick crude oil (which makes them perfect for liquid-terminal or bulk-transfer applications).
PD pumps are available in two categories – reciprocating and rotary, with rotary pumps consisting of single- or multiple-rotor configurations. For our discussion, we will consider the rotary-pump family. By their design and operation, rotary pumps displace a fixed quantity of liquid for every rotation of the pump shaft. Again, vanes, lobes, gears and screw are among the pumping elements that can be used to facilitate the transfer of the liquid.
Within the single-rotor rotary-pump family tree reside sliding vane pumps. The design of the sliding vane pump places a series of metal or plastic “vanes” in dedicated slots in an offset rotor in the pump casing. As the rotor spins past the suction port, the vanes are forced out of their slots and ride against the inner bore of the pump casing, forming pumping chambers. The pumping chambers trap the liquid and transport it around the pump casing to the discharge port, where it flows into the discharge piping. This design virtually eliminates product “slip” (the movement of the fluid being handled against the direction it’s being pumped), meaning that the pump’s high volumetric efficiency is maintained. The method of operation also makes sliding vane pumps ideal for use with thin, low-viscosity liquids, such as propane, ammonia, solvents, alcohol, gasoline, fuel oil, petroleum-based chemicals, refrigerants, and multi-phase and high vapor-pressure liquids with zero net positive suction head available (NPSHA).
Based on their self-compensating design that accounts for pumping element wear through the extension of the vanes during operation, PD sliding vane pumps are energy and mechanically efficient. Other operational advantages of sliding vane pumps – in addition to their ability to handle a wide variety of thin industrial liquids and self-compensate for wear – include:
- Self-compensating vanes ensure consistent flow rates and energy consumption
- Dry-priming capability that allows them to run dry for extended periods
- Superior suction-lift capabilities
- Perfect for low-flow, high-head applications
- Low-pulsation, low vibration pumping for shear-sensitive liquids
- Suitability for use in metered-flow applications
- Optional seal-less construction for elimination of potential leak paths
- Vane replacement that takes minutes and does not require the entire pump to be taken out of service
Sliding Vane vs. Gear Pumps
Rotary self-compensating sliding vane pump technology was perfected in the early 1900s by an engineer, Robert M. Blackmer, who was looking for a solution to ill-performing gear pumps that were constantly wearing and losing their volumetric efficiency, leading to product slip that was hampering the pump’s desired flow rates and operational efficiency.
At the time of Blackmer’s invention, gear pumps were far and away the most common type of PD pump being used in industrial liquid-handling applications. There are two typical types of gear pumps: internal and external gear, both of which transport liquids through the action of a series of gears coming into and out of mesh. While the pumping action for both is comparable, external gear pumps utilize two similar rotating gears to mesh whereas the internal gear pump utilizes a drive, or rotor, gear operating against a smaller internal, or idler, gear.
Admittedly, both modes of gear pumps possess some advantages that are similar to sliding vane pumps – non-pulsing, self-priming and dry-run capability; ability to handle thin liquids at varying pressures; and ease of maintenance – but it is their operational disadvantages that can make them an inferior choice when compared to sliding vane pumps.
Because of their style of operation, from day one gear pumps wear constantly as the pump’s gears mesh, or come into contact with each other, in order to move fluid. This constant wear increases the internal pumping clearances, in the process reducing flow capacity that results in less fluid being pumped per rotation while simultaneously increasing the slip within the pump. To compensate for these larger clearances – and the operational problems that they cause – the pump speed or size must be increased, which not only results in higher energy consumption, but also further accelerates the pump’s wear.
The alternative in this gear-wear scenario is to tolerate a lower level of pumping capacity until the pump’s performance drops to an unacceptable level. However, the gear wear can often go undetected by the operator, which will sap the pump of efficiency – both energy- and performance- related – for a potentially significant period of time before the reduced operating capability is detected and the necessary maintenance can be performed.
Conversely, because the self-compensating vanes in the sliding vane pump continuously adjust for wear, they are able to allow the pump to maintain near-original efficiency and capacity throughout their life. The pump speed also does not need to be increased over time, making sliding vane pumps natural energy-savers, which, as noted previously, is a critical concern for bottom line-conscious operators of industrial facilities.
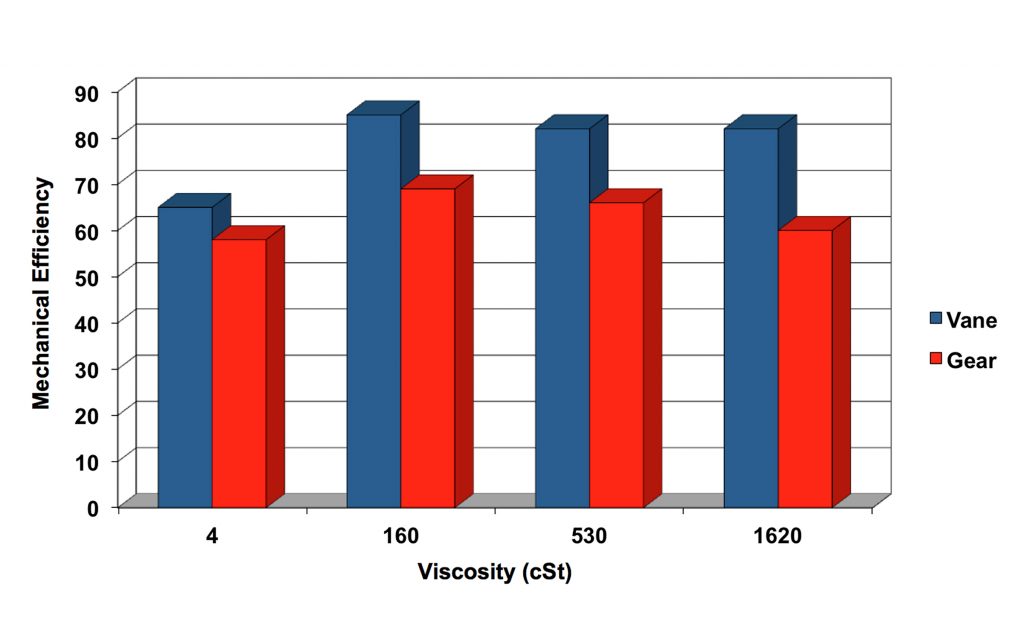
A Mechanical Efficiency Comparison between sliding vane and gear pumps shows that from the lowest to highest viscosities, sliding vane technology delivers the highest level of mechanical efficiency, which equates to the lowest overall energy consumption.
Additionally, if the sliding vanes do wear out or are damaged, replacing them is quick and easy. Vane replacement can be accomplished by simply removing the pump’s outboard head assembly, removing the old vanes, inserting new ones and reinstalling the head, all without the need for special tools. Also, the pump does not need to be removed from the system assembly, with all replacements completed while the pump remains in line, Therefore, in a matter of minutes, the pump is back in operation.
Finally, cavitation – which is present in almost all pumping setups, but occurs at varying levels of severity depending on the pump style – is caused when a liquid changes to a vapor inside the pump chamber. This effect decreases flow through the pump and can cause substantial damage as the vapor bubbles collapse back to a liquid state. Cracking and popping noises indicate cavitation, which can lead to increased slip, capacity loss and expensive repairs if left uncorrected. However, unique to sliding vane technology is an optional Cavitation Suppression Liner that will minimize the wear effects associated with cavitation, while simultaneously reducing slip and capacity loss and maintaining the highest level of energy efficiency.
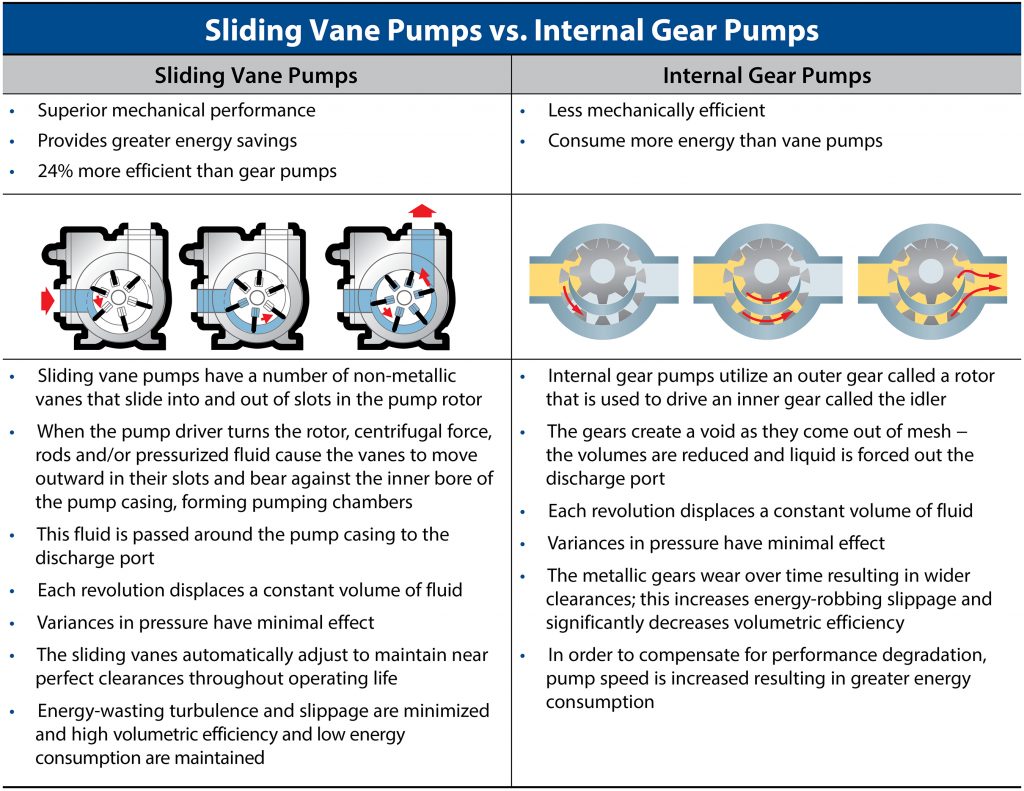
As the chart illustrates, sliding vane pumps offer a wide array of operational advantages when compared to internal gear pumps, most significantly in lower energy consumption that results in lower life-cycle costs.
Conclusion
Today, the task of outfitting an industrial facility with pumps is so much more complex than just picking a technology, turning it on and watching it go. With demanding production schedules, tight operating budgets and environmental-safety concerns to consider, facility operators have to identify and implement a pumping technology that can reliably satisfy these demands, which can often appear to be at odds with each other.
The operational characteristics of sliding vane pumps have proven to hold many advantages over centrifugal pumps and other PD-pump technologies in the areas of maintaining flow rates and optimizing energy efficiency – especially if the application requires the handling of non-abrasive liquids at temperatures less than 500ºF (260ºC) and with viscosities less than 22,500 cP. In the end, the main goal of today’s industrial manufacturer is to improve pump performance in an era where consistent global energy consumption and population growth will continue to put pressure on them to control their energy usage while maintaining strict production rates – and sliding vane pumps can pay a significant role in meeting those demands.
About the author:
Mark Pyk is the Marketing Communications Manager for Blackmer® and PSG®. He can be reached at mark.pyk@psgdover.com. For more information on Blackmer’s full line of pumps and compressors, please call +1 (616) 241-1611 or go to blackmer.com. Blackmer is a product brand of PSG®, a Dover company, Oakbrook Terrace, IL, USA. PSG is comprised of leading pump brands, including Abaque™, Almatec®, Blackmer®, Ebsray®, EnviroGear®, Finder, Griswold™, Mouvex®, Neptune™, Quattroflow™, RedScrew® and Wilden®. You can find more information on PSG at psgdover.com.
Comments