Many industrial applications harbor challenging operating conditions such as corrosive or erosive atmospheres and high temperatures. Every component of rotating machinery used in these conditions needs to operate reliably to ensure an extended overall service life for the equipment. In many cases, specialist coatings form an important part of the design from the original equipment manufacturer (OEM) (or upgrade) and these must be reconditioned or improved during any maintenance project.
Laser metal deposition (LMD) is a repair technique that can be used for the restoration of many components used in rotating equipment similar to methods like conventional welding and high velocity oxidized fuel (HVOF). The range of repairs that can be achieved using LMD is extensive. From restoring worn bearing journals and seal areas to renewing steam turbine blade leading edges and the impeller vane tips of pumps.
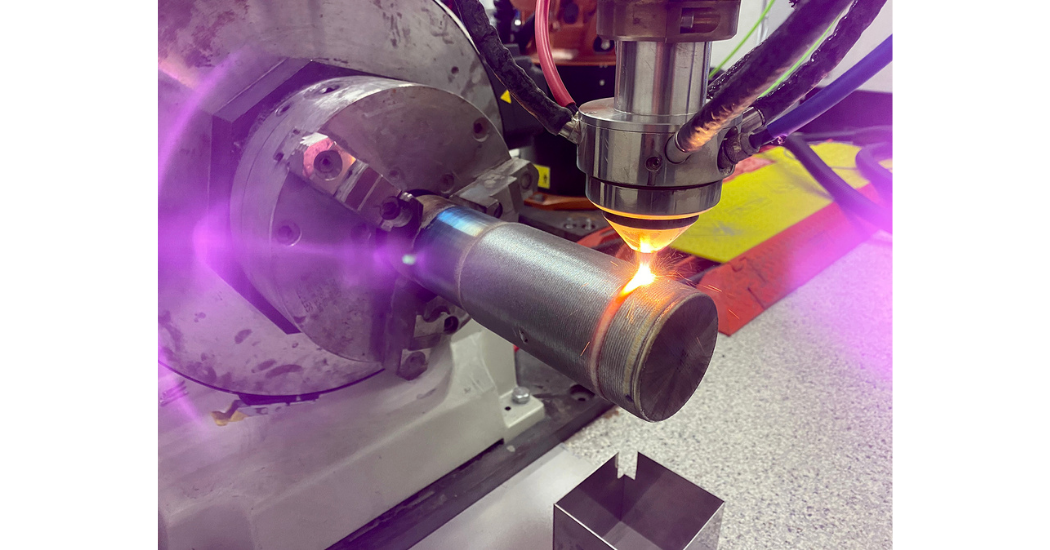
Laser metal deposition (LMD) is a repair technique that can be used for the restoration of many components used in rotating equipment similar to methods like conventional welding and high velocity oxidized fuel (HVOF).
The laser in the LMD repair process offers benefits beyond what both HVOF and submerged arc welding provide. The most obvious is the reduced heat input, which minimizes distortion, reduces the heat-affected zone (HAZ) and almost eliminates the need for post-weld procedures. At the same time, the metallurgical bond of LMD assures excellent consistency in material density and perfect adhesion with the parent material of the component.
LMD is the latest addition to HICoat’s range of solutions, offering a variety of materials including Inconel® 625 and Stellite® 6 as well as others for hard-facing, improved corrosion resistance, and general dimensional restoration.
With over 25 years’ experience in delivering coating solutions for rotating equipment, Sulzer HICoat has extensive in-house expertise and cutting-edge facilities to ensure the best solution is delivered for every project. LMD can be used to re-establish original dimensions in the repair of shafts up to 23 feet (7 meters) in length and 50’000 lbs (25 tonnes) in weight, impellers measuring up to 94 inches (2.4 meters), casings and diaphragms.
Combined with precision machining facilities, Sulzer offers a fast and effective repair service for all types of rotating equipment using the most effective solutions available. LMD is just one more technique Sulzer uses to help operators minimize downtime and extend the working life of important assets.
About Sulzer
Sulzer is a global leader in fluid engineering. We specialize in pumping, agitation, mixing, separation and application technologies for fluids of all types. Our customers benefit from our commitment to innovation, performance and quality and from our responsive network of 180 world-class production facilities and service centers across the globe. Sulzer has been headquartered in Winterthur, Switzerland, since 1834. In 2020, our 15’000 employees delivered revenues of CHF 3.3 billion. Our shares are traded on the SIX Swiss Exchange (SIX: SUN). www.sulzer.com. The Pumps Equipment division specializes in pumping solutions specifically engineered for the processes of our customers. We provide pumps, agitators, compressors, grinders and screens developed through intensive research and development in fluid dynamics and advanced materials. We are a market leader in pumping solutions for water, oil and gas, power, chemicals and most industrial segments.
Throughout the Americas, Sulzer provides cutting-edge parts as well as maintenance and repair solutions for pumps, turbines, compressors, motors and generators. We service our own original equipment as well as third-party rotating equipment operated by our customers. Our technology-based solutions maximize reliability and lifecycle cost effectiveness.
For more information on Sulzer, visit www.sulzer.com
Comments