Sulzer minimizes downtime for food manufacturer with round-the-clock repair
A UK food manufacturer asked Sulzer to pull out all the stops and turnaround repairs to screw conveyors used on three of its production lines at the same time. Balancing consumer safety with ongoing production meant that repairs needed to be completed as quickly as possible. Drawing on the resources of four service centers, Sulzer worked around the clock to repair the conveyors and assist with reinstallation to restart production as quickly as possible.
Of all the things consumers take for granted, food safety is one of the most obvious. Food hygiene standards are of paramount importance for manufacturers and consumers alike. Quality control systems ensure manufacturers are made aware of potential issues, enabling them to take necessary measures and resolve any issues, keeping consumers safe.
In this case, the manufacturer uses screw conveyors to transport powdered ingredients from a storage location to the production line. The 400 mm diameter stainless steel screws are suspended using split roller bearings in a stainless steel trough. Each conveyor was made up of five scroll sections that were connected using a spigot socket joint and a locking bolt.
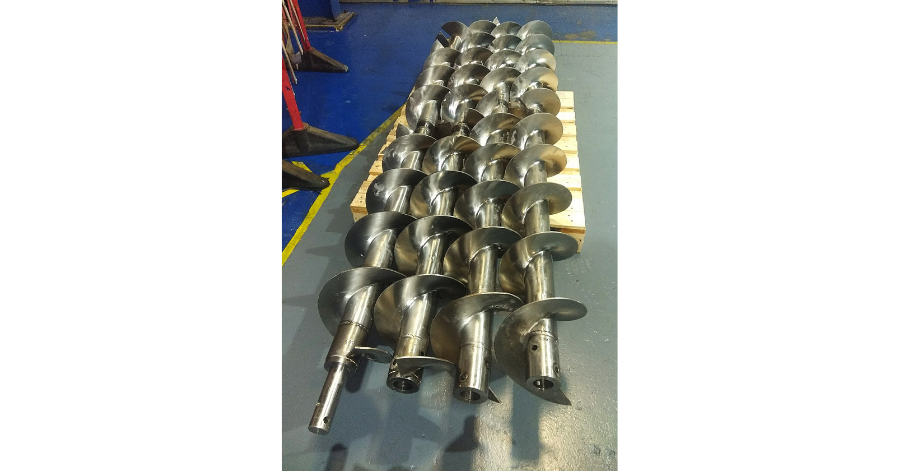
The refurbished scroll sections were delivered back to the customer for installation
Call to action
The first sign of an issue came from the integrated metal detection system, which identified small pieces of steel in the powdered ingredient. This alarm caused the immediate stoppage of one conveyor to prevent any contaminated material getting into the finished product. Meanwhile, the source of the metal was investigated and found to be the bearing journals on the scroll sections.
Having previously worked with Sulzer, the manufacturer contacted the Daventry Service Center and explained the situation. Shortly afterwards, the complete screw was dismantled onsite and transported to Daventry for repair.
However, due to the design of all the conveyors being the same, there was a risk that the same problem could develop on the other production lines. This was an unacceptable risk, however small, and shortly after Sulzer started work on the first conveyor, the customer explained that the decision had been taken to remove all the screw conveyors, adding to the work load significantly.
Neil Fuller, Daventry Service Center Manager, explains: “The initial enquiry was placed with us, but as soon as the scope expanded, we scaled up our operation to deliver the project within the revised timeframe by calling upon others within the Sulzer network. We immediately contacted our facilities in Nottingham, Birmingham and Avonmouth who supported the repair project.”
Precision manufacturing
The scroll sections are joined together using a spigot and socket arrangement that is also cross-pinned to ensure all the sections rotate together. The customer removed the scroll sections from the conveyor troughs, but in some case the sections would not come apart easily and had to be cut. These joints would be replaced by Sulzer as part of the repair process.
Each scroll was set up on a horizontal boring machine to remove the old journals and bored out to accept a new coupling section, which was being manufactured at the same time. The new couplings included the bearing journals and were manufactured to tolerances that required them to be cryogenically installed before being welded in place. The new sections were cross-pinned and machined to the finished diameter.
As an additional measure, 5 mm of material was removed from all of the flights using plasma cutters to prevent any contact between the scrolls and the trough in the event of a repeat bearing failure. This was achieved by setting each scroll section up on a set of bearings so that it could rotate slowly, and fixing the plasma torch so that it could move along the scroll removing the material. After which, the flights were dressed to give a smooth surface finish.
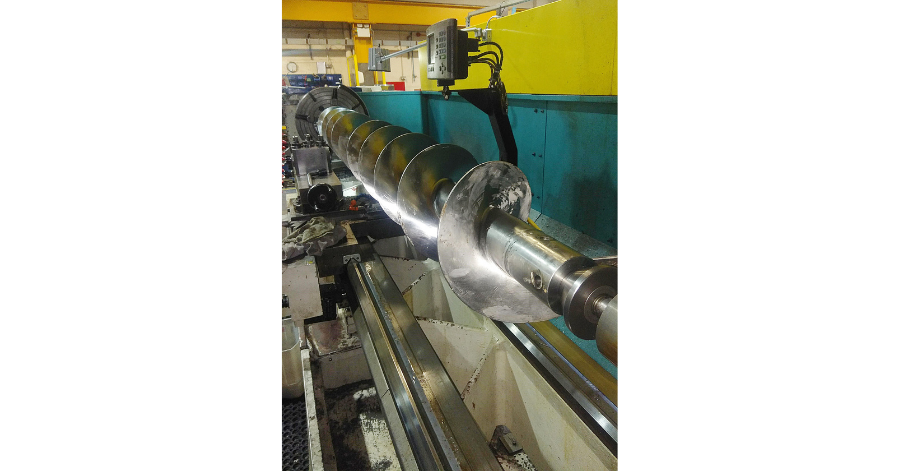
Each scroll section was precision machined to ensure optimum clearance in operation
Team effort
Neil continues: “The Sulzer team pulled out all the stops to get all the work completed on time. Nottingham and Avonmouth bored out the shafts while Birmingham manufactured the new stub shafts to a rough machined finish. These were shipped to Daventry where they were machined to their final dimensions and installed.” Meanwhile, the split roller bearings were replaced by the customer before the refurbished screw conveyor sections were shipped back to site, where they were carefully washed and sanitized. Sulzer’s field service engineers assisted with reassembly and installation, which took two days.
Throughout the project, the customer was in regular communication, asking how the project could be completed more quickly. To speed up the project even further, day and night shifts were used as well as the weekend to deliver all the materials as quickly as possible.
Neil concludes: “The customer really was going above and beyond in taking out the other two production lines at the same time, but they did not want to risk any chance of further issues on any of the production lines. The additional work was easily accommodated thanks to the flexibility of the Sulzer network, ensuring the project was delivered in the shortest possible timeframe. All the work, from the first point of contact to the last section being installed and production restarted, was completed in just 10 days.”
About Sulzer:
Sulzer is a global leader in fluid engineering. We specialize in pumping, agitation, mixing, separation and application technologies for fluids of all types. Our customers benefit from our commitment to innovation, performance and quality and from our responsive network of 180 world-class production facilities and service centers across the globe. Sulzer has been headquartered in Winterthur, Switzerland, since 1834. In 2020, our 15’000 employees delivered revenues of CHF 3.3 billion. Our shares are traded on the SIX Swiss Exchange (SIX: SUN).
Comments