A gland is housed in the stuffing box of a pump. The gland compresses the packing used to seal the pumped fluid. This allows the pump to pass through a hole without leakage. The reliability of the stuffing box is critical to the condition and performance of the whole fluid sealing program. The better the performance and reliability of a fluid sealing program, the better the condition of the internal pump components, including the stuffing box.
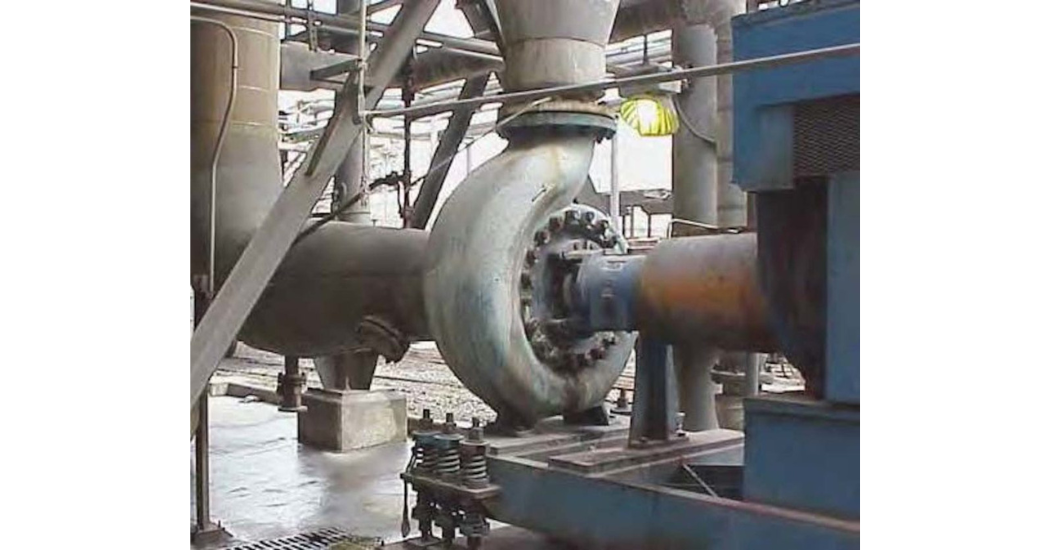
All centrifugal pumps have a stuffing box or seal chamber.
Proper packing installation to prevent excessive leakage, shaft stabilization to prolong shaft/sleeve and packing life, and thorough equipment inspections help improve stuffing box reliability.
Defining Compression Packing
Compression packing is constructed of relatively soft materials which are inserted into the stuffing box between the rotating member, usually the shaft or sleeve, and the body of the rotating asset. Successful compression packing performance depends on a pressurized fluid film between the surface of the rotating shaft/sleeve and the packing for lubrication. By tightening the gland against the outboard ring, pressure is transmitted to the packing set to expand the rings radially. This creates a seal.
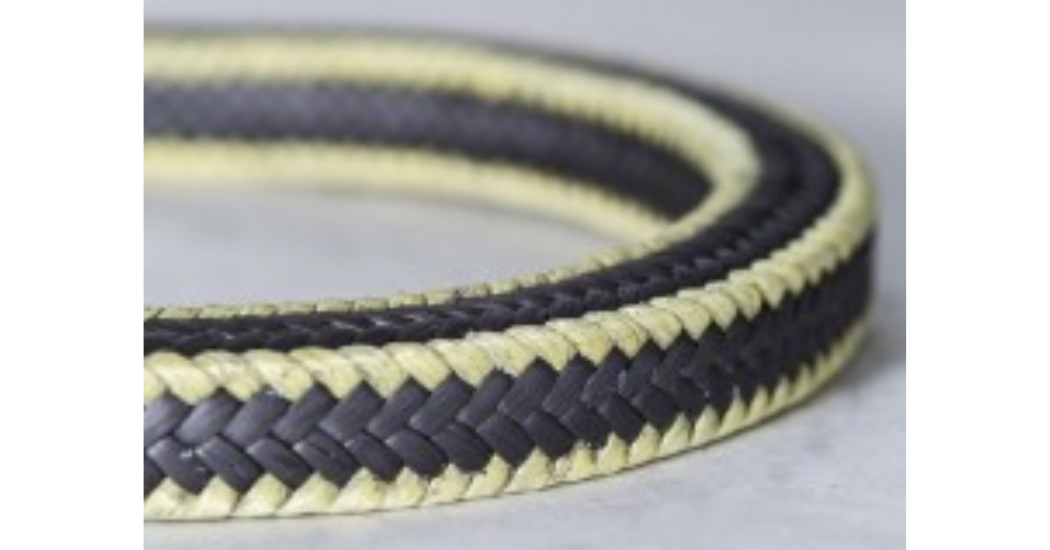
Selecting the right packing for the application will improve stuffing box reliability.
To fully understand these components, you must know the principles and the function of braided packing. Packing has a dynamic surface along the inside diameter at the shaft/sleeve surface. It has a static surface on the outside diameter , which is compressed along the stuffing box bore. The inside surface along the shaft controls flush water leakage at a consistent rate of 10 to 12 drops per minute per inch of shaft size.
Compression packing leaks one of two things:
- Product being pumped if the product is cool and clean
- External flush fluid in all slurry applications or other applications that contain solid particles
The outside surface at the stuffing box bore is static and can be thought of as a gasket. No fluid should ever leak from this area.
Proper Packing Installation for Stuffing Box Reliability
You want to prevent excessive leakage caused by improper packing installations. Proper packing should primarily eliminate leakage, which results in less equipment downtime because of gland water issues.
Three main factors affect proper packing installation:
- Fiber compatibility—Carefully select the packing materials to meet specific application requirements. Consider shaft speeds, pressures, temperatures, and the product being sealed (including pH and solids content).
- Precise installation—Pay particular attention to break-in procedures.
High equipment standards—Strive for high standards in the condition, maintenance, and reliability of equipment. - Using seating installation tools ensures that you have proper loading of every ring. This helps seat each ring correctly in the stuffing box and make sure that the load is carried across all the rings.
Proper seating will:
- Increase packing life
- Increase packing performance
- Decrease shaft/sleeve wear
- Reduce flush water use
- Decrease energy costs
Shaft Stabilization
Shaft deflection is the bending of a pump shaft that occurs when the velocity of liquid being pushed by an impeller is not equal at all points around the impeller. Deflection causes premature packing and mechanical seal wear. It is also more difficult to control flush water use and leakage with deflection.
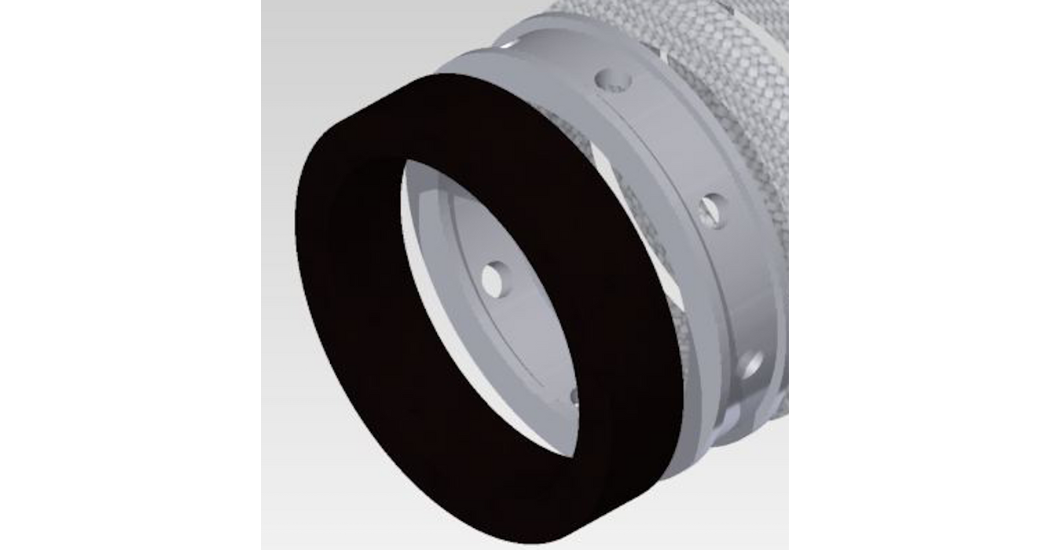
Bushings help support the shaft and prevent deflection.
We know that packing the stuffing box correctly maximizes packing life and performance. But what if the pump experiences shaft deflection? How can you further enhance your stuffing box reliability and prevent excess leakage?
If shafts can be stabilized, the life of technology, such as packing and mechanical seals, can be extended. Bushings may be the answer to provide this stabilization. Some bushings can stabilize shafts in overhung shaft designs, long shafts with little support, and shafts with excessive runout.
A shaft-stabilizing bushing (that is separate from the lantern ring for ease of installation and removal) replaces two rings of packing.
This bushing in tandem with the lantern ring and packing also:
- Reduces flush water use by 80%
- Increases flush water velocity and efficiency
- Can be used with many packing configurations
- Has a low coefficient of friction, which allows for reduced power consumption
Thorough Equipment Inspections
The condition of some equipment components is almost never checked, which may negatively impact reliability. These components include the stuffing box throat and/or throat bushings, along with the gland follower and lantern rings.
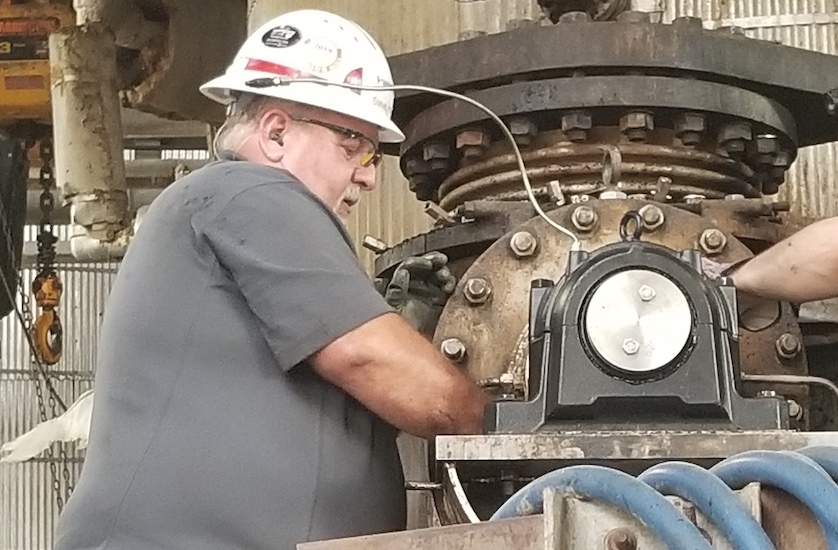
Proper inspections are critical for a reliable stuffing box.
To inspect the stuffing box, you should remove all the packing. Be sure all the rings are removed, including the lantern ring. You can then inspect the shaft/sleeve, stuffing box, throat bushing, and gland for wear or damage. This will also allow you to ensure that the flush line is clear, clean the flush ports, and replace the lantern ring, if necessary.
The shaft/sleeve is a component that is often inspected for wear, but some may not understand how to inspect it correctly. For an effective inspection, first examine the shaft and see where the predominant wear has occurred. It may have occurred in front of the lantern ring or on the gland side.
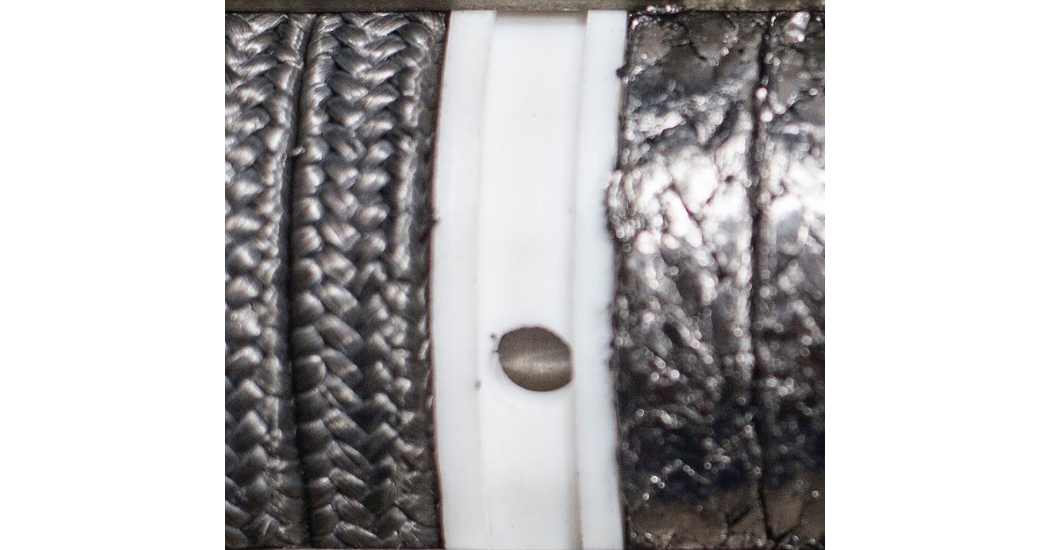
The lantern ring is one component that must be inspected.
Front-side wear is most likely caused by a loss of flush water, which may have happened because the lantern rings or flush water lines became plugged. The wear could also happen if personnel add the packing rings without completely repacking the stuffing box.
If the shaft or sleeve wear is on the gland side, the packing rings may not have been properly seated. Improper seating causes the outside rings to burn and glaze. On the other hand, over tightening the packing may cut off all flush water lubrication. Some wear is normal, but if it exceeds 1/32 inch, you may need to add or replace the shaft or sleeve.
Best Practices for Overall Packing Performance
For ideal packing performance, eliminate as much excessive leakage as possible. This reduces equipment downtime and results in more reliable packing performance.
To help extend packing’s life and effectiveness and improve stuffing box reliability, implement these best practices:
- Select the most effective base fiber and fiber treatment for your industry and application. For pumps, consider the operating temperature, pressure, shaft speed, and pH range. For valves, consider the maximum line temperature, pressure, and pH range.
- Always ensure that the packing is installed correctly and the lantern ring is in the correct location. Not using an installation tool may lead to packing that is not seated effectively and uneven ring loading. Proper installation, using an installation tool to seat each ring, increases packing life and performance and allow all the rings to be loaded effectively.
- Flush and properly maintain the packing’s operating environment according to the manufacturer’s recommendations. Most packing must be flushed to properly cool and clean the stuffing box environment.
- If your operating parameters change from those used to select the packing, reevaluate the fiber and fiber treatment. Changes of flow volume, hours of operation, operating temperature, and the material being pumped may necessitate a fiber or treatment change.
- Replace the packing when the gland adjustment is exhausted or if excess leaking occurs. At some point, the gland will no longer be able to be tightened. Then the packing should be replaced because it will no longer seal effectively. Leakage of more than 10 to 12 drops per minute per inch of shaft/sleeve diameter is excessive and should be investigated.
With proper packing installation, shaft stabilization, and thorough equipment inspections, having a reliable stuffing box is achievable.
About the Author
David Brewer is the Atlantic coast regional manager for SEPCO. Before this role, he served four years in the U.S. Navy and received three Letters of Commendation. He began his career in the fluid sealing industry in January 1995 with AW Chesterton. Brewer later became Virginia regional manager for John Crane until he joined the SEPCO team. He has served many industries including pulp and paper, chemical processing, food and beverage, power generation, textile, and waste treatment. He graduated from Lees McRae College. He may be reached at Davidb@sepco.com.
Comments